Файл: Сварочный полуавтомат оборудование, предназначенное в полуавтоматическом режиме для сварки в среде защитных газов. Этот аппарат при своей относительно невысокой стоимости отличается хорошей мощностью.doc
ВУЗ: Не указан
Категория: Не указан
Дисциплина: Не указана
Добавлен: 24.11.2023
Просмотров: 32
Скачиваний: 1
ВНИМАНИЕ! Если данный файл нарушает Ваши авторские права, то обязательно сообщите нам.
Введение
Сварочный полуавтомат – оборудование, предназначенное в полуавтоматическом режиме для сварки в среде защитных газов. Этот аппарат при своей относительно невысокой стоимости отличается хорошей мощностью. Подача сварочной проволоки полностью автоматизирована, а вот сам агрегат перемещается вручную. Сварочный полуавтомат обладает массой достоинств. В частности, здесь могут применяться как плавящиеся электроды, так и неплавящиеся. MIG/MAG - режим полуавтоматической сварки плавящейся электродной проволокой в среде углекислого газа или газовых смесей. Кроме того, сварочный полуавтомат, для выполнения широкого спектра работ, может быть оснащен горелками различных типов.
Представленные в нашем каталоге сварочные полуавтоматы – это оборудование высочайшего класса. Мы реализуем аппараты, которые на практике зарекомендовали себя с лучшей стороны и потому пользуются большой популярностью. Все сварочные полуавтоматы соответствуют общепринятым стандартам безопасности и при полном соблюдении правил эксплуатации будут служить длительное время.
В 1802 году В.В. Петров впервые в мире открыл явление электрической дуги и указал на возможность использования тепловой энергии дуги в расплавлении металлов. Он первый построил самую большую для того времени батарею, при помощи которой и проводил свои опыты. Эти замечательные опыты с электрической дугой В.В. Петров опубликовал в 1803 году. В ней указывается на возможность применения электрической дуги.
Первый в мире электродуговую сварку осуществил русский инженер Николай Николаевич Бенардос (1842-1904 гг.). Работы над созданием крупных аккумуляторных батарей привели его в 1882 году к изобретению способа электрической дуговой сварки металлов в России и ряде других стран.
Дальнейшее развитее сварки нашло применение в работах Н.Г. Славянова (1854-1897 гг.). С именем Славянова связано развитие металлургических основ электрической сварки и создание метода сварки металлическим электродом. Ему также принадлежит заслуга создания автоматического регулятора длины дуги и первого сварочного генератора.
Н.Г. Славянов на Пермских пушечных заводах, начальником которых он являлся, организовал значительный по тем временам электросварочный цех и выполнявший большое количество сварочных работ с искусством заслуживающий внимание и в настоящее время. С 1891 по 1894 года лично С.Г. Славяновым и под его руководством выполнено ремонтно-сварочных робот на 1631 изделий с общим весом 250 тонн и израсходовано при этом 11 тонн электродов.
Н.Г. Славянов являлся инженером-металлургом, глубоко понимал физико-химическую сущность процессов, происходящих при сварке и разработал ряд флюсов и шлаков, позволяющих получить высококачественный, наплавленный метал.
Развитие сварки можно разделить на три этапа:
-
первый этап с 1924 по 1935 год. Сварочный процесс в то время осуществлялся вручную, электродами без покрытия или с тонким изолирующим покрытием электродов.
-
Второй этап с 1935 по 1940 год. В эти годы сварка широко внедрялась во всех отраслях промышленности на базе применения электродов со специальным покрытием.
-
Третий этап с 1940 года. Этот этап характеризуется максимальным внедрением механизации в сварочный процесс на базе разработанного в 1940 году под руководством Е.О. Патонова современного способа автоматической сварки под слоем флюса.
Большие заслуги в деле развития и совершенствования теории и практики сварочного производства имеют коллективы Института им. Е.О. Патона АНУССР, ЦНИИТМаш, ЛПИ им. Калинина, МВТУ им. Баумана, отраслевых ЦНИИ, завод «Электрик», Кировского, Уралмаш и др.
Применение сварки даёт не только экономию металла (на 20-25%), но и экономию времени и рабочей силы. Разработаны и применяются в некоторых отраслях промышленности новые методы сварки: сварка давлением, трением, ультразвуком, токами высокой частоты, плазменной дугой, сварка электронным лучом в вакууме, диффузионная сварка в вакууме, взрывом, сварка под водой лучом лазера. В ближайшие годы можно достичь серьезных дальнейших успехов в развитие и в промышленном применении новых видов сварки. Произошли достижения в области механизации и автоматизации сварочных процессов, которые позволили поднять на высокий технический уровень изготовление котлов, труб и трубопроводов, морских и речных судов, нефтеаппаратуры, прокатных станков, мощных прессов и насосов и других машин и механизмов.
1 Особенности сварки в среде углекислого газа
Полуавтоматическая сварка в углекислом газе (CO2), выполняется преимущественно плавящимся электродом. В роли плавящегося электрода при использовании сварочного полуавтомата выступают сварочные проволоки сплошного сечения (из низколегированной стали), а также порошковые проволоки.
Активные газы или продукты диссоциации в процессе сварки взаимодействуют с металлом сварочной ванны, растворяются в ней или образуют химические соединения с элементами входящие в состав ванны.
Сварку низколегированными проволоками сплошного сечения ведут, когда используют сварочный полуавтомат, постоянным током обратной полярности. При сварке постоянным током прямой полярности, вследствие более высокого содержания в металле шва водорода, наблюдается интенсивное образование пор. Сварка активной проволокой сплошного сечения возможна и на прямой полярности.
При сварке полуавтоматом порошковой проволокой возможно питание дуги переменным током, если в составе проволоки содержатся вещества, предназначенные для стабилизации дуги. Вследствие того, что углекислый газ является достаточно энергичным окислителем, при высоких температурах, вольфрамовые электроды не представляется возможным использовать, так они просто сгорают. Сварку в защитном, углекислом газе, возможно, выполнять в любых пространственных положениях. При работе с низколегированными либо низкоуглеродистыми сталями также рекомендуется использовать углекислый газ (CO2).
Расширение области применения полуавтоматической электродуговой сварки (MIG/MAG) идёт за счёт замены ручной дуговой сварки покрытыми электродами (MMA) и полуавтоматической сварки под флюсом. Широкое использование электрической сварки в защитном газе взамен ручной дуговой сварки покрытыми электродами обусловлено большей производительностью, лучшими условиями труда и меньшими требованию к квалификации рабочих. Перед полуавтоматической сваркой под флюсом её преимущество заключается в возможности визуального наблюдения за расплавлением электрода, отсутствие операций по удалению и удержанию флюса и возможности выполнять сварку во всех пространственных положениях.
Полуавтоматическая сварка в среде углекислого газа применяется для сварки прерывистых коротких швов и швов, недоступных для сварки автоматом, а также для сварки стыков швеллеров, двутавровых балок и гнутых профилей. Сварка в среде углекислого газа обеспечивает глубокий провар в местах переходов от стенки к полке швеллеров и балок. Для сварки в среде углекислого газа применяют полуавтоматы А-537, А-765, А-1035, позволяющие выполнять швы любого вида.
Производительность сварки в среде углекислого газа выше ручной в полтора раза и на 15—20% выше полуавтоматической под слоем флюса. Кроме того, сварка в среде углекислого газа не требует приспособлений и времени для подачи, удержания и удаления флюса. Это дает возможность производить сварку в любом пространственном положении, обеспечивая глубокий провар.
Недостатком сварки в среде углекислого газа является сильное разбрызгивание металла и посредственное формирование шва. При сварке в открытых помещениях, а также при наличии сквозняков или ветра углекислый газ оттесняется от свариваемых швов, что снижает его защитное действие. В результате в сварных швах могут появиться норы, которые снижают механические свойства наплавленного металла. В замкнутых сосудах сварку швов в среде углекислого газа применять не рекомендуется, так как в процессе сварки образуется значительная концентрация углекислого газа, при которой сварщик может угореть.
Углекислый газ является активным газом. При высоких температурах происходит диссоциация (разложение) его с образованием свободного кислорода:
2СО2 -> 2СО + О2
Молекулярный кислород под действием высокой температуря сварочной дуги диссоциирует на атомарный по формуле:
О2 -> 2О
Атомарный кислород, являясь очень активным, вступает в реакцию с железом и примесями, находящимися в стали, по следующим уравнениям:
Fe + O =FeO,
C + O =CO,
Mn + O =MnO,
Si + 2O = SiО2.
Чтобы подавит реакцию окисления углерода и железа при сварке в углекислом газе, в сварочную ванну вводят раскислители (марганец и кремний), которые тормозят реакции окисления и восстанавливают окислы по уровням:
FeO + Mn = MnO + Fe,
2FeO + Si = SiО2 + 2Fe и т.д.
Образующиеся окислы кремния и марганца переходят в шлак. Исходя из этого при сварке в углекислом газе малоуглеродистых и низкоуглеродистых сталей необходимо применять кремний-марганцовистые проволоки, а для сварки легированных сталей – специальные проволоки.
