Файл: Лекция 14 Подготовка кромок. Сборка деталей, определение величины зазора. Инструмент для выполнения измерений ушс3.docx
ВУЗ: Не указан
Категория: Не указан
Дисциплина: Не указана
Добавлен: 06.12.2023
Просмотров: 217
Скачиваний: 1
ВНИМАНИЕ! Если данный файл нарушает Ваши авторские права, то обязательно сообщите нам.
Методы проверки
Контроль качества сварочных работ, выполняемых на производстве, может быть разрушающим и неразрушающим. Первые методы используются выборочно. Проверяется одно или несколько изделий из большой партии, или часть металлоизделия в строительной конструкции.
Оно проверяется по различным параметрам определенным протоколом испытаний. Но главным образом используют специальные приборы или материалы позволяющие проверить качество сварных соединений без разрушения конструкции.
Основными способами неразрушающего контроля качества сварки являются:
-
визуальный; -
капиллярный; -
проверка на проницаемость; -
радиационный; -
магнитный; -
ультразвуковой.
Имеются и другие способы и виды контроля качества сварки, но в силу своей специфики они не получили распространения.
Проверка состояния сварных швов не является одноразовым актом, это результирующий этап, который показывает, как работает система контроля качества на предприятии.
Для минимизации дефектов сварочных соединений проводят операционный контроль работ. Регулярно проводится аттестация, на которой комиссия сначала дает разрешение на сварку контрольного соединения. При прохождении сварщиками этого испытания проверяются теоретические знания.
Перед началом работ проверяется квалификация сварщика, у него должно быть удостоверение на право сваривания определенных марок стали и наряд-допуск.
Инженер по сварке и контролер из службы техконтроля проверяют качество сборки, состояние кромок, работоспособность сварочного аппарата, контролирует температуру прогрева, если это предусмотрено нормативно-технической документацией.
Контроль качества сварочных материалов осуществляется с момента поступления их на предприятие и до использования на сварочном посту. Проверку электродов проводят на каждом этапе хранения и использования, при необходимости их прокаливают.
При непосредственном проведении работ проверяют, какой режим сварки используется, дуговая сварка, аргонодуговая или иной вид сварки. Проверяют порядок наложения швов, размеры слоев и всего соединения.
Если предусмотрены специальные требования в проектно-технической документации, то и их реализацию. По завершении сваривания проверяет наличие клейма сварщика.
Внешний осмотр
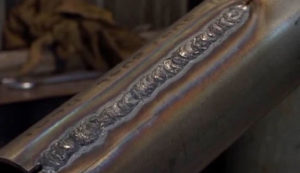
Визуальный контроль помогает выявить, наряду с наружными, часть внутренних изъянов. Так, переменные по габаритам валики швов и неравномерные складки говорят о непроварах, возникающих из-за частых обрывов электрической дуги.
Перед началом работ со сварных соединений удаляют шлак, окалины прочие загрязнения. Чтобы лучше можно было разглядеть дефекты, швы обрабатывают азотной кислотой (10%). Это придает матовость шву, что облегчает поиск изъянов.
После обработки кислотой необходимо провести тщательную протирку спиртом, чтобы предупредить ее вредное влияние на сплав.
Для повышения качества проверки можно использовать фонарь и оптическую лупу. Для контроля геометрических размеров применяют штангенциркуль и шаблоны.
Капиллярный метод
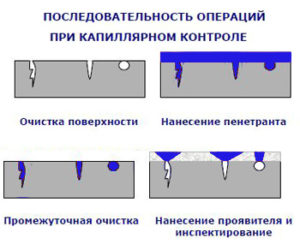
Капиллярный способ контроля качества шва позволяет иметь дело не только с любыми металлами, но и с керамикой, пластмассой, стеклом. Главное его применение связано с проявлением внешних изъянов, которые невозможно или трудно определить невооруженным глазом. Иногда, используя, к примеру, керосин, можно обнаружить сквозные дефекты.
Способ очень простой, работает со времен возникновения потребности проверки сварочных швов. Для него даже разработан специальный ГОСТ 18442-80.
В капиллярном методе контроля качества сварки используют пенетранты – вещества, имеющие малое поверхностное натяжение и сильный цветовой контраст.
Проникая в дефектные зоны, и подсвечивая их, пенетранты визуализируют изъяны сварки. Их делают на основе воды, керосина, масла для трансформаторов и прочих жидкостей.
Наиболее чувствительные пенетранты могут проявить дефекты диаметром от 0,1 микрона. Капиллярный метод контроля качества сварки эффективен для дефектов до 0,5 мм шириной. При больших диаметрах пор или трещин он не работает.
