Файл: Курсовой проект По мдк. 01. 01 Техническое обслуживание и ремонт автомобильного транспорта.docx
ВУЗ: Не указан
Категория: Не указан
Дисциплина: Не указана
Добавлен: 09.11.2023
Просмотров: 157
Скачиваний: 5
ВНИМАНИЕ! Если данный файл нарушает Ваши авторские права, то обязательно сообщите нам.
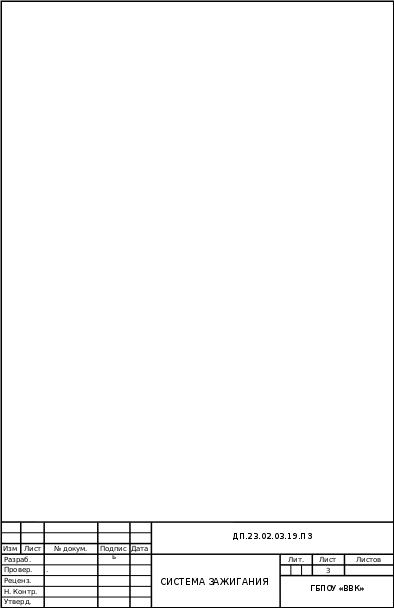
ГБПОУ «Вышневолоцкий колледж»
Курсовой проект
По МДК.01.01 «Техническое обслуживание и ремонт автомобильного транспорта»
На тему: «Восстановление поворотного кулака автомобиля КАМАЗ »
Выполнил студент 3 курса, А-33
Богаев Сергей
Проверил преподаватель: Бойков Ю.А
Вышний Волочек
2023г.
СОДЕРЖАНИЕ
Введение
Глава 1. Описание конструкции и работы поворотного кулака
1.1 Конструкция и технические характеристики поворотного кулака
1.2 Описание работы поворотного кулака
1.3 Анализ неисправностей возникающих в процессе эксплуатации
Глава 2. Разработка технологического процесса ремонта поворотного кулака
2.1 Дефектация деталей
2.2 Анализ вариантов ремонта деталей поворотного кулака
2.3 Описание варианта изготовления новой детали
2.4. Основные методы восстановления деталей
2.5. Обоснование выбора рационального способа восстановления или изготовления детали
2.6. Подбор технологического оборудования
Глава 3. Разработка технологического процесса ремонта поворотного кулака
3.1. Разработка маршрутного технологического процесса ремонта поворотного кулака
3.2. Техническое нормирование
3.3. Расчет режимов механической обработки
3.4. Разработка операционного технологического процесса ремонта детали
поворотного кулака
3.5. Описание метода и оборудования для технологического контроля
Заключение
Список использованных источников
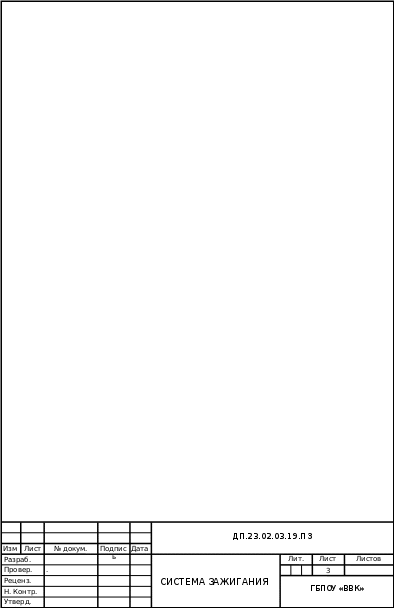
Введение
Постоянная необеспеченность ремонтного производства запасными частями является серьезным фактором снижения технической готовности автомобильного парка. Расширение их производства, новых запасных частей связано с увеличением материальных и трудовых затрат. Вместе с тем около 75% деталей, выброшенных при первом капитальном ремонте автомобилей, являются ремонтно-пригодными, либо могут быть использованы вообще без восстановления. Поэтому целесообразной альтернативой расширению производства запасных частей являются вторичное использование изношенных деталей, восстанавливаемых в процессе ремонта автомобиля и его агрегатов.
