ВУЗ: Не указан
Категория: Не указан
Дисциплина: Не указана
Добавлен: 08.11.2023
Просмотров: 11
Скачиваний: 1
ВНИМАНИЕ! Если данный файл нарушает Ваши авторские права, то обязательно сообщите нам.
Вариант 6
Задание №1
1. Изобразите схему устройства электродуговой печи. Опишите способы выплавки стали в электродуговых печах с окислением примесей и методом переплава.
Производство стали в электродуговых печах
Плавильные электропечи имеют преимущества по сравнению с другими плавильными агрегатами:
• легко регулировать тепловой процесс, изменяя параметры тока;
• можно получать высокую температуру металла;
• можно создавать окислительную, восстановительную, нейтральную атмосферу и вакуум, что позволяет раскислять металл с образованием минимального количества неметаллических включений.
Электропечи используют для выплавки конструкционных низко- и высоколегированных сталей, инструментальных и специальных сталей и сплавов. Различают дуговые и индукционные электропечи.
Дуговая печь, схема которой приведена на рисунке 1, питается трехфазным переменным током, имеет три цилиндрических электрода 4 из графитированной массы, закрепленных в электрододержателях, к которым подводится электрический ток по кабелям 7. Между электродом и металлической шихтой возникает электрическая дуга. Корпус печи имеет форму цилиндра.
Снаружи он заключен в прочный стальной кожух, внутри футерован основным или кислым кирпичом. Съемный свод 3 имеет отверстия для электродов. В стенке корпуса находится рабочее окно 2 (для слива шлака, загрузки ферросплавов, взятия проб), закрытое при плавке заслонкой.
| |
Готовую сталь 6 выпускают через сливное отверстие со сливным желобом 1. Печь опирается на секторы и имеет опорные ролики 5 для наклона в сторону рабочего окна или желоба. Печь загружают при снятом своде.
Вместимость печей составляет от 0,5 до 400 т. В металлургических цехах используют электропечи с основной футеровкой, в литейных – с кислой.
В основной дуговой печи осуществляется плавка двух видов: на шихте из легированных отходов (методом переплава) и на углеродистой шихте (с окислением примесей).
Плавку на шихте из легированных отходов ведут без окисления примесей. После расплавления шихты из металла удаляют серу, наводя основной шлак, при необходимости науглероживают и доводят металл до заданного химического состава. Проводят диффузионное раскисление, подавая на шлак измельченные ферросилиций, алюминий, молотый кокс. Так выплавляют легированные стали из отходов машиностроительных заводов.
Плавку на углеродистой шихте применяют для производства конструкционных сталей. В печь загружают шихту: стальной лом, металлизированные окатыши, чушковый передельный чугун, железную руду для окисления примесей, электродный бой или кокс для науглероживания металла, известь.
Опускают электроды, включают ток. Шихта под действием электродов плавится, металл накапливается в подине печи. Во время плавления шихты кислородом воздуха, оксидами шихты и окалины окисляются железо, кремний, фосфор, марганец и частично углерод. К концу «окислительного» периода заканчивается удаление фосфора в основной железистый шлак.
