ВУЗ: Не указан
Категория: Не указан
Дисциплина: Не указана
Добавлен: 08.11.2023
Просмотров: 51
Скачиваний: 1
ВНИМАНИЕ! Если данный файл нарушает Ваши авторские права, то обязательно сообщите нам.
С О Д Е Р Ж А Н И Е
№п.п. | Наименование раздела | № листа |
| Введение | 3 |
| Классификация металлорежущих станков | 3 |
| Описание основных групп и типов станков | 3 |
| Применяемый режущий инструмент | 5 |
| Особенности работы, конструкция и применяемая оснастка токарно-винторезного станка. | 18 |
| Заключение | 22 |
| Литература | 22 |
Введение
Металлорежущий станок – станок, предназначенный для размерной обработки металлических заготовок путем снятия материала.
История металлорежущих станков
Считается, что история металлорежущих станков начинается с изобретения суппорта токарного станка. Около 1751 г. французский инженер и изобретатель Жак Де Вокансон первый применил специальное устройство для фиксации резца – устранив, таким образом, непосредственное влияние руки человека на формообразование поверхности.
Классификация металлорежущих станков
Станки классифицируются по множеству признаков:
По классу точности металлорежущие станки классифицируются на пять классов:
-
(Н) Нормальной точности -
(П) Повышенной точности -
(В) Высокой точности -
(А) Особо высокой точности -
(С) Особо точные станки (мастер-станки)
Классификация металлорежущих станков по массе:
-
лёгкие (< 1 т) -
средние (1-10 т) -
тяжёлые (>10 т) -
уникальные (>100 т)
Классификация металлорежущих станков по степени автоматизации:
-
ручные -
полуавтоматы -
автоматы -
станки с ЧПУ -
гибкие производственные системы
Классификация металлорежущих станков по степени специализации:
-
Универсальные. Для изготовления широкой номенклатуры деталей малыми партиями. Используются в единичном и серийном производстве. Также используют при ремонтных работах. -
Специализированные. Для изготовления больших партий деталей одного типа. Используются в среднем и крупносерийном производстве -
Специальные. Для изготовления одной детали или детали одного типоразмера. Используются в крупносерийном и массовом производстве
Описание основных групп и типов станков
По виду обработки в СССР была принята классификация станков, которая продолжает действовать и в настоящее время в России. В соответствии с ней металлорежущие станки разделяются на следующие группы и типы:
Станки | Группа | Типы станков | ||||||||
1 | 2 | 3 | 4 | 5 | 6 | 7 | 8 | 9 | ||
Токар-ные | 1 | Автоматы и полуавтоматы | Револь-верные | Сверли-льно-отрезные | Кару-сельные | Токар-ные и лобото-карные | Много-резцовые | Специа-лизированные для фасон-ных изделий | Разные токарные | |
Одно-шпин-дельные | Много-шпиндельные | |||||||||
Свер-лильные и расточ-ные | 2 | Верти-кально-сверлильные | Одно-шпиндельные полуав-томаты | Много-шпиндельные полу-автоматы | Координатно-расточ-ные односто-ечные | Радиа-льно-сверли-льные | Горизонтально-расточ-ные | Алмазно-расточные | Горизон-тально-сверлиль-ные | Разные сверлильные |
Шлифо-вальные, полиро-вальные, доводоч-ные | 3 | Кругло-шлифо-вальные | Внутри-шлифо-вальные | Обдироч-ношлифо-вальные | Специа-лизиро-ванные шлифо-вальные | - | Заточ-ные | Плоско-шлифова-льные с прямоуго-льным или круглым столом | Прити-рочные и полиро-вальные | Разные станки, работаю-щие аб-разивным инстру-ментом |
Комбинированные | 4 | Универ-сальные | Полуав-томаты | Автоматы | Электро-хими-ческие | Элект-роиск-ровые | - | Электро-эрозион-ные, ульт-развуко-вые | Анодно-механические | - |
Зубо- резьбо-обрабатывающие | 5 | Зубостр-огальные для цилинд-рических колёс | Зуборезные для кониче-ских колёс | Зубофре-зерные для цилиндри-ческих ко-лёс и шли-цевых валиков | Зубофре-зерные для червяч-ных колёс | Для обрабо-тки торцов зубьев колёс | Резьбо-фрезер-ные | Зубоотде-лочные | Зубо- и резбо- шлифовальные | Разные зубо- и резьбо- обрабат-ывающие |
Фрезер-ные | 6 | Вертика-льно-фрезер-ные | Фрезер-ные непре-рывного дейст-вия | - | Копиро-вальные и гравиро-вальные | Верти-кальные бескон-сольные | Продо-льные | Широко-универ-сальные | Горизон-тальные консоль-ные | Разные фрезер-ные |
Строга-льные, долбеж-ные, про-тяжные | 7 | Продольные | Попереч-ностро-гальные | Долбёж-ные | Протя-жные горизонтальные | - | Протяж-ные вертика-льные | - | Разные строгаль-ные | |
Односто-ечные | Двухс-тоечные | |||||||||
Разрез-ные | 8 | Отрезные, работающие: | Правиль-но-отрезные | Пилы | - | - | ||||
токарным резцом | Абразив-ным кругом | Фрикцио-нным блоком | Ленточ-ные | Диско-вые | Ножовоч-ные | |||||
Разные | 9 | Муфто- и трубо- обрабат-ывающие | Пилона-секате-льные | Правиль-но- и бес-центрово- обдироч-ные | - | Для испыта-ния ин-струме-нта | Делите-льные машины | Балансировочные | - | - |
Формообразующие движения
Для осуществления процесса резания на металлорежущих станках необходимо обеспечить взаимосвязь формообразующих движений.
