Файл: 1. Описание судна и его энергетической установки Рисунок 1 Внешний вид Буксира Азов Стар.docx
ВУЗ: Не указан
Категория: Не указан
Дисциплина: Не указана
Добавлен: 08.11.2023
Просмотров: 88
Скачиваний: 1
ВНИМАНИЕ! Если данный файл нарушает Ваши авторские права, то обязательно сообщите нам.
Средства контроля за работой дизеля и состоянием параметров расположены на щите приборов дизеля:
-
Манометры масла, топлива, наддувочного воздуха. -
Термометры воды, выходящей из дизеля; масла, поступающего в дизель. -
Система для измерения температуры выпускных газов на выходе из каждого цилиндра, перед турбокомпрессором и за турбокомпрессором. -
Тахометр частоты вращения коленчатого вала.
Охлаждающая жидкость внутреннего контура - пресная вода с временной жесткостью с добавлением антикоррозионной присадки.
Системы обслуживающие ГД.
Системы главного дизеля обеспечиваются работой — пуска и реверса, маслоподачи (циркуляционной и цилиндровой смазки), топливоподачи, охлаждения, газовыпуска и воздухоснабжения, системой управления, аварийно-предупредительной сигнализации
Система пуска и реверса.
Безопасность эксплуатации судна прежде всего обеспечивается системой пуска и реверса, поскольку пуск двигателя – это единственное средство привести корпус судна в движение, а реверс – изменить направление движения. Потребность в этих операциях возникает в самые ответственные моменты эксплуатации судна. Она включает в себя главный пусковой клапан 1, воздухораспределитель 5, трубопроводы пускового 2 и управляющего воздуха 4, пусковые клапаны цилиндров 3, пневматические элементы системы управления 7 и защиты 6.
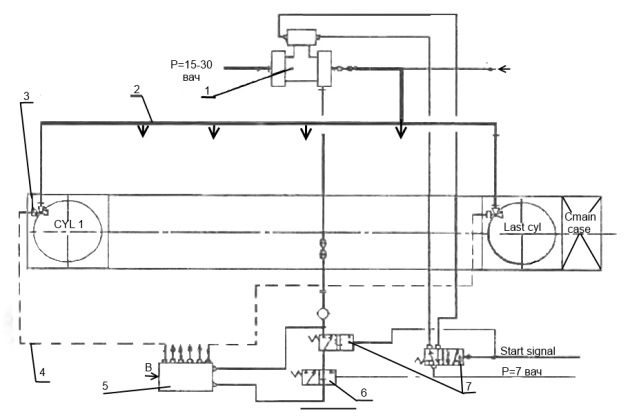
Система смазки (СС) – циркуляционная, комбинированная, предназначена для размещения возимого запаса масла и подачи его под определенным давлением к трущимся поверхностям деталей в целях уменьшения их износа и отвода от них тепла. Система смазки состоит из масляного бака, масляного радиатора трубчато-пластичного типа, масляного насоса, двух фильтров (заборного и тонкой очистки), масло очистителя, масло закачивающего насоса, редукционного и сливного клапанов
Система топливоподачи
Работа системы подачи топлива высокого давления в цилиндр (системы впрыска) имеет исключительное значение для обеспечения длительной надежной и эффективной эксплуатации дизеля. Топливо подается под давлением 600-900 бар (в некоторых современных дизелях – до 1 500-1 600 бар). В систему входят топливный насос высокого давления, форсуночный трубопровод и форсунка.
Поскольку условия работы всех элементов топливной системы определяется высоким давлением впрыска, то к элементам системы предъявляются требования высокой механической прочности, высокой поверхностной твердости деталей и плотности системы, находящейся под давлением. Детали системы изготавливаются с высокой точностью из высоколегированной стали с упрочнением материала путем закалки.
Система охлаждения
Задача обеспечения приемлемого теплового состояния деталей двигателя решается частично системой смазки, но в основном – системой охлаждения. У всех судовых двигателей имеется система водяного охлаждения зарубашечного пространства и крышки, могут быть автономные системы охлаждения форсунок, поршней, продувочного воздуха. Принципиально система охлаждения зарубашечного пространства может быть одноконтурной или двухконтурной. В одноконтурной системе забортная вода подается непосредственно на охлаждение цилиндров. На современных морских судах такие системы не применяются.
Система выпуска отработавших газов (СОГ) предназначена для отвода отработавших газов через эжекторные коробки в атмосферу, обеспечения эжекторного охлаждения систем двигателя и отсоса пыли из воздухоочистителя и циклона. Она состоит из правого и левого ресиверов с соплами и газоводов.
