Файл: Характеристика машиностроительного предприятия и его деятельности.docx
ВУЗ: Не указан
Категория: Не указан
Дисциплина: Не указана
Добавлен: 05.12.2023
Просмотров: 136
Скачиваний: 6
ВНИМАНИЕ! Если данный файл нарушает Ваши авторские права, то обязательно сообщите нам.
– пластина режущая Т-max Р для растачивания CNMG 120408-МF 2015;
– сверло 2317–0111 ГОСТ 14952 [1];
– сверло 2301–0106 ГОСТ 10903 [1];
Измерительный инструмент:
– штангенциркуль ШЦ–II–250–0,05 ГОСТ 166 [1];
– штангенглубиномер ШГ–160-0,1 ГОСТ 162 [1].
Операция 020. Токарно-винторезная (WNC 300Sx1120AT)
А. Установить заготовку в патрон за Ø180 мм, выверить, закрепить.
Переход №1: Подрезать торец "как чисто" выдерживая размер 66мм.
Переход №2: Сверлить внутреннюю поверхность под резьбу G1.
Переход №3: Нарезать резьбу G1.
Переход №4: Точить внутреннюю поверхность 40 на глубину 4мм.
Переход №5: Подрезать торец "как чисто" выдерживая размер 64мм.
Переход №6: Точить наружную поверхность 152 мм. на глубину 6мм
Переход №7: Точить торец на диаметре 160 мм.
Переход №8: Точить фаску на угол 30 мм.
Переход №9: Точить внутреннюю поверхность 152 мм на глубину 14мм.
Б. Переустановить, выверить, закрепить на разжим.
Переход №1: Центровать отв. 4 мм на глубину 10 1 мм.
Переход №2: Сверлить отв. 8 мм напроход.
Переход №3: Точить наружную поверхность 174 мм напроход
Переход №4: Точить наружную поверхность 164 мм на глубину 210 мм
Режущий инструмент:
– державка призматическая Т–max Р для точения PCLNR 3225P 12;
– пластина для токарной обработки ромбическая CNMG 120408 NEG АC630M;
– державка призматическая Т-max Р для растачивания S32U PCLNR 3225P 12;
– пластина режущая Т-max Р для растачивания CNMG 120408-МF 2015;
– резец 2145–0601 ГОСТ 20874 [1], пластина твердосплавная 03114–090304 ГОСТ 19052 [1];
– резец резьбовой для внутренней резьбы Vargus AVR25-3.
Измерительный инструмент:
– индикатор ИЧ10Б кл.1 ГОСТ 577 [1];
– угломер тип 1-2 ГОСТ 5378 [1];
– радиусный шаблон, набор №3, ТУ 2-034–228 [1];
– пробка 8221–3126 7Н ГОСТ 17758 [1];
– штангенциркуль ШЦ–II–250–0,05 ГОСТ 166 [1].
4.4 Выбор оборудования
В основе выбора технологических баз лежит принцип их совмещения с конструкторскими и измерительными базами.
Процесс токарной обработки строится по принципу дифференциации операций, поэтому черновую и чистовую обработку поверхностей производим раздельно на двух операциях.
Предварительную обработку с формированием черновой базовой поверхности Ø174 мм выполняем на токарно–винторезном станке 1М63 с закреплением заготовки в трёхкулачковом самоцентрирующем патроне. Базами служат наружная необработанная поверхность Ø176 мм (установ А) и обработанная поверхность Ø164 мм (установ Б).
Окончательную обработку, в том числе фасонных поверхностей и сверловку отверстий, выполняем на токарно–винторезном станке с ЧПУ WNC 300Sx1120AT с применением трёхкулачкового самоцентрирующего патрона и базированием по Ø174 мм (установ А).
Сверление отверстий в торцах производим на радиально-сверлильном станке 2М55 с базированием в кондукторе по отверстию.