Из ремонтной практики известно, что большинство выбракованных на износ деталей теряют не более 1-2% исходной массы, при этом прочность деталей практически сохраняется.
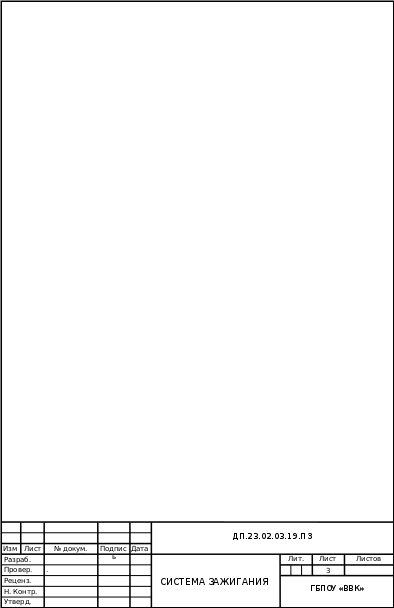
Глава 1. Описание конструкции и работы поворотного кулака
1.1 Конструкция и технические характеристики поворотного кулака
Главное предназначение поворотного кулака - принимать на себя и выдерживать усилия от ударов колес о неровности дороги и создание угла поворота для колес, при помощи которых осуществляется управление автомобилем. Изготавливается кулак из высокопрочной легированной стали 30Х или 40Х с соблюдением очень высокой точности геометрических размеров для установки сопрягаемых деталей.
1.2 Описание работы поворотного кулака
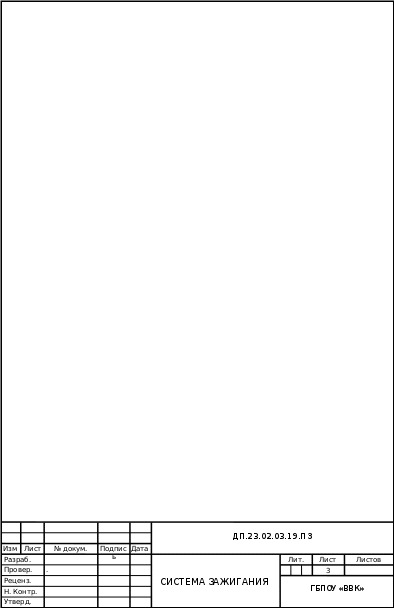
Высокие скорости оказывают огромное давление на сборку рулевого управления и шасси. Поворотный кулак помогает водителю сохранить контроль над автомобилем.
1.3 Анализ неисправностей возникающих в процессе эксплуатации
– геометрические изменения, которые можно достаточно просто измерить штангенциркулем, резьбовым микрометром или компаратором;
– структурные изменения, которые можно обнаружить, осматривая поверхность детали. Это исследование можно проверить невооруженным глазом, только если есть изменения цвета. Иногда необходимо проводить исследование с помощью микрометра;
– износ, или, скорее, различные виды износа, так как причины и следствия многочисленны;
– трещины, которые могут привести к разрушению.
