ВУЗ: Не указан
Категория: Не указан
Дисциплина: Не указана
Добавлен: 08.11.2023
Просмотров: 135
Скачиваний: 1
ВНИМАНИЕ! Если данный файл нарушает Ваши авторские права, то обязательно сообщите нам.
СОДЕРЖАНИЕ
Уход за искрогасителем заключается в периодической проверке крепления корпуса к крыше кузова тепловоза. Ослабшие крепления следует своевременно подтягивать. Через три-четыре месяца работы тепловоза при очередном ремонте необходимо осмотреть внутреннюю полость корпуса и очистить ее от нагарообразования. Для этого необходимо вынуть из корпуса направляющее устройство, предварительно отвернув болты 2. При проверке зазор Б должен быть не менее 3 - 4 мм по периметру между приемным патрубком корпуса искрогасителя и корпусом выпускного патрубка 6. Указанный зазор восстанавливают за счет перемещения корпуса искрогасителя на опорах 3.
Топливоподающее устройство
Топливный насос (рис. 29), предназначенный для подачи в цилиндры дизеля под высоким давлением и в соответствии с нагрузкой строго определенных доз топлива на каждый цикл, состоит из следующих основных деталей: картера, кулачкового вала, толкателей, съемных плунжерных секций и коллектора.
Техническая характеристика насоса
Тип насоса - плунжерный
Число плунжеров (секций) - 6
Диаметр плунжера, мм - 20
Ход плунжера, мм - 19,8
Порядок работы секций - 1-3-5-6-4-2
Номинальная частота хода плунжера - 375 (вдвое меньше частоты вращения вала дизеля)
Направление вращения вала насоса - по часовой стрелке (если смотреть со стороны генератора)
Картер 22 представляет собой чугунную цельнолитую коробчатую конструкцию, которая служит опорной частью всех элементов топливного насоса и объединяет их в единую взаимосвязанную систему. Поперечной перегородкой картер разделяется на два отсека, один из которых (правый) используется для установки и крепления деталей и узлов топливного насоса, другой-для установки и крепления регулятора частоты вращения вала дизеля с приводом, регулятора безопасности, механизма аварийной остановки дизеля и электропневматического сервомотора. Внутри правого отсека имеются две полости со сливными отверстиями. Верхняя полость является резервуаром для топлива, просачивающегося через неплотности плунжерных пар, а нижняя-резервуаром для масла, стекающего с трущихся поверхностей.
В горизонтальной перегородке, разделяющей обе полости, расточено шесть гнезд, предназначенных для направления движения толкателей. Для смазки трущихся поверхностей толкателей гнезда соединены маслоподво-дящими каналами с отверстием средней опоры кулачкового вала.
В картере имеются три люка: один снизу-для очистки картера, другой сбоку - для обслуживания узлов и деталей топливного насоса, расположенных в картере, а третий-с торца левого отсека для обслуживания узла привода регулятора и выемки кулачкового вала 17. Последний предназначен для периодического перемещения плунжеров секций насоса из нижнего положения в верхнее. Он выполнен из одной поковки и имеет три опорные шейки и шесть кулачков, расположенных между собой под углом 60° в порядке 1 - 3 - 5 - 6 - 4 - 2. В средней части опорных шеек расточены радиальные отверстия
, сообщающиеся со сквозным осевым каналом, подводящим смазку к опорным подшипникам кулачкового вала и приводу регулятора частоты вращения вала дизеля.
