Файл: На ручную электродуговую сварку корневого слоя шва электродами с основным видом покрытия при сварке станых изолированных труб.doc
Добавлен: 26.10.2023
Просмотров: 47
Скачиваний: 2
ВНИМАНИЕ! Если данный файл нарушает Ваши авторские права, то обязательно сообщите нам.
- трубы с царапинами, рисками, задирами глубиной более 5% от толщины стенки, вмятинами глубиной, превышающей 3,5% от диаметра трубы, или с забоинами и задирами фасок глубиной более 5 мм ремонту не подлежат; дефектные участки труб следует обрезать;
- концы труб проверить визуально на расслоение металла. В случае трудности идентификации расслоения необходимо провести цветную дефектоскопию или ультразвуковой контроль. Концы с выявленным расслоением обрезаются с последующим ультразвуковым контролем.
Работы по сборке и сварке корневого слоя шва выполняет бригадой в составе 5 человек (сварка слоя выполняется не менее, чем 2 сварщиками), включая звено подготовительных работ, которое выполняет следующие технологические операции:
- очищает внутреннюю полость труб от попавшего грунта, грязи.
- трубы, подлежащие сварке, имеют разделку кромок в соответствии с ТУ на их поставку, обрабатывает кромки и концы труб вручную или шлифовальной машинкой до металлического блеска на ширину не менее 10-15 мм.
Технология ручной электродуговой сварки корневого слоя шва.
Смещают кромки труб, при сборке равномерно распределяя по периметру стыка, максимальная величина смещения кромок не должна превышать 2,0 мм, изменение величины смещения труб производят по наружным поверхностям.
При сборке заводские продольные швы смещаются относительно друг друга не менее чем на 100 мм, а также располагать в верхней половине периметра свариваемых труб (см. рис.7).
*
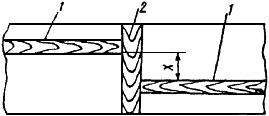
Рис.7. Схема сварки труб с продольным швом:
1 - продольные швы; 2 - кольцевой шов; Х - не менее 100 мм
Выполненные работы по сборке стыков труб предъявляют мастеру для осмотра и освидетельствования на соответствии проекту.
Приступают к ручной электродуговой сварке корневого слоя шва поворотного кольцевого стыка в следующей технологической последовательности:
- сварка корневого слоя шва производят электродами с основным видом покрытия;
- после выполнения всего периметра корневого слоя шва освобождают жимки центратора, удаляют (перемещают) наружный центратор;
- после снятия центратора все сваренные участки зачищаются, начало и конец каждого участка обрабатывается механическим способом (шлифовальной машинкой с абразивным кругом);
- корневой слой шва стыков труб, зачищается снаружи трубы, после чего осуществляется осмотр сварного соединения на отсутствие наружных дефектов и соответствие геометрических параметров регламентированным значениям;
Запрещается выполнять подварку способом "на спуск". Подварочный слой допускаеся шириной 8±1 мм и усилением 1

- усиление обратного валика корневого слоя шва при односторонней сварке допускается от 0,5 до 3,0 мм;
- усиления сварного соединения снаружи трубы, а также прилегающей околошовной зоны зачищается шлифмашинкой с применением дисковых проволочных щеток до полного удаления шлака и брызг наплавленного металла;
- после сварки корневого шва последующие слои выполняют механизированной сваркой (МПС) самозащитной порошковой проволокой.
Все свариваемые торцы труб на ширине не менее 150 мм просушиваются до температуры +50°C независимо от температуры окружающего воздуха, толщины стенки и диаметра трубы.
При сварке поворотных стыков корневой слой накладывается так, чтобы обеспечить хорошее проплавление и провар корня шва. Для уменьшения образования грата внутри стыка рекомендуется производить сварку в такой последовательности (см. рис.8):
- заваривают первым слоем участки от точки 1 до точки 2 и от точки 4 до точки 3 на стыке труб;
- затем производят заварку участков от точки 4 до точки 1 и от точки 3 до точки 2.
