ВУЗ: Не указан
Категория: Не указан
Дисциплина: Не указана
Добавлен: 07.11.2023
Просмотров: 67
Скачиваний: 2
ВНИМАНИЕ! Если данный файл нарушает Ваши авторские права, то обязательно сообщите нам.
для чугуна составляет от 40 МПа до 60 МПа,
PzM = 8,84 - давление газов в цилиндре при вспышке на режиме максимального крутящего момента (из теплового расчета), МПа.
4.2.2 Расчет силовых шпилек (болтов) крепления головки
Силовые шпильки (болты) крепления головки проверяются на усталостную прочность от газовых сил и усилия предварительной затяжки.
За расчетный режим следует принять режим максимального крутящего момента. Материал шпильки – сталь 45.
Диаметр шпилек (болтов) ориентировочно может быть определен на основании статистических данных
d = (0.12 - 0.14) D=0,13·0,0917=0,01183м,
где D = 0,0917 - диаметр цилиндра, м.
Полученное значение d скорректируем до ближайшего значения по ГОСТ (приложение 2). d = 12 мм.
Параметр метрической резьбы М16х1,5. Для данной резьбы площадь сечения по внутреннему диаметру резьбы f=155,0


Газовая сила, действующая на шпильку (болт), МН, определяется следующим образом:

где PzM - максимальное давление газов при вспышке в цилиндре на режиме максимального крутящего момента, МПа;
iшп - число шпилек (болтов), окружающих один цилиндр. При верхнеклапанном газораспределительном механизме iшп = 6.
Fпр - площадь проекции камеры сгорания на плоскость, перпендикулярную оси цилиндра, ограниченную завальцованным краем прокладки, м. При верхнеклапанном газораспределительном механизме
Fпр = 1,1·Fп = 1,1·((πD2)/4) = 1,1·((3,14·0,0917 2)/4) = 0,0073 м2,
где Fп - площадь днища поршня;
Усилие предварительной затяжки шпильки (болта), МН,

где m = 3 - коэффициент затяжки шпильки (болта);
χ=0,25 - коэффициент основной нагрузки резьбового соединения.
Максимальная сила, растягивающая шпильку (болт), МН,

Максимальные и минимальные напряжения, возникающие в шпильке (болте), МПа,


= 0,03622/(155,0 ·10-6) = 233,677 МПа,
где f - площадь минимального сечения стержня шпильки (болта), м2.
Среднее значение и амплитуда напряжений цикла, МПа,
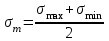
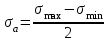
После этого определяем, в какой области диаграммы усталостной прочности лежит данный цикл.
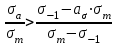


Так как неравенство не выполняется, то запас прочности определяется по пределу текучести:
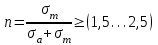

В этих формулах:
a = 0,1 - коэффициент приведения данного цикла к равно опасному симметричному;
-1 = 300 МПа - предел усталости материала при симметричном цикле, МПа;
т = 340 МПа - предел текучести материала, МПа.
4.3 Расчет деталей поршневой группы
4.3.1 Расчет поршня
Материал поршня - эвтектический алюминиевый сплав с содержанием диоксида кремния около 14%.
Днище поршня проверяется на поперечный изгиб как круглая плита, свободно опирающаяся на кольцо и нагруженная равномерно распределенной нагрузкой максимального давления газов при вспышке на режиме максимального крутящего момента PzM.
Максимальное напряжение изгиба в диаметральном сечении днища поршня равно:
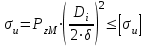