Глава 2. Разработка технологического процесса ремонта
поворотного кулака
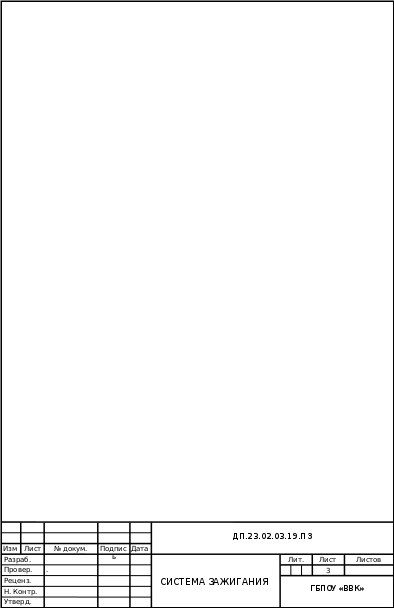
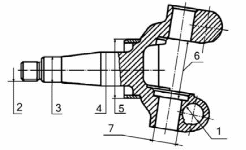
2.1 Дефектация деталей
Карта дефекации поворотного кулака | |||||||||
№ по каталогу | Наименование | Материал | Твердость | ||||||
53-3001012-А/13-А | Кулак повортный | Сталь 35Х С=0,31-0,36% | НВ 269-321 | ||||||
№ дефекта | Возможные Дефекты | | Размер, мм | | |||||
Номинальный | Предельно допустимый | Способ Ремонта | |||||||
1 | Обломы или трещины | Осмотр. Дефектоскоп | | | Браковать | ||||
2 | Износ проушины под балку передней оси | Калибр 99,25 мм штангенциркуль ШЦ 1-125-01 ГОСТ 166-89 | 97+0,2 | 99,25 | Ремонтировать. Обработка торцов и постановка регулировочных шайб при сборке. Браковать при размере более 99,25мм. | ||||
3 | Износ отверстий под поворотные рычаги | Конусный калибр. Большой диаметр конуса 30,05 мм. Конусность 12,5% | Большой диаметр ![]() | Смещение калибра относительно большего торца конуса не более 1,5мм | Смещение калибра относительно большего торца конуса не более 1,5мм | ||||
4 | Износ канавки | Осмотр. Штангенциркуль ГОСТ 166-89 | 5-0,1+0,25 | 5,25 | Ремонтировать. Фрезеровать | ||||
![]() | | | | | | ||||
6 | Износ шейки под наружный подшипник ступицы | Скоба 29,95 мм, микрометр 25-50 мм ГОСТ 18360-93 | ![]() ![]() | 29,95 | Ремонтировать. Хромирование, осталивание, наплавка |
2.2 Анализ вариантов ремонта деталей поворотного кулака
Трещины или обломы проушин - при данном дефекте дальнейшая эксплуатация и восстановление невозможно, поэтому деталь бракуется.
Срыв резьбы под гайку цапфы - для восстановления детали при данном дефекте рассмотрим два способа: автоматическая вибродуговая наплавка в среде углекислого газа (С 02), автоматическая вибродуговая наплавка.
Износ посадочных поверхностей под внутренний и наружный подшипники - для восстановления детали при данном дефекте рассмотрим два способа: железнение и хромирование.
Износ конусного отверстия под рычаг рулевой трапеции - разворачиваем до ремонтного размера.
Износ шпоночного паза по ширине - для восстановления детали при данном дефекте рассмотрим два способа: наплавка, фрезеруем шпоночный паз до ремонтного размера. Наиболее экономично фрезеровать шпоночный паз до ремонтного размер, используется меньше оборудования.
Износ отверстий под втулки шкворня - разворачиваем до ремонтного размера.
Износ проушины под головку оси - дополнительные ремонтные детали
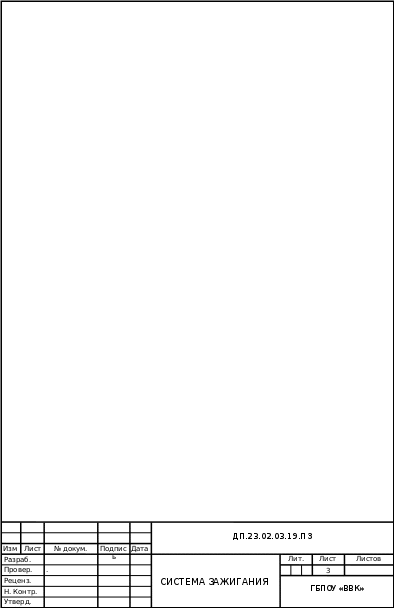
Заготовки кулаков получают штамповкой (способом выдавливания) на кривошипных горячештамповочных прессах , материалом служит сталь 45Х. Последовательность получения поковок такая: отрезка штучной заготовки; нагрев до температуры ковки; штамповка в три перехода(осадка, предварительная штамповка с выдавливание хвостовика вниз и двух головок наклонно вверх, окончательная штамповка ) ; обрезка заусенцев в горячем состояние ; горячая правка на кривошипном чеканном прессе; подрезания
концов хвостовика в холодном состояние заготовки. Затем заготовка проходит термическую обработку.
