Файл: Организация монтажа, наладки и технического обслуживания кип системы.docx
ВУЗ: Не указан
Категория: Не указан
Дисциплина: Не указана
Добавлен: 30.11.2023
Просмотров: 350
Скачиваний: 12
ВНИМАНИЕ! Если данный файл нарушает Ваши авторские права, то обязательно сообщите нам.
СОДЕРЖАНИЕ
Глава Ⅰ. Описание технологического процесса системы автоматизации перемещения грузов на предприятии
1.4. Требования к обслуживающему персоналу
Глава Ⅱ. Подготовка к производству монтажных и наладочных работ
2.1. Автоматизация в области транспортных операции
Глава III. Автоматизация ленточных конвейеров и конвейерных линий
2.1. Автоматизация в области транспортных операции
Транспортирующие машины непрерывного действия, характерные постоянным режимом непрерывной работы по строго определенной трассе и объединенные в единый транспортный комплекс, более чем другие подъемно-транспортные машины, пригодны для широкого применения автоматизации.
В отдельных агрегатах и системах (комплексах) транспортирующих машин возможна автоматизация следующих операций.
1.Дистанционное управление работой комплекса последовательно расположенных транспортирующих машин с применением автоматических устройств. Эта задача включает в себя: а) последовательный автоматизированный пуск и остановку группы конвейеров транспортной системы с центрального пульта управления; б) автоматический контроль вступления в работу (и выключения) каждого конвейера системы с необходимой выдержкой времени, обеспечивающий нормальное непрерывное движение транспортируемого груза. Пуск системы конвейеров производят, в обратной последовательности движению груза: первым пускают последний конвейер последовательной системы, за ним автоматически включается расположенный перед ним конвейер и последним -- первый конвейер системы, чтобы обеспечить подачу груза без завалов на уже работающую машину. Остановку системы конвейеров осуществляют в обратном порядке; сначала останавливают первый, загружающий конвейер, затем последовательно, автоматически, с необходимой выдержкой времени, достаточной для освобождения конвейера от находящегося на нем груза, останавливаются последующие (по потоку груза) конвейеры, вплоть до последа него, который останавливается после полного освобождения его от груза.
В эту задачу входит также автоматический контроль работы каждой машины системы и её выключение при появлении той или иной ненормальности, например чрезмерной пробуксовки ленты на приводном барабане конвейера, завале перегрузочной воронки, обрыве ленты или цепи. Сигналы об этом поступают автоматически на центральный пульт от разнообразных датчиков контроля, установленных на машинах. В эту же задачу входит автоматизация обеспечения оптимального режима работы системы, например, путем регулирования скорости движения груза
, с целью обеспечения постоянства нагрузки на рабочий элемент машины. Такая автоматика успешно внедряется на комплексных системах механизации транспорта литейных цехов, обогатительных фабрик, на топливоподаче и т. п.
Автоматизация управления работой отдельной машины или системой машин с центрального пульта по заданной программе, как часть автоматизации всего технологического процесса производства на предприятии. Эта задача имеет очень широкие перспективы и возможности; внедрение такой автоматики необходимо во многих отраслях промышленности. При решении этой задачи перспективно применение электронных цифровых машин с целью установления оптимальных режимов работы транспортирующей машины или системы транспортирующих и технологических машин.
Автоматизация операций загрузки, разгрузки и распределения грузов (автоматическое адресование грузов) по заданным пунктам-адресам на общей транспортной трассе машины или системы машин с центрального пульта управления по заданной программе или по командам рабочих-операторов. К этой же задаче относится автоматическое накопление (складирование) грузов и выдача их в производство по командам с цен трального пульта управления или по требованиям с отдельных производственных участков.
Автоматическая сортировка транспортируемых грузов по различным характерным признакам: цвету, высоте, весу, заданным кодовым отметкам и т. п.
Автоматическое выполнение отдельных вспомогательных технологических операций при непрерывном движении грузов: взвешивание, дозирование по весу и объёму, счёт (учёт) в целом и по отдельным видам грузов.
6. Автоматический контроль заполнения емкостей бункеров и подвесных складов, автоматическая выдача грузов в зависимости от заполнения, автоматическое управление загрузочными механизмами в зависимости от заполнения емкостей.
Перечисленные задачи далеко не полностью исчерпывают возможный объем работ по автоматизации транспортирующих машин и охватывают только основные вопросы. Способы выполнения указанных задач разнообразны, в некоторой части они кратко рассматриваются в последующих главах книги. Более подробное их рассмотрение является предметом специального курса.