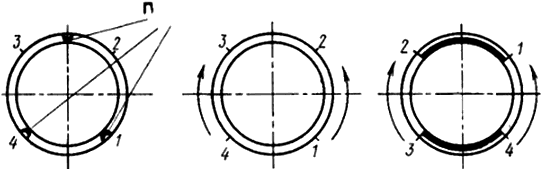
Рис.8. Сварка корневого слоя шва поворотного стыка
Сварку корневого слоя шва обычно осуществляют без поперечных колебаний способом снизу-вверх путем резких продольных колебаний с амплитудой 20

Сварку корневого слоя шва следует осуществлять преимущественно на постоянном токе прямой полярности на короткой дуге. Запрещается зажигать дугу вне шва на трубе. Не допускается повторное зажигание одного и того же электрода.
Амплитуда колебаний должна составлять не более 2-х диаметров стержня электрода.
Не рекомендуется осуществлять сварку техникой резкого выброса сварочной дуги вверх до начала стекания расплавленного металла с последующим его "размазыванием" поперечными колебаниями.
При наличии отклонения дуги или ее выдувания из разделки кромок необходимо установить основную причину этого явления - магнитное дутье. С этой целью необходимо:
- соблюдать правила подключения полюса "земля", которые требуют систематического распределения магнитных масс по обе стороны от дуги;
- при намагниченных трубах произвести их размагничивание путем намотки нескольких витков сварочного кабеля вокруг одной из свариваемых труб и подключения кабеля через балластный реостат на некоторое время к сварочному источнику питания.
При ручной сварке корневого слоя поверхность шва должна быть гладкой мелкочешуйчатой и плавно сопрягаться с кромками. Она должна быть тщательно зачищена абразивными кругами с применением электрической шлифовальной машинки PWS 750-125. После сварки удаляют шлак и проводят визуальный осмотр шва. Места наплавов, пропусков, не сплавлений зачищают шлифовальной машинкой, при необходимости подваривают электродами с основным видом покрытия. Шаблоном контролируют равномерность заполнения разделки. Участки стыка с выпуклыми швами или излишне заполненные зачищают шлифовальной машинкой.
После завершения сварки корневого слоя шва необходимо с помощью шлифовальной машинки тщательно очистить его от шлака.
3.6.13. Перемещать наружный центратор разрешается только после того, как корневой слой шва сварен на

2. ТРЕБОВАНИЯ К КАЧЕСТВУ РАБОТ
Контроль и оценку качества ручной электродуговой сварки корневого слоя шва электродами с основным видом покрытия стальных изолированных труб

Контроль качества выполняемых работ должен осуществляться специалистами с привлечением аккредитованной производственно-испытательной лаборатории (ПИЛ) оснащенной техническими средствами, обеспечивающими необходимую достоверность и полноту контроля и возлагается на производителя работ или мастера, выполняющего работы по ручной электродуговой сварке корневого слоя шва.
Строительный контроль качества работ должен включает в себя входной контроль проектной рабочей документации и результатов инженерных изысканий, а также качество выполненных предшествующих работ, операционный контроль строительно-монтажных работ, процессов или технологических операций и приемочный контроль выполненных работ с оценкой соответствия.
Контроль качества сварочных работ включает:
- входной контроль технологической документации, монтируемых сварных конструкций, сварочных материалов, оборудования, инструмента и приспособлений;
- операционный контроль сборки под сварку соединений, узлов и конструкций, технологии сварки и качества выполняемых сварных соединений;
- приемочный контроль качества сварных соединений, узлов и конструкций.
Контроль качества сварочных работ и приемку сварных соединений и узлов на всех стадиях сборки и сварки труб выполняется специализированной организацией, Производственно-испытательные лаборатории или подразделения, имеющие соответствующую лицензию, аттестованные специалисты сварочного производства и дефектоскописты неразрушающего контроля.