2 Технология сварки
Подготовка металла под сварку состоит в следующем. Чтобы в наплавленном металле не было пор, кромки сварных соединений необходимо зачищать от ржавчины, грязи, масла и влаги на ширину до 30мм по обе стороны от зазора. В зависимости от степени загрязнения зачищать кромки можно протиркой ветошью, зачисткой стальной щёткой, опескоструиванием, а также обезжириванием с последующим травлением. Следует заметить, что окалина почти не влияет на качество сварного шва, поэтому детали после газовой резки могут свариваться сразу после зачистки шлака.
2.1 Принципы процесса, характеристики дуги
Технологические свойства дуги существенно зависят от физических и химических свойств защитных газов, электродного и свариваемого металлов, параметров и других усло вий сварки. Это обусловливает многообразие способов сварки в защитных газах.
Полуавтоматическая сварка плавящимся электродом производится в инертных газах Аг и Не (MIG) и их смесях Аг + Не, в активном газе СO2 (MAG), а также в смесях инертных и активных Аг + О2, Аг + СО2, Аг + СО + О2 и активных газов СО2 + О2. В качестве электродных проволок применяют сплошные из нелегированных и легированных сталей и цветных металлов (Ni, Си, Mg, Al, Ti, Mo), а также несплошные порошковые и активированные. Сварка плавящимся электродом выполняется в основном на постоянном токе, приме няется также и сварка импульсным током и тока обратной полярности. Находят применение и другие способы сварки: на нормальном и увеличенном вылете, со свободным и принудительным формированием шва, без колебаний и с колебаниями электродной проволоки, в атмосфере и под водой, в стандартную и нестандартную узкую щелевую разделку кромок и др. Принцип дуговой сварки плавящимся металлическим электродом в защитном газе показан на (рис. 5).
Основные типы, конструктивные элементы и размеры сварных соединений из сталей, а также сплавов на железоникелевой и никелевой основах, выполняемых дуговой сваркой в защитном газе указаны в ГОСТ 14771
В зависимости от уровня механизации и автоматизации процесса различают сварку: - механизированную, при которой перемещения горелки выполняются вручную, а подача проволоки механизирована;
- автоматизированную, при которой все перемещения горелки и подача проволоки механи зированы, а управление процессом сварки выполняется оператором-сварщиком;
- автоматическую (роботизированную), при которой управление процессом сварки выполняется без непосредственного участия оператора-сварщика.
Рис.5 Схема полуавтоматической сварки
3 Сварочное оборудование
Шланговые полуавтоматы, предназначенные для сварки в защитных газах, содержа следующие основные элементы: горелку с держателем, шлаг для подвода к горелке электродной или присадочной проволоки, механизм подачи проволоки с катушкой для нее и блок управления полуавтоматом. Эти элементы, отличающиеся конструктивными особенностями, входят во все разновидности полуавтоматов.
Современные механизмы подачи содержат два или несколько подающих роликов различной конструкции и в различных сочетаниях. По расположению подающего механизма различают полуавтоматы толкающего и тянущего типов. В шланговом полуавтомате толкающего типа подача проволоки с катушки осуществляется подающим механизмом, установленным рядом с катушкой. Механизм состоит из электродвигателя переменного или постоянного тока, коробки скоростей, ведущего и прижимного роликов. Проволока подается роликами с постоянной скоростью через внутренний канал гибкого шланга, держатель и наконечник.
Рабочий инструмент полуавтомата – горелка. Примером ее конструкции может служить горелка полуавтомата А-1197П, предназначенного для сварки как обычной проволокой сплошного сечения, так и порошковой проволокой. Горелка содержит изогнутый мундштук с переходной втулкой и наконечником, рукоятку с гашеткой пусковой кнопки, защитный щиток и сопло для создания воны сварки защитной атмосферы.
Одной из основных частей полуавтомата является шланг, состоящий из проволочной спирали с оплеткой и резиновой оболочки. Сварочный ток, защитный ток и охлаждающая вода в современных полуавтоматах подводятся к горелке автономными шлангами. Подача проволоки вперед и назад осуществляется переключением пакетного переключателя, расположенного на блоке управления. Кнопка включения подающего механизма находится на горелке.
4 Устройство полуавтомата
Универсальные полуавтоматы позволяют выполнить быструю переналадку без существенных трудовых и материальных затрат. К универсальным полуавтоматам относят прежде всего модель, применяемую для сварки в среде углекислого газа сплошной или порошковой проволокой. У всех полуавтоматов подача электродной проволоки осуществляется по пустотелому шлангу, поэтому они именуются шланговыми полуавтоматами.
Схематично полуавтомат для сварки в среде защитного газа состоит из следующих основных составные частей - сменная газовая горелка, подающий механизм, шланг подачи электродной проволоки, кассеты для хранения проволоки, газового шланга, блока управления, источника питания, провода цепи управления, газовой аппаратуры, кабеля.
Мы часто упоминаем о сварочной горелке. Вкратце объясним ее устройство. Для этого обратимся к рисунку. Горелка предназначена для подачи в зону горения электродной проволоки и защитного газа.
Рукоятка сварочной горелки должна быть прочной и удобной для работы. С этой целью ее изготавливают из литьевого изоляционного материала. На рукоятке размещены предохранительный щиток и пусковая кнопка. Наиболее ответственными элементами сварочной горелки являются сопло и наконечник, подводящий ток.
-
Сварочная проволока
2. Газовое сопло
3. Токоподводящий мундштук
4. Корпус горелки
5. Рукоять горелки
6. Механизм подачи проволоки
7. Атмосфера защитного газа
8. Сварочная дуга
9. Сварочная ванна
Сопло горелки - на нем из-за высокой температуры постоянно возникает налипание расплавленного металла. Чтобы устранить это, металлическое сопло хромируют или полируют. Есть и другой выход - сопло изготавливают из керамического материала. В случае, если сварочный ток достигает значения 315 А и выше, применяется дополнительное охлаждение сопла горелки. Периодичность смены горелки - через каждые полгода.
Наконечники для подачи тока изготавливаются из меди с гарантированным сроком работы - от 5 до 10 часов непрерывной работы. Если наконечник изготовлен из бронзы,-то срок его службы еще меньше. Изготавливаемые в последнее время медно-гра-фитовые наконечники имеют тоже малый срок службы, но лучше обеспечивают контакт и гарантируют хорошее скольжение, что важно при сварке алюминиевой проволокой.
Только наконечник на медно-вольфрамовой основе обеспечивает более длительную работу без замены.
Полуавтомат ПШП-10 предназначен для дуговой сварки углеродистых, нержавеющих и жаропрочных сталей, алюминиевых сплавов и других металлов плавящимся электродом в среде защитных газов. Полуавтомат позволяет выполнять сварку постоянным током. В его комплект входят катушка с кронштейном и шкаф с электроаппаратурой.
Полуавтомат А-547 предназначен для сварки тонкой электродной проволокой диаметром 0,8-1,0мм.
Полуавтомат А-537 предназначен для сварки электродной проволокой диаметром 1,6-2мм.
Сварочная головка типа ТСГ-7 предназначена для сварки в защитных газах плавящимся колеблющимся электродом поворотных стыков труб из низкоуглеродистых и нержавеющих сталей без подкладных колец.
5 Выбор режимов сварки
К параметрам режима сварки в углекислом газе относятся: род тока и полярность, диаметр электродной проволоки, сила сварочного тока, напряжение дуги, скорость подачи проволоки, вылет электрода, расход углекислого газа, наклон электрода относительно шва и скорость сварки.
При сварке в углекислом газе обычно применяют постоянный ток обратной полярности, так как сварка током прямой полярности приводит к неустойчивому горению дуги. Переменный ток можно применять только с осциллятором, однако в большинстве случаев рекомендуется применять постоянный ток.
Диаметр электродной проволоки следует выбирать в зависимости от толщины свариваемого металла.
Сварочный ток устанавливается в зависимости от выбранного диаметра электродной проволоки.
С увеличением силы сварочного тока увеличивается глубина провара и повышается производительность процесса сварки.
Напряжение дуги зависит от длины дуги. Чем длиннее дуга, тем больше напряжения на ней. С увеличением напряжения дуги увеличивается ширина шва и уменьшается глубина его провара. Устанавливается напряжение дуги в зависимости от выбранной силы сварочного тока.
Скорость подачи электродной проволоки подбирают с таким расчётом, чтобы обеспечивалось устойчивое горение дуги при выбранном напряжении на ней.
Вылетом электрода называется длина отрезка электрода между его концом и выходом его из мундштука. Величина вылета оказывает большое влияние на устойчивость процесса сварки и качества сварного шва . С увеличением вылета ухудшается устойчивость горения дуги и формирования шва, а также увеличивается разбрызгивание. При сварке с очень малым вылетом затрудняется наблюдение за процессом сварки и часто подгорает контактный наконечник. Величину вылета рекомендуется выбирать в зависимости от диаметра электродной проволоки.
Кроме вылета электрода, необходимо выдерживать определённое расстояние от сопла горелки до изделия, так как с увеличением этого расстояния возможно попадание кислорода и азота воздуха в наплавленный металл и образования пор в шве. Величину расстояния от сопла горелки до изделия следует выдерживать в приведенных значениях.