Финишную обработку производим на станке 1М63
5 Основные условия безопасного ведения работ на рабочих местах
Реальные производственные условия характеризуются, как правило, наличием следующих опасных и вредных производственных факторов, сопровождающих процесс резания, которые могут повлиять на человека при работе в помещении данного участка:
‒ неудовлетворительное освещение является одной из причин повышенного утомления, особенно при напряжённых зрительных работах, продолжительная работа при недостаточном освещении приводит к снижению производительности труда, увеличению брака, повышению вероятности нарушения зрения;
‒ повышенная запыленность и загазованность воздуха рабочей зоны;
‒ выделение в воздух рабочей зоны аэрозолей масел и смазочно-охлаждающих жидкостей;
‒ повышенная или пониженная температура рабочей зоны, колебания которой связаны с сезонными изменениями состояния атмосферы, что может привести к дискомфорту рабочего и понижению его внимания;
‒вероятность поражения электрическим током при нарушении целостности изоляции токоведущих проводов, что может привести к различным электротравмам с высокой вероятностью смертельного исхода;
‒ физические перегрузки, возникающие при установке, закреплении и съеме крупногабаритных деталей, монотонность труда, что приводит к быстрому утомлению, и повышает вероятность совершения человеком неправильных действий, влекущих возникновение различного рода опасных ситуаций.
Нормируемые параметры шума на рабочих местах определены ГОСТ 12.1.003-83 и Санитарными нормами СН 2.2.4/2.1.8.562-96 «Шум на рабочих местах, в помещениях жилых, общественных зданий и на территории жилой застройки». Общий уровень звукового давления не должен превышать 85 дБ.
Основными источниками шума большинства металлорежущих станков являются приводы, электродвигатели и режущий инструмент в процессе работы.
Шумовые характеристики оборудования:
Токарный с ЧПУ 16К20Ф3 – 83 дБ,
Токарный полуавтомат 1283 – 83 дБ,
Вертикально – фрезерный 6Р11 – 32 дБ,
Вертикально – сверлильный 2Н150 - 50 дБ,
Радиально – сверлильный 2М55 - 45 дБ,
Горизонтально – протяжной 7Б55 – 40 дБ.
На участке уровень шума не превышает 85дБ, что лежит в допустимых пределах и не вызывает психические и физиологические нарушения у работающих.
При обслуживании электроустановок применены следующие меры безопасности: диэлектрические перчатки, боты или галоши, диэлектрические коврики или подставки, инструмент с токоизолирующими рукоятками.
В производственных условиях самыми распространёнными источниками воспламенения являются:
а) искры, образующиеся при коротких замыканиях;
б) пробой изоляции;
в) курение на рабочем месте;
г) использование открытого огня в помещении;
д) использование неисправных электроприборов.
Пожаровзрывоопасность производства определяется параметрами пожароопасности и количеством используемых в технологических процессах материалов и веществ, режимами работы станков, наличием возможных источников зажигания и условий для быстрого распространения огня в случае пожара.
Согласно НПБ 105-95 все объекты в соответствии с характером технологического процесса по взрывопожарной и пожарной опасности подразделяются на 5 категорий. Категория здания участка обработки дисков – Д; степень огнестойкости здания I согласно СНиП 21.01- 97.
Меры предупреждения пожара:
‒ использование скрытой проводки для питания аппаратуры;
‒ применение в цепях питания автоматического выключения;
‒ регулярный инструктаж работающих;
‒контроль за состоянием электрооборудования и своевременное устранение его неисправности;
‒ запрет курения на рабочем месте;
‒ допуск к электрооборудованию только лиц, знакомых с правилами его эксплуатации.
Средства пожаротушения:
‒ огнетушители ОУ-5, ОУ-8;
‒ ящик с песком;
‒ кран пожарного водопровода, расположенный на территории участка.
На участке механической обработки основными примесями сточных вод являются пыль, металлические абразивные частицы, сода, масла, растворители, мыла, краски. Бытовые сточные воды, образующиеся в раковинах санитарных узлах, душевых содержат крупные примеси (остатки пищи, тряпки, песок и т.п.). Для спуска производственных и хозяйственных вод предусмотрены канализационные устройства. Канализация состоит из внутренних канализационных устройств, расположенных в здании, наружной канализационной сети (подземных труб, каналов), насосных станций, сооружений для очистки, обезвреживания и утилизации сточных вод, устройства их выпуска в водоём .
