Файл: Реферат по теме Современные способы защиты металлов от коррозии.rtf
Добавлен: 07.11.2023
Просмотров: 268
Скачиваний: 9
ВНИМАНИЕ! Если данный файл нарушает Ваши авторские права, то обязательно сообщите нам.
Если трубу, по которой, к примеру, транспортируется нефть, ничем не защищать изнутри, то лет через пять из-за соприкосновением с кислой средой нашего «черного золота» коррозия проест ее насквозь. Имеющиеся зарубежные средства, которые сейчас наносят на трубы, способны продлить срок их службы до 15-20 лет.
Вещество, смоделированное Константином Катиным, относится к новому классу защитных покрытий, которые отличает от существующих абсолютная экологичность, низкая цена и высокая эффективность.
Сам по себе химический состав нового вещества не содержит никакого секрета, - оно состоит в основном из водорода, углерода и азота. Однако его защитные свойства определяются многими факторами, среди которых - уникальная пространственная структура молекулы, ее адгезия, то есть сцепление со стальной поверхностью. Именно сложное взаимодействие всех этих факторов, по словам Константина Катина, и определяет эффективность защитного средства.
- Мы сейчас идем по пути создания таких методов защиты, чтобы они могли сохранять трубы на порядок дольше, - говорит ученый. - Это будет достигаться путем периодического подмешивания защитного вещества в саму нефть, которая идет по трубопроводу.
Внутри трубы оно будет постепенно оседать на стальной поверхности, восстанавливая покрытие. Требования к такому средству высоки: оно не должно портить качество самой нефти, хорошо оседать на стенках трубы, да в основном в тех местах, где его особо не хватает.
Кроме нефтяных труб, по словам Катина, средство, благодаря его безопасности, можно будет использовать для защиты от ржавчины стальных конструкций мостов. Оно, конечно, будет потихоньку смываться морскими или речными потоками, но если периодически возле конструкций добавлять в эти потоки антикоррозийное вещество, оно легко будет «примагничиваться» к стальным сваям, восстанавливая их защитный слой.
По словам ученого, несмотря на практическую значимость противодействия коррозии, подбор подходящих веществ до сих пор часто проводится методом проб и ошибок. Иными словами, все зависит от интуиции, творческого озарения исследователя.
- Сейчас интуитивная составляющая в нашей работе преобладает, - говорит Катин. - Но постепенно мы начинаем переходить к так называемой рациональной схеме, передавая «полномочия» в этом искусственному интеллекту.
19931
4 МАТЕРИАЛА ПО ТЕЕ
- Вы сейчас видите эти направления?
- Основная задача химиков с давних времени и до сих пор - создать молекулу, вещество с каким-то конкретным набором свойств. Раньше для этого перебирали различные вещества, иногда они получались случайно, как это произошло со стеклом. Теперь мы придумываем концепцию, а искусственный интеллект помогает довести идею до абсолюта. Только ему благодаря огромной базе, заложенной в «мозг», подвластно быстро перебрать все известные вещества, вспомнить, какими свойствами они обладают, скомбинировать эту информацию и предложить нам сразу сотни необходимых вариантов. Он только комбинирует то, что у же есть, но не могут создать чего-то принципиально нового.
Наша цель - создать такую программу, которая сможем осуществить компьютерный перебор множества молекул и найти такие ингибиторы, эффективность которых приблизится к 100% (новое вещество обладает эффективностью 97,6%).
Недавно вещество, смоделированное российскими учеными, было синтезировано их коллегами в Турции, в Республиканском университете Сиваса. Сейчас специалисты заняты его испытанием для защиты различных поверхностей. Не исключено, что срок службы стальных конструкций, покрытых им, превысит существующие.
Антикоррозийные технологии: что нового на рынке
Современные технологии не стоят на месте в любой области и отрасль антикоррозии – не исключение. Ежегодно проводятся различные форумы и выставки, где презентуются инновационные способы антикоррозийной защиты. Однако, пока инновации прочно войдут в жизнь стандартных потребителей – пока неизвестно. Чтобы типовому автолюбителю или даже владельцу завода металлоконструкций применить для защиты металлов новую технологию, придется постараться – вложить немало сил, времени и, конечно, средств. К тому же, новые технологии – это всегда риск, так как они не проверены временем. Что лучше использовать – новинки рынка или проверенные методы – расскажем в этой статье.