Расход углекислого газа определяют в зависимости от силы тока, скорости сварки, типа соединения и вылета электрода. В среднем газа расходуется от 5 до 20 л/мин. шва. В зависимости от угла наклона сварку можно производить углом назад и углом вперёд.
При сварке углом назад в пределах 5 – 10 град. улучшается видимость зоны сварки, повышается глубина провара и наплавленный металл получается боле плотным.
При сварке углом вперёд труднее наблюдать за формированием шва, но лучше наблюдать за свариваемыми кромками и направлять электрод точно по зазорам. Ширина валика при этом возрастает, а глубина провара уменьшается. Этот способ рекомендуется применять при сварке тонкого металла, где существует опасность сквозного прожога.
Скорость сварки устанавливается самим сварщиком в зависимости от толщины металла и необходимой площади поперечного сечения шва. При слишком большой скорости сварки конец электрода может выйти из-под зоны защиты газом и окислиться на воздухе.
6 Расчет номинальнног тока электродвигателя переносного блока:
где Рном – номинальная мощность электродвигателя, Вт;
U – напряжение, кВ;
cosj – коэффициент мощности;
η – КПД двигателя.
-
Номинальный ток трехфазных нагревательных элементов:
-
Номинальный ток электромагнитов:
где S – полная мощность электромагнита, ВА
6.1 Выбор электромагнитного пускателя
Электромагнитные пускатели необходимо выбирать только для управления силовыми нагрузками. В случае, если электромагнитный пускатель не коммутирует силовые цепи, преимущество при выборе необходимо отдавать промежуточным реле, которые отличаются от электромагнитных пускателей малыми габаритами и низкой потребляемой мощностью.
Электромагнитные пускатели выбирают по следующим условиям:
-
Серия электромагнитного пускателя.
Наибольшее применение в настоящее время находят пускатели серии ПМЛ и ПМ12. Более дорогие, но и более качественные пускатели серии ПМУ и зарубежных фирм производителей «Сименс», «Легранд», «АББ», «Шнайдер Электрик».
-
Величина электромагнитного пускателя (ток нагрузки, который способен включать и выключать пускатель своими главными контактами).
Электромагнитные пускатели бывают 1-й величины (ток главных контактов – 10 и 16А), 2-й величины (25А), 3-й величины (40А), 4-й величины (63А). Если нагрузки выше 63А, то в цепях управления электродвигателями и другими силовыми элементами схемы находят применение электромагнитные контакторы. Ток главных контактов аппарата должен быть больше тока нагрузки.
-
Рабочее напряжение катушки.
Должно соответствовать напряжению цепей управления – стандартные значения напряжения
24 В,
110 В,
220 В,
380 В, DC 24 В.
Введение
Сварочный полуавтомат – оборудование, предназначенное в полуавтоматическом режиме для сварки в среде защитных газов. Этот аппарат при своей относительно невысокой стоимости отличается хорошей мощностью. Подача сварочной проволоки полностью автоматизирована, а вот сам агрегат перемещается вручную. Сварочный полуавтомат обладает массой достоинств. В частности, здесь могут применяться как плавящиеся электроды, так и неплавящиеся. MIG/MAG - режим полуавтоматической сварки плавящейся электродной проволокой в среде углекислого газа или газовых смесей. Кроме того, сварочный полуавтомат, для выполнения широкого спектра работ, может быть оснащен горелками различных типов.
Представленные в нашем каталоге сварочные полуавтоматы – это оборудование высочайшего класса. Мы реализуем аппараты, которые на практике зарекомендовали себя с лучшей стороны и потому пользуются большой популярностью. Все сварочные полуавтоматы соответствуют общепринятым стандартам безопасности и при полном соблюдении правил эксплуатации будут служить длительное время.
В 1802 году В.В. Петров впервые в мире открыл явление электрической дуги и указал на возможность использования тепловой энергии дуги в расплавлении металлов. Он первый построил самую большую для того времени батарею, при помощи которой и проводил свои опыты. Эти замечательные опыты с электрической дугой В.В. Петров опубликовал в 1803 году. В ней указывается на возможность применения электрической дуги.
Первый в мире электродуговую сварку осуществил русский инженер Николай Николаевич Бенардос (1842-1904 гг.). Работы над созданием крупных аккумуляторных батарей привели его в 1882 году к изобретению способа электрической дуговой сварки металлов в России и ряде других стран.
Дальнейшее развитее сварки нашло применение в работах Н.Г. Славянова (1854-1897 гг.). С именем Славянова связано развитие металлургических основ электрической сварки и создание метода сварки металлическим электродом. Ему также принадлежит заслуга создания автоматического регулятора длины дуги и первого сварочного генератора.
Н.Г. Славянов на Пермских пушечных заводах, начальником которых он являлся, организовал значительный по тем временам электросварочный цех и выполнявший большое количество сварочных работ с искусством заслуживающий внимание и в настоящее время. С 1891 по 1894 года лично С.Г. Славяновым и под его руководством выполнено ремонтно-сварочных робот на 1631 изделий с общим весом 250 тонн и израсходовано при этом 11 тонн электродов.
Н.Г. Славянов являлся инженером-металлургом, глубоко понимал физико-химическую сущность процессов, происходящих при сварке и разработал ряд флюсов и шлаков, позволяющих получить высококачественный, наплавленный метал.
Развитие сварки можно разделить на три этапа:
-
первый этап с 1924 по 1935 год. Сварочный процесс в то время осуществлялся вручную, электродами без покрытия или с тонким изолирующим покрытием электродов.
-
Второй этап с 1935 по 1940 год. В эти годы сварка широко внедрялась во всех отраслях промышленности на базе применения электродов со специальным покрытием.
-
Третий этап с 1940 года. Этот этап характеризуется максимальным внедрением механизации в сварочный процесс на базе разработанного в 1940 году под руководством Е.О. Патонова современного способа автоматической сварки под слоем флюса.
Большие заслуги в деле развития и совершенствования теории и практики сварочного производства имеют коллективы Института им. Е.О. Патона АНУССР, ЦНИИТМаш, ЛПИ им. Калинина, МВТУ им. Баумана, отраслевых ЦНИИ, завод «Электрик», Кировского, Уралмаш и др.
Применение сварки даёт не только экономию металла (на 20-25%), но и экономию времени и рабочей силы. Разработаны и применяются в некоторых отраслях промышленности новые методы сварки: сварка давлением, трением, ультразвуком, токами высокой частоты, плазменной дугой, сварка электронным лучом в вакууме, диффузионная сварка в вакууме, взрывом, сварка под водой лучом лазера. В ближайшие годы можно достичь серьезных дальнейших успехов в развитие и в промышленном применении новых видов сварки. Произошли достижения в области механизации и автоматизации сварочных процессов, которые позволили поднять на высокий технический уровень изготовление котлов, труб и трубопроводов, морских и речных судов, нефтеаппаратуры, прокатных станков, мощных прессов и насосов и других машин и механизмов.
1 Особенности сварки в среде углекислого газа
Полуавтоматическая сварка в углекислом газе (CO2), выполняется преимущественно плавящимся электродом. В роли плавящегося электрода при использовании сварочного полуавтомата выступают сварочные проволоки сплошного сечения (из низколегированной стали), а также порошковые проволоки.
Активные газы или продукты диссоциации в процессе сварки взаимодействуют с металлом сварочной ванны, растворяются в ней или образуют химические соединения с элементами входящие в состав ванны.
Сварку низколегированными проволоками сплошного сечения ведут, когда используют сварочный полуавтомат, постоянным током обратной полярности. При сварке постоянным током прямой полярности, вследствие более высокого содержания в металле шва водорода, наблюдается интенсивное образование пор. Сварка активной проволокой сплошного сечения возможна и на прямой полярности.
При сварке полуавтоматом порошковой проволокой возможно питание дуги переменным током, если в составе проволоки содержатся вещества, предназначенные для стабилизации дуги. Вследствие того, что углекислый газ является достаточно энергичным окислителем, при высоких температурах, вольфрамовые электроды не представляется возможным использовать, так они просто сгорают. Сварку в защитном, углекислом газе, возможно, выполнять в любых пространственных положениях. При работе с низколегированными либо низкоуглеродистыми сталями также рекомендуется использовать углекислый газ (CO2).
Расширение области применения полуавтоматической электродуговой сварки (MIG/MAG) идёт за счёт замены ручной дуговой сварки покрытыми электродами (MMA) и полуавтоматической сварки под флюсом. Широкое использование электрической сварки в защитном газе взамен ручной дуговой сварки покрытыми электродами обусловлено большей производительностью, лучшими условиями труда и меньшими требованию к квалификации рабочих. Перед полуавтоматической сваркой под флюсом её преимущество заключается в возможности визуального наблюдения за расплавлением электрода, отсутствие операций по удалению и удержанию флюса и возможности выполнять сварку во всех пространственных положениях.