Заготовки поворотных кулаков обрабатывают на автоматических линиях. Специфическим требованием к обработке резанием, обусловленным конструктивной особенностью кулаков, является обеспечения точного угла наклона оси хвостовика к оси отверстий под шкворень.
2.4. Основные методы восстановления деталей
- осталивание
-хромирование
-Вибродуговая наплавка
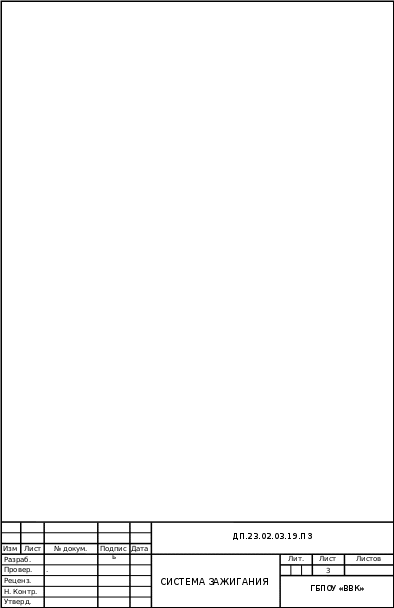
2.5. Обоснование выбора рационального способа восстановления или изг При разработке технологического процесса восстановления детали придерживаются следующих правил: сначала устраняют трещины, отколы, обломы, затем восстанавливают базовые технологические поверхности, наращивают изношенные поверхности, обрабатывают рабочие поверхности под ремонтный или номинальный размер. При восстановлении деталей определенного наименования необходимо выбрать способ устранения каждого из имеющихся на ней дефектов, а затем, уже, руководствуясь приведённой последовательностью устранения дефектов, проектировать технологический процесс ремонта детали. Для устранения дефекта №1 существуют следующие способы устранения: хромирование, осталивание, накатка. Наиболее рациональный способ: осталивание. Этот метод наиболее выгоден для больших партий деталей. Для устранения дефекта №2 существуют следующие способы устранения: осталивание, хромирование. Наиболее рациональный способ: осталивание. Этот способ наиболее выгоден для больших партий деталей. Для устранения дефекта №3 существуют следующие способы устранения: вибродуговая наплавка. Наиболее
рациональный способ: вибродуговая наплавка. Этот способ экономически выгоден.
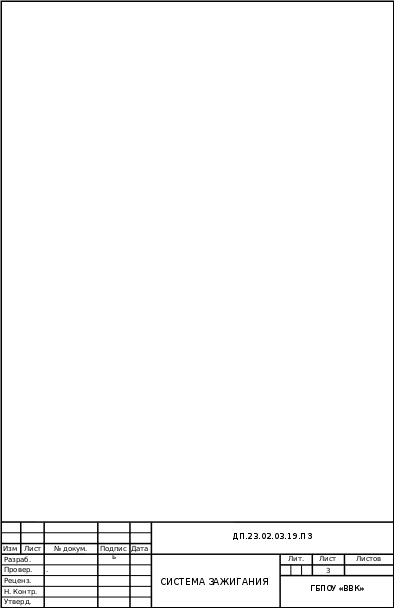
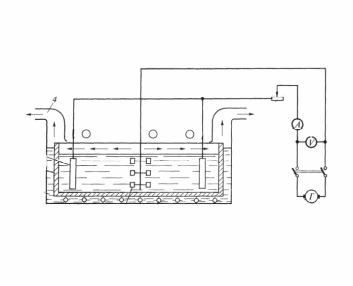
Ванна для хромирования -это емкость для нанесения на металлические поверхности хрома методом гальванического осаждения хрома из электролитического раствора под действием электрического тока прямой и обратной полярности. Ванна хромирования изготовление по размерам и техническому заданию – это комбинация несущего каркаса и фторопластового вкладыша.
Глава 3. Разработка технологического процесса ремонта поворотного кулака
3.1. Разработка маршрутного технологического процесса ремонта поворотного кулака
Цель технологического маршрута - дать общий план обработки заготовки при изготовлении детали, наметить содержание и последовательность технологического процесса.