5.Описание конструкции ВДГ и систем обслуживающих вспомогательный дизель – генератор (схемы систем, поперечный разрез дизеля)
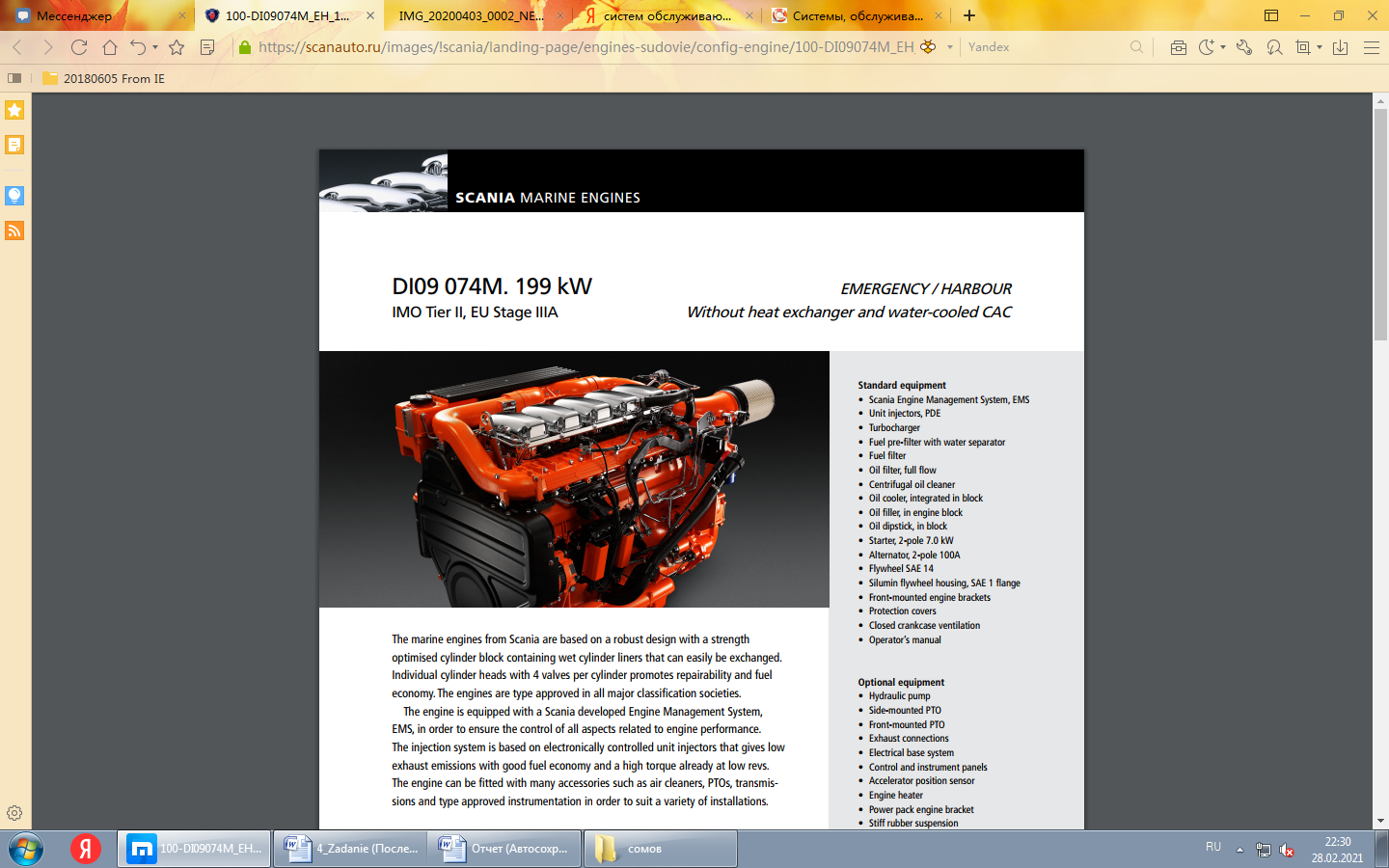
Рис. 5.1 (Scania DI09 074M)
Судовые двигатели Scania имеют прочную конструкцию с блоком цилиндров, оптимизированным по прочности и оснащенным мокрой футеровкой, которую можно легко заменить.
Отдельные головки цилиндров с 4 клапанами на цилиндр обеспечивают ремонтопригодность и экономию топлива. Двигатели сертифицированы по типу конструкции во всех основных классификационных обществах.