В соответствии с «Основами водного законодательства Российской Федерации» все сточные воды предприятия должны подвергаться очистке от вредных веществ перед сбросом в водоём.
6 Индивидуальное задание
Тема индивидуального задания:
ЗАКЛЮЧЕНИЕ
Во время прохождения производственной практики на предприятии ООО «Россельмаш» в г. Ростов-на-Дону был ознакомленн:
- с основным перечнем и кратким описанием продукции, выпускаемой предприятием или структурным подразделением, со структурой и функциями конструкторско-технологических служб предприятия, с работой конструкторско-технологических служб предприятия (подразделения), а также с функциями цеховых технологов;
-
с технологическими процессами машиностроительных производств, средствами технологического оснащения и контроля качества выпускаемой продукции;
-
с организацией труда на рабочем месте и основные мероприятия по охране труда;
А также были научился:
-
работать с нормативно-технической, конструкторской и технологической документацией;
-
анализировать и выбирать рациональные методы, способы и оборудование для получения заготовок деталей машин;
-
выполнять инженерный анализ изделий и технологий их изготовления;
-
проектировать технологические процессы изготовления деталей;
-
проектировать технологическую оснастку для изготовления изделий механической обработкой, сваркой, сборкой (сборкой-сваркой);
-
определять меры по предупреждению брака и повышению качества изготавливаемых изделий механической обработкой, сваркой, сборкой (сборкой-сваркой);
- обеспечивать техническое оснащение рабочих мест с размещением и обеспечением работоспособности технологического оборудования для реализации технологического процесса изготовления изделий;
Благодаря производственной практике были освоены:
-
методы анализа технологических процессов производства изделий, а также их влияния на качество получаемых изделий;
-
работа с современными программными продуктами подготовки конструкторской и технологической документации;
-
методики проведения лабораторных испытаний и контроля качества изготавливаемых деталей.
Было выполнено индивидуальное задание.
Цели учебной практики были выполнены. Задачи достигнуты.
СПИСОК ИСПОЛЬЗОВАННЫХ ИСТОЧНИКОВ
-
Официальный сайт http://www. rostselmash.com -
Марочник сталей и сплавов. Под ред. В.Г. Сорокина. – М.: Машиностроение, 1989. – 489 с. -
Кузнецов Ю.И. и др. Оснастка для станков с ЧПУ: Справочник.-2-е изд., перераб и доп.-М.: Машиностроение.2015г.-512с. -
Клепиков В.В., Бодров А.Н. Технология машиностроения. – М.: ФОРУМ: ИНФА – М. 2004. – 860 с. -
Краткий справочник металлиста./Под общ. ред. П.Н. Орлова, Е.А. Скороходова. – М.: Машиностроение, 1986. – 960 с. -
Добрыднев И.С. Курсовое проектирование по предмету “Технология машиностроения”. – М.: Машиностроение, 1985. – 184 с. -
Нефедов Н.А. Дипломное проектирование в техникумах. –М.: Высш. школа, 1986. – 239 с. -
Балабанов А.Н. Краткий справочник технолога-машиностроителя.- М.: Издательство стандартов, 1992. – 464 с. -
Справочник технолога-машиностроителя. В 2-х томах. Т 1. /Под ред. Косиловой А.Г., Мещерякова В.К. – М.: Машиностроение,1986. – 656 с. -
Справочник технолога-машиностроителя. В 2-х томах. Т 2 /Под ред. А.Г. Косиловой и Р.К. Мещерякова – М.: Машиностроение,1986. – 496 с. -
Обработка металлов резанием. Справочник технолога. Под общей ред. А.А. Панова. – М.: Машиностроение, 1988. – 736 с. -
Справочник технолога – машиностроителя. В 2-х т. Т.2 / Под ред. А.Г. Косиловой и Р.К. Мещерякова, -4-е изд., перераб. и доп. –М.: Машиностроение, 1986. – 496 с.