| |
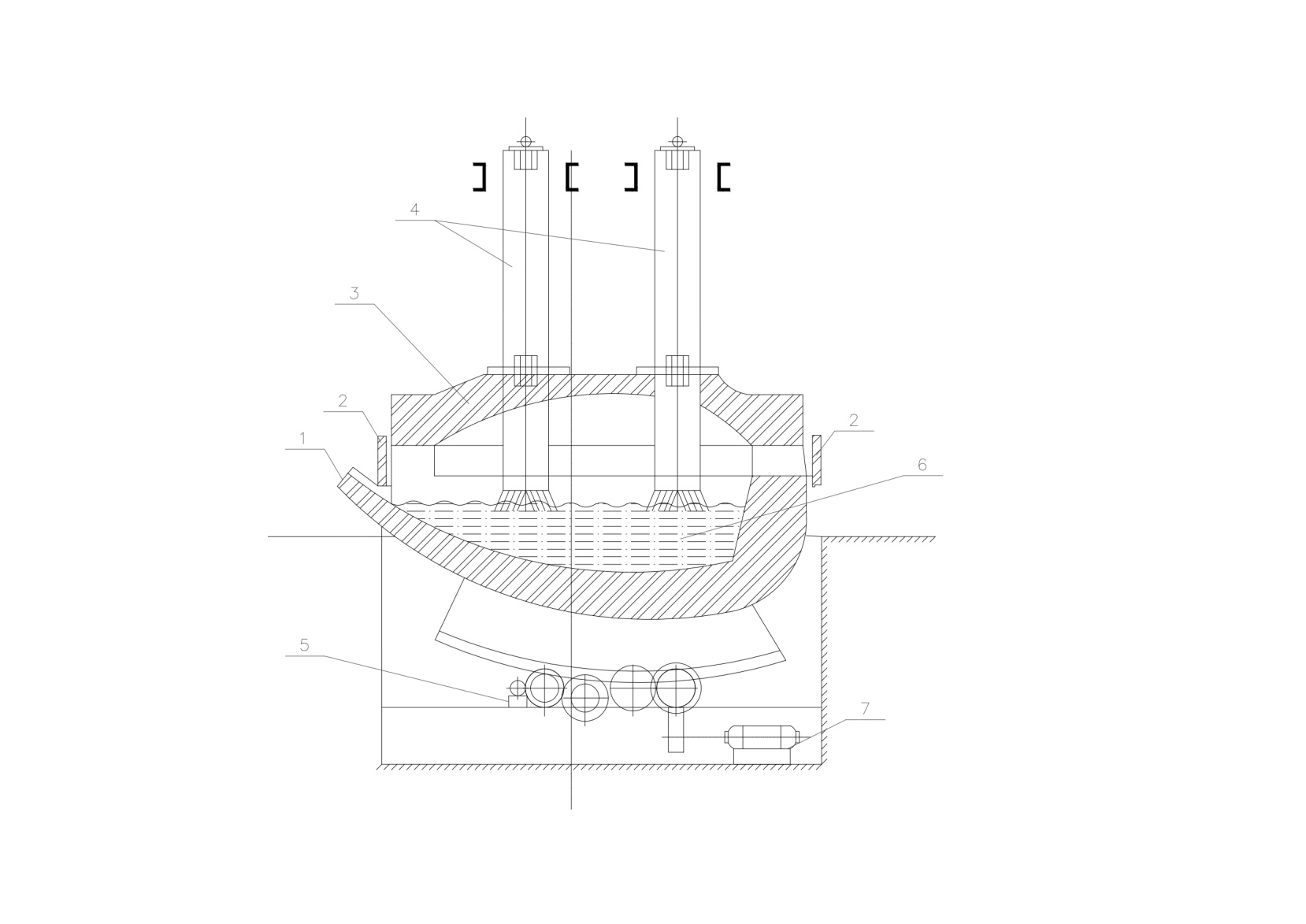
Рисунок 1 - Схема дуговой плавильной печи
После нагрева до 1500–1540 °C начинается период «кипения» металла, для дальнейшего окисления углерода.
При достижении нужного количества углерода прекращают кипение и приступают к удалению серы, раскислению для получения металла заданного химического состава. Раскисление производят осаждающим и диффузионным методами. Для диффузионного раскисления наводят шлак, содержащий известняк и молотый кокс. Благодаря повышенному содержанию в шлаке оксида кальция и пониженному содержанию оксида железа в него из металла переходит сера. Для определения химического состава металла берут пробы и при необходимости вводят в печь ферросплавы для получения заданного химического состава. Затем выполняют конечное раскисление алюминием и силикокальцием, выпускают сталь в ковш.
При выплавке легированных сталей в дуговых печах в сталь вводят легирующие элементы в виде ферросплавов.
В дуговых печах выплавляют качественные и высококачественные углеродистые и легированные стали – конструкционные и инструментальные.
Задание №2
2. По эскизу детали (рис.11.) разработайте эскиз отливки с модельно-литейным указанием, приведите эскизы металлических модельных плит, стержневого ящика и собранной литейной формы (в разрезе).