Полуавтоматическая сварка в среде углекислого газа применяется для сварки прерывистых коротких швов и швов, недоступных для сварки автоматом, а также для сварки стыков швеллеров, двутавровых балок и гнутых профилей. Сварка в среде углекислого газа обеспечивает глубокий провар в местах переходов от стенки к полке швеллеров и балок. Для сварки в среде углекислого газа применяют полуавтоматы А-537, А-765, А-1035, позволяющие выполнять швы любого вида.
Производительность сварки в среде углекислого газа выше ручной в полтора раза и на 15—20% выше полуавтоматической под слоем флюса. Кроме того, сварка в среде углекислого газа не требует приспособлений и времени для подачи, удержания и удаления флюса. Это дает возможность производить сварку в любом пространственном положении, обеспечивая глубокий провар.
Недостатком сварки в среде углекислого газа является сильное разбрызгивание металла и посредственное формирование шва. При сварке в открытых помещениях, а также при наличии сквозняков или ветра углекислый газ оттесняется от свариваемых швов, что снижает его защитное действие. В результате в сварных швах могут появиться норы, которые снижают механические свойства наплавленного металла. В замкнутых сосудах сварку швов в среде углекислого газа применять не рекомендуется, так как в процессе сварки образуется значительная концентрация углекислого газа, при которой сварщик может угореть.
Углекислый газ является активным газом. При высоких температурах происходит диссоциация (разложение) его с образованием свободного кислорода:
2СО2 -> 2СО + О2
Молекулярный кислород под действием высокой температуря сварочной дуги диссоциирует на атомарный по формуле:
О2 -> 2О
Атомарный кислород, являясь очень активным, вступает в реакцию с железом и примесями, находящимися в стали, по следующим уравнениям:
Fe + O =FeO,
C + O =CO,
Mn + O =MnO,
Si + 2O = SiО2.
Чтобы подавит реакцию окисления углерода и железа при сварке в углекислом газе, в сварочную ванну вводят раскислители (марганец и кремний), которые тормозят реакции окисления и восстанавливают окислы по уровням:
FeO + Mn = MnO + Fe,
2FeO + Si = SiО2 + 2Fe и т.д.
Образующиеся окислы кремния и марганца переходят в шлак. Исходя из этого при сварке в углекислом газе малоуглеродистых и низкоуглеродистых сталей необходимо применять кремний-марганцовистые проволоки, а для сварки легированных сталей – специальные проволоки.
2 Технология сварки
Подготовка металла под сварку состоит в следующем. Чтобы в наплавленном металле не было пор, кромки сварных соединений необходимо зачищать от ржавчины, грязи, масла и влаги на ширину до 30мм по обе стороны от зазора. В зависимости от степени загрязнения зачищать кромки можно протиркой ветошью, зачисткой стальной щёткой, опескоструиванием, а также обезжириванием с последующим травлением. Следует заметить, что окалина почти не влияет на качество сварного шва, поэтому детали после газовой резки могут свариваться сразу после зачистки шлака.
2.1 Принципы процесса, характеристики дуги
Технологические свойства дуги существенно зависят от физических и химических свойств защитных газов, электродного и свариваемого металлов, параметров и других усло вий сварки. Это обусловливает многообразие способов сварки в защитных газах.
Полуавтоматическая сварка плавящимся электродом производится в инертных газах Аг и Не (MIG) и их смесях Аг + Не, в активном газе СO2 (MAG), а также в смесях инертных и активных Аг + О2, Аг + СО2, Аг + СО + О2 и активных газов СО2 + О2. В качестве электродных проволок применяют сплошные из нелегированных и легированных сталей и цветных металлов (Ni, Си, Mg, Al, Ti, Mo), а также несплошные порошковые и активированные. Сварка плавящимся электродом выполняется в основном на постоянном токе, приме няется также и сварка импульсным током и тока обратной полярности. Находят применение и другие способы сварки: на нормальном и увеличенном вылете, со свободным и принудительным формированием шва, без колебаний и с колебаниями электродной проволоки, в атмосфере и под водой, в стандартную и нестандартную узкую щелевую разделку кромок и др. Принцип дуговой сварки плавящимся металлическим электродом в защитном газе показан на (рис. 5).
Основные типы, конструктивные элементы и размеры сварных соединений из сталей, а также сплавов на железоникелевой и никелевой основах, выполняемых дуговой сваркой в защитном газе указаны в ГОСТ 14771
В зависимости от уровня механизации и автоматизации процесса различают сварку: - механизированную, при которой перемещения горелки выполняются вручную, а подача проволоки механизирована;
- автоматизированную, при которой все перемещения горелки и подача проволоки механи зированы, а управление процессом сварки выполняется оператором-сварщиком;
- автоматическую (роботизированную), при которой управление процессом сварки выполняется без непосредственного участия оператора-сварщика.
Рис.5 Схема полуавтоматической сварки
3 Сварочное оборудование
Шланговые полуавтоматы, предназначенные для сварки в защитных газах, содержа следующие основные элементы: горелку с держателем, шлаг для подвода к горелке электродной или присадочной проволоки, механизм подачи проволоки с катушкой для нее и блок управления полуавтоматом. Эти элементы, отличающиеся конструктивными особенностями, входят во все разновидности полуавтоматов.
Современные механизмы подачи содержат два или несколько подающих роликов различной конструкции и в различных сочетаниях. По расположению подающего механизма различают полуавтоматы толкающего и тянущего типов. В шланговом полуавтомате толкающего типа подача проволоки с катушки осуществляется подающим механизмом, установленным рядом с катушкой. Механизм состоит из электродвигателя переменного или постоянного тока, коробки скоростей, ведущего и прижимного роликов. Проволока подается роликами с постоянной скоростью через внутренний канал гибкого шланга, держатель и наконечник.
Рабочий инструмент полуавтомата – горелка. Примером ее конструкции может служить горелка полуавтомата А-1197П, предназначенного для сварки как обычной проволокой сплошного сечения, так и порошковой проволокой. Горелка содержит изогнутый мундштук с переходной втулкой и наконечником, рукоятку с гашеткой пусковой кнопки, защитный щиток и сопло для создания воны сварки защитной атмосферы.
Одной из основных частей полуавтомата является шланг, состоящий из проволочной спирали с оплеткой и резиновой оболочки. Сварочный ток, защитный ток и охлаждающая вода в современных полуавтоматах подводятся к горелке автономными шлангами. Подача проволоки вперед и назад осуществляется переключением пакетного переключателя, расположенного на блоке управления. Кнопка включения подающего механизма находится на горелке.
4 Устройство полуавтомата
Универсальные полуавтоматы позволяют выполнить быструю переналадку без существенных трудовых и материальных затрат. К универсальным полуавтоматам относят прежде всего модель, применяемую для сварки в среде углекислого газа сплошной или порошковой проволокой. У всех полуавтоматов подача электродной проволоки осуществляется по пустотелому шлангу, поэтому они именуются шланговыми полуавтоматами.
Схематично полуавтомат для сварки в среде защитного газа состоит из следующих основных составные частей - сменная газовая горелка, подающий механизм, шланг подачи электродной проволоки, кассеты для хранения проволоки, газового шланга, блока управления, источника питания, провода цепи управления, газовой аппаратуры, кабеля.
Мы часто упоминаем о сварочной горелке. Вкратце объясним ее устройство. Для этого обратимся к рисунку. Горелка предназначена для подачи в зону горения электродной проволоки и защитного газа.
Рукоятка сварочной горелки должна быть прочной и удобной для работы. С этой целью ее изготавливают из литьевого изоляционного материала. На рукоятке размещены предохранительный щиток и пусковая кнопка. Наиболее ответственными элементами сварочной горелки являются сопло и наконечник, подводящий ток.
-
Сварочная проволока
2. Газовое сопло
3. Токоподводящий мундштук
4. Корпус горелки
5. Рукоять горелки
6. Механизм подачи проволоки
7. Атмосфера защитного газа
8. Сварочная дуга
9. Сварочная ванна
Сопло горелки - на нем из-за высокой температуры постоянно возникает налипание расплавленного металла. Чтобы устранить это, металлическое сопло хромируют или полируют. Есть и другой выход - сопло изготавливают из керамического материала. В случае, если сварочный ток достигает значения 315 А и выше, применяется дополнительное охлаждение сопла горелки. Периодичность смены горелки - через каждые полгода.
Наконечники для подачи тока изготавливаются из меди с гарантированным сроком работы - от 5 до 10 часов непрерывной работы. Если наконечник изготовлен из бронзы,-то срок его службы еще меньше. Изготавливаемые в последнее время медно-гра-фитовые наконечники имеют тоже малый срок службы, но лучше обеспечивают контакт и гарантируют хорошее скольжение, что важно при сварке алюминиевой проволокой.
Только наконечник на медно-вольфрамовой основе обеспечивает более длительную работу без замены.
Полуавтомат ПШП-10 предназначен для дуговой сварки углеродистых, нержавеющих и жаропрочных сталей, алюминиевых сплавов и других металлов плавящимся электродом в среде защитных газов. Полуавтомат позволяет выполнять сварку постоянным током. В его комплект входят катушка с кронштейном и шкаф с электроаппаратурой.
Полуавтомат А-547 предназначен для сварки тонкой электродной проволокой диаметром 0,8-1,0мм.