где PzM - максимальное давление газов при вспышке на режиме максимального крутящего момента, МПа;
Di - внутренний диаметр головки поршня в зоне первого поршневого кольца, м;
- толщина днища поршня без ребер, м;
[и] =20…25 - допустимое нормальное напряжение изгиба для алюминиевых сплавов, МПа.
Так как напряжение значительно превышает допустимое, то устанавливаем ребра жесткости на днище поршня.
При наличии ребер жесткости на днище поршня допускаемые напряжения увеличиваются в 3 - 4 раза.
Сечение "X - X" головки поршня на уровне нижнего маслосъемного кольца, ослабленное отверстиями для отвода масла, проверяется на сжатие и разрыв.
Напряжения сжатия возникают от максимальной силы давления газов при вспышке на режиме максимального крутящего момента PzM:
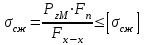

где Fx-x - площадь сечения "X - X" поршня, м2;
Fп - площадь поршня, м2;


(3,14/4)*(0,09796^2-0,07776^2)-8*0,00009=0,00207 м^2.
[cж] = 30…40 - допустимое нормальное напряжение сжатия для алюминиевых сплавов, МПа.
Размеры основных элементов поршневой группы представлены на рисунке 1.
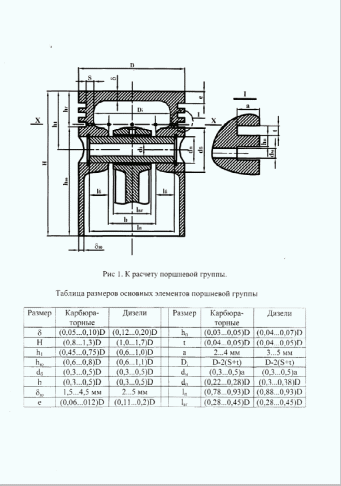
Рисунок 1. К расчету поршневой группы
Размеры основных элементов поршневой группы:










Напряжения разрыва

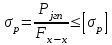
,

где

Pjгг = 90*0,0066*0,0046*653,122*(1+0,25)*10-6 = 0,001457 МН,
где mгп- конструктивная масса головки поршня с кольцами, расположенная выше сечения "X - X", кг/м2:


где mпг = 150 кг/м2 - конструктивная масса поршневой группы, принятая в динамическом расчете, кг/м2;

где - угловая скорость вращения коленчатого вала при максимальной мощности, рад/с;





= R/L = 0,25 - отношение радиуса кривошипа к длине шатуна, принятое в динамическом расчете;
[σр] = 4 … 10 - допустимое напряжение растяжения для алюминиевых сплавов, МПа.
Юбка поршня проверяется на износостойкость (давление) от максимальной боковой силы Pбок на режиме максимального крутящего момента:
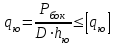

где





4.3.2 Расчет поршневого пальца
Материал поршневого пальца – сталь 15Х.
Максимальное напряжение в пальцах двигателей внутреннего сгорания имеет место на режиме максимального крутящего момента.
Газовая сила, передающаяся через палец от поршня на верхнюю головку шатуна, МН:

где


Сила инерции поршневой группы, передающаяся на верхнюю головку шатуна, МН:




где



R - радиус кривошипа, м;
= R/L - отношение радиуса кривошипа к длине шатуна, принятое в динамическом расчете.
Расчетные силы, действующие на палец во втулке верхней головки шатуна Pвг и в бобышках поршня Pбп:
Pвг = Pг +Pjпг = 0,05834-0,0003592 = 0,05798 МН;
Pбп = Pг +КпPjпг = 0,05834 +0.75*(-0,0001962) = 0,05819 МН,
где Кп = 0.75 - коэффициент, учитывающий массу поршневого пальца.
4.3.3 Расчет поршневого пальца на прочность
Нормальные напряжения поперечного изгиба в опасном сечении в середине поршневого пальца, МПа,
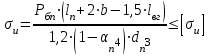

Касательные напряжения от среза пальца в опасных сечениях, расположенных между бобышками и верхней головкой шатуна, МПа:
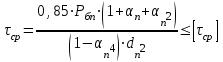

Максимальная овализация (наибольшее увеличение горизонтального диаметра) подсчитывается для средней, наиболее нагруженной части пальца, мм: