Добавлен: 06.11.2023
Просмотров: 67
Скачиваний: 2
ВНИМАНИЕ! Если данный файл нарушает Ваши авторские права, то обязательно сообщите нам.
4. Блок схема моделирования работы СТО



УМР
Зона
ожидания
Приемка
выдача
Участок
диагностики
Участок
ТО и ТР

ОТК




Агрегатный
участок
Кузовной,
арматурный,
обойный
участок
Окрасочный
участок
Противокоррозионный
участок





























Специализированные участки ремонта



Рисунок 2 - Схема производственного процесса на СТО
Функции участков:
Участок моечно-уборочных работ включает в себя: уборку салона автомобиля, мойку двигателя, мойку автомобиля снизу, наружную мойку, сушку и полировку кузова автомобиля.
Участок приемки и выдачи автомобилей, этот участок является начальным и конечным пунктом пребывания автомобилей на СТО, здесь клиент передает свой автомобиль обслуживающему персоналу и получает его обратно.
Диагностика автомобилей служит для определения технического состояния автомобиля, его агрегатов и механизмов в технически исправном состоянии.
Участок ТО и ТР. На данном участке выполняются все виды ТО.
Отдел технического контроля (ОТК) главной задачей этого участка является проверка требований стандартов и технических условий, а также укрепление производственной дисциплины и повышение качества работы.
На агрегатно-механическом участке выполняются разборочно-сборочные, моечные, ремонтно-восстановительные и контрольные работы по двигателю, коробки передач, рулевому управлению и т. д.
На кузовном участке осуществляют замену отдельных деталей кузова, а также сварочные работы.
На обойном участке выполняют ремонт сидений и спинок, замену и ремонт обивки потолка, а также изготовление чехлов и обивки салона.
Окрасочный участок имеет в своем составе три производственных отделения, связанных функционально между собой: подготовительных работ, краска - приготовительных и окрасочных.
5. Агрегатный участок
Агрегатный участок является составной частью зоны ТР.
При проведении работ в зоне ТР на универсальных или специализированных постах устраняют, в основном, мелкие дефекты и неисправности путем проведения диагностических, разборочно-сборочных, контрольно-регулировочных и технологических работ по ремонту оборудования и агрегатов. Для сокращения времени простоя подвижного состава ТР выполняется преимущественно агрегатным методом, при котором производится замена неисправных или требующих капитального ремонта агрегатов и узлов на исправные, взятые из оборотного фонда.
В рамках агрегатного участка зоны ТР осуществляется полное диагностирование агрегатов автомобилей с целью выявления неисправностей, а также ремонтные и восстановительные работы по устранению выявленных дефектов и замене износившихся деталей, узлов на новые или ранее восстановленные.
Перед отправкой детали или узла в ремонтный участок, на универсальном посту зоны ТР осуществляется предварительное диагностирование с целью определения работоспособности деталей или узлов и принятия решения о направлении их на участок для более глубокого диагностирования, проведения ремонтных работ.
5.1 Выбор оборудования.
Таблица 9-Оборудованние агрегатного участка
№ п/п | Наименование оборудования; габаритные размеры, мм | Тип, модель, марка | Количество, шт. | Технические характеристики, габаритные размеры, мм | Примечания | |
1 | Установка для мойки агрегатов | М-206 | 1 | 1140×600; Р=6кВт | | |
2 | Верстак однотумбовый | ВС-1 | 2 | 1400×800 | | |
3 | Нагнетатель смазки | С-322 | 1 | 470×540 | Механический | |
4 | Пресс для клепки накладок | Р-340 | 1 | 640×1630 | | |
5 | Стол для деффектовки | 2209 | 1 | 1500×800 | | |
6 | Стенд для разборки коробок передач | Р-201 | 2 | 692×195 | | |
7 | Стенд для разборки мостов | 1450 | 1 | 830×660 | | |
8 | Сверлильный станок | СЧС-1 | 1 | 710×390 | | |
9 | Тумба для инструмента | П-009 | 1 | 800×500 | | |
10 | Установка для проверки гидросистем рулевого управления | К-465 | 1 | 910×730 | | |
11 | Тележка для агрегатов | П-523 | 1 | 1000×600 | | |
12 | Ларь для отходов | 01-03 | 1 | 800×500 | |
Рисунок 3. Стенд «Р-770Е» для разборки и сборки ДВС.
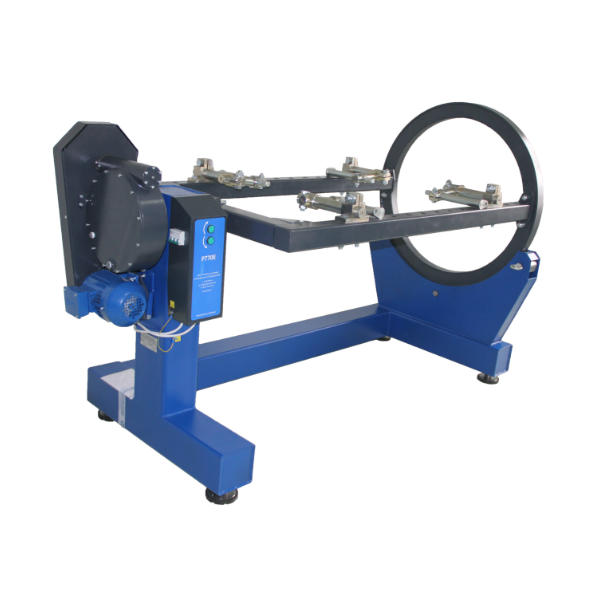
5.2 Технологический процесс агрегатного участка
Агрегаты, снятые с автомобиля поступает на участок, где на специальных стендах производится его испытание. Используя приспособления, производят разборку двигателей, передних и задних мостов, коробок передав и сцеплений. Технологический процесс ремонта агрегатов производят в следующем порядке.
