Файл: Отчет по учебной ознакомительной практике огу 15. 03. 06. 7023. Ххх п руководитель по практической подготовке А. А. Терентьев Студент группы 22МР(б)Мех И. А. Филимонов.docx
Добавлен: 25.10.2023
Просмотров: 100
Скачиваний: 4
ВНИМАНИЕ! Если данный файл нарушает Ваши авторские права, то обязательно сообщите нам.
Во всех случаях выбор типа оборудования определяется технологией обработки, необходимой производительностью, весом и размерами обрабатываемых деталей. Механообрабатывающие цехи комплектуются следующим оборудованием: токарными, револьверными, фрезерными, зубофрезерными, строгальными, расточными, карусельными, долбёжными, шлифовальными, сверлильными, и другими металлорежущими станками. Сборочные цехи обычно комплектуются оборудованием для гальвано-покрытий, сварочными агрегатами, испытательными стендами. При механообработке и сборке применяется следующий инструмент: режущий (резцы, фрезы, свёрла, абразивы, полировальные круги и др.); мерительный калибры (пробки и скобы), штангенциркули, микрометры); слесарный (молотки, плоскогубцы, ключи, отвертки, зубила, напильники, ножовки, пробойники и др.), а также технологическая оснастка (кондукторы, патроны, многорезцовые головки, универсальные сборочные приспособления и др.). В конструкции технологической оснастки для станков с числовым программным управлением (ЧПУ), а также автоматов и полуавтоматов имеются свои существенные особенности.
4 Конструкции и области применения металлорежущих станков, металлорежущих инструментов, технологической и инструментальной оснастки
Металлорежущее оборудование – это станки, которые предназначены для обработки заготовок и полуфабрикатов из металла путем придания детали необходимой формы за счет снятия стружки.
На рисунке 2 показан внешний вид токарного станка с ЧПУ модели ТС1720Ф4.
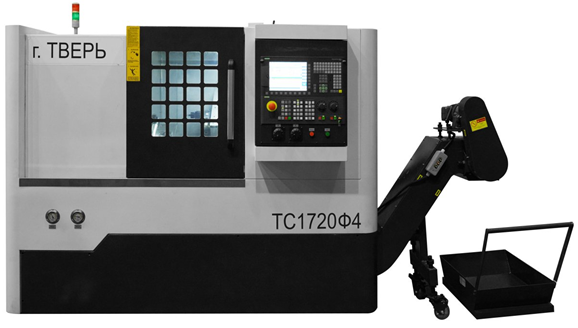
Рисунок 2 – Внешний вид станка модели ТС1720Ф4
ТС1720Ф4 токарный станок с функцией фрезерования, предназначен для следующей обработки фланцев, валов и деталей из прутка [2]:
• автоматическая обработка внутренних и внешних цилиндрических, конусообразных, радиусных и торцевых поверхностей;
• точение канавок и выемок валов, дисков;
• нарезание метрических, дюймовых и конусных резьб;
• выполнение сверлильных и фрезерных операции в радиальном и осевом направлениях.
Тяжелое основание и надежные применяемые компоненты перемещений по осям обеспечивают высокую жесткость станка. Прямой привод. Мотор подачи - шарико-винтовая пара обеспечивает получение максимальной точности установки координат. 12-ти позиционная револьверная головка и современная русифицированная система ЧПУ позволяют обрабатывать детали сложных форм с высокой производительностью. Стружкосборник, податчик прутка, улавливатель готовых деталей и паров СОЖ позволяют добиться оптимальной автоматизации производства при максимальной безопасности.
Основными узлами станка являются: станина, шпиндельная бабка, задняя бабка, револьверная головка, привод оси Z, привод оси Х, кожуха, система подачи СОЖ, стружкосборник, система ЧПУ, электрошкаф, электрооборудо-вание.
Управляемая ось С с контролем позиции от высокоточного датчика, установленного напрямую на шпинделе обеспечивает высокоточную обработку при выполнении фрезерных операций.
Наклонная конструкция обрабатывающего центра обеспечивает свободный отвод стружки из зоны резания и улучшенную защиту направляющих и винтовых передач. Увеличенное отверстие для падающей стружки, предусмотренное в станине, в сочетании с пластинчатым стружкосборником (базовая комплектация), минимизирует потери времени на ее удаление из рабочей зоны в процессе работы.