Двигатель оснащен разработанной Scania системой управления двигателем EMS, чтобы обеспечить контроль всех аспектов, связанных с эксплуатационными характеристиками двигателя.
Система впрыска основана на инжекторах с электронным управлением, что обеспечивает низкие выбросы выхлопных газов при хорошей экономии топлива и высоком крутящем моменте уже при низких оборотах. Двигатель может быть оснащен различными принадлежностями, такими как воздухоочистители, ВОМы, трансмиссии и утвержденные типы приборов, чтобы соответствовать различным условиям монтажа.
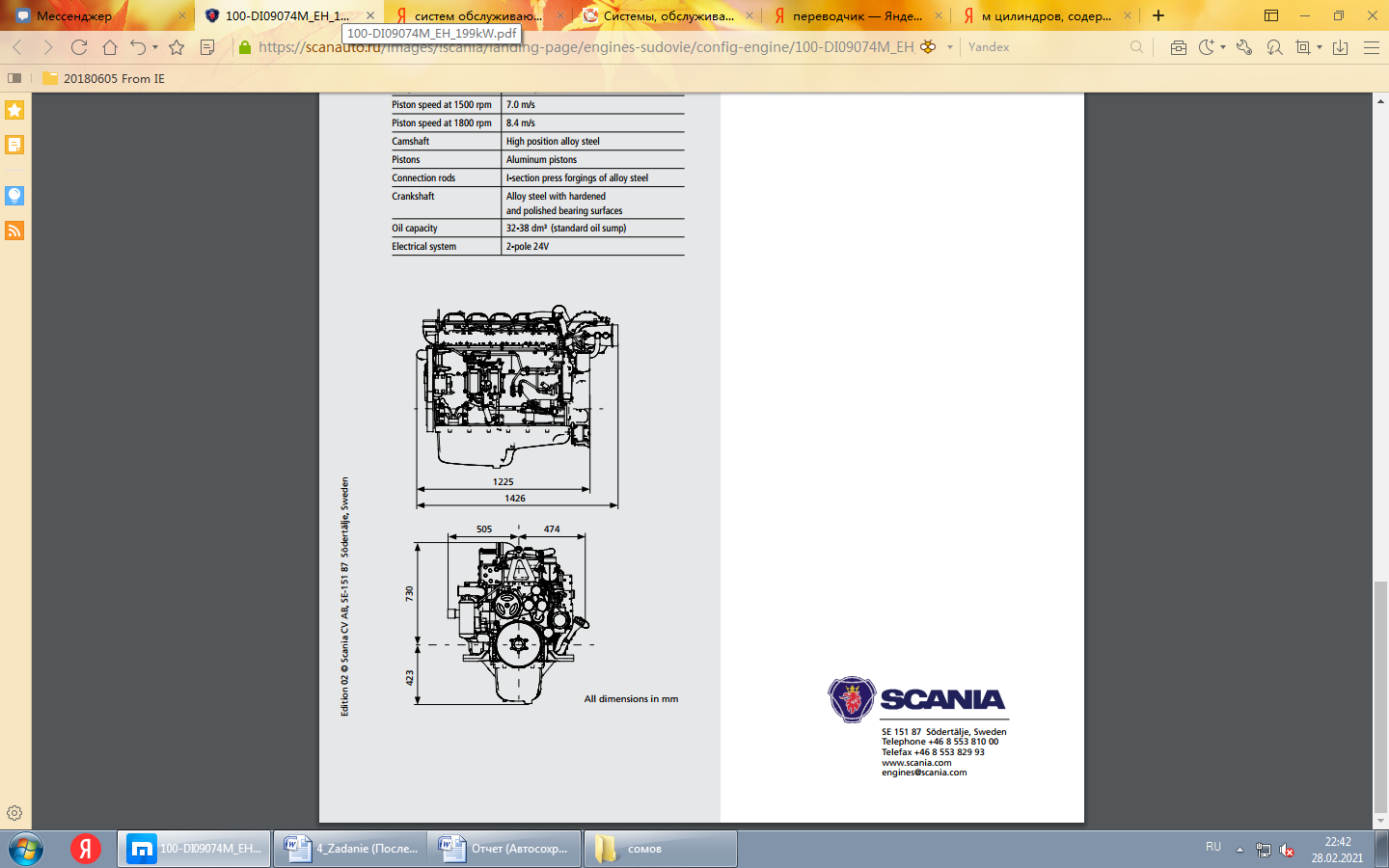
Рис. 5.2 (Поперечный и продольный разрез)
Системы, обслуживающие ВДГ
Топливная система (рис. 5.3) служит для подачи дозированных порций топлива, различных для разных режимов нагрузки. Порции топлива впрыскиваются под высоким давлением в вихревые камеры, распыливаются на мельчайшие капли. При этом обеспечивается регулярность и требуемая последовательность впрысков.