ПРИЛОЖЕНИЕ А
(обязательное)
Чертёж детали
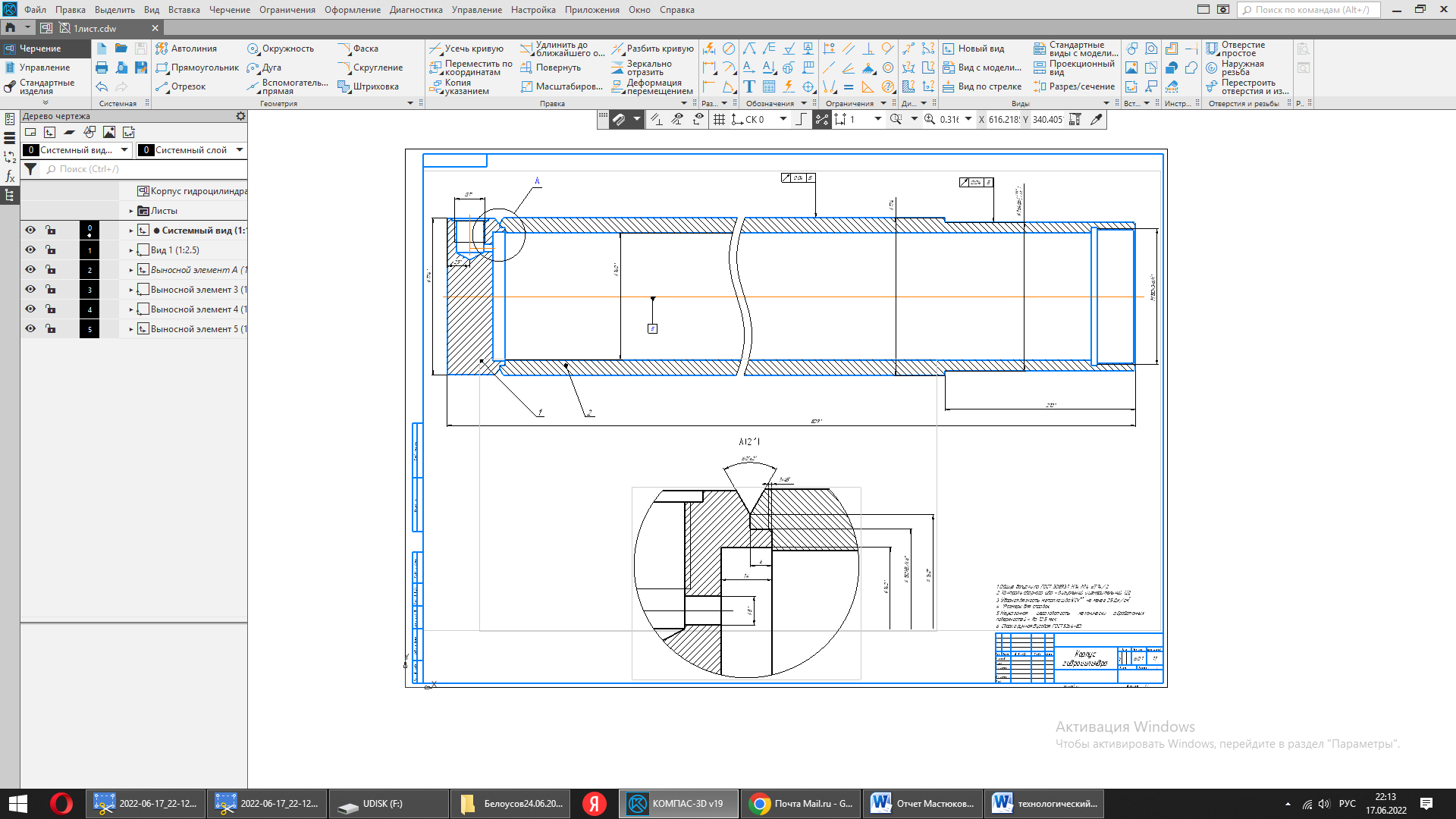