Высокая производительность ТС1720Ф4 также обусловлена высокой скоростью перемещения по осям X и Z. В качестве приводов продольных подач применяются сервомоторы, способные работать с большим ускорением даже при переменном характере нагрузки. Безлюфтовые муфты, подшипники и роликовые направляющие качения повышенной жесткости - Hiwin (Тайвань) обеспечивают минимальное сопротивление движению исполнительного механизма, достигая максимальной скорости перемещения (20000 мм/мин). Высокоточные ШВП класса С3 преднатянутого типа позволяют исключить люфты и обеспечить преобразование крутящего момента привода в поступательное движение исполнительного механизма с высокой точностью позиционирования (±0,005 мм). Автоматическая импульсная система смазки направляющих и ШВП увеличивает срок эксплуатации станка.
Обрабатывающий центр оснащен шпиндельным узлом картриджного типа, что обеспечивает высокую нагрузочную способность к восприятию осевых нагрузок и минимальное тепловыделение.
Высокая скорость шпинделя (до 4500 об/мин) и мощный электродвигатель с высоким крутящим моментом позволяют производить как чистовую, так и черновую обработку деталей. Комплект высокоточных высокоскоростных подшипников позволяет сохранять высокую точность обработки при длительных интенсивных нагрузках.
Для зажима заготовки применяется полый гидравлический 3-х кулачковый патрон. Для удобства оператора управлять зажимом патрона можно как с помощью педали, так и с пульта ЧПУ, что повышает производительность. Возможна установка цангового патрона с различными размерами по требованию заказчика и 2-х, 4-х кулачковых патронов.
Для достижения максимальной автоматизации и производительности станка возможна установка податчика прутка (опция). Барфидер позволит обеспечить подачу материала для обработки в автоматическом режиме.
Задняя бабка включает пиноль с гидравлическим приводом, которая перемещается во внутренней части корпуса. Выдвижение и отвод пиноли осуществляется гидроцилиндром, управляемым оператором с пульта или педалью, что позволяет быстрее закрепить заготовку в центрах и обрабатывать ее за одну установку. Перемещение задней бабки по направляющим станины станка производится вручную. устанавливается она на V-образные и прямоугольные направляющие. Прилегающие поверхности основания задней бабки пришабрены по требованиям точности к направляющим станины. Широкое расположение направляющих и конструкция задней бабки, рассчитанная на обработку в тяжелых условиях, обеспечивают дополнительную жесткость центра.
Револьверную головку отличают компактность, высокая точность позиционирования, хорошая жесткость и надежность зажима инструментального диска.
Установка инструмента как в осевом, так и в радиальном направлении позволяет увеличить концентрацию операций на станке. В конструкции револьверной головки предусмотрена подача СОЖ непосредственно в зону резания через инструментальный диск и инструментальные блоки, что обеспечивает улучшенный теплоотвод и чистоту поверхности.
Револьверная головка позволяет использовать аксиальный и радиальный приводной инструмент VDI30 для выполнения фрезерных работ, сверления и нарезания резьбы на торцевой поверхности и по диаметру.
Мощный парк станков с числовым программным управлением (ЧПУ) представлен токарными, фрезерными, обрабатывающими центрами зарубежного и отечественного производства [3].
Обрабатывающий центр с ЧПУ модели 800VHT российского производства предназначен для обработки крупногабаритных деталей. За одну установку с высокой производительностью может производиться как токарная обработка на вращающемся столе, так и фрезерная пятикоординатная обработка.
Станок токарный сверлильно-фрезерно-расточный портального типа с ЧПУ модели 2000VНТ российского производства предназначен для высокопроизводительной комплексной обработки деталей из различных конструкционных материалов. Поворотный шпиндель станка обеспечивает возможность комплексной обработки деталей сложной формы с пяти сторон за одну установку при точности углового позиционирования 0,003 град. Станок выполняет операции сверления, зенкерования, развертывания отверстий при горизонтальном или вертикальном положении шпинделя, нарезание резьбы метчиками, получистовое и чистовое прямолинейное, контурное и объемное фрезерование, внешней и внутренней токарной обработки на вращающемся столе. Наибольший диаметр обрабатываемой детали: 2000 мм. Наибольшая масса обрабатываемой детали: 5000 кг.