Методы и объемы контроля назначаются в соответствии с требованиями проектной документации.
Входной контроль
Входной контроль проводится с целью выявления отклонений от требований проекта и соответствующих стандартов. Входной контроль поступающих на объект строительных материалов, конструкций и изделий, осуществляется согласно ГОСТ 24297-2013. Верификация продукции проводится:
- регистрационным методом путём анализа данных зафиксированных в документах (сертификатах, паспортах, накладных и т.п.);
- внешним визуальным осмотром;
- техническим осмотром;
- при необходимости - измерительным методом с применением средств измерения (проверка основных геометрических параметров), в т.ч. лабораторного оборудования;
- контрольными испытаниям в случаях сомнений в правильности характеристик или отсутствии необходимых данных в сертификатах и паспортах заводов-изготовителей.
Сварочные материалы хранятся в сухих отапливаемых помещениях, с температурой воздуха не менее 15°C и влажностью не более 60%, с сохранением герметичности упаковки.
Электроды, при условии сохранности герметичности упаковки и централизованного складирования в специально оборудованном помещении могут храниться без дополнительной проверки перед использованием в течение одного года. При хранении сварочных материалов более одного года, проходят повторную проверку в соответствии с требованиями п.4.4.1 непосредственно перед их использованием.
Если упаковка негерметична или повреждена, то электроды и проволока подвергается дополнительной проверке их внешнего вида и сварочно-технологических свойств и использованы в первую очередь. Дальнейшему длительному хранению такие сварочные материалы не подлежат.
Электроды с основным видом покрытия после прокалки хранятся:
- в термостатах (термопеналах), сушильных шкафах, прокаленных печах при температуре от +100°C до +150°C;
- в герметичных емкостях в сухих отапливаемых помещениях при температуре воздуха не ниже +15°C и относительной влажности не более 60% в течение не более 2-х суток;
- после истечения 2-х суток перед использованием электродов требуется повторная прокалка.
Входной контроль производится для всей партии сварочных материалов, включающий:
- проверку наличия сертификатов качества или сертификатов соответствия фирмы завода-изготовителя (для сварочных материалов импортного производства - дубликатов сертификатов качества на русском языке);
- проверку сохранности упаковки;
- внешний вид;
- проверку соответствия электродов требованиям ГОСТ;
- определение диаметра электродов и проверку их соответствия данным сертификата;
- проверку внешнего вида покрытия электродов - прочности (адгезии) покрытия электродов, отсутствия поверхностных дефектов электродных покрытий, разнотолщинности электродного покрытия;
- проверку сварочно-технологических свойств электродов.
Каждая прибывшая с предприятия-изготовителя траверса до пуска в работу осматривается и опробируется руководителем работ (начальником колонны, мастером, бригадиром) и после заполнения формы N 1 паспорта траверса запускается в эксплуатацию.
Входной контроль поступающих траверс осуществляется путем визуального осмотра. На балке, с двух сторон, эмалью ПФ-115 красного цвета наносятся надписи:
- на центральной части - грузоподъемность траверсы и диаметр поднимаемых труб;
- над каждой парой симметричных крюков диапазоны длин поднимаемых труб данной парой крюков;
- на двух боковых сторонах каждого навешенного на стропах крюка - грузоподъемность каждого крюка.
Каждая траверса должна быть снабжена табличкой, прикрепленной к балке, должно быть нанесено:
- наименование завода-изготовителя и его товарный знак;
- индекс изделия;
- его порядковый номер по нумерации завода-изготовителя;
- год и месяц выпуска.
Траверса проверяется на отсутствие задиров и искривлений на торцевых захватах. Крюки торцевых захватов снабжаются прокладками из мягкого материала типа капролон.
Результаты входного контроля регистрируются в "Журнале входного учета и контроля качества получаемых деталей, материалов, конструкций и оборудования".
Операционный контроль