У металлорежущего станка имеется привод (механический, гидравлический, пневматический), с помощью которого обеспечивается передача движения рабочим органам: шпинделю, суппорту и т. п. Комплекс этих движений называется формообразующими движениями. Их классифицируют на два вида:
1) Основные движения (рабочие), которые предназначены непосредственно для осуществления процесса резания:
а) Главное движение Dг – осуществляется с максимальной скоростью. Может передаваться как заготовке (например в токарных станках) так и инструменту (напр. в сверлильных, шлифовальных, фрезерных станках). Характер движения: вращательный или поступательный. Характеризуется скоростью — v (м/с).
б) Движение подачи Ds – осуществляется с меньшей скоростью и так же может передаваться и заготовке и инструменту. Характер движения: вращательный, круговой, поступательный, прерывистый. Виды подач:
-
подача на ход, на двойной ход Sх. (мм/ход), Sдв.х. (мм/дв.ход); -
подача на зуб Sz (мм/зуб); -
подача на оборот So (мм/оборот); -
частотная (минутная) подача Sm (об/мин).
2) Вспомогательные движения – способствуют осуществлению процесса резания, но не участвуют в нём непосредственно. Виды вспомогательных движений:
-
наладка станка; -
задача режимов резания; -
установка ограничителей хода в соответствии с размерами и конфигурациями заготовок; -
управление станком в процессе работы; -
установка заготовки, снятие готовой детали; -
установка и смена инструмента и прочие.
Применяемый режущий инструмент
Режущий инструмент – инструмент, предназначенный для изменения формы и размеров обрабатываемой заготовки путём удаления части материала в виде стружки или шлама с целью получения готовой детали или полуфабриката.
Подразделяется:
-
по типу применения – на ручной и машинный (станочный), строительный, монтажный, и т. д. -
по типу обрабатываемого материала – металлорежущий, дереворежущий, и т. д., -
по типу применяемого материала – быстрорежущий, для высокоскоростной обработки, и т. д., -
по типу обрабатываемой детали – зуборезный, резьбообразующий, и т. д., -
по характеру обработки – абразивный, шлифовальный, и т. д., -
по чистоте обработанной поверхности – черновая обработка, получерновая обработка, чистовая обработка, получистовая обработка, суперчистовая обработка.
На станках применяется следующий инструмент:
Резец
Резец – ( англ. cutting tool ) – режущий инструмент с одним прямым, изогнутым или фасонным главным режущим ребром.
Р
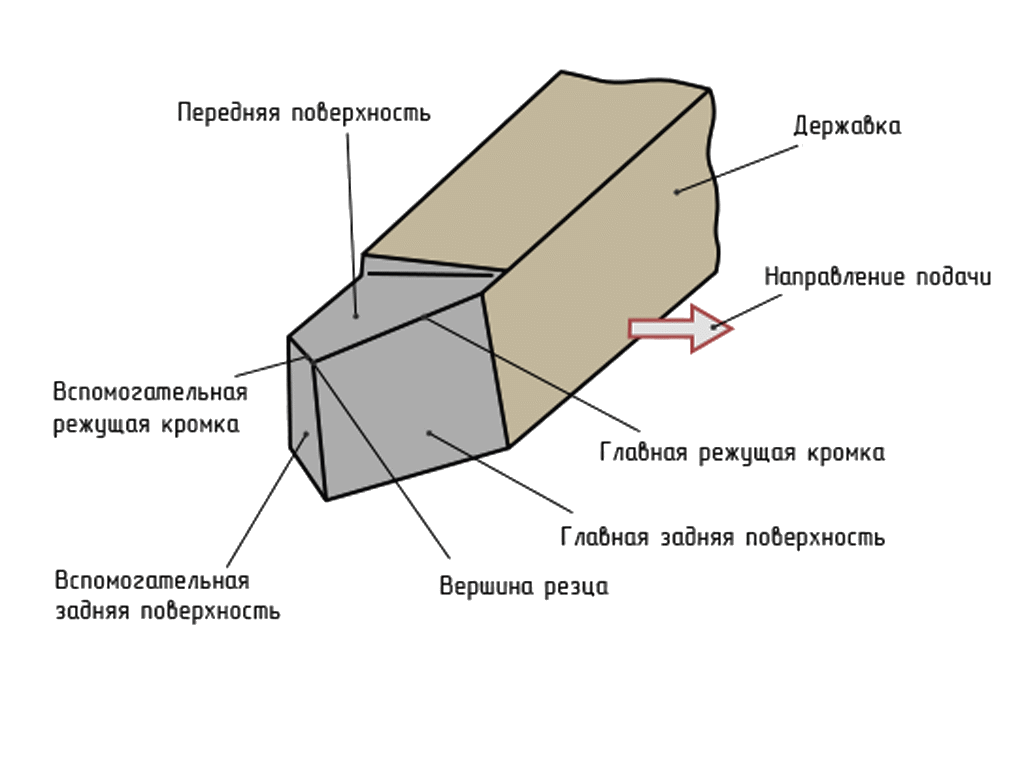
Резцы применяются для токарных, строгальных и долбёжных работ для полу-чения простых поверхностей и в ряде специальных случаев.