Горизонтальный обрабатывающий центр с ЧПУ модели ИР-1400 предназначен для высокопроизводительной обработки крупногабаритных деталей и сборок из любых конструкционных материалов. Станок обладает высокой степенью автоматизации, обеспечивает высокую производительность, точность обработки и экономичность. Максимальные габариты обрабатываемой детали: 2500х2000х2000мм с максимальной массой детали 16 000 кг.
Станок вертикальный фрезерно-расточный с ЧПУ модели 500V22/4 российского производства предназначен для высокопроизводительной обработки деталей длиной до 5м из различных конструкционных материалов в условиях единичного, мелкосерийного и серийного производства. Станок оснащен поворотным столом диаметром 700 мм с частотой вращения 16 об/мин, шпинделем с частотой вращения от 0 до 8000 об/мин и номинальным крутящим моментом 95,5 Нм.
Станок координатно-расточной 2Е470АФ11 российского производства предназначен для обработки отверстий, связанных между собой точными расстояниями, методом точного чистового растачивания. Размеры рабочей поверхности стола 1400х2240 мм. Пределы частоты вращения шпинделя 10…2000 об/мин. Грузоподъемность стола 2500 кг. Обеспечивает возможность проведения таких операций, как развертывание, зенкерование, сверление, подрезка торцев, фрезерование плоскостей (получистовое и чистовое), разметка, проверка линейных размеров, проверка межцентровых расстояний обработанных отверстий в прямоугольной системе координат, расточка отверстий в полярной системе координат с помощью накладного поворотного стола.
Пятикоординатные шлифовально-заточные станки с ЧПУ нового поколения позволяют производить фрезеровку, шлифовку и заточку режущего инструмента одновременно. Программное обеспечение содержит стандартные циклы обработки: вышлифовка канавок из цельного материала, полировка канавок при переточке, вышлифовка наружного диаметра, переточка передней режущей кромки торца, и т.д. Высококвалифицированные специалисты создают собственные циклы обработки. С помощью камеры и программного обеспечения возможно измерение геометрии изготавливаемого инструмента непосредственно на станке. Возможно измерение всех поверхностей на контрольно-измерительной машине с точностью до 2 мкм. Маркировка инструмента производится на оборудовании с помощью лазера, согласно ГОСТ.
Широко представлена на объединении электроэрозионная обработка.
Линейный электроискровой (электроэрозионный) координатно-прошивочный станок модели AG35L LР1 - это установка с линейными сервоприводами по осям, керамическим столом 600х400 мм, встроенной 3D CAD/CAM - системой + автопрограммирование с автотехнологом (достижимая точность обработки - ± 2,5 мкм).
Электроэрозионный проволочно-вырезной станок с ЧПУ модели CUT 20P оснащен системой автоматической заправки и перезаправки проволоки.
Металлорежущий инструмент используют для изменения формы и размеров обрабатываемой металлической заготовки [4].
Резцыприменяют на металлорежущих станках для точения цилиндрических, конических, торцовых и фасонных поверхностей на заготовках типа тел вращения, а также расточки отверстий, прорезания канавок и нарезания резьб.
На фрезерном оборудовании основным режущим инструментом являются фрезы, которые осуществляют обработку и резку заготовки.
Для получения и обработки отверстий используют различные сверла, зенкеры, развертки.
На рисунке 3 показаны различные виды технологической оснастки.