Новые технологии в защите от ржавчины автомобилей
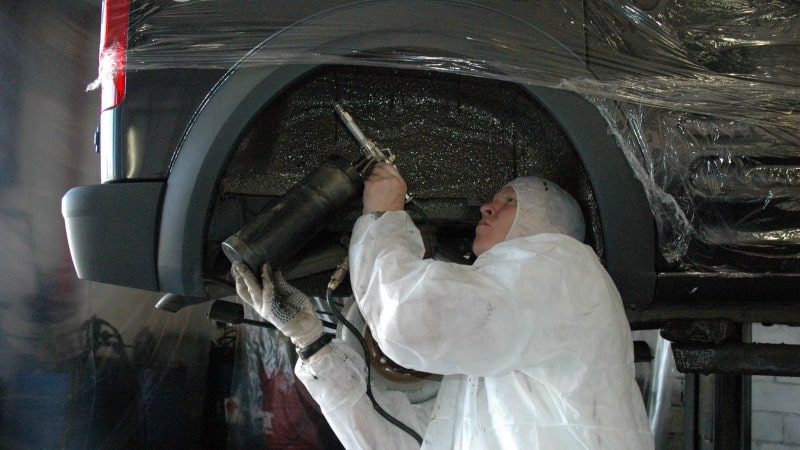
Как защитить автомобиль от коррозии – волнует не только автолюбителей, но и производителей авто по всему миру. Ежегодно появляются новые разработки кузовов с использованием таких материалов, как различные полимеры и стекловолокно. Но, внедрение новых методов защиты естественно удорожает стоимость автомобиля, причем на кругленькую сумму. В итоге, производители вроде бы стараются для конечного потребителя, а в итоге спрос на такие защищенные авто снижается, потому что будущие автовладельцы всегда стремятся сэкономить и приобрести авто подешевле. На автомобили с пробегом пока еще в хорошем состоянии – спрос всегда большой. А в последние пару лет, он продолжает расти просто семимильными шагами.
Автовладельцы готовы ежегодно тратиться на специальные антикоры, обрабатывать авто самостоятельно, оплачивать антикоррозийную обработку в автосервисе, чем приобретать автомобиль уже в хорошем антикоррозийном покрытии, но дороже на пару сотен тысяч рублей. Хоть в погоне за экономией, они тратят и больше. Потому что эти деньги, можно тратить небольшими частями, а не нужно отдавать сразу. Таков уж российский менталитет.
Чем же пользуются сегодня для защиты от коррозии?
Выбор антикоррозийных средств в наши дни весьма велик. Все они подразделяются на группы и виды в зависимости от желаемого результата и характера обрабатываемых поверхностей.
Для автомобилей из года в год популярными остаются такие средства:
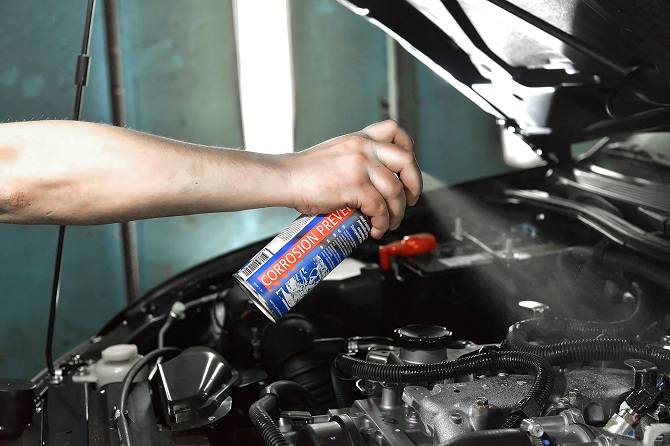
-
Сланцевая мастика - используется для обработки внешних сторон колесных арок и днища. Результатом обработки этим средством является образование битумной пленки, что обеспечивает полную гидроизоляцию открытых частей кузова. Помимо автосервиса, сланцевые мастики используют в строительстве и в обычном быту.
-
Резинобитумной мастикой также обрабатываются днища и колесные арки машин – но, в данном случае, с обеих сторон – внутренней и наружной. Это средство защищает от «бомбардировок» гравием и хорошо устойчиво к низким температурам (выдерживает мороз до –60С). Полимерно-битумный слой весьма эластичен и практически не деформируется, поэтому можно не бояться его отслоения или растрескивания. Такая обработка полезна, если вы активно эксплуатируете свое транспортное средство в сильные морозы.
-
Битумно-каучуковая мастика также защищает внешние и внутренние поверхности, в том числе и не покрытые лакокрасочными материалами – пороги, днище, арки, внутренние поверхности багажника, капота и крыльев, а также пол салона автомобиля. Кроме того это средство используется для прочих металлических и даже деревянных конструкций (например, столбов линий электропередач) с целью их гидроизоляции.
-
Мовиль – популярное и эффективное средство для борьбы со ржавчиной. Помимо уже названных выше деталей, им можно надежно защитить также места соединений и стыков деталей автомобильного кузова. Мовиль обладает высокими проникающими характеристиками, хорошо растекается и быстро образует специальный воскообразный слой, качественно вытесняя влагу с металлических поверхностей. Им можно дополнительно обрабатывать металл после использования других средств, а разновидностей мовилей существует достаточно много – силиконовые, преобразующие ржавчину и прочие.