Способ с применением пенетрантов заключается в очистке поверхности, нанесении контрольной жидкости и проявлении изъянов. Очень эффективен способ контроля сварных соединений с помощью керосина.
Несмотря на разнообразные приборы контроля качества сварки, проверку этим способом используют до сих пор. С одной стороны наносят раствор мела, дают время для сушки, затем с другой стороны шов смазывается керосином. Бракованные места проявляются через несколько часов в виде темных пятен.
Проверка сварных соединений на проницаемость
В случае применения сварки при изготовлении резервуаров требуется контроль герметичности. Для этого проводят испытания на непроницаемость соединений. Контроль качества проходит с применением газов или жидкостей.
Суть метода основана на создании большой разности давлений между наружной и внутренней областью емкости. При сквозных изъянах в сварном шве жидкость или газ будут переходить из области с высоким давлением в область с низким давлением.
В зависимости от используемого вещества и способа получения избыточного давления контроль проницаемости осуществляют пневматикой, гидравликой или вакуумом.
Пневматический способ
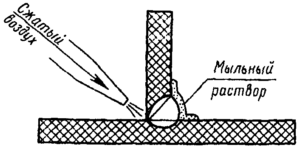
Затем все сварные швы смачивают мыльным раствором. В местах протечек образуются пузыри, что очень легко фиксируется. Для лучшей визуализации используют добавку аммиака, а шов покрывают бинтом пропитанным фенолфталеином. В местах протечек появляются красные пятна.
Если нет возможности накачать емкость, то применяют способ обдува. С одной стороны шов обдувается под давлением не менее 2,5 атмосферы, а с другой обмазывается мыльным раствором. Если имеется брак, то он выявится в виде пузырьков.
Гидравлический способ
При гидравлическом способе контроля качества сварки проверяемая емкость заполняется водой или маслом. В сосуде создается избыточное давление, которое больше номинального в полтора раза.
Затем в течение определенного времени, обычно 10 минут, область вокруг шва обстукивают молотком со скругленным бойком. При наличии сквозного дефекта сварки появится течь. Если избыточное давление невелико, то время выдержки резервуара увеличивают до нескольких часов.
Магнитная дефектоскопия
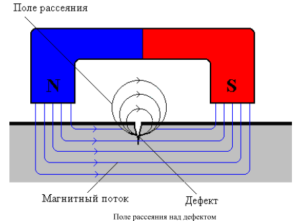
Явление электромагнетизма используется в магнитных дефектоскопах. Каждый металл имеет свою степень магнитной проницаемости. При прохождении через неоднородные материалы магнитное поле искажается, что говорит о присутствии инородных элементов внутри структуры.
Это используется в приборе для контроля качества сварки. Он вырабатывает магнитное поле, которое проникает в исследуемый металл. Неоднородности фиксируются магнитопорошковым или магнитографическим способом.
В первом случае на сварной шов наносят ферромагнитный порошок. Там где происходит скопление порошка вероятнее всего непровар, нет сплошного соединения. Порошок может быть сухим или влажным, с примесью масла или керосина.
Во втором случае на шов накладывают ферромагнитную ленту. Затем ее пропускают через прибор, где анализируют все аномалии, зафиксированные на ленте, и определяют дефекты сварки.
Магнитный способ контроля качества имеет ограничения, связанные с самим принципом действия прибора. Он может проверять качество сварных соединений только ферромагнетиков, к которым некоторые стали и цветные металлы не относятся. Соответственно, такой способ контроля имеет ограниченное применение.
Ультразвуковая дефектоскопия
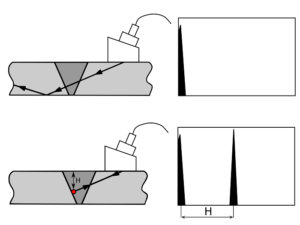
Датчик и излучатель плотно прикладывают к исследуемому материалу, после чего устройством вырабатывается ультразвук. Он проходит через весь металл и отражается от задней стенки, возвращаясь, попадает на приемный сенсор, который в свою очередь преобразует ультразвук в электрические колебания. Прибор представляет полученный сигнал в виде изображения отраженных волн.
Если внутри металла присутствуют какие-нибудь изъяны, датчик зафиксирует искажение отраженной волны. Опытным путем установлено, что различные дефекты сварки по-разному себя проявляют на ультразвуковом дефектоскопе. Это позволило провести их классификацию. При соответствующем обучении специалист может точно определить вид брака в шве.