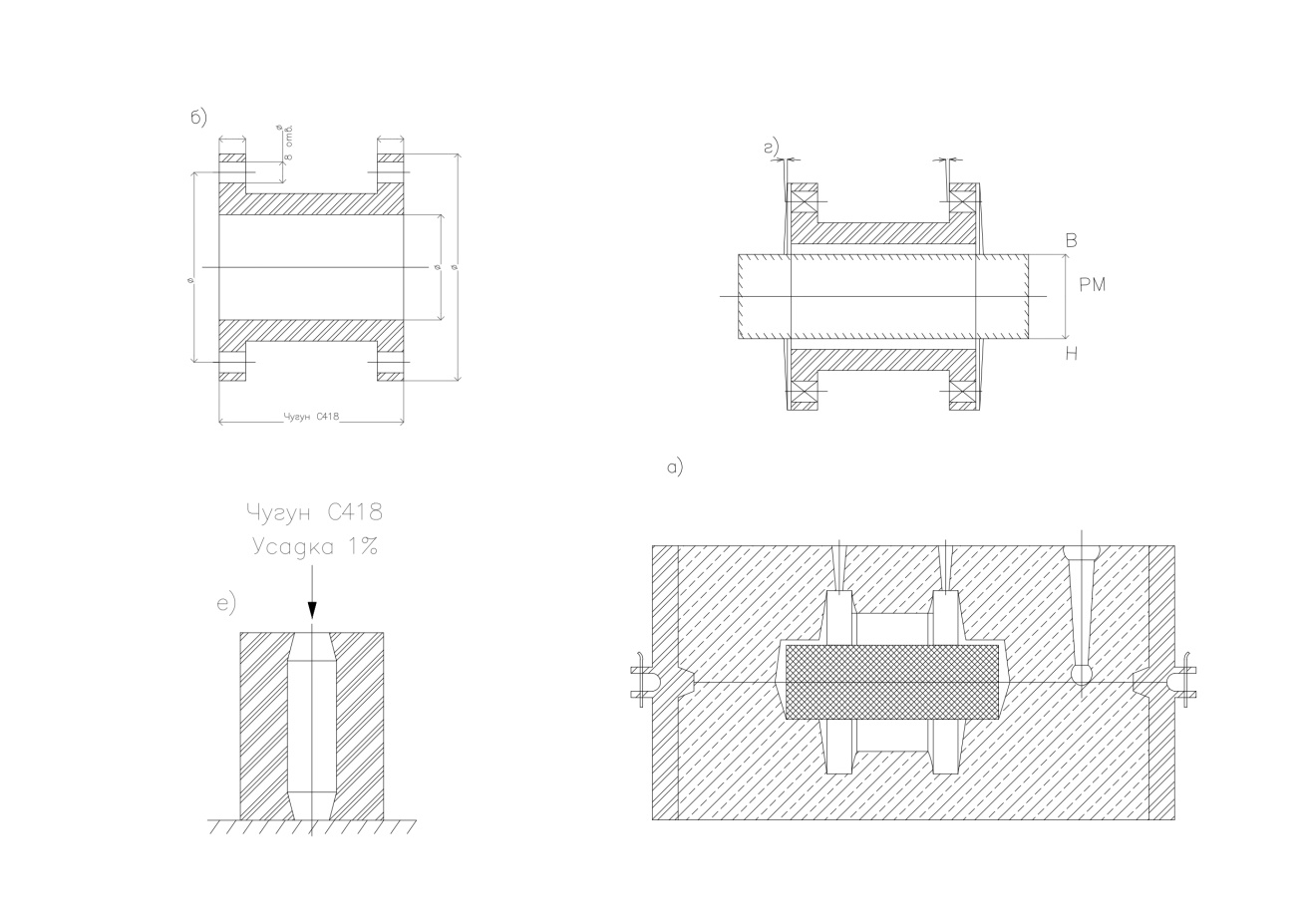
Задание №3
3. Опишите последовательность производства отливок по выплавляемым моделям и приведите поясняющие эскизы. Укажите преимущества, недостатки и области применения этого метода литья.
Сущность метода и область применения. Сущность состоит в том, что по неразъемной легкоплавкой модели изготавливают неразъемную разовую форму. Модели из этой формы выплавляют, а образовавшуюся полость заливают жидким металлом. При этом способе получаемые отливки настолько точны, что объем механической обработки уменьшается на 80... 100% и в 1,5...2 раза сокращается расход жидкого металла. Высокая точность и чистота поверхности отливки обеспечиваются: применением неразъемных моделей (модели выплавляют, и не требуется их расталкивать); отсутствием формовочных уклонов; изготовлением стержней в процессе формовки, а не отдельно в стержневых разъемных ящиках; использованием маршалита (кварцевая мука) в качестве наполнителя в формовочной смеси, что обеспечивает получение гладкой поверхности отливки.