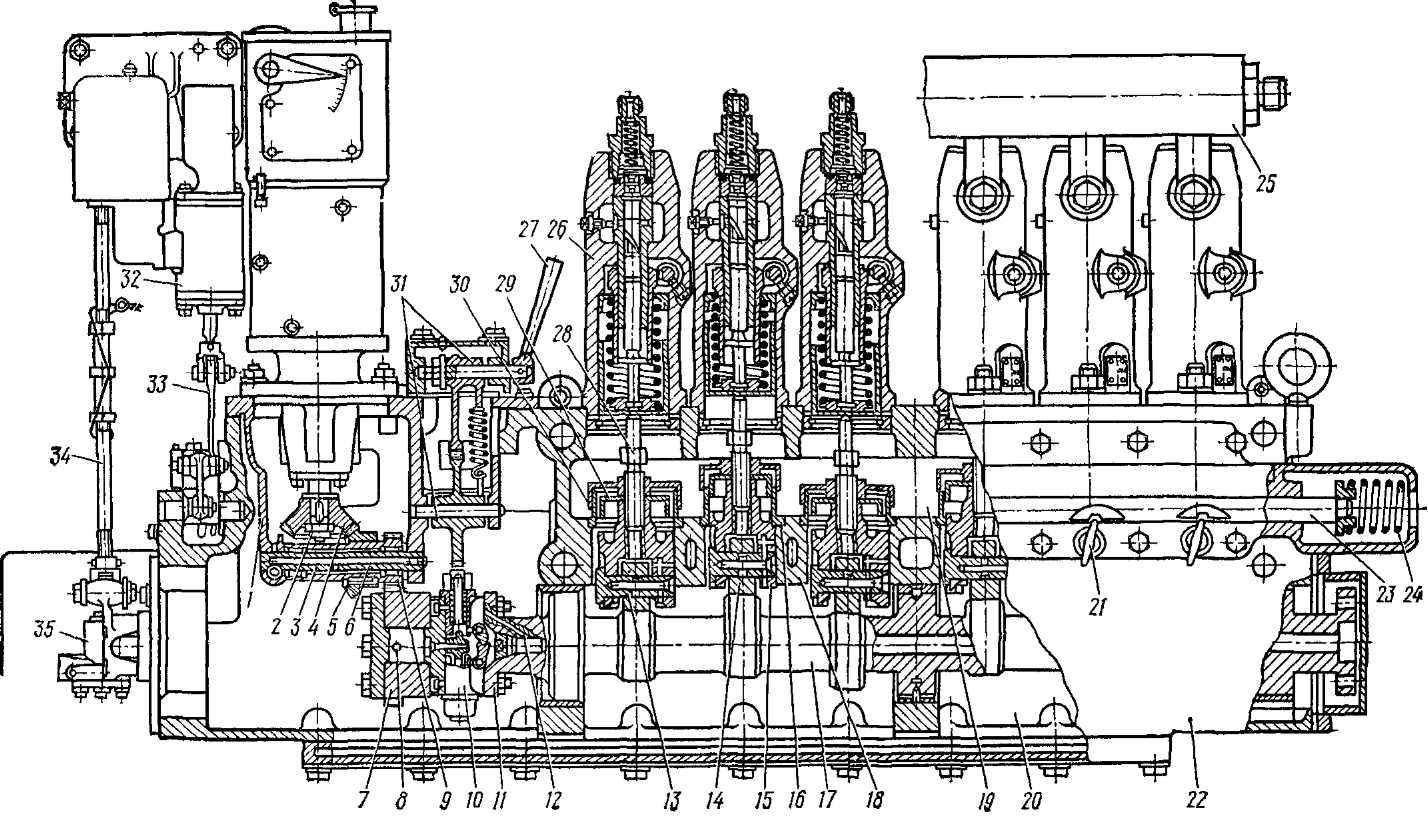
Рис. 29. Топливный насос:
1- корпус привода регулятора; 2 - вал привода регулятора; 3 - ось цилиндрической шестерни привода регулятора; 4, 5 - конические шестерни привода регулятора- в, « - каналы; 7, 9 - цилиндрические шестерни привода регулятора; « - отверстие; 10 - предельный регулятор; 11-фланец кулачкового вала- 13 - палец толкателя-- ролнк толкателя; 15 - корпус толкателя; 16 - цилиндр; 17 - кулачковый вал; 18 - горизонтальная перегородка картера; 19 - верхняя полость; 20 - нижняя полость; 21 - стопор секции насоса; 22 - картер топливного насоса; 23 - тяга выключения секций насоса; 24 - пружина; 26 - коллектор топливного насоса- 26 - секция топливного насоса; 27 - рукоятка механизма аварийной остановки дизеля; 28 - регулировочный болт; 29 - манжета; 30 - направляющий стакан- 31 - механизм аварийной остановки дизеля; 32 - регулятор частоты вращения вала дизеля; 33 - рычажный механизм управлення топливоподачей; 34 - рычажный механизм Затяжки всережимной пружины; 3$ - электропневматический сервомотор и " 4
С обоих концов кулачковый вал имеет фланцы. Левый фланец служит для связи с приводом регулятора дизеля, правый - для связи с приводным валом топливного насоса. Толкатель является промежуточным звеном, связывающим кулачковый вал с плунжером секции топливного насоса. Корпус 15 толкателя стальной цементированный. В нижней его части на полом пальце 13, установленном в сквозном поперечном отверстии, имеется ролик 14. Прямоугольная головка пальца входит в вертикальные пазы корпуса толкателя и отверстия картера, предохраняя толкатель от проворачивания. С правой стороны в корпусе выполнены горизонтальное и вертикальное сверления, которые совместно с двумя радиальными сверлениями в правой и средней частях пальца служат для подвода смазки к ролику.