Карта маршрутная | Группа | | |||||||||||
![]() | | | | ||||||||||
Кулак поворотный | 53-3001012-А/13-А | Сталь 35Х ГОСТ 4543-71 | | ||||||||||
№ | Наименование операции | Оборудование | Приспособление | Примечание | | ||||||||
1 | 2 | 3 | 4 | 5 | | ||||||||
005 | Мойка | Моечная машина ОМ-5360 | Моющий раствор Лабомид 201 | Мыть все поверхности | | ||||||||
010 | Точение предварительное c Ø24 в Ø22, на L= 30 мм, деф.№4. c Ø30 в ![]() L= 32 мм, деф.№5 | Токарно-винторезный станок 16К20 | Резец проходной ГОСТ 2719-83 | Сточить резьбу. Обработать до выведения следов износа. Обработать поверхность для запрессовки втулок | | ||||||||
| 015 | Рассверливание (2 отв.) c Ø33 в ![]() на L=43 мм,деф.№2 | Вертикально-сверлильный станок 2Н118 | Сверло спиральное ГОСТ 10902-77 | Обеспечить точность центрирования сверла | ||||||||
| 020 | Фрезерование (2 торца) расстояние между торцами L=97+0,2мм, деф.№1 | Вертикально-фрезерный станок 6012Ц | Фреза торцевая ГОСТ 26595-85 | Фрезеровать до устранения дефекта и в необходимую шероховатость | ||||||||
| 025 | Наплавка вибродуговая с Ø 22 до Ø28 мм, на L = 30 мм, деф.№4 с Ø 29 до мм на L = 32 мм, деф.№5 | Установка для вибродуговой наплавки в среде жидкости УД-209 | Проволока Нп-80 | Обеспечить равномерный слой наплавки без пор, раковин, инородных включений. Не допускается непроплавление рабочих поверхностей. | ||||||||
| | | | | ![]() | ||||||||
| 035 | Точение черновое с Ø 28 в Ø24,1 мм, на L = 30 мм, деф.№4 с 35 в ![]() на L= 32 мм, деф.№5 | Токарно-винторезный станок 16К20 | Резец проходной ГОСТ 2719-83 | Обработать поверхность после наплавки. | ||||||||
| 040 | Точение чистовое с Ø 30,2 в ![]() на L= 32 мм, деф.№5 | Токарно-винторезный станок 16К20 | Резец фасонный ГОСТ 2719-83 | Обеспечить третий класс чистоты поверхности по ГОСТ 2759-89 | ||||||||
| 045 | Нарезание наружной резьбы М24х1,5, на L = 30 мм, деф.№4 | Токарно-винторезный станок 16К20 | Резец фасонный для резьбы ГОСТ 2719-83 | Нарезать резьбу М24х1,5 на длину 30 мм. Не допускать перекоса резца | ||||||||
| 050 | Сверление в мм на L = 43 мм, деф.№2 | Вертикально-сверлильный станок 2Н118 | Сверло спиральное ГОСТ 10902-77 | Обеспечить точное центрирование сверла | ||||||||
| 055 | Фрезерование канавки L= мм, деф.№3 | Вертикально-фрезерный станок 6012Ц | Фреза шпоночная ГОСТ 26595-85 | Фрезеровать до устранения дефекта и в необходимую шероховатость | ||||||||
| 060 | Зенкерование (2 отв.) в ![]() L = 43 мм, деф.№2 | Вертикально-сверлильный станок 2Н118 | Зенкер ГОСТ 3231-71 | Зенкеровать до номинального размера | ||||||||
| 065 | Шлифование в ![]() L = 32 мм, деф.№5 | Станок кругло-шлифовальный 3Б110 | Шлифовальный круг ГОСТ 2424-83 | Шлифовать в необходимые размеры с допусками. Не допускать смещения инструмента | ||||||||
| 070 | Контрольная | Стенд для контроля | Нутромер НИ-18-50-1 ГОСТ 868-82 Микрометр МК 025 ГОСТ 6507-90 Калибр – пробка ГОСТ 14816-69 | Для всех дефектов Контролировать размеры,овальность отверстий, конусность, бочкообразность, неплоскостность и непараллельность |