Литье по выплавляемым моделям применяют при производстве отливок очень сложной конфигурации из любых литейных сплавов, в том числе из высоколегированных сталей, имеющих высокую температуру плавления и трудно поддающихся механической обработке и ковке. Этим способом можно получать отливки массой 0,02... 100 кг, с толщиной стенок до 0,5 мм и отверстиями диаметром • до 2 мм.
2. Технология получения отливок литьем по выплавляемым моделям включает следующие этапы: а) изготовление разъемных пресс-форм; б) получение неразъемных легкоплавких моделей в пресс-формах; в) изготовление неразъемной разовой формы по легкоплавким моделям; г) выплавление моделей из формы; д) обжиг формы; е) заливка формы металлом и выбивка готовых отливок.
Разъемные пресс-формы изготовляют из стали или алюминиевых сплавов. Полость пресс-формы точно повторяет конфигурацию и размеры будущей детали с учетом усадки модельного состава.
Неразъемные легкоплавкие модели получают запрессовкой в пресс-форму модельного состава, нагретого до тестообразного состояния. Для его изготовления широко используют легкоплавкие материалы: парафин, стеарин, воск, церезин, канифоль и др. Легкоплавкая модель в отличие от обычной является точной копией изготовляемой детали: она неразъемна, имеет все внутренние полости, отверстия, резьбу и не имеет стержневых знаков.
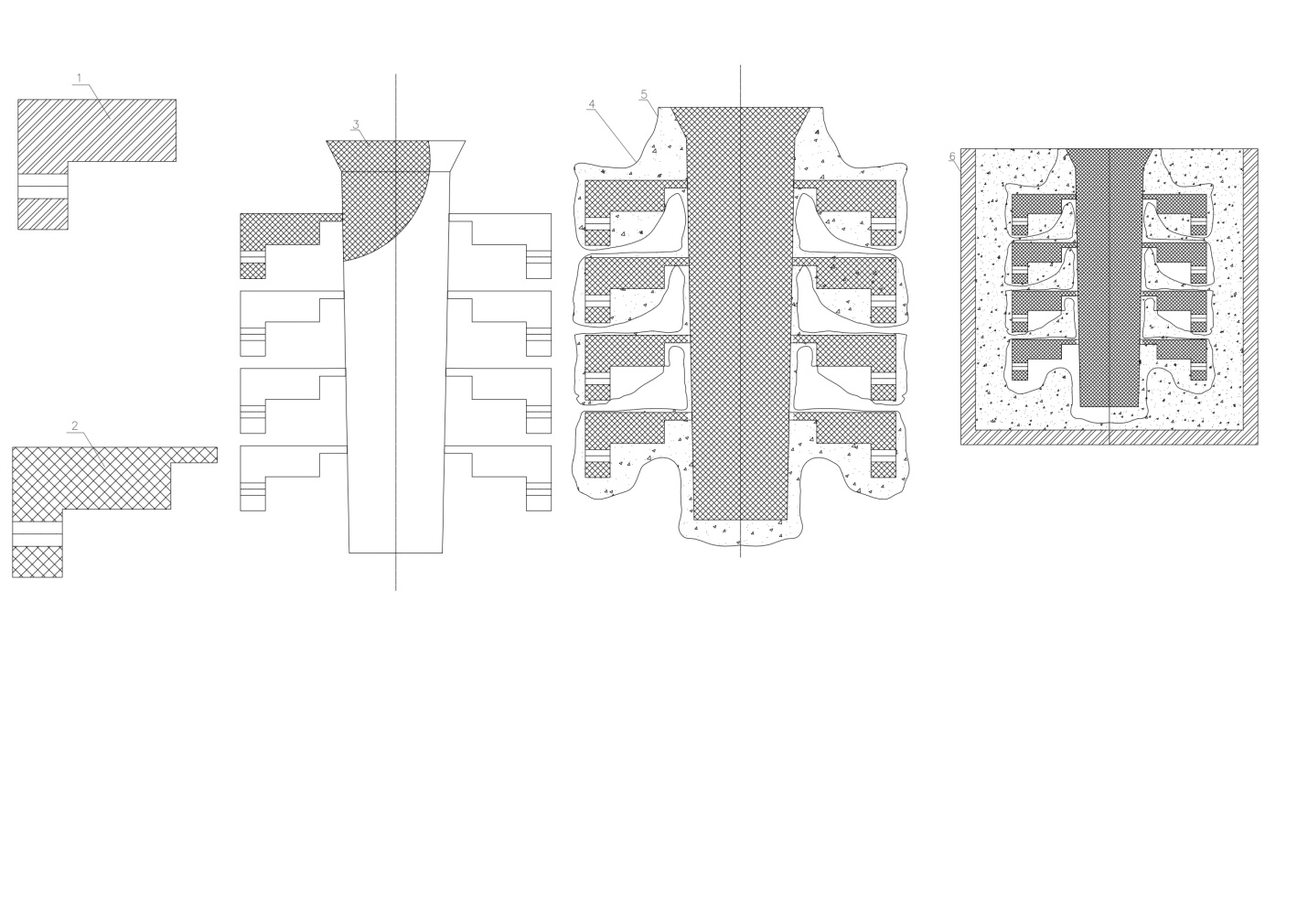
Рисунок 2 - Литье по выплавляемым моделям.