Относительно обрабатываемой детали резцы могут быть двух типов: радиальные и тангенциальные.
Первый из них работает с установкой перпендикулярно оси обрабатываемой детали, второй – касательно. При работе радиального резца усилие Рг создает соответствующий изгибающий момент, а в тангенциальном резце усилие Рг направлено вдоль оси резца, благодаря чему тело резца не подвергается изгибу.
Если первый тип резца имеет широкое применение в промышленности за счет простоты своего крепления и более удобного выбора геометрических параметров режущей части, то второй применяется главным образом на токарных автоматах и полуавтоматах, где основой является чистота обработки.
Резцы разделяются на правые и левые.
Правым называется резец, у которого при наложении на него сверху ладони правой руки так, чтобы пальцы были направлены к его вершине, главная режущая кромка будет находиться под большим пальцем. На токарных станках эти резцы работают при подаче справа налево, то есть к передней бабке станка.
Левым называется резец, у которого при наложении на него левой руки указанным выше способом главная режущая кромка окажется под большим пальцем.
По форме головки и ее положению относительно стержня резцы разделяются на прямые, отогнутые, изогнутые и с оттянутой головкой.
Прямыми резцами называются такие, у которых ось в плане и боковом виде прямая.
Отогнутыми называются резцы, у которых ось резца в плане изогнута.
Изогнутыми резцами называют такие, у которых ось в боковом виде загнута назад (вниз) или вперед (вверх).
По применяемости на станках, виду и характеру обработки резцы разделяются на:
-
токарные -
строгальные -
долбежные
Токарные резцы:
-
проходные, производящие обтачивание детали вдоль оси ее вращения или в плоскости, перпендикулярной к этой оси (лобовые) -
подрезные — для подрезания уступов под прямым и острым углом к основному направлению обтачивания -
отрезные — для отрезки материала под прямым углом к оси вращения и для прорезания узких канавок -
расточные — для растачивания отверстий в направлении оси вращения -
фасочные — для снятия фасок -
фасонные — для получения сложной фасонной формы обтачиваемой детали
Основные типы токарных резцов в настоящее время стандартизованы.
Кроме стандартных резцов, имеется ряд типов резцов, предложенных в разное время и используемых в тех или иных случаях.
Для тяжелых обдирочных работ находят применение чашечные резцы. Так как затупление чашечного резца при каждой его установке происходит на небольшом участке его режущей кромки, то, поворачивая резец вокруг оси, можно значительно увеличить его стойкость до переточки. Такой резец состоит из державки, собственно чашечного поворотного резца («грибка») и эксцентрикового прижимного кольца. Чашечный резец крепят в державке на пальце. Существуют и другие конструкции крепления этих резцов.
Строгальные и долбежные резцы
-
проходные — для строгания верхней поверхности обрабатываемой детали; -
боковые — подрезные для строгания детали с боков; -
отрезные и прорезные — для разрезания детали и прорезания канавок.
Резец, снимающий стружку при прямолинейном взаимном перемещении резца и материала, называется строгальным (при горизонтальном резании) или долбежным (при вертикальном).
Характер работы строгального и долбежного резцов одинаков и отличается от работы токарных резцов, где резание непрерывно. Как при строгании, так и при долблении резец режет только при рабочем ходе. В то же время в моменты начала и конца каждого хода возникают толчки, вредно влияющие на работу этих резцов.
В указанных ГОСТах приведены типы и размеры резцов: проходных, подрезных и керамические резцы
Керамические резцы
Применение керамических резцов является дальнейшим шагом в развитии инструмента для скоростного резания металлов по сравнению с использованием твердосплавных резцов. Высокая красностойкость таких резцов позволяет обеспечить более высокие скорости резания в сравнении с твердосплавными резцами, однако повышенная хрупкость керамики ограничивает их применение; в настоящее время они большей частью применяются при чистовом и получистовом обтачивании