Полуавтомат А-537 предназначен для сварки электродной проволокой диаметром 1,6-2мм.
Сварочная головка типа ТСГ-7 предназначена для сварки в защитных газах плавящимся колеблющимся электродом поворотных стыков труб из низкоуглеродистых и нержавеющих сталей без подкладных колец.
5 Выбор режимов сварки
К параметрам режима сварки в углекислом газе относятся: род тока и полярность, диаметр электродной проволоки, сила сварочного тока, напряжение дуги, скорость подачи проволоки, вылет электрода, расход углекислого газа, наклон электрода относительно шва и скорость сварки.
При сварке в углекислом газе обычно применяют постоянный ток обратной полярности, так как сварка током прямой полярности приводит к неустойчивому горению дуги. Переменный ток можно применять только с осциллятором, однако в большинстве случаев рекомендуется применять постоянный ток.
Диаметр электродной проволоки следует выбирать в зависимости от толщины свариваемого металла.
Сварочный ток устанавливается в зависимости от выбранного диаметра электродной проволоки.
С увеличением силы сварочного тока увеличивается глубина провара и повышается производительность процесса сварки.
Напряжение дуги зависит от длины дуги. Чем длиннее дуга, тем больше напряжения на ней. С увеличением напряжения дуги увеличивается ширина шва и уменьшается глубина его провара. Устанавливается напряжение дуги в зависимости от выбранной силы сварочного тока.
Скорость подачи электродной проволоки подбирают с таким расчётом, чтобы обеспечивалось устойчивое горение дуги при выбранном напряжении на ней.
Вылетом электрода называется длина отрезка электрода между его концом и выходом его из мундштука. Величина вылета оказывает большое влияние на устойчивость процесса сварки и качества сварного шва . С увеличением вылета ухудшается устойчивость горения дуги и формирования шва, а также увеличивается разбрызгивание. При сварке с очень малым вылетом затрудняется наблюдение за процессом сварки и часто подгорает контактный наконечник. Величину вылета рекомендуется выбирать в зависимости от диаметра электродной проволоки.
Кроме вылета электрода, необходимо выдерживать определённое расстояние от сопла горелки до изделия, так как с увеличением этого расстояния возможно попадание кислорода и азота воздуха в наплавленный металл и образования пор в шве. Величину расстояния от сопла горелки до изделия следует выдерживать в приведенных значениях.
Расход углекислого газа определяют в зависимости от силы тока, скорости сварки, типа соединения и вылета электрода. В среднем газа расходуется от 5 до 20 л/мин. шва. В зависимости от угла наклона сварку можно производить углом назад и углом вперёд.
При сварке углом назад в пределах 5 – 10 град. улучшается видимость зоны сварки, повышается глубина провара и наплавленный металл получается боле плотным.
При сварке углом вперёд труднее наблюдать за формированием шва, но лучше наблюдать за свариваемыми кромками и направлять электрод точно по зазорам. Ширина валика при этом возрастает, а глубина провара уменьшается. Этот способ рекомендуется применять при сварке тонкого металла, где существует опасность сквозного прожога.
Скорость сварки устанавливается самим сварщиком в зависимости от толщины металла и необходимой площади поперечного сечения шва. При слишком большой скорости сварки конец электрода может выйти из-под зоны защиты газом и окислиться на воздухе.
6 Расчет номинальнног тока электродвигателя переносного блока:
где Рном – номинальная мощность электродвигателя, Вт;
U – напряжение, кВ;
cosj – коэффициент мощности;
η – КПД двигателя.
-
Номинальный ток трехфазных нагревательных элементов:
-
Номинальный ток электромагнитов:
где S – полная мощность электромагнита, ВА
6.1 Выбор электромагнитного пускателя
Электромагнитные пускатели необходимо выбирать только для управления силовыми нагрузками. В случае, если электромагнитный пускатель не коммутирует силовые цепи, преимущество при выборе необходимо отдавать промежуточным реле, которые отличаются от электромагнитных пускателей малыми габаритами и низкой потребляемой мощностью.
Электромагнитные пускатели выбирают по следующим условиям:
-
Серия электромагнитного пускателя.
Наибольшее применение в настоящее время находят пускатели серии ПМЛ и ПМ12. Более дорогие, но и более качественные пускатели серии ПМУ и зарубежных фирм производителей «Сименс», «Легранд», «АББ», «Шнайдер Электрик».
-
Величина электромагнитного пускателя (ток нагрузки, который способен включать и выключать пускатель своими главными контактами).
Электромагнитные пускатели бывают 1-й величины (ток главных контактов – 10 и 16А), 2-й величины (25А), 3-й величины (40А), 4-й величины (63А). Если нагрузки выше 63А, то в цепях управления электродвигателями и другими силовыми элементами схемы находят применение электромагнитные контакторы. Ток главных контактов аппарата должен быть больше тока нагрузки.
-
Рабочее напряжение катушки.
Должно соответствовать напряжению цепей управления – стандартные значения напряжения
24 В,
110 В, 
Введение
Сварочный полуавтомат – оборудование, предназначенное в полуавтоматическом режиме для сварки в среде защитных газов. Этот аппарат при своей относительно невысокой стоимости отличается хорошей мощностью. Подача сварочной проволоки полностью автоматизирована, а вот сам агрегат перемещается вручную. Сварочный полуавтомат обладает массой достоинств. В частности, здесь могут применяться как плавящиеся электроды, так и неплавящиеся. MIG/MAG - режим полуавтоматической сварки плавящейся электродной проволокой в среде углекислого газа или газовых смесей. Кроме того, сварочный полуавтомат, для выполнения широкого спектра работ, может быть оснащен горелками различных типов.
Представленные в нашем каталоге сварочные полуавтоматы – это оборудование высочайшего класса. Мы реализуем аппараты, которые на практике зарекомендовали себя с лучшей стороны и потому пользуются большой популярностью. Все сварочные полуавтоматы соответствуют общепринятым стандартам безопасности и при полном соблюдении правил эксплуатации будут служить длительное время.
В 1802 году В.В. Петров впервые в мире открыл явление электрической дуги и указал на возможность использования тепловой энергии дуги в расплавлении металлов. Он первый построил самую большую для того времени батарею, при помощи которой и проводил свои опыты. Эти замечательные опыты с электрической дугой В.В. Петров опубликовал в 1803 году. В ней указывается на возможность применения электрической дуги.
Первый в мире электродуговую сварку осуществил русский инженер Николай Николаевич Бенардос (1842-1904 гг.). Работы над созданием крупных аккумуляторных батарей привели его в 1882 году к изобретению способа электрической дуговой сварки металлов в России и ряде других стран.
Дальнейшее развитее сварки нашло применение в работах Н.Г. Славянова (1854-1897 гг.). С именем Славянова связано развитие металлургических основ электрической сварки и создание метода сварки металлическим электродом. Ему также принадлежит заслуга создания автоматического регулятора длины дуги и первого сварочного генератора.
Н.Г. Славянов на Пермских пушечных заводах, начальником которых он являлся, организовал значительный по тем временам электросварочный цех и выполнявший большое количество сварочных работ с искусством заслуживающий внимание и в настоящее время. С 1891 по 1894 года лично С.Г. Славяновым и под его руководством выполнено ремонтно-сварочных робот на 1631 изделий с общим весом 250 тонн и израсходовано при этом 11 тонн электродов.
Н.Г. Славянов являлся инженером-металлургом, глубоко понимал физико-химическую сущность процессов, происходящих при сварке и разработал ряд флюсов и шлаков, позволяющих получить высококачественный, наплавленный метал.
Развитие сварки можно разделить на три этапа:
-
первый этап с 1924 по 1935 год. Сварочный процесс в то время осуществлялся вручную, электродами без покрытия или с тонким изолирующим покрытием электродов. -
Второй этап с 1935 по 1940 год. В эти годы сварка широко внедрялась во всех отраслях промышленности на базе применения электродов со специальным покрытием. -
Третий этап с 1940 года. Этот этап характеризуется максимальным внедрением механизации в сварочный процесс на базе разработанного в 1940 году под руководством Е.О. Патонова современного способа автоматической сварки под слоем флюса.
Большие заслуги в деле развития и совершенствования теории и практики сварочного производства имеют коллективы Института им. Е.О. Патона АНУССР, ЦНИИТМаш, ЛПИ им. Калинина, МВТУ им. Баумана, отраслевых ЦНИИ, завод «Электрик», Кировского, Уралмаш и др.
Применение сварки даёт не только экономию металла (на 20-25%), но и экономию времени и рабочей силы. Разработаны и применяются в некоторых отраслях промышленности новые методы сварки: сварка давлением, трением, ультразвуком, токами высокой частоты, плазменной дугой, сварка электронным лучом в вакууме, диффузионная сварка в вакууме, взрывом, сварка под водой лучом лазера. В ближайшие годы можно достичь серьезных дальнейших успехов в развитие и в промышленном применении новых видов сварки. Произошли достижения в области механизации и автоматизации сварочных процессов, которые позволили поднять на высокий технический уровень изготовление котлов, труб и трубопроводов, морских и речных судов, нефтеаппаратуры, прокатных станков, мощных прессов и насосов и других машин и механизмов.