ПРИЛОЖЕНИЕ Б
(обязательное)
Технологический процесс изготовления детали
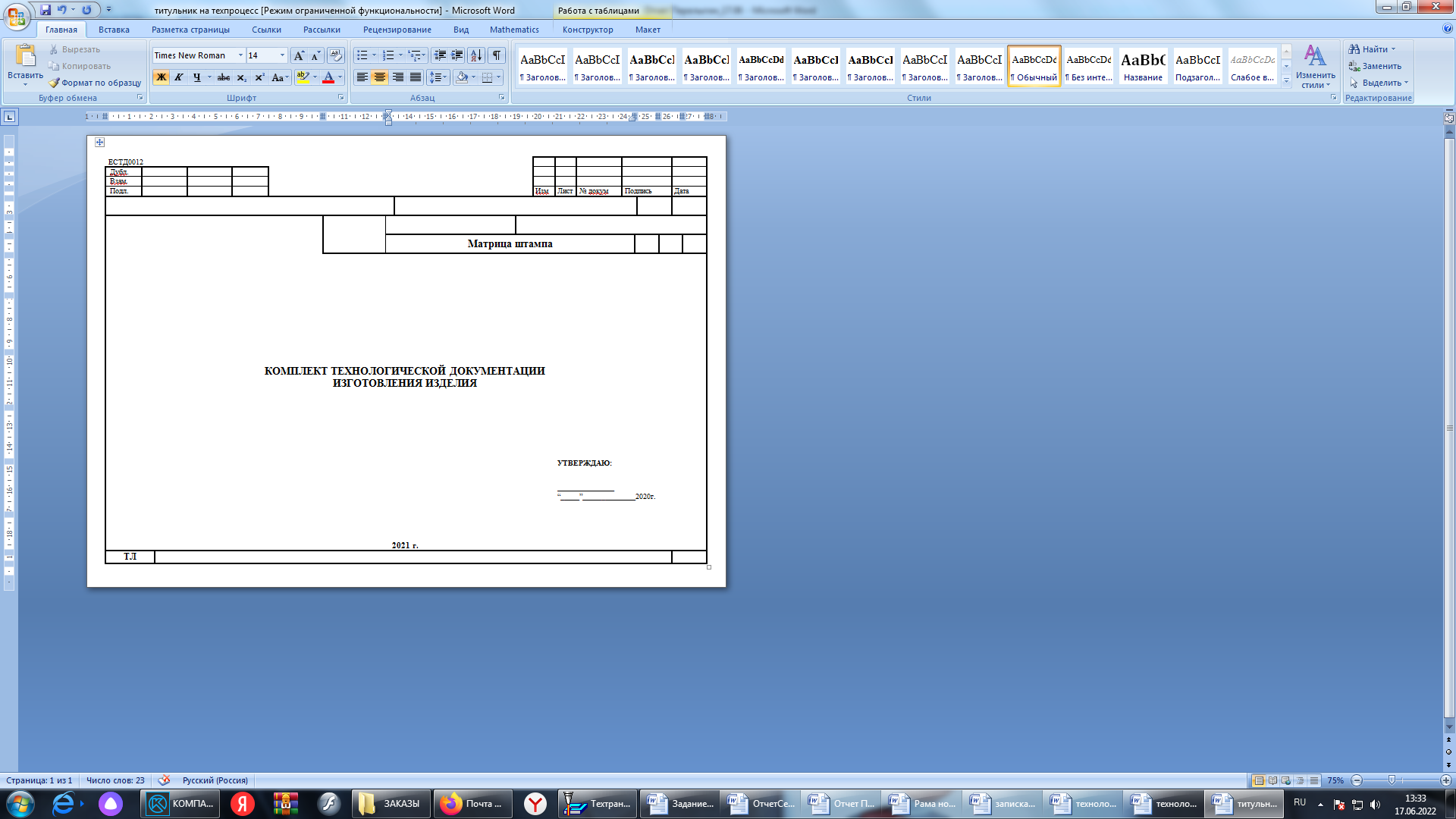
