Файл: Реферат по дисциплине Основы трибологии нефтегазопромыслового оборудования по теме покозатели качества поверхности изделий и их влияние на.docx
Добавлен: 04.12.2023
Просмотров: 89
Скачиваний: 2
ВНИМАНИЕ! Если данный файл нарушает Ваши авторские права, то обязательно сообщите нам.
Сульфидирование представляет собой процесс насыщения поверхностей стальных и чугунных деталей серой для повышения их износостойкости и предупреждения задиров.
Борирование (рисунок 2) - это насыщение поверхности деталей из стали и сплавов на основе никеля, кобальта и тугоплавких металлов бором для повышения твердости, теплостойкости, износостойкости и коррозионной стойкости. [6]
Изделия до борирования подвергают окончательной механической обработке, выполняя после ХТО лишь шлифовку и доводку. Метод местной защиты от борирования — гальваническое меднение с осаждением слоя меди толщиной 0,015 мм.
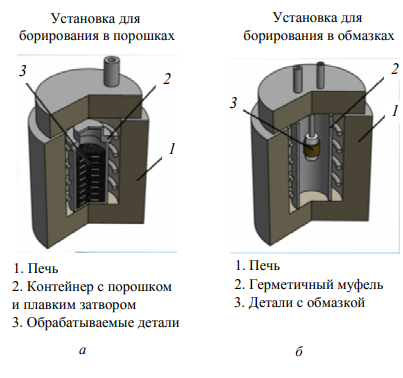
Рисунок 2 – Установка для борирования
Применение технологии борирования прежде всего перспективно для деталей, работающих в условиях коррозионно-абразивного изнашивания: крыльчатки и втулки грязевых насосов, запорная арматура, экструзионные матрицы и др.
Цементация заключается в насыщении поверхности детали при 900.950°С углеродом с последующей закалкой для повышения твердости, износоустойчивости и усталостной прочности. [3]
Гальваническая обработка. Пористое хромирование рабочей поверхности производится в электролитической ванне. Вначале наносится слой хрома толщиной 0,15. 0,20 мм. Пористость создается переключением тока на обратный на 15.20 мин. Обратный ток вызывает выпадение частиц хрома с образованием мельчайших пор. Такая пористость улучшает смазку трущихся поверхностей и повышает срок службы деталей.
4 Механическое упрочнение
Для механического упрочнения деталей применяют накатку, простое или ультразвуковое виброобкатывание, дробеструйную и гидроструйную обработку. Накатка шеек и галтелей осуществляется роликами, которые прижимают к поверхности детали. Трехроликовое приспособление исключает деформацию детали и разгружает суппорт и ходовой винт станка. Накатка выполняется за три оборота при 12. 15 об/мин. В процессе накатки в зону контакта подается смесь масла с керосином или полимерная жидкость. Одновременно с упрочнением поверхности повышается и ее чистота. [5]
Виброобкатывание заключается в обкатывании поверхности детали шариком, который вибрирует параллельно оси вращения детали, совершая 2600 двойных ходов в минуту при амплитуде 2 мм.
Ультразвуковое виброобкатывание получается при наложении на ролик колебаний ультразвуковой частоты
, направленных перпендикулярно к обрабатываемой поверхности. В результате при весьма малых статических усилиях обкатывания получается высокая степень упрочнения, при этом в зоне контакта создается температура 1000. 1200 "С. Этот способ применяется для упрочнения закаленной стали и чугуна.
Дробеструйная обработка заключается в том, что на механически и термически обработанную поверхность с большой скоростью направляют поток стальной или чугунной дроби диаметром 0,5. 1,5 мм. Дробь выбрасывается энергией сжатого воздуха или лопатками колеса.
Гидроструйная обработка заключается в обработке деталей струей воды под давлением 0,4.0,6 МПа. Высоконапорная струя воды позволяет упрочнять поверхности сложной конфигурации.
Электромеханическое упрочнение. Данная обработка выполняется на токарно-винторезном станке. При вращении детали и перемещении инструмента с пластинкой из твердого сплава в зону контакта подводят электрический ток силой 350. 1300 А и напряжением 2. 6 В. Вместо резца можно использовать сглаживающий ролик.
В зоне контакта выделяется значительная тепловая энергия, которая мгновенно нагревает зону контакта до температуры закалки. За счет радиального усилия инструмента поверхность сглаживается, а затем быстро охлаждается за счет отвода теплоты внутрь детали. В итоге получается эффект поверхностной закалки на глубину 0,2.0,3 мм с одновременным поверхностным наклепом, значительно повышающим износоустойчивость (до 10 раз) и усталостную прочность детали (до 6 раз).