Агрегат разбирается и детали его промываются и обезжириваются горячим содовым раствором в моечной машине ГОСНИТИ-574. Промытые детали контролируют путем обмера или внешнего осмотра и сортируют на годные, подлежащие ремонту и негодные. Делается заключение о возможности дальнейшего их использования. В случае необходимости, производится изготовление или ремонт деталей на слесарно-механическом участке.
Взамен изношенных деталей устанавливают заведомо исправные. После сборки двигателей, коробок передач или мостов производят их обкатку.
Разборку и сборку агрегатов производят на специальных стендах. Разборка и сборка двигателей осуществляется на стенде Р-235, ремонт задних и передних мостов осуществляется с использованием стенда 2450. Разборка и сборка коробок передач выполняется на стенде Р-201. Разборка и сборка ступиц колес,дифференциалов и сцепления производится в соответствующих приспособлениях, монтируемых на верстаках. Неплотное прилегание рабочей поверхности клапана к гнезду устраняют притиркой при помощи приспособления ОГР-1841А. При сильном износе производят шлифование фаски головки клапана на станке Р-108 или гнезд седел клапанов в головке блока цилиндров на станке 2447.
Контроль и дефектовка деталей производится на специальном верстаке ОРГ-1468-01-090А и поверочной плиты с использованием контрольных приспособлений и измерительного инструмента.
Для мелких прессовых работ (выпрессовки и запрессовки втулок, пальцев, подшипников и др.) применяется гидравлический пресс модели 21355М. Он же может использоваться для правки мелких деталей.
5.3 Техника безопасности в агрегатном участке.
При выполнении работ на агрегатном участке возможны следующие опасные и вредные производственные факторы:
- термические факторы (ожоги при контакте с горячей поверхностью),
- падение узлов, агрегатов, инструмента и деталей,
- вращающиеся элементы испытываемых агрегатов и элементов привода оборудования,
- осколки металла при его обработке,
- пониженная температура воздуха в холодный период года,
- недостаточная освещенность.
Для уменьшения вероятности и ликвидации выше перечисленных факторов необходимо выполнять следующие требования:
- рабочие производящие ремонт и обслуживание агрегатов, узлов и деталей должны обеспечиваться исправным инструментом и приспособлениями,
- снятые с автомобиля агрегаты, узы следует устанавливать на специальные устойчивые подставки,
- выпрессовка втулок, подшипников и других деталей должна производится на специальном оборудовании,
- при работе с гаечными ключами необходимо подбирать их в соответствии с размерами гаек (не допускается затяжка гайки рывком),
- вращающиеся части стендов и агрегатов при испытании должны иметь защитные кожухи.
Во время работы оборудования нельзя снимать, ставить или открывать ограждения. На станках нельзя сидеть, облокачиваться на них, передавать через них, а также класть на них инструменты и изделия. Не разрешается пользоваться ручной подачей охлаждающей жидкости на металлорежущих станках.
Под ногами рабочего, должна быть прочная деревянная решетка.
Приступая к работе на станке, рабочий должен тщательно одеться: застегнуть куртку или халат на все пуговицы, проверить застежки на манжетах рукавов, убрать концы завязок, спрятать волосы под головной убор. Это особенно важно при работе на стендах с открытыми вращающимися частями.
Не следует работать на станках в рукавицах во избежание захвата их вращающимися частями. В рукавицах разрешается только ставить или снимать тяжелые агрегаты, после чего рукавицы необходимо снимать.
Заключение
В данном курсовом проекте видно, что автомобильный транспорт стал быстрее развиваться, стали вводиться новые технологии, которые раньше не применялись. В исследовательском разделе были решены следующие задачи: выбор производственного оборудования, работы, выполняемые в данной зоне. Это способствует быстрому нахождению неисправностей в автомобиле и их дальнейшему устранению тем самым повышается техническая готовность автомобиля. Из расчетно-технологического процесса видно, что при правильном подборе оборудования и рабочих повышается качество работ. В организационном разделе был выбран метод организации ТО и ТР на предприятии. Подводя черту под всем вышесказанным, думаю, можно сказать, что все основные задачи, поставленные в части данного проекта мною были решены. Данная работа сыграла огромную роль в закреплении как теоретических, так и практических навыков по организации и технологии ТО и ТР автомобилей, полученных за период обучения.