На рисунке 2 приведен чертеж отливаемой детали 1 и неразъемной модели, отличающейся от нее наличием питателя 2. Модели питателями «припаивают» к общему легкоплавкому стояку 5, и в результате получают блок моделей. Чтобы изготовить литейную форму, готовый блок моделей окунают в огнеупорную смесь, представляющую собой суспензию маршалита (60...70 %) в гидролизованном этилсиликате (30...40 %). После окунания на моделях, питателях и стояке остается тонкая огнеупорная пленка смеси 4. Эта же смесь заполняет все полости и отверстия в моделях, образуя стержни. Для упрочнения огнеупорной пленки блок моделей посыпают мелким сухим кварцевым песком 5. Прилипая к сырой пленке, песок образует огнеупорный слой, который сушат либо на воздухе, либо помещая блок моделей в аммиачную камеру для ускоренной химической сушки. Когда слой высыхает, операции окунания, посыпания песком и сушки повторяют от 3 до 5 раз. После сушки последнего огнеупорного слоя получают форму в виде многослойной оболочки с заформованными легкоплавкими моделями. Форму помещают в сушильный шкаф и выдерживают при температуре более 100 °С или погружают в горячую воду. Модели и элементы литниковой системы (стояк и питатели) плавятся и вытекают из формы. Для выжигания остатков модельного состава из полости, а также для упрочнения оболочки полученную литейную форму в металлическом ящике 6 засыпают металлической дробью и помещают в термическую печь, где обжигают при температуре 800...900 °С. Заливку металла производят в горячую форму, что дает возможность получать тонкостенные сложной конфигурации отливки. Выбивку отливок и отделение литников осуществляют на виброустановках.
Преимущества метода
Главный плюс литья по выплавляемым моделям — тщательность передачи формы и низкая шероховатость поверхности. Кроме того, в наличии другие достоинства:
-
Доступно производство деталей из сплавов, слабо подверженных механической обработке. -
Снижается необходимость в дальнейшей механической обработке. -
Отливаются изделия, которые иными методами пришлось бы изготавливать частями и собирать воедино. -
При крупных сериях достигается снижение удельной трудоемкости (в расчете на одно изделие) и его себестоимости. -
Возможность механизации и частичной автоматизации подготовительных операций самого литья. -
Недостатки литья по выплавляемым моделям -
Несомненные преимущества способа, казалось бы, должны были обеспечить его доминирование среди других способов. Однако, несмотря на популярность метода литья по выплавляемым моделям, недостатки сдерживают его широкое распространение. Основной недостаток заключается в сложности многоэтапного технологического процесса. Он требует достаточно сложного и дорогостоящего технологического оборудования для подготовительных этапов. Для несложных изделий, выпускаемых небольшими сериями, данный метод имеет более высокую себестоимость. -
Для экономически эффективного применения литья по выплавляемым моделям преимущества и недостатки метода сопоставляются, решение о его выборе принимается на основе оценки соотношения цена/качество. Поэтому и применяется он в основном для самых ответственных и дорогостоящих изделий, которые затруднительно получить другим способом, например турбинных лопаток, скульптур, высокоскоростных инструментов и т. п. Еще одна область применения — крупносерийные отливки, на которых эффект масштаба позволяет добиться значительного снижения себестоимости.