Несмотря на широкие возможности автоматизации транспортирующих машин, конкретное осуществление и внедрение перечисленных задач является сложной проблемой. Основные трудности заключаются в широком разнообразии производственных условий работы транспортирующих машин и большом количестве их конструктивных типов. Для широкого и успешного внедрения автоматизации необходимы совместные усилия специалистов машиностроителей (механиков) и автоматчиков. Машиностроители должны обеспечить высокую надежность машин и простоту их обслуживания в тяжелых условиях эксплуатации. Для автоматической работы машины или комплекса машин недостаточно только установить необходимые приборы автоматического управления, очень важно и необходимо обеспечить длительную непрерывную и надежную работу машины при минимальном количестве обслуживающего персонала. Для выполнения этого условия, помимо общих требований обеспечения надежности машин, необходимо внедрение целого ряда вспомогательных автоматических устройств, обусловливающих и контролирующих надежную и долговечную работу машины, например автоматические устройства для смазки элементов машин, центрирования хода ленты, очистки ленты от прилипших частиц груза, сигнализации о перегрузке рабочих элементов и т. п. Автоматизированные системы требуют высокой культуры производства и обслуживания машин.
2.2. Организация технического обслуживания и ремонта контрольно-измерительных приборов и системы автоматизации перемещения грузов на предприятии
Основой организации работ службы КИПиА на предприятии является система планово-предупредительных ремонтов средств КИПиА.
Система ППР представляет собой совокупность организационно-технических мероприятий по планированию, подготовке, организации проведения контроля и учета различного вида работ по обслуживанию и ремонту, осуществляемых с учетом установленного порядка в определенной последовательности и периодичности. Организация работ по техническому обслуживанию и ремонту должна обеспечивать точность измерений и работоспособное состояние приборов, а также равномерность загрузки сменного персонала.
В графике ППР предусматривается техническое обслуживание, периодические текущие и капитальные ремонты; систематические поверки всех приборов, находящихся в эксплуатации. В техническое обслуживание входят: осмотр внешней части прибора; проверка электропроводки; предупреждение и выявление неисправностей, возникающих в процессе эксплуатации; смазка; смена диаграммной ленты, поверка на «0» показывающих приборов.
Во время текущего осмотра обеспечивается нормальная эксплуатация прибора, замена или восстановление отдельных быстроизнашивающихся деталей. Текущий ремонт проводится с периодичностью до одного года за счет затрат, включаемых в себестоимость продукции. В состав работ, выполняемых при текущем ремонте, входит наружный ремонт - осмотр, вскрытие и чистка приборов, частичная разборка подвижных систем, проверка изоляции и состояния цепей прибора, регулирование подвижной системы по основным точкам, смена сальников, чистка соединительных трубок расходомеров, замена стекол, настройка регулирующей части системы.
Капитальный ремонт проводится для приборов, имеющих продолжительность цикла не менее одного года. При капитальном ремонте проводятся все работы текущего ремонта, а также: разборка подвижной части узлов, поверка схем приборов, ремонт вторичных приборов, датчиков. Капитальный ремонт проводится за счет амортизационных отчислений.
После ремонта все приборы подлежат государственной или ведомственной поверке, после проведения которой ставится клеймо и производится запись в паспорте прибора.
Глава III. Автоматизация ленточных конвейеров и конвейерных линий
Автоматизация отдельных конвейеров и конвейерных линий производится по двум основным схемам: дистанционное управление, при котором автоматизируются только пуск и остановка конвейера; автоматизированный контроль за работой конвейера и его элементов, при котором приводные двигатели автоматически отключаются при нарушении режима работы конвейера или его отдельных элементов.
Согласно правилам безопасной эксплуатации к аппаратуре автоматизированного или дистанционного управления отдельными конвейерами или конвейерными линиями предъявляются следующие основные требования: обеспечение подачи предпускового предупредительного сигнала длительностью не менее 5 с; включение конвейеров в линию в последовательности, обратной направлению грузопотока, и обеспечение пуска последующего конвейера (против грузопотока) после разгона предыдущего; автоматическое одновременное отключение всех конвейеров в линии, транспортирующих груз на вышедший из строя конвейер; невозможность повторного включения неисправного конвейера при срабатывании электрических защит электродвигателя механической части конвейера и др.; отключение провода из любой точки по длине конвейера и наличие местной блокировки, предотвращающей пуск данного конвейера с пульта управления; возможность перехода на местное ручное управление приводами отдельных конвейеров при ремонте, осмотре и регулировании.