Топливоподающий насос 10 забирает топливо из расходного бака по трубопроводу 9 и под давлением по трубопроводу 8 подает его к топливному фильтру 6. Из фильтра очищенное топливо поступает по трубопроводу 7 к топливному насосу высокого давления 2, откуда по трубопроводам высокого давления 3 подается к форсункам 4 и впрыскивается в вихревые камеры, где и распыляется. Топливо, просочившееся между иглой и корпусом распылителя форсунок, по трубопроводу 5 отводится в топливный фильтр 6.
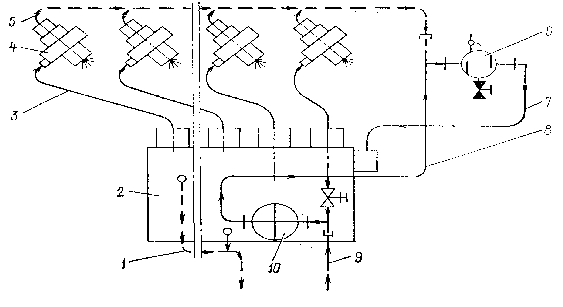
Рис. 5.3 – Схема топливной системы дизеля
1- сливная трубка; 2 - топливный насос; 3 - трубопровод высокого давления;
4 - форсунка; 5 - трубопровод слива топлива из форсунок; 6 - топливный фильтр; 7 - трубка от фильтра к топливному насосу; 8 - трубка от топливоподкачивающего насоса к фильтру; 9 - подвод топлива; 10 - топливоподкачивающий насос.
Система смазки (рис. 5.4) обеспечивает подачу масла ко всем трущимся поверхностям дизеля и очищает его от загрязнения.
Масло из поддона 12 через приемный фильтр 2 насосом 4 подается к фильтру грубой очистки 6. Часть очищенного в фильтре 6 масла проходит через фильтр тонкой очистки 11, очищается в нем и сливается в поддон. Основная часть масла поступает в центральный масляный канал, откуда по трубопроводам 10 к подшипникам коленвала и распредвала.
По сверлениям коленвала масло от рамовых (коренных) подшипников поступает к мотылёвым (шатунным) подшипникам и далее по каналам в шатунах масло поступает к подшипникам в верхние головки шатунов 9. Распределительные шестерни, кулачки распределительных валов, толкатели, втулки цилиндров, подшипники качения смазываются разбрызгиванием.
Давление в системе контролируется манометром 5, а температура масла термометром 3. Уровень масла в поддоне 12 проверяется маслощупом 14.
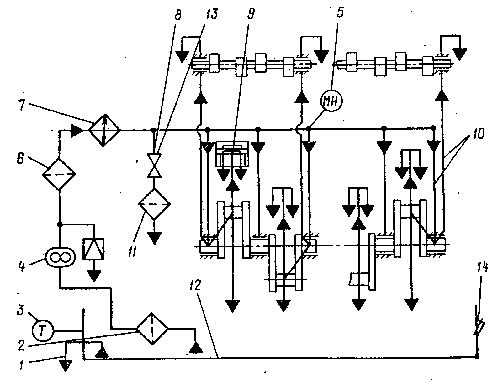
Рисунок 5.4 – Схема масляной системы дизеля
1 - слив масла из поддона; 2 - приемный фильтр; 3 - термометр; 4 - масляный насос; 5 - манометр; 6 - фильтр грубой очистки масла; 7 - холодильник (дизели 6ч); 8 - маслопровод к фильтру тонкой очистки масла; 9 - маслопровод к пальцу поршня; 10 - маслопровод к подшипникам коленчатого и распределительного валов; 11 - фильтр тонкой очистки масла; 12 - поддон; 13 - кран (кроме дизелей 4чСП8,5/11 и 10Д6); 14-маслошуп.
Система охлаждения в дизель-компрессорной установке 2-х контурная. Система охлаждения служит для отвода тепла от рабочих втулок, крышек, поршня и поддержания номинального температурного режима.
Первый контур (рис. 5.5) – система пресной воды, циркулирующей под давлением для охлаждения дизеля. Насос 8 нагнетает воду в коллекторе 5, откуда вода поступает в блок цилиндров 4 и крышки цилиндров. После их охлаждения нагретая вода нагнетается в водяную полость выхлопного коллектора 2 и далее в расширительный бачок 1, через нижний патрубок к термостату 6 и в холодильник 7, где охлаждается проточной водой подаваемой через патрубок 9. Когда температура циркулирующей воды ниже 80 °С, термостат 6 автоматически направляет весь её поток к насосу, минуя холодильник.