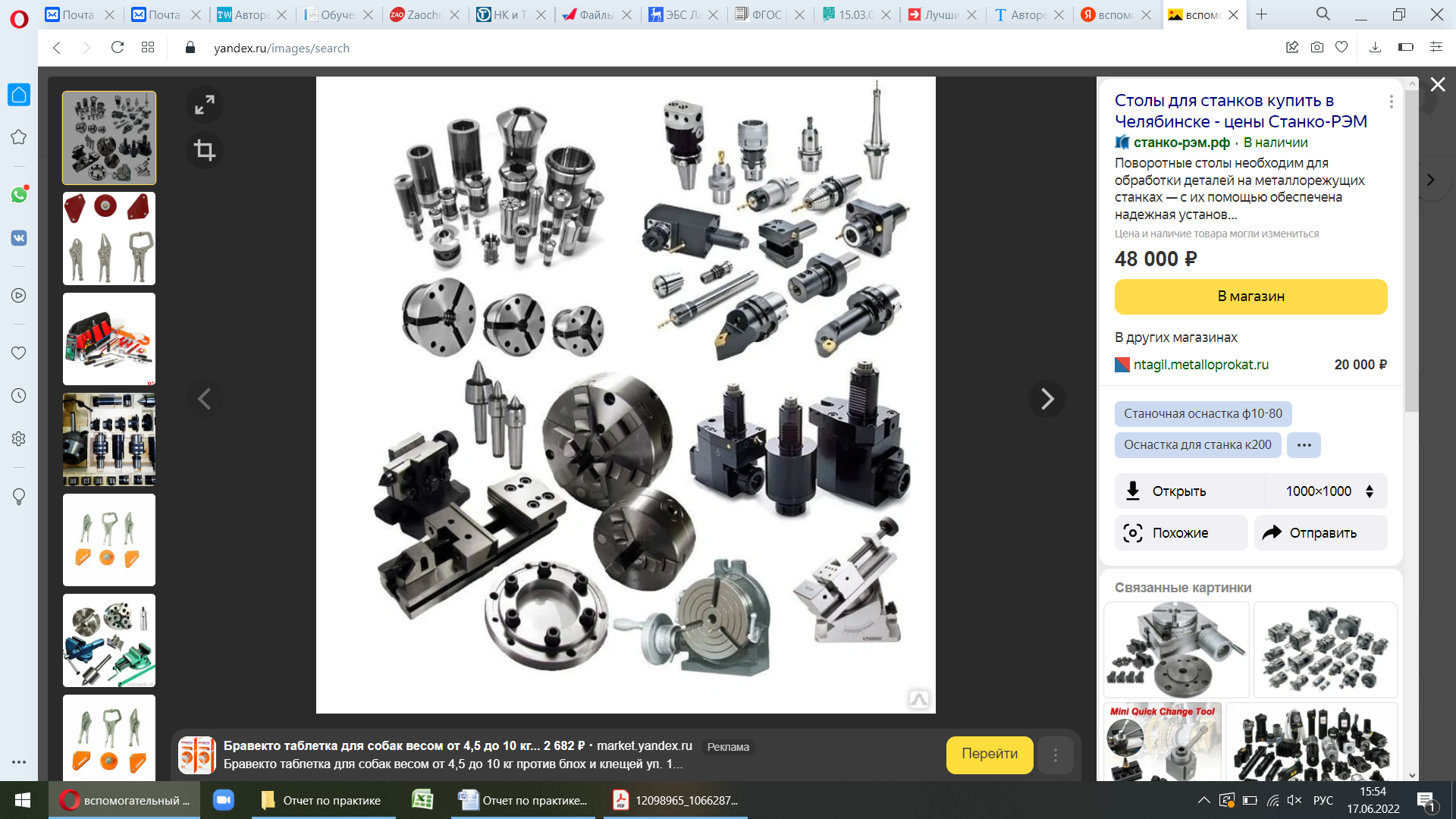
Рисунок 3 – Технологическая оснастка
К технологической оснастке относятся также приспособления для установки и закрепления заготовок и инструмента (вспомогательные инструменты).
Приспособления для установки и закрепления заготовок в зависимости от вида механической обработки подразделяют на токарные, сверлильные, фрезерные, расточные, шлифовальные и другие. Примерами универсальных приспособлений являются прихваты, угловые плиты, призмы, машинные тиски, патроны и другие.
Вспомогательные инструменты — это различного вида резцедержатели, патроны, оправки, удлинители и переходники, специальные блоки и т.д. Они позволяют существенно расширить область применения режущего инструмента и обеспечить его эксплуатацию в автоматическом режиме, а за счет унификации — сократить номенклатуру специальных инструментов и осуществить агрегатно-модульный принцип их конструирования.
Важнейшую роль в обеспечении качества и конкурентоспособности продукции практически всех отраслей промышленности играет контрольно-измерительная техника, в которой особое место занимают средства измерения и контроля геометрических параметров ответственных деталей, узлов машин и механизмов [5].
Для высокоточных измерений наружных и внутренних линейных размеров, а также глубин отверстий используется электронный штангенциркуль.
Для измерения параметров шероховатости методом ощупывания плоских и цилиндрических (наружных и внутренних) поверхностей ответственных деталей применяют цифровые измерители шероховатости.