Файл: 1. Общие сведения о металлорежущих станках 1 Анализ конструкции современных металлорежущих станков.rtf
Добавлен: 30.11.2023
Просмотров: 341
Скачиваний: 5
СОДЕРЖАНИЕ
1. Общие сведения о металлорежущих станках
1.1 Анализ конструкции современных металлорежущих станков
1.3 Технические характеристики станка
1.6 Конструктивные особенности станка
2. Расчет базовых элементов станка
2.1 Обоснование вида направляющих станка и выбор материала
2.2 Обоснование конструкции основных базовых элементов и выбор материала
3. Кинематический анализ станка
3.1 Описание кинематической схемы станка
4. Указания по эксплуатации и обслуживанию станка
5. Требования техники безопастности и экологии при работе станка
6. Обоснование экономической эффективности станка
7.1 Назначение режущего инструмента
7.2 Технические требования, предъявляемые к режущему инструменту
7.3 Элементы конструкции и геометрические параметры инструмента
1.6 Конструктивные особенности станка
Станки с ЧПУ обеспечивают высокую производительность и точность отработки перемещений, задаваемых программой, а также сохранение этой точности в заданных пределах при длительной их эксплуатации. Станки с ЧПУ имеют расширенные технологические возможности при сохранении высокой надежности работы.
Конструкция станков с ЧПУ должна, как правило, обеспечить совмещение различных видов обработки (точение - фрезерование, фрезерование - шлифование, обработка резанием - контроль и т.д.), удобство загрузки заготовок, выгрузки деталей, что особенно важно при применении промышленных роботов, автоматическое или дистанционное управление сменой инструмента, возможность встройки в общую автоматическую систему управления.
Повышение точности обработки достигается высокой точностью изготовления и жесткостью станка, превышающей жесткость обычного станка того же назначения. Статическая и динамическая жесткость повышается при сокращении длины кинематических цепей. С этой целью для всех рабочих органов применяют автономные приводы, а механические передачи используют в минимально возможном количестве. Приводы станков с ЧПУ должны обеспечивать высокое быстродействие.
Повышению точности способствует также устранение зазоров в передаточных механизмах приводов подач, снижение потерь на трение в направляющих и других механизмах, повышение виброустойчивости, снижение тепловых деформаций, применение в станках датчиков обратной связи. Для уменьшения тепловых деформаций необходимо обеспечить равномерный температурный режим в механизмах станка, чему, например, способствует предварительный разогрев станка и гидросистемы. В высокоточных станках температурную погрешность можно в некоторой степени уменьшить, вводя коррекцию в привод подач от сигналов датчиков температур.
2. Расчет базовых элементов станка
Несущие системы станков должны обеспечивать и сохранять в течение срока службы станка возможность обработки с заданными режимами и требуемой точностью. Исходя из этого, основными критериями работоспособности несущей системы являются жесткость, а также виброустойчивость в смысле обеспечения возможности устойчивой работы станка при заданных режимах и ограничения уровня амплитуд вынужденных колебаний допустимыми пределами.
Металлорежущие станки должны обеспечивать возможность высокопроизводительного изготовления без последующей ручной доводки деталей, удовлетворяющих современным непрерывно возрастающим требованиям к точности. Поэтому проектирование станков и их наиболее ответственных деталей и механизмов, в частности, деталей несущей системы, в значительной степени подчиняется критерию точности. К этому критерию относятся: точность изготовления, сохранение точности в работе (обеспечиваемое малостью приведенных упругих, температурных деформаций и амплитуд колебаний) и сохранение точности за установленные межремонтные периоды (обеспечиваемое малым износом и короблением от остаточных напряжений).
Несущая система станка образуется совокупностью элементов станка, через которые замыкаются силы, возникающие между инструментом и заготовкой в процессе резания.