Для удаления воздуха и паров воды из системы охлаждения служит краник 3 на выхлопном коллекторе 2, а для слива воды - краники на блоке и холодильнике и пробка на насосе (на схеме не указаны). При минусовой температуре окружающего воздуха в систему охлаждения рекомендуется заливать низкозамерзающие жидкости (антифризы).
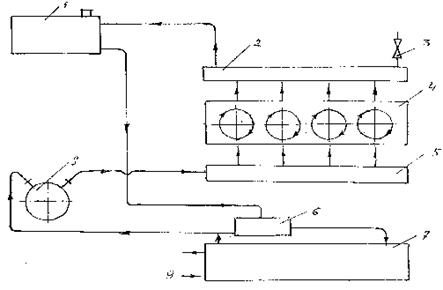
Рисунок 5.5 – Схема 1-го контура системы охлаждения дизеля (пресная вода):
1 - расширительный бачок; 2 - выхлопной коллектор; 3 - краник спуска воздуха; 4 - блок цилиндров; 5 - коллектор-распределитель; 6 - термостат; 7 - холодильник; 8 - насос; 9 - подвод проточной воды (забортной).
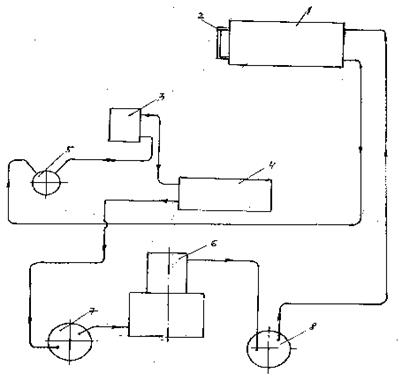
Рисунок 5.6 – Схема 2-го контура системы охлаждения дизель-компрессорной установки:
1 - бак технической воды; 2 - мерное стекло; 3 - охладитель масла дизеля; 4 - охладитель воды дизеля; 5 - насос воды 2-го контура (навешенный на дизель); 6 - воздушный компрессор
; 7 - охладитель воздуха 1-й ступени; 8 - охладитель воздуха 2-й ступени.
Второй контур (рис. 5.6) – проточная система для охлаждения дизеля и воздушного компрессора под давлением. Вихревой насос 5 забирает воду из блока технической воды 1 и под давлением нагнетает её в охладитель масла 3 дизеля, откуда вода поступает в охладитель воздуха 7 первой ступени, далее в зарубашечное пространство воздушного компрессора 6 для охлаждения ЦПГ. Из компрессора вода направляется в охладитель воздуха 2-й ступени и по трубопроводу возвращается обратно в бак 1. Таким образом, обеспечивается непрерывность подаваемой воды 2 контура в условиях лаборатории.
В судовых условиях вода для охлаждения дизель-компрессорной установки забирается из кингстона и после прохождения всех элементов установки отводится за борт.
6.Описание конструкции котельной установки и систем обслуживающих паровой котёл
Котельная установка КОАВ-68
Котлоагрегат предназначен для отопления помещений. Используется на судах и плавсредствах всех классов и назначений, а также на предприятиях хозяйственно-бытового и промышленного сектора.
Котел удобен в эксплуатации и надежен в работе. Прошел все виды испытаний, включая длительные эксплуатационные, соответствует требованиям Регистра.
-
Высокий уровень автоматизации, эксплуатация при безвахтенном обслуживании. -
Горение котлоагрегатов во всех режимах работы бездымное. -
Экономичный, малая потребляемая мощность. -
Полное агрегатирование конструкции. -
Возможно подключение элементов дистанционной сигнализации и защиты. -
Максимальная температура поверхности обшивы не превышает 318 К. -
Экологические характеристики соответствуют требованиям санитарных норм.
Теплопроизводительность, Ккал/час | 68000 | ![]() |
Рабочее давление, МПа | 0,18 | |
Расход топлива, кг/час | 7,8 | |
Температура уходящих газов, °С | 290 | |
Давление топлива перед форсункой, МПа | 0,75 | |
КПД, % | 89 | |
Напряжение переменного тока, В | постоянный | |
Потребляемая мощность, кВт | 1,2 | |
Тип топлива | дизельное, ГОСТ 305-82 | |
Тип горелки | механическая форсунка | |
Габариты, мм | 1150x680x1120 |