Аварийное отключение привода конвейера должно осуществляться при обрыве ленты, затянувшемся пуске, снижении скорости ленты до 75% от номинальной, завале перегрузочного пункта и т.д. Между пультом управления, местом расположения приводов конвейера и пунктами загрузки конвейерной линии должна быть двухсторонняя телефонная связь или кодовая сигнализация.
Для шахтных ленточных конвейеров применяют комплекс АУК.1М, обеспечивающий выполнение основных технических требований к автоматизации конвейерных установок и предназначенный для автоматизированного управления конвейерами и контроля работы стационарных и полустационарных неразветвленных конвейерных линий с числом конвейеров до 10. Комплекс обеспечивает централизованное управление из пункта оператора, расположенного в шахте или на поверхности, и включает в себя пульт управления и блоки управления, в которые входят датчики скорости
,датчики контроля схода ленты, кабель-тросовые выключатели, сирена и др.
Для контроля скорости ленты применяют тахогенераторные марка датчики, устанавливаемые у приводной станции между холостой и рабочей ветвями ленты. Ролик датчика прижимается пружиной к ленте. При вращении ролика тахогенератор вырабатывает ток с определенными параметрами, которые изменяются при изменении скорости ленты. Это фиксируется приборами, подающими команду на электропривод конвейера.
Датчик контроля схода ленты контролирует ее положение и при аварийном сходе ленты в сторону подает сигнал в систему дистанционного или автоматизированного управления.
Для экстренного прекращения пуска и экстренной остановки конвейеров с любого места технологической линии используют кабель-тросовые выключатели, состоящие из гибких тяг (тросов), протянутых вдоль става конвейера, и конечных выключателей.
Для контроля состояния тросовой основы резинотросовых лент применяют устройства, обеспечивающие обнаружение поврежденных тросов в поперечном сечении ленты при ее движении, автоматическое суммирование повреждений тросовой основы по длине ленты и выдачу команды на отключение конвейера при обнаружении недопустимых повреждений.
Применяют также датчики контроля работы перегрузочных пунктов (контроля заполнения бункеров и течек в местах перегрузок горной массы с конвейера на конвейер), аппаратуру автоматизации орошения на перегрузках, предназначенную для автоматического включения и отключения системы орошения в местах перегрузки на конвейерах и др.
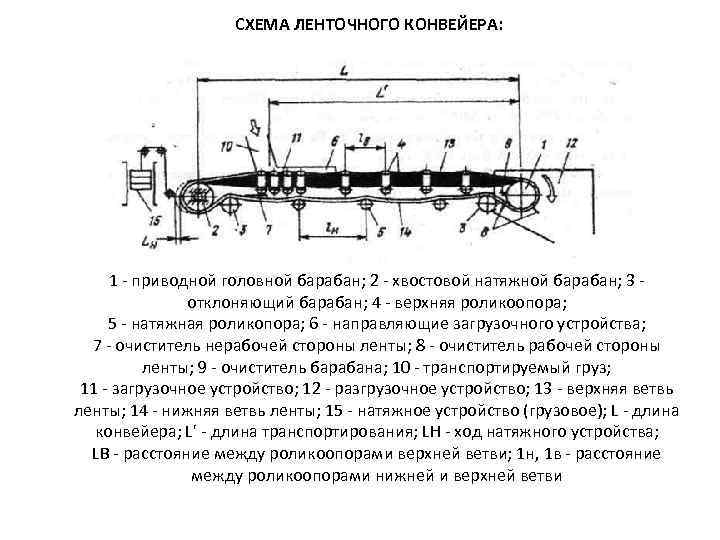
Рисунок 2. Схема автоматизированного ленточного конвейера
3.1 Датчики конвейерной ленты
Принципы работы датчиков конвейерной безопасности определены их функциональным назначением, местом и способом установки на линии.
Датчики контроля скорости ленты конвейера для измерения скорости используют оптоэлектронный импульсный преобразователь и микропроцессор, позволяющий производить необходимый расчет измеряемой величины. Датчик выдает сигнал о величине скорости в виде аналогового токового сигнала стандартного диапазона 4…20 мА, а также релейный сигнал о снижении скорости ниже допустимого предела, остановке или движении в обратном направлении.