На наружной поверхности корпуса имеется горизонтальная смазочная канавка и коническое отверстие для стопора, а в донной его части-шесть сквозных отверстий для прохода масла и воздуха при движении толкателя. Сверху в хвостовик корпуса ввернут болт 28, служащий для регулировки моментов начала подачи топлива плунжерами. Он снабжен шестигранником под ключ и цилиндрической головкой с шаровой поверхностью, на которую опирается стакан пружины плунжера. Положение болта фиксируется стаканом 30. Стакан 30 и манжета 29 толкателя совместно с цилиндром 16, ввернутым в горизонтальную перегородку картера, образуют лабиринтное уплотнение, предотвращающее попадание топлибэ из верхней полости в нижнюю - масляную полость картера.
Основными деталями секции топливного насоса (рис. 30, а) являются две прецизионные пары, выполненные с высокой точностью и смонтированные вместе с другими ее деталями в корпусе 22, отлитом из чугуна. Первая пара - насосный элемент состоит из гильзы 10 и плунжера /7, а вторая-клапанная пара - из нагнетательного клапана 5 и седла 6, Обе пары изготовлены из высоколегированной термически обработанной стали. Уплотнение в каждой паре достигается путем тщательной притирки одной детали к другой. Поэтому в случае повреждения одной из деталей пара заменяется новой.
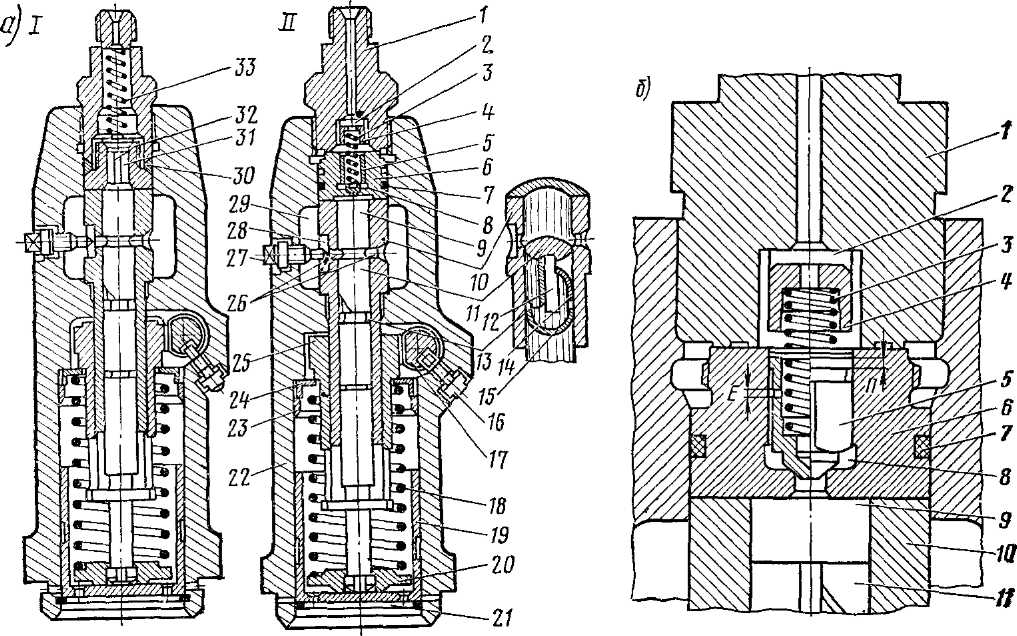
Рис 30 Секция топливного насоса (а) и ее нагнетательный клапан (б): 1- нажимной штуцер, 2, 8 - полости, сообщающиеся с нагнетательным трубопроводом, 3 - пружина нагнетательного клапана, 4- упор; 5- нагнетательный клапан, 6 - седло нагнетательного клапана, 7 - резиновое уплотнителььое кольцо, 9 - надплунжерное пространство, 10 - гильза, 11- плунжер; 12 - вертикальный паз, 13 - кольцевая выточка; 14 - верхняя кромка, 15 - нижняя кромка, 16, 27 - стопорные вннты, 17 - регулирующая рейка, 18 - пружина плунжера, 19 - направляющий стакан, 20 - тарелка пружины нижняя, 21 - стопорное кольцо; 22 - корпус секции, 23 - пружинное кольцо, 24 - тарелка пружины верхняя, 35 - шестерня; 26 - отверстие, 28 - паз, 29 - всасывающая полость корпуса, 30-уплотннтельное медное кольцо; 31 - нагнетательный клапан; 32 - седло нагнетательного клапана, 33 - пружина нагнетательного клапана (1- до модернизации! 11- после модернизации)
Гильза 10 плунжера насосной пары выполнена в виде цилиндра с утолщенной верхней частью. Два сквозных отверстия 26 в верхней части соединяют надплунжерное пространство 9 гильзы с полостью 29 корпуса, к которой подводится топливо. Одно из этих отверстий на наружной поверхности гильзы имеет коническую зенковку, а другое - снабжено вертикальной канавкой, в которую входит стопорный винт 27, удерживающий гильзу от проворачивания. При этом отверстие для прохода топлива остается открытым. Нижним буртом гильза плотно притерта к кольцевой выточке корпуса.