2.1 Обоснование вида направляющих станка и выбор материала
В станке применяют направляющие скольжения из серого чугуна, выполненные как одно целое с базовой деталью, наиболее просты, но при интенсивной работе не обеспечивают необходимой долговечности. Их износостойкость повышают закалкой с нагревом токами высокой частоты или газопламенным методом. Закалкой одной из сопряженных поверхностей до HRCa 48-53 можно повысить износостойкость более чем в 2 раза. Легирующие присадки к чугунным направляющим дают повышение износостойкости только при последующей закалке. Значительного повышения износостойкости чугунных направляющих можно добиться применением специальных покрытий.
По форме поперечного сечения трапециевидные (типа ласточкина хвоста) направляющие.
2.2 Обоснование конструкции основных базовых элементов и выбор материала
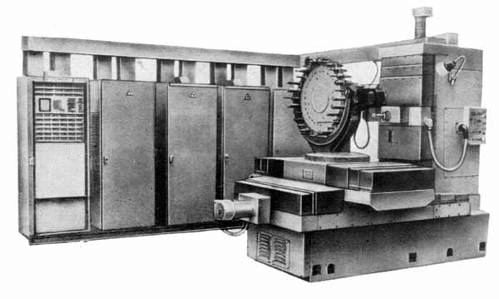
Рис.2 Общий вид
Станок имеет горизонтальную компоновку. На основании смонтирована колонна, по вертикальным направляющим которой перемещается шпиндельная головка (подача по координате Y). Шпиндельная головка размещена в нише колонны, в результате исключается консольное расположение шпинделя; для повышения жесткости шпиндель не имеет осевого перемещения. По горизонтальным направляющим основания перемещается крестовый поворотный стол, осуществляющий продольное и поперечное перемещение по координатам X' и Z', а также поворот вокруг вертикальной оси. На колонне размещен механизм смены инструмента, состоящий из магазина, перегружателя и автооператора.
3. Кинематический анализ станка
3.1 Описание кинематической схемы станка
Порядок передачи вращения от электродвигателей до исполнительных органов показан в кинематической схеме. Кинематическая схема многоцелевого станка состоит из валов и шестерен, электродвигателей и блоков.
3.2 Движения резания
Движение резания осуществляется от регулируемого электродвигателя.
В результате переключения муфт М1, М2, М3 и блоков Б1 и Б2 шпиндель имеет 36 теоретических и 23 практических значения частот вращения. Уравнение кинематического баланса для минимальной частоты вращения шпинделя: nmin = 1600 ∙ 32/40 ∙ 18/72 ∙ 19/60 ∙ 19/61 ∙ 20/86 = 10 мин
3.3 Движения подач
Движение подач и поворот стола осуществляется от высокомоментных электродвигателей постоянного тока М2, М3, М4, М5, М6. Вращение ходовых винтов непосредственно от высокомоментных электродвигателей постоянного тока исключает длинные кинематические цепи, обеспечивая таким образом высокую точность перемещений и гибкость в управлении подачей, что необходимо для контурной обработки деталей.
smin=

3.4 Вспомогательные движения
Колесо z = 24 на валу XIII передает движение или на поперечную подачу стола или на его поворот. Перемещение колеса z = 24 производится двигателем М6 типа РД-09 (N = 10 Вт, n = 1200 мин-1) со встроенным редуктором, а контролируется положение колеса z = 24 микропереключателями.
Стол, салазки и шпиндельная головка, горизонтального фрезерно-сверлильно-расточного станка 2204ВМФ2, перемещаются по замкнутым направляющим качения с предварительным натягом. Ручное перемещение подвижных органов осуществляют через квадраты на соответствующих валах. Зажим поступательно перемещающихся рабочих органов осуществляется путем торможения транспортных винтов. На каждом ходовом винте закреплен стальной диск, проходящий между прижимными пластинами механизма зажима. Зажим осуществляется тарельчатыми пружинами через тягу, пластины. При отжиме эксцентриковый вал, приводимый во вращение электродвигателем, отжимает пакет тарельчатых пружин. Микропереключатели, контролирующие зажим и отжим, включаются кулачком через рычаг.
4. Указания по эксплуатации и обслуживанию станка
Надежность работы станка в значительной степени зависит от систематической и своевременной смазки всех трущихся поверхностей, качества смазочных материалов, состояния рабочих элементов системы смазки, в особенности фильтров.
Во время эксплуатации станка необходимо тщательно и регулярно следить за наличием масла в резервуарах станины, ваннах редукторов и коробок подач. Не допускается падение уровня масла ниже той величины, при которой возможно засасывание воздуха через фильтры в систему смазки. Масло обязательно должно касаться поверхностей разбрызгивающих элементов передач.
Необходимо соблюдать общие правила техники безопасности при работе на металлорежущих станках.
К работе на станке допускаются лица, знакомые с общими положениями условий техники безопасности при фрезерных работах, а также изучившие особенности станка и меры предосторожности, приведенные в данном руководстве и руководстве по эксплуатации электрооборудования станка.
Периодически проверять правильность работы блокировочных устройств.
При установке станок должен быть надежно заземлен и подключен к общей системе заземления. Болт заземления находится с правой стороны основания станка.
5. Требования техники безопастности и экологии при работе станка
1. Масса и габаритные размеры обрабатываемых заготовок должны соответствовать паспортным данным станка.
. При обработке заготовок массой более 16 кг устанавливать и снимать с помощью грузоподъемных устройств, причем не допускать превышения нагрузки, установленной для них. Для перемещения применять специальные строповочно-захватные приспособления. Освобождать обработанную деталь от них только после надежной укладки, а при установке - только после надежного закрепления на станке.
. При необходимости пользоваться средствами индивидуальной защиты. Запрещается работать в рукавицах и перчатках, а также с забинтованными пальцами без резиновых напальчников, на станках с вращающимися обрабатываемыми заготовками или инструментами.
. Перед каждым включением станка убедиться, что его пуск ни для кого не опасен; постоянно следить за надежностью крепления станочного приспособления, обрабатываемой заготовки, а также режущего инструмента.
. При работе станка не переключать рукоятку режимов работы, измерений, регулировки и чистки. Не отвлекаться от наблюдения за ходом обработки самому и не отвлекать других.
. Если в процессе обработки образуется отлетающая стружка, установить переносные экраны для защиты окружающих и при отсутствии на станке специальных защитных устройств надеть защитные очжи или предохранительный щиток из прозрачного материала. Следить за своевременным удалением стружки как со станка, так и с рабочего места, остерегаться наматывания стружки на заготовку или инструмент, не удалять стружку руками, а пользоваться для этого специальными устройствами; запрещается с этой целью обдувать сжатым воздухом обрабатываемую заготовку и части станка.
. Правильно укладывать обработанные детали, не загромождать подходы к станку, периодически убирать стружку и следить за тем, чтобы пол не был залит охлаждающей жидкостью и маслом, обращая особое внимание на недопустимость попадания; их на решетку под ноги.
. При использовании для привода станочных приспособлений сжатого воздуха следить за тем, чтобы отработанный воздух отводился в сторону от станочника.
. Постоянно осуществлять контроль за устойчивостью отдельных деталей или штабелей деталей на местах складирования, а при размещении деталей в таре обеспечивать устойчивое положение их, а также самой тары. Высота штабелей не должна превышать для мелких деталей 0,5 м, для средних - 1м, для крупных - 1,5 м.
. Обязательно выключать станок при уходе даже на короткое время, при перерывах в подаче электроэнергии или сжатого воздуха, при измерении обрабатываемой детали, а также при регулировке, уборке и смазывании станка.
. При появлении запаха горящей электроизоляции или ощущения действия электрического тока при соприкосновении с металлическими частями станка немедленно остановить станок и вызвать мастера. Не открывать дверцы электрошкафов и не производить какую-либо регулировку электроаппаратуры.