1 Особенности сварки в среде углекислого газа
Полуавтоматическая сварка в углекислом газе (CO2), выполняется преимущественно плавящимся электродом. В роли плавящегося электрода при использовании сварочного полуавтомата выступают сварочные проволоки сплошного сечения (из низколегированной стали), а также порошковые проволоки.
Активные газы или продукты диссоциации в процессе сварки взаимодействуют с металлом сварочной ванны, растворяются в ней или образуют химические соединения с элементами входящие в состав ванны.
Сварку низколегированными проволоками сплошного сечения ведут, когда используют сварочный полуавтомат, постоянным током обратной полярности. При сварке постоянным током прямой полярности, вследствие более высокого содержания в металле шва водорода, наблюдается интенсивное образование пор. Сварка активной проволокой сплошного сечения возможна и на прямой полярности.
При сварке полуавтоматом порошковой проволокой возможно питание дуги переменным током, если в составе проволоки содержатся вещества, предназначенные для стабилизации дуги. Вследствие того, что углекислый газ является достаточно энергичным окислителем, при высоких температурах, вольфрамовые электроды не представляется возможным использовать, так они просто сгорают. Сварку в защитном, углекислом газе, возможно, выполнять в любых пространственных положениях. При работе с низколегированными либо низкоуглеродистыми сталями также рекомендуется использовать углекислый газ (CO2).
Расширение области применения полуавтоматической электродуговой сварки (MIG/MAG) идёт за счёт замены ручной дуговой сварки покрытыми электродами (MMA) и полуавтоматической сварки под флюсом. Широкое использование электрической сварки в защитном газе взамен ручной дуговой сварки покрытыми электродами обусловлено большей производительностью, лучшими условиями труда и меньшими требованию к квалификации рабочих. Перед полуавтоматической сваркой под флюсом её преимущество заключается в возможности визуального наблюдения за расплавлением электрода, отсутствие операций по удалению и удержанию флюса и возможности выполнять сварку во всех пространственных положениях.
Полуавтоматическая сварка в среде углекислого газа применяется для сварки прерывистых коротких швов и швов, недоступных для сварки автоматом, а также для сварки стыков швеллеров, двутавровых балок и гнутых профилей. Сварка в среде углекислого газа обеспечивает глубокий провар в местах переходов от стенки к полке швеллеров и балок. Для сварки в среде углекислого газа применяют полуавтоматы А-537, А-765, А-1035, позволяющие выполнять швы любого вида.
Производительность сварки в среде углекислого газа выше ручной в полтора раза и на 15—20% выше полуавтоматической под слоем флюса. Кроме того, сварка в среде углекислого газа не требует приспособлений и времени для подачи, удержания и удаления флюса. Это дает возможность производить сварку в любом пространственном положении, обеспечивая глубокий провар.
Недостатком сварки в среде углекислого газа является сильное разбрызгивание металла и посредственное формирование шва. При сварке в открытых помещениях, а также при наличии сквозняков или ветра углекислый газ оттесняется от свариваемых швов, что снижает его защитное действие. В результате в сварных швах могут появиться норы, которые снижают механические свойства наплавленного металла. В замкнутых сосудах сварку швов в среде углекислого газа применять не рекомендуется, так как в процессе сварки образуется значительная концентрация углекислого газа, при которой сварщик может угореть.
Углекислый газ является активным газом. При высоких температурах происходит диссоциация (разложение) его с образованием свободного кислорода:
2СО2 -> 2СО + О2
Молекулярный кислород под действием высокой температуря сварочной дуги диссоциирует на атомарный по формуле:
О2 -> 2О
Атомарный кислород, являясь очень активным, вступает в реакцию с железом и примесями, находящимися в стали, по следующим уравнениям:
Fe + O =FeO,
C + O =CO,
Mn + O =MnO,
Si + 2O = SiО2.
Чтобы подавит реакцию окисления углерода и железа при сварке в углекислом газе, в сварочную ванну вводят раскислители (марганец и кремний), которые тормозят реакции окисления и восстанавливают окислы по уровням:
FeO + Mn = MnO + Fe,
2FeO + Si = SiО2 + 2Fe и т.д.
Образующиеся окислы кремния и марганца переходят в шлак. Исходя из этого при сварке в углекислом газе малоуглеродистых и низкоуглеродистых сталей необходимо применять кремний-марганцовистые проволоки, а для сварки легированных сталей – специальные проволоки.
2 Технология сварки
Подготовка металла под сварку состоит в следующем. Чтобы в наплавленном металле не было пор, кромки сварных соединений необходимо зачищать от ржавчины, грязи, масла и влаги на ширину до 30мм по обе стороны от зазора. В зависимости от степени загрязнения зачищать кромки можно протиркой ветошью, зачисткой стальной щёткой, опескоструиванием, а также обезжириванием с последующим травлением. Следует заметить, что окалина почти не влияет на качество сварного шва, поэтому детали после газовой резки могут свариваться сразу после зачистки шлака.
2.1 Принципы процесса, характеристики дуги
Технологические свойства дуги существенно зависят от физических и химических свойств защитных газов, электродного и свариваемого металлов, параметров и других усло вий сварки. Это обусловливает многообразие способов сварки в защитных газах.
Полуавтоматическая сварка плавящимся электродом производится в инертных газах Аг и Не (MIG) и их смесях Аг + Не, в активном газе СO2 (MAG), а также в смесях инертных и активных Аг + О2, Аг + СО2, Аг + СО + О2 и активных газов СО2 + О2. В качестве электродных проволок применяют сплошные из нелегированных и легированных сталей и цветных металлов (Ni, Си, Mg, Al, Ti, Mo), а также несплошные порошковые и активированные. Сварка плавящимся электродом выполняется в основном на постоянном токе, приме няется также и сварка импульсным током и тока обратной полярности. Находят применение и другие способы сварки: на нормальном и увеличенном вылете, со свободным и принудительным формированием шва, без колебаний и с колебаниями электродной проволоки, в атмосфере и под водой, в стандартную и нестандартную узкую щелевую разделку кромок и др. Принцип дуговой сварки плавящимся металлическим электродом в защитном газе показан на (рис. 5).
Основные типы, конструктивные элементы и размеры сварных соединений из сталей, а также сплавов на железоникелевой и никелевой основах, выполняемых дуговой сваркой в защитном газе указаны в ГОСТ 14771
В зависимости от уровня механизации и автоматизации процесса различают сварку: - механизированную, при которой перемещения горелки выполняются вручную, а подача проволоки механизирована;
- автоматизированную, при которой все перемещения горелки и подача проволоки механи зированы, а управление процессом сварки выполняется оператором-сварщиком;
- автоматическую (роботизированную), при которой управление процессом сварки выполняется без непосредственного участия оператора-сварщика.
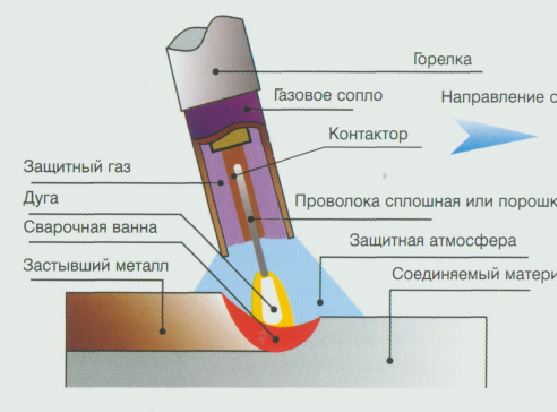
Рис.5 Схема полуавтоматической сварки
3 Сварочное оборудование
Шланговые полуавтоматы, предназначенные для сварки в защитных газах, содержа следующие основные элементы: горелку с держателем, шлаг для подвода к горелке электродной или присадочной проволоки, механизм подачи проволоки с катушкой для нее и блок управления полуавтоматом. Эти элементы, отличающиеся конструктивными особенностями, входят во все разновидности полуавтоматов.
Современные механизмы подачи содержат два или несколько подающих роликов различной конструкции и в различных сочетаниях. По расположению подающего механизма различают полуавтоматы толкающего и тянущего типов. В шланговом полуавтомате толкающего типа подача проволоки с катушки осуществляется подающим механизмом, установленным рядом с катушкой. Механизм состоит из электродвигателя переменного или постоянного тока, коробки скоростей, ведущего и прижимного роликов. Проволока подается роликами с постоянной скоростью через внутренний канал гибкого шланга, держатель и наконечник.
Рабочий инструмент полуавтомата – горелка. Примером ее конструкции может служить горелка полуавтомата А-1197П, предназначенного для сварки как обычной проволокой сплошного сечения, так и порошковой проволокой. Горелка содержит изогнутый мундштук с переходной втулкой и наконечником, рукоятку с гашеткой пусковой кнопки, защитный щиток и сопло для создания воны сварки защитной атмосферы.
Одной из основных частей полуавтомата является шланг, состоящий из проволочной спирали с оплеткой и резиновой оболочки. Сварочный ток, защитный ток и охлаждающая вода в современных полуавтоматах подводятся к горелке автономными шлангами. Подача проволоки вперед и назад осуществляется переключением пакетного переключателя, расположенного на блоке управления. Кнопка включения подающего механизма находится на горелке.