Плунжер 11 состоит из цилиндрической головки и фасонного хвостовика, выполненных как одно целое. На поверхности головки в верхней части имеется кольцевая выточка 13, соединенная вертикальным пазом 12 с надплунжерным пространством 9. Нижняя кромка 15 выточки выполнена круглой, а верхняя -14 - фигурной по винтовой линии. На некотором расстоянии от торца головки плунжера она пересекается с кромкой вертикального паза 12. Винтовая кромка служит для отсечки и регулирования количества топлива, подаваемого плунжером. На хвостовике плунжера имеются два выступа и головка. Выступы входят в вертикальные пазы хвостовика шестерни 25, находящейся в зацеплении с регулирующей зубчатой рейкой 17, а головка опирается на донышко направляющего стакана 19, подпираемого снизу сферической поверхностью регулировочного болта 28 толкателя (см. рис. 29). На головку надета тарелка 20 (см. рис. 30, а) пружины 18, возвращающей плунжер в нижнее положение.
Клапанная пара установлена на верхний торец гильзы плунжера. Для обеспечения плотности седло клапанной пары притерто к торцу гильзы и прижато к ней нажимным штуцером 1. Плотность с корпусом секции обеспечивается резиновым кольцом 7. В центре седла 6 имеется отверстие, служащее гнездом для нагнетательного клапана 5.
Клапан 5 (рис. 30, б) выполнен полым. В нижней части он имеет игольчатый посадочный конус, в средней-боковое отверстие Е, а в верхней- кольцевой буртик П.
Буртик П разобщает нагнетательный трубопровод от надплунжерного пространства раньше, чем это выполнит игольчатый конус, а отверстие Е перепускает топливо из нагнетательного трубопровода в надплунжерное пространство 9 после разобщения их буртиком П.
Клапан прижимается к посадочному конусу седла пружиной 3, которая другим своим концом упирается в упор 4, служащий для ограничения подъема нагнетательного клапана.
Работа топливного насоса. Топливо подается плунжерами, которые движутся вверх под действием кулачков, а вниз - под действием пружин. При ходе плунжера вниз надплунжерное пространство 9 (см. рис. 30, а) через два сквозных отверстия 26 в верхней части гильзы 10 плунжера заполняется топливом. При ходе плунжера вверх топливо частично вытесняется плунжером через всасывающие отверстия в гильзе обратно в топливный коллектор дизеля. После перекрытия всасывающих отверстий верхним торцом плунжера давление над плунжером возрастает. Когда давление топлива, создаваемое плунжером, превысит силу сопротивления пружины нагнетательного клапана, последний откроется и топливо пройдет в нагнетательный трубопровод. При достижении в нем давления, необходимого для поднятия иглы форсунки, топливо поступит в цилиндр дизеля.
При дальнейшем подъеме плунжер своей винтовой кромкой 14 открывает одно из отверстий 26 в стенке гильзы, вследствие чего топливо из надплунжерного пространства 9 через паз 12 плунжера и отверстия гильзьт устремляется в топливный коллектор дизеля. Давление топлива над плунжером при этом резко падает. Нагнетательный клапан 5 (см. рис 30, б) под воздействием пружины 3 и давления топлива в нагнетательном трубопроводе, быстро опускаясь, входит своим буртиком П в седло 6, разобщая тем самым нагнетательный трубопровод с полостью 8 (полость под буртиком Я). Впрыск топлива прекращается. К этому моменту плунжер достигает мертвой точки и начинает двигаться вниз, отсасывая топливо из нагнетательного трубопровода через отверстие Е клапана в надплунжерное пространство вплоть до момента посадки игольчатого конуса, причем количество отсасываемого топлива тем больше, чем выше давление в нагнетательном трубопроводе (форсуночной трубке).