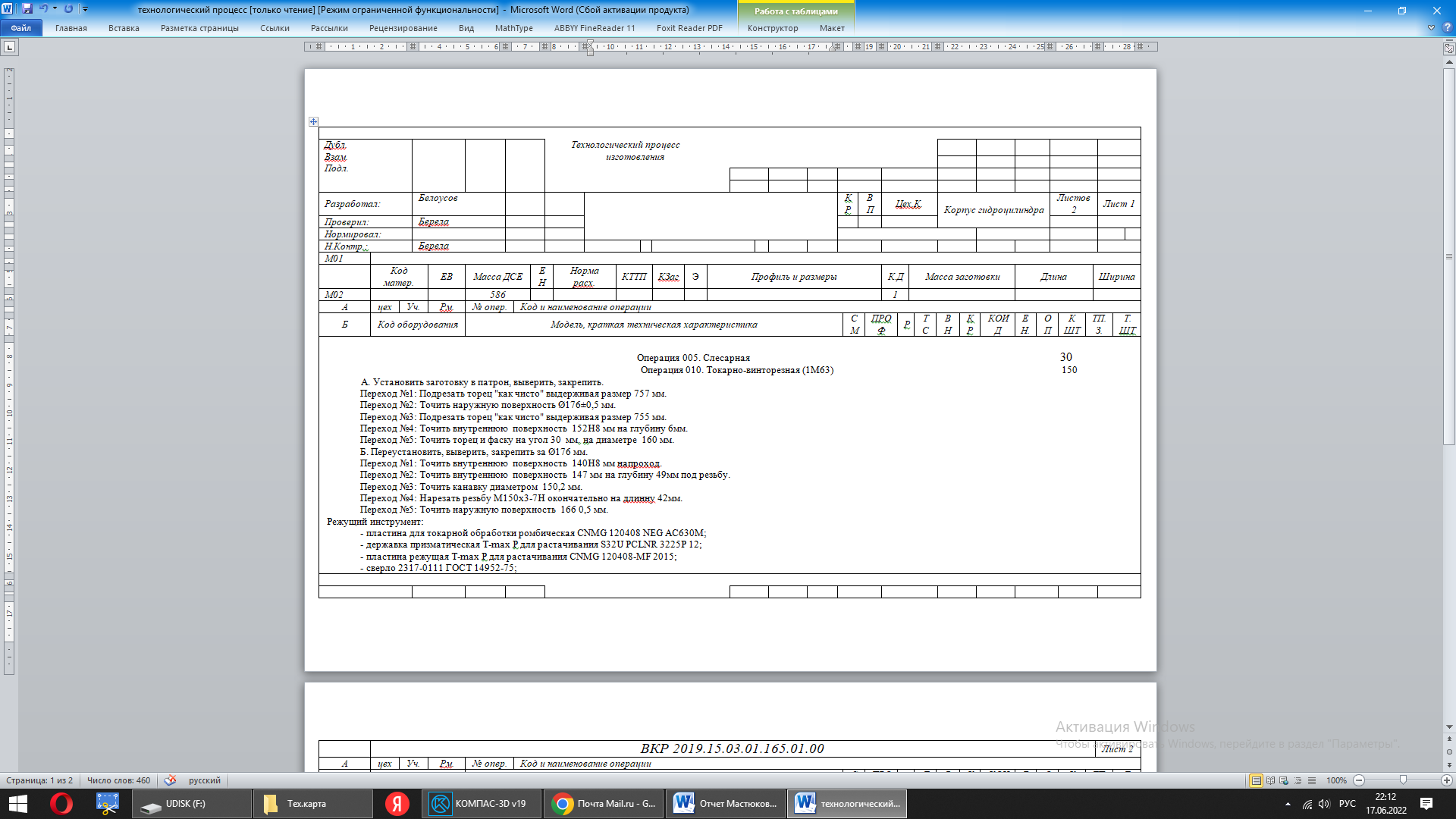
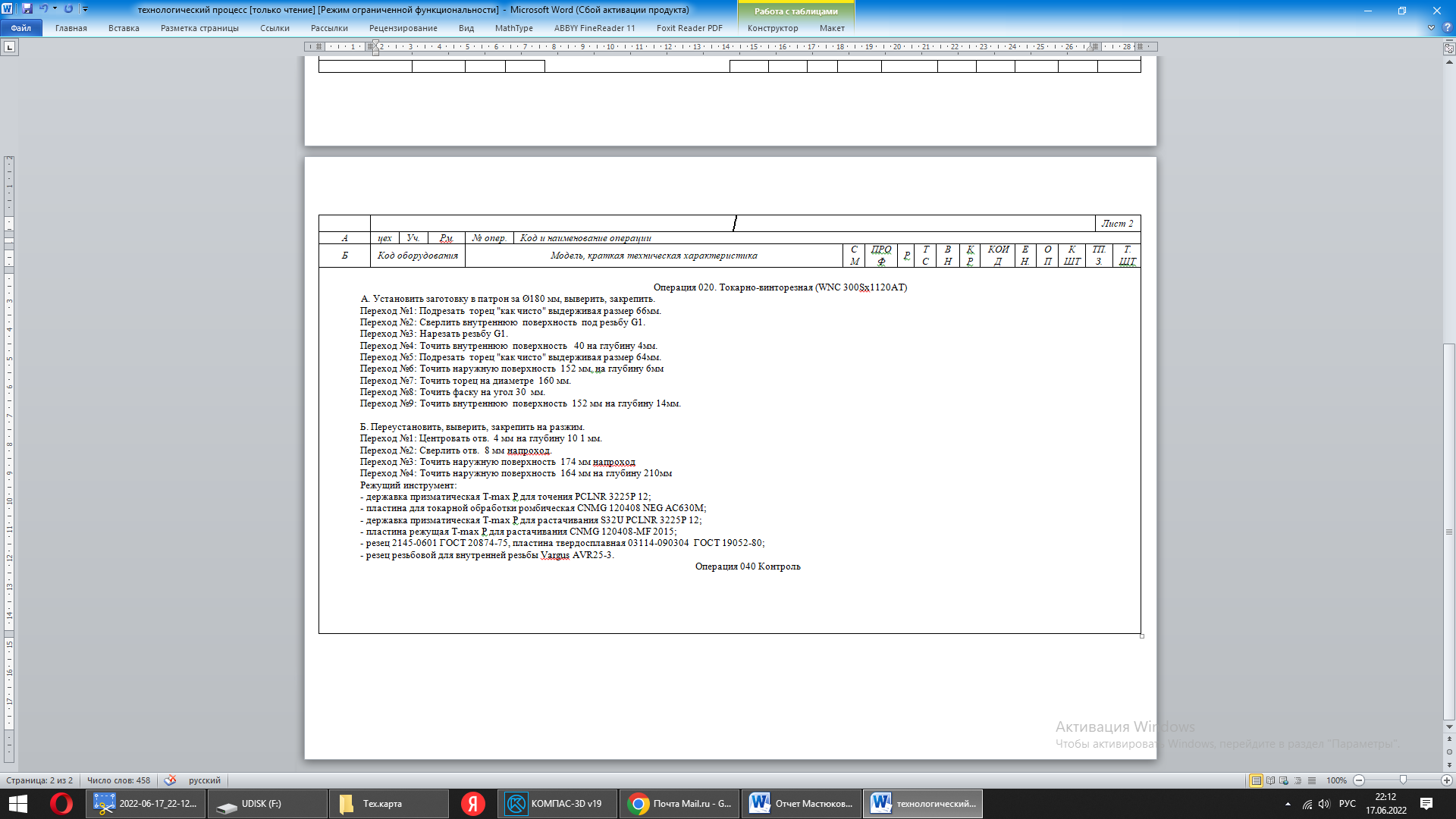