4 Устройство полуавтомата
Универсальные полуавтоматы позволяют выполнить быструю переналадку без существенных трудовых и материальных затрат. К универсальным полуавтоматам относят прежде всего модель, применяемую для сварки в среде углекислого газа сплошной или порошковой проволокой. У всех полуавтоматов подача электродной проволоки осуществляется по пустотелому шлангу, поэтому они именуются шланговыми полуавтоматами.
Схематично полуавтомат для сварки в среде защитного газа состоит из следующих основных составные частей - сменная газовая горелка, подающий механизм, шланг подачи электродной проволоки, кассеты для хранения проволоки, газового шланга, блока управления, источника питания, провода цепи управления, газовой аппаратуры, кабеля.
Мы часто упоминаем о сварочной горелке. Вкратце объясним ее устройство. Для этого обратимся к рисунку. Горелка предназначена для подачи в зону горения электродной проволоки и защитного газа.
Рукоятка сварочной горелки должна быть прочной и удобной для работы. С этой целью ее изготавливают из литьевого изоляционного материала. На рукоятке размещены предохранительный щиток и пусковая кнопка. Наиболее ответственными элементами сварочной горелки являются сопло и наконечник, подводящий ток.
-
Сварочная проволока
2. Газовое сопло
3. Токоподводящий мундштук
4. Корпус горелки
5. Рукоять горелки
6. Механизм подачи проволоки
7. Атмосфера защитного газа
8. Сварочная дуга
9. Сварочная ванна
Сопло горелки - на нем из-за высокой температуры постоянно возникает налипание расплавленного металла. Чтобы устранить это, металлическое сопло хромируют или полируют. Есть и другой выход - сопло изготавливают из керамического материала. В случае, если сварочный ток достигает значения 315 А и выше, применяется дополнительное охлаждение сопла горелки. Периодичность смены горелки - через каждые полгода.
Наконечники для подачи тока изготавливаются из меди с гарантированным сроком работы - от 5 до 10 часов непрерывной работы. Если наконечник изготовлен из бронзы,-то срок его службы еще меньше. Изготавливаемые в последнее время медно-гра-фитовые наконечники имеют тоже малый срок службы, но лучше обеспечивают контакт и гарантируют хорошее скольжение, что важно при сварке алюминиевой проволокой.
Только наконечник на медно-вольфрамовой основе обеспечивает более длительную работу без замены.
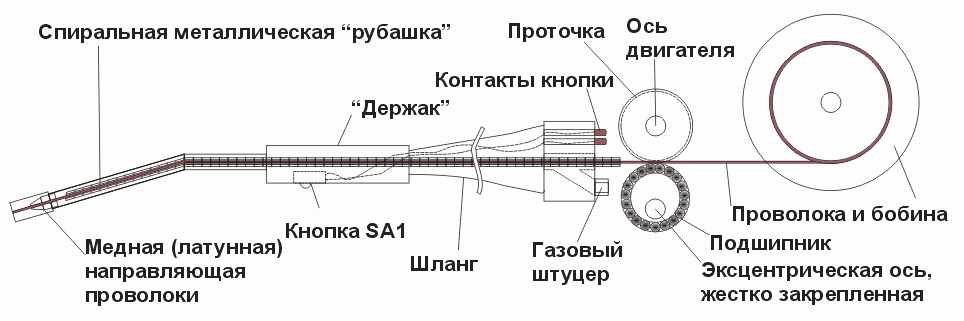
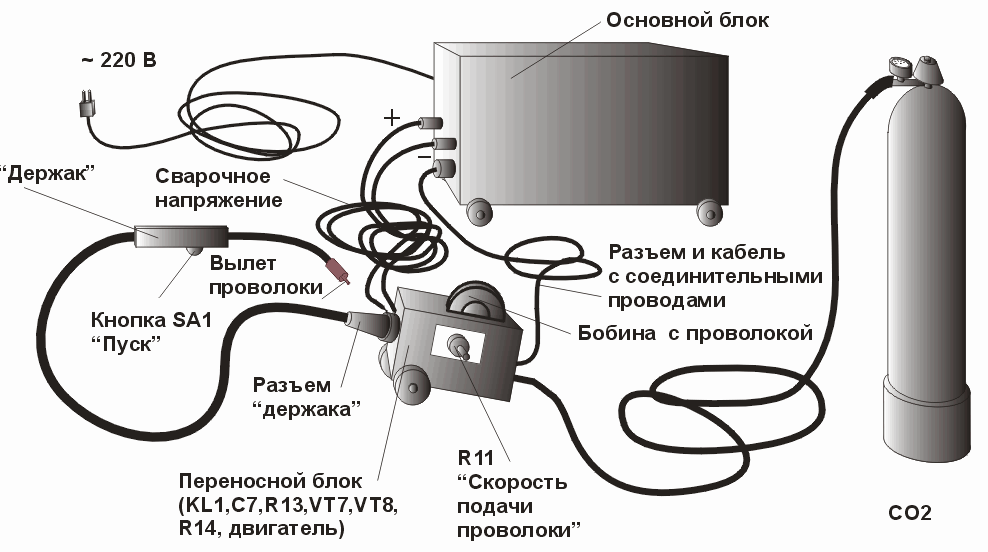
Полуавтомат ПШП-10 предназначен для дуговой сварки углеродистых, нержавеющих и жаропрочных сталей, алюминиевых сплавов и других металлов плавящимся электродом в среде защитных газов. Полуавтомат позволяет выполнять сварку постоянным током. В его комплект входят катушка с кронштейном и шкаф с электроаппаратурой.
Полуавтомат А-547 предназначен для сварки тонкой электродной проволокой диаметром 0,8-1,0мм.
Полуавтомат А-537 предназначен для сварки электродной проволокой диаметром 1,6-2мм.
Сварочная головка типа ТСГ-7 предназначена для сварки в защитных газах плавящимся колеблющимся электродом поворотных стыков труб из низкоуглеродистых и нержавеющих сталей без подкладных колец.
5 Выбор режимов сварки
К параметрам режима сварки в углекислом газе относятся: род тока и полярность, диаметр электродной проволоки, сила сварочного тока, напряжение дуги, скорость подачи проволоки, вылет электрода, расход углекислого газа, наклон электрода относительно шва и скорость сварки.
При сварке в углекислом газе обычно применяют постоянный ток обратной полярности, так как сварка током прямой полярности приводит к неустойчивому горению дуги. Переменный ток можно применять только с осциллятором, однако в большинстве случаев рекомендуется применять постоянный ток.
Диаметр электродной проволоки следует выбирать в зависимости от толщины свариваемого металла.
Сварочный ток устанавливается в зависимости от выбранного диаметра электродной проволоки.
С увеличением силы сварочного тока увеличивается глубина провара и повышается производительность процесса сварки.
Напряжение дуги зависит от длины дуги. Чем длиннее дуга, тем больше напряжения на ней. С увеличением напряжения дуги увеличивается ширина шва и уменьшается глубина его провара. Устанавливается напряжение дуги в зависимости от выбранной силы сварочного тока.
Скорость подачи электродной проволоки подбирают с таким расчётом, чтобы обеспечивалось устойчивое горение дуги при выбранном напряжении на ней.
Вылетом электрода называется длина отрезка электрода между его концом и выходом его из мундштука. Величина вылета оказывает большое влияние на устойчивость процесса сварки и качества сварного шва . С увеличением вылета ухудшается устойчивость горения дуги и формирования шва, а также увеличивается разбрызгивание. При сварке с очень малым вылетом затрудняется наблюдение за процессом сварки и часто подгорает контактный наконечник. Величину вылета рекомендуется выбирать в зависимости от диаметра электродной проволоки.
Кроме вылета электрода, необходимо выдерживать определённое расстояние от сопла горелки до изделия, так как с увеличением этого расстояния возможно попадание кислорода и азота воздуха в наплавленный металл и образования пор в шве. Величину расстояния от сопла горелки до изделия следует выдерживать в приведенных значениях.
Расход углекислого газа определяют в зависимости от силы тока, скорости сварки, типа соединения и вылета электрода. В среднем газа расходуется от 5 до 20 л/мин. шва. В зависимости от угла наклона сварку можно производить углом назад и углом вперёд.
При сварке углом назад в пределах 5 – 10 град. улучшается видимость зоны сварки, повышается глубина провара и наплавленный металл получается боле плотным.
При сварке углом вперёд труднее наблюдать за формированием шва, но лучше наблюдать за свариваемыми кромками и направлять электрод точно по зазорам. Ширина валика при этом возрастает, а глубина провара уменьшается. Этот способ рекомендуется применять при сварке тонкого металла, где существует опасность сквозного прожога.
Скорость сварки устанавливается самим сварщиком в зависимости от толщины металла и необходимой площади поперечного сечения шва. При слишком большой скорости сварки конец электрода может выйти из-под зоны защиты газом и окислиться на воздухе.
6 Расчет номинальнног тока электродвигателя переносного блока:

где Рном – номинальная мощность электродвигателя, Вт;
U – напряжение, кВ;
cosj – коэффициент мощности;
η – КПД двигателя.