-
Пороговый автоконсервант используется не только для защиты порогов, но и эффективно бережет от агрессивного воздействия окислителей двери, лонжероны, стойки и прочие детали. Он также хорош для временной защиты колесных арок, днища и краски на стыках. При обработке скрытых полостей, это вещество можно наносить после предварительного покрытия поверхностей консервирующими составами. Автоконсервант порогов не боится уже появившейся ржавчины и влаги, успешно борясь с ними на радость автовладельцу.
-
Антигравий двух основных цветов – черного и серого – защищает кузов в местах, которые наиболее часто подвергаются разрушительным абразивным атакам: двери, арки колес, спойлер, пороги. Это текстурное покрытие изготавливается на каучуковой основе с использованием битума и смол. Оно защищает машину не только от ржавчины и влажности, но и от вылетающих из-под колес камушков и дорожной соли – одной из главных неприятностей зимнего автовождения. Серый и черный антигравий можно окрасить сверху разнообразными красками различных цветов, в зависимости от желания владельца авто.
Как борются с коррозией в промышленных масштабах?
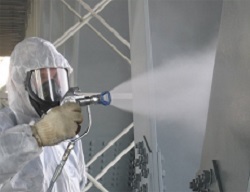
Методы борьбы с коррозией беспокоят не только автовладельцев, а всех, кто имеет дело с металлическими конструкциями: заводы, производящие и сами использующие металлоконструкции, кузницы и компании по производству кованых изделий.
Кто-то выбирает проверенные методы защиты от ржавчины, используемые уже более 160 лет, а кто – то все-таки понимает, что прогресс не стоит на месте и применяет новые технологии, которые обходятся дешевле и удобнее применяются.
Так на рынке антикоррозии пока остаются несколько популярных, проверенных методов:
-
Горячее цинкование; -
Гальваническое цинкование; -
Термодиффузионное; -
Газо-термическое; -
Холодное цинкование.
Гальваническое цинкование, термодиффузионное и газо-термическое – применяют редко, из-за сложности процесса, очень мало компаний на рынке предлагают эти способы. Малая конкуренция, как все мы знаем, ведет к большой стоимости, что не выгодно производителям и потребителям. Самыми распространенными и востребованными остаются два метода: горячее и холодное цинкование.
Горячее цинкование – заключается в окунании металлических конструкций в ванны с антикоррозийным средством – расплавленным цинком. После окунания конструкции просушивают, подвешивая их. Металлические конструкции приобретают сплошное защитное покрытие без пропусков, защищены даже труднодоступные места.
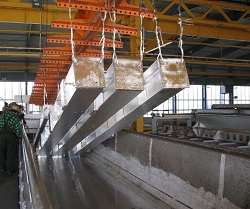
-
Преимущества: цинк проникает внутрь конструкций, защищает все труднодоступные места, металлы приобретают привлекательный внешний вид. Вы просто отвозите конструкции в специальной цех и забираете готовыми, с антикоррозийным покрытием.
-
Недостатки: не подходит для очень больших конструкций – не помещаются в ванну, необходима перевозка конструкции на место проведения процедуры оцинковки и перевозить обратно, за счет этого увеличивается стоимость, к конструкциям необходимо приваривать «ушки», чтобы окунать их и сушить, а высокие температуры (более 400°С) могут деформировать конструкцию.
Холодное цинкование – это нанесение на подготовленную поверхность металлов особых грунтов или красок с большим содержанием цинка (95 и более %). Сегодня, это самый современный, простой, быстрый и экономичный способ защиты металлов от коррозии, являющийся по сути новой технологией – применяется с 80-х годов.
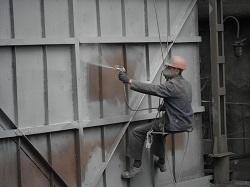
-
Преимущества: удобно наносить на конструкции прямо на месте их эксплуатации, не нужно никуда перевозить, экономичная стоимость – доступные цены составов, надежная, долговечная защита.
-
Недостатков практически нет: минусами можно считать серый, матовый цвет, который приобретают металлы после нанесения, но возможна последующая окраска. Также небольшой сложностью является самостоятельное применение, но нанесение практически не отличается от обычной покраски, поэтому с процессом легко справляются даже не профессионалы красочного дела.
Вывод
Новейшей технологии в области антикоррозии, которая доступна сегодня любому потребителю – будь то автовладелец или директор крупного завода металлоконструкций - является холодного цинкование. Несмотря на то, что технология является новой по сравнению с другими методами, например, горячим цинкованием, холодное цинкование уже успело зарекомендовать себя как надежный, проверенный способ защиты от коррозии, работающий до 50 и более лет.
Самые современные, проверенные и надежные составы для холодного цинкования вы можете найти в нашем магазине.
Есть вопросы по выбору состава? Обращайтесь в представительство в вашем городе:
в Санкт-Петербурге: +7 (812) 603-41-53, +7 (921) 927-58-47
в других городах: 8 (800) 707-53-17
e-mail: info@terazinc.ru