Электроискровая обработка. Упрочнение деталей этим способом основано на ударном воздействии направленного искрового разряда, вызывающего взрыв на поверхности детали в точке приложения импульса. В результате происходит перенос металла и упрочнение поверхности детали. Важную роль в повышении износостойкости и усталостной прочности деталей играют подбор пар трения и их смазки, а также применение защитных покрытий. [4]
Подбор пар трения и их смазки. Для снижения износа трущихся поверхностей следует правильно подбирать пары трения и смазку к ним. При этом важно учитывать, что:
- лучшей парой трения является пара трения бронза - сталь;
- коэффициент трения сталь - хром составляет 2/3 коэффициента трения сталь - сталь;
- зубчатые колеса, изготовленные из одного материала, при совместном зацеплении должны иметь разную термообработку;
- применение химических присадок к смазочным маслам позволяет в несколько раз уменьшить износ, увеличить долговечность и надежность механизмов;
- моющие присадки очищают поверхности деталей от отложений, что улучшает охлаждение деталей, смазку и т.д. [5]
Защитные покрытия. Эти покрытия наносят на поверхность деталей для защиты их от коррозии, увеличения сопротивления истиранию, действию высоких температур и т.п. На тепловозах из них применяются гальванические покрытия; пропитка изоляции электрических машин лаками; окраска автоэмалью охлаждающей поверхности; пропитка охлаждающей поверхности жидким стеклом под давлением; окрашивание деталей, агрегатов и тепловоза в целом. Окраска также придает тепловозу товарный вид. [1]
5 Защитные покрытия износостойкости сталей
В основе повышения износостойкости и усталостной прочности деталей лежит воздействие на рабочую поверхность деталей и элементы кристаллической решетки металла путем применения различных видов обработок.
Одним из методов повышения износостойкости является нанесение защитных покрытий.
Покрытиями называют искусственно созданные поверхностные слои, которые могут отличаться от материала основы химическим и фазовым составами, структурой и свойствами.
Покрытия наносятся как для защиты поверхности от различных видов воздействий (высоких нагрузок, температур, различных агрессивных сред) и в декоративных целях, так и для восстановления нарушенной геометрии изделий. [3]
В современной металлургии широко распространенной является технология цинкования.
Защитное действие цинкового покрытия построено на том, что при наличии контакта с агрессивной средой (например, влажной атмосферой) процессы коррозии предпочтительно развиваются на цинке. Тем самым коррозия основного материала – железа (стали) временно подавляется. Однако защита подобного рода не слишком долговечна – она действует до полного окисления слоя цинка на поверхности стали. В машиностроении толщины цинковых покрытий обычно составляют 7-15 мкм, в строительной индустрии — 50-100 мкм.
Внешне процесс коррозии стали с гальваническим цинковым покрытием в камере соляного тумана (стандартная испытательная среда) выглядит так. Через несколько часов после начала испытаний на изделии появляется белый, сперва компактный, а позднее – рыхлый налет – оксид цинка. Затем через его поры начинается коррозия основного металла. Она проявляется в виде красно-коричневых точек и пятен – ржавчины, в тех местах, где цинковое покрытие уже стало проницаемым.
Технология электролитического цинкования основана на процессе электролиза. Схема установки для электролиза очень проста (рисунок 3).
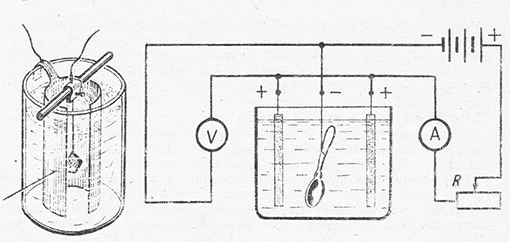
Рисунок 3 – Установка для электролиза
ванне с электролитом помещаются стальное изделие (ложка), которое необходимо покрыть, и пластины чистого цинка. К ним через специальные зажимы подводится постоянный ток. При этом «-» подается на изделие (катод), а «+» — на цинковые пластины (аноды). Электролитом служат растворы различных кислот, щелочей и солей. В процессе электролиза цинковый анод растворяется, его ионы переносятся катоду – изделию, где восстанавливаются до металла и осаждаются на поверхности покрываемого изделия. Следует иметь в виду, что одновременно с осаждением цинка на той же поверхности образуется газообразный водород. Он проникает в металл, формирует газовые пустоты, которые перестраивают кристаллическую решетку, снижая тем самым механические характеристики металла. Именно поэтому цинкование не рекомендуется применять для изделий из материала с классом прочности выше 8.8. [6]
Для повышения коррозионной стойкости и придания изделиям улучшенного декоративного вида применяют пассивирование. Оно заключается в том, что непосредственно после нанесения и промывки цинковое покрытие погружают на 5-10 минут в раствор бихромата натрия и серной кислоты. Цинковое покрытие при этом приобретает зеленовато-желтую окраску с радужными оттенками. Поэтому при неформальном общении его часто называют «желтым цинком». Если необходимо получить блестящее покрытие, применяют другой раствор, содержащий хромовый ангидрид, серную и азотную кислоты. [4] Он не только пассивирует, но и осветляет поверхность изделия. Защитный эффект, вызываемый пассивированием, основан на заполнении пор цинкового покрытия соединениями хрома VI. Довольно часто употребляется термин «голубое» хроматирование. В этом случае речь идет о покрытиях, полученных при пассивировании составом, содержащим хром III.
На сегодняшний день электролитическое цинкование является самым распространённым способом защиты крепежных изделий от коррозии. Это обусловлено высокой производительностью гальванических агрегатов, низкой себестоимостью процесса и достаточно высокой защитной способностью.
Другой массовой технологией нанесения цинка является горячее цинкование. В этом случае стальные изделия погружают в расплавленный цинк при температуре от 445 до 460°C. Образование покрытия при этом происходит гораздо быстрее, чем при электролитическом способе: скорость горячего цинкования может достигать 80 мкм/мин. Это чрезвычайно удобно при нанесении покрытий на крупногабаритные детали. [1]
6 Термодиффузное цинкование
Термодиффузное цинкование (шерардизация) – насыщение верхнего слоя металлического изделия цинком (термодиффузный слой). Достаточно сложная и дорогая технология нанесения защиты. Производится в разогретых вращающихся центрифугах с цинковой пылью (рисунок 4). Температура в контейнере достигает 290–450 °C. Шерардизация позволяет получить толщину покрытия в диапазоне от 6 до 110 мкм, причём покрытие образуется ровное и беспористое, с высокой адгезией к подложке. Защитная способность такого покрытия в 3–5 раз выше, чем у гальванического, и сравнима с горячецинковым. Этот способ используется для защиты металлопродукции специального назначения, например, для деталей железнодорожного транспорта. К минусам стоит отнести небольшую производительность, лимитируемую объёмами камер для цинкования, ограничение размера деталей размером контейнера и отсутствие декоративных свойств у диффузионного покрытия (серые тона, отсутствие блеска). [6]
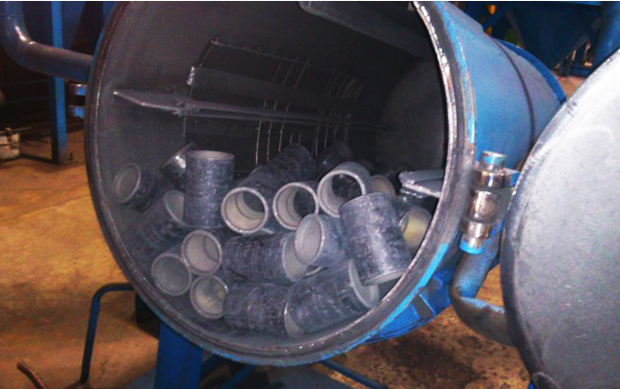
Рисунок 4 – Процесс цинкования в центрифуге
Цинк-ламельное покрытие содержит до 80% цинковых чешуек (ламелей), 10% алюминиевых и связующую основу (акриловые, уретановые, эпоксидные и кремнийорганические смолы). Микроскопические чешуйки расположены параллельно, поэтому перекрывают друг друга, не оставляя «пробелов» на металлической поверхности, куда мог бы попасть кислород. Кроме того, скорость окисления алюминия ниже, чем цинка, поэтому цинк-алюминиевое покрытие в 3 раза устойчивее к коррозии, чем стандартное горячеоцинкованное покрытие.
Цинк-ламельное покрытие можно наносить не только на чёрный металл, но и на оцинкованную сталь, никель, алюминий, медь, нержавеющую сталь и другие металлы. При необходимости на базовое покрытие наносятся дополнительные слои, которые повышают коррозионную и химическую устойчивость, придают нужный цвет и увеличивают износостойкость. Как правило крепежные изделия покрываются цинк-ламелью методом погружения в раствор, остатки которого удаляются в центрифуге. [2]
Среди всех видов покрытия цинк-ламельное заметно превосходит аналогичные, выигрывая по физическим и эстетическим параметрам. Несмотря на то, что детали покрываются тонким слоем состава и полностью сохраняют свою форму, они на 100% защищены от коррозии, а металл – от проникновения водорода и охрупчивания. Такое покрытие выдерживает максимальный класс нагрузки – С5. Его просто наносить на детали сложной формы, а требования к толщине материала базы минимальны. Несмотря на очевидные преимущества цинк-ламельного покрытия, в России его пока используют предприятия, которые можно сосчитать по пальцам одной руки.