-
Номинальный ток трехфазных нагревательных элементов:
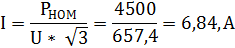
-
Номинальный ток электромагнитов:


где S – полная мощность электромагнита, ВА
6.1 Выбор электромагнитного пускателя
Электромагнитные пускатели необходимо выбирать только для управления силовыми нагрузками. В случае, если электромагнитный пускатель не коммутирует силовые цепи, преимущество при выборе необходимо отдавать промежуточным реле, которые отличаются от электромагнитных пускателей малыми габаритами и низкой потребляемой мощностью.
Электромагнитные пускатели выбирают по следующим условиям:
-
Серия электромагнитного пускателя.
Наибольшее применение в настоящее время находят пускатели серии ПМЛ и ПМ12. Более дорогие, но и более качественные пускатели серии ПМУ и зарубежных фирм производителей «Сименс», «Легранд», «АББ», «Шнайдер Электрик».
-
Величина электромагнитного пускателя (ток нагрузки, который способен включать и выключать пускатель своими главными контактами).
Электромагнитные пускатели бывают 1-й величины (ток главных контактов – 10 и 16А), 2-й величины (25А), 3-й величины (40А), 4-й величины (63А). Если нагрузки выше 63А, то в цепях управления электродвигателями и другими силовыми элементами схемы находят применение электромагнитные контакторы. Ток главных контактов аппарата должен быть больше тока нагрузки.
-
Рабочее напряжение катушки.
Должно соответствовать напряжению цепей управления – стандартные значения напряжения
-
Количество дополнительных контактов электромагнитного пускателя.
Должно соответствовать необходимому числу контактов в схеме управления. Отдельно необходимо считать контакты замыкающие и размыкающие. В случае, если количество контактов оказывается аппарата оказывается меньше необходимого и в качестве аппарата была выбрана серия ПМЛ, то существует возможность использовать приставку с дополнительными контактами серии ПКЛ.
-
Степень защиты, IP.
Электромагнитный пускатель должен соответствовать условиям окружающей среды в которой он работает. Необходимо учитывать то, что аппарат установленный в пыльном помещении, но находящийся в шкафу управления со степенью защиты IP44, может иметь степень защиты IP20.
-
Наличие теплового реле.
Если электромагнитный пускатель включает и выключает электродвигатели, которые по своим технологическим режимам могут испытывать перегрузки, то необходимо выбирать аппарат с тепловыми реле.
-
Наличие реверса.
Для управления реверсивным электродвигателем существует возможность использовать реверсивный магнитный пускатель, который содержит 2 электромагнитных катушки, 6 силовых контактов, механическую блокировку и может иметь 2 тепловых реле.
-
Дополнительные элементы управления (кнопки на корпусе, лампочка). -
Класс износостойкости (количество срабатываний).
Важный параметр в том случае, когда аппарат предназначен для коммутации нагрузки, работающей в режиме частых включений и выключений. При большом значении количества вкл/выкл в час используют бесконтактные пускатели.
Таблица 4. Результаты выбора магнитных пускателей
Позиционные обозначения и типы | Напр-ние главных контактов, В | Ток главных контактов, А | Число главных контактов зам./разм | Число вспом. контактов зам./разм | Напряжение катушки, В | |
КМ1 ПМЛ-150104 с приставкой ПКЛ-2004 (+2 з.) | требуется | 65 | 5 | 3/0 | 2/1 | 110 |
| выбрано | 380 | 10 | 3/0 | 2/1 | 110 |
6.2 Выбор промежуточных реле
Реле – электрическое устройство (выключатель), предназначенное для замыкания и размыкания различных участков электрических цепей при заданных изменениях электрических или неэлектрических входных величин. Различают электрические, механические и тепловые реле.
Основные части электромагнитного реле: электромагнит, якорь и переключатель. Электромагнит представляет собой электрический провод, намотанный на катушку с сердечником из магнитного материала. Якорь – пластина из магнитного материала, через толкатель управляющая контактами.
Таблица 5. Результат выбора промежуточных реле
Позиционные обозначения и типы | Число замыкающих контактов | Число размыкающих Контактов | Напряжение катушки, В | Степень защиты | |
КV1 РПЛ-131 с приставкойПКЛ-22М (2 з.+1 р.) | требуется | 4 | 2 | 380 | IP20 |
| выбрано | 5 | 2 | 380 | IP20 |
6.3 Выбор трансформатора
Трансформатор (преобразовывать) – это статическое электромагнитное устройство, имеющее две или более индуктивно связанные обмотки на каком-либо магнитопроводе и предназначенное для преобразования посредством электромагнитной индукции одной или нескольких систем (напряжений) переменного или постоянного тока в одну или несколько других систем (напряжений), без изменения частоты.
1. Расчет полной мощности:

где Рном – номинальная мощность электродвигателя, Вт;
cosj – коэффициент мощности;
2. Расчет номинальной мощности трансформатора:

где



Из таблицы П5.1 справочника выбираем двухобмоточный трансформатор 2хТМ25/6.
6.4 Выбор предохранителей
Iном

где Рном – номинальная мощность электродвигателя, Вт;
U – напряжение, кВ;
cosj – коэффициент мощности;
η – КПД двигателя.
Таблица 8. Выбор предохранителя
Позиционное обозначение | Тип предохранителя | | Напряжение, В | Номинальный ток, А | Номинальный ток плавкой ставки, А | | |
FU1 | ПРС-25 | требуется | 380 | 17,41 | 25 | ||
| выбрано | 380 | 25 |
7 Расчет и выбор проводов и кабелей
Для питания электродвигателя, выбираем провод в соответствии с условием:
I≤

Для питания электромагнита выбираем провод ВВГ 1,5, т.к. номинальный ток электромагнита равен

Для питания 3-х фазных нагревательных элементов используем провод ВВГ 1,5, т.к. номинальный ток нагревательных элементов равен 6,08 А. По этому проводу может течь длительно допустимый ток в величине 19 А.
8 Охрана труда и техника безопасности при выполнении сварочных работ
Состояние изоляции проводов проверяют не реже одного раза в месяц, а осмотр подвижных контактов, переключателей, рубильников и клемм - не реже одного раза в три дня. Напряжение холостого хода на зажимах генератора или трансформатора не должно превышать 110 В для машин постоянного тока и 70 В для машин переменного тока. Сварочные машины должны находиться под наблюдением специалистов. Установку и ремонт их могут производить только электромонтеры.
Корпусы сварочной аппаратуры и источников тока необходимо заземлять. Кроме того, обязательно должно быть заземлено свариваемое изделие. Заземление сварочных агрегатов на контур производят присоединением медного провода сечением не менее 6 мм2 или железного сечением не менее 12 мм2 к какой-либо точке корпуса и к трубе диаметром 37--50 мм, длиной 1--2 м. Трубу закапывают в землю. Вместо трубы можно использовать полосовую сталь толщиной не менее 4 мм, сечением 48--50 мм2.
Категорически запрещается использовать контур заземления в качестве обратного провода сварочной цепи. При появлении напряжения на частях аппаратуры и оборудования, не являющихся токоведущими, необходимо прекратить сварку и вызвать мастера или дежурного электрика. Номинальная сила тока плавких предохранителей не должна превышать указанного в схеме.
При ручной электродуговой сварке несчастные случаи могут быть в результате поражения электрическим током, светового излучения дуги, а также в результате ожогов каплями металла и шлака.
Поражение электрическим током. В результате действия электрического тока на организм могут быть повреждены нервная система (электрический удар) или кожный покров (ожоги). Характер и степень поражения зависят от величины силы тока и сопротивления тела человека. Сила тока до 0,002 А переносится безболезненно, а 0,05 А -- является опасной. Более высокая сила тока может вызвать смерть. Чем выше напряжение и ниже сопротивление, тем сильнее будет поражение током. В сухих помещениях при нормальных условиях работы и исправной сухой одежде и обуви напряжение ниже 36 В, а в сырых помещениях ниже 12 В -- безопасно, более высокое напряжение опасно, наибольшую опасность представляет двухполюсное прикосновение (рис. 89).
При работах внутри резервуаров рабочего снабжают резиновым ковриком, а также резиновым шлемом для защиты головы от случайных прикосновений к металлическим частям, находящимся под напряжением. Электрододержатель должен иметь механическую или электрическую блокировку, исключающую смену электрода при невыключенном токе. Сварщика, работающего в резервуаре, должен сопровождать наблюдатель, находящийся снаружи, который должен и может оказать сварщику при несчастном случае необходимую помощь.
В случае поражения током пострадавшему необходимо оказать следующую помощь: отсоединить его от проводов, предварительно надев резиновые рукавицы или встав на резиновый коврик (ток можно выключить также рубильником, вывертыванием предохранительной пробки или замыканием проводов накоротко, в результате чего перегорят предохранители), обеспечить пострадавшему доступ свежего воздуха (открыть окна и двери или вынести его на улицу); если пострадавший потерял сознание, нужно немедленно вызвать медицинскую помощь, до прибытия врача пострадавшему необходимо производить искусственное дыхание.