Файл: Курс лекций по неразрушающему контролю технические устройства уфа 2017 содержание технические устройства опасных производственных объектов 3 Виды контроля 3.docx
ВУЗ: Не указан
Категория: Не указан
Дисциплина: Не указана
Добавлен: 23.11.2023
Просмотров: 38
Скачиваний: 3
ВНИМАНИЕ! Если данный файл нарушает Ваши авторские права, то обязательно сообщите нам.
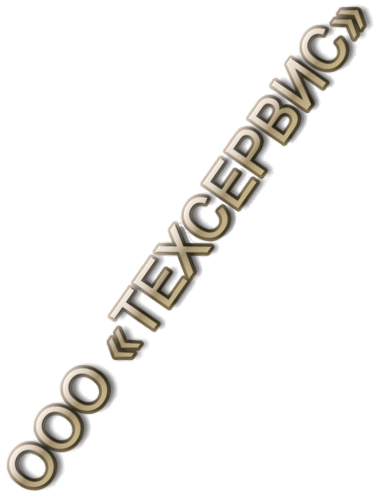

ОБЩИЙ КУРС ЛЕКЦИЙ
ПО НЕРАЗРУШАЮЩЕМУ КОНТРОЛЮ
ТЕХНИЧЕСКИЕ УСТРОЙСТВА
Уфа - 2017
СОДЕРЖАНИЕ
1.Технические устройства опасных производственных объектов 3
2.Виды контроля 3
3.Изготовление технических устройств 4
4.Классификация технических устройств 7
-
Технические устройства опасных производственных объектов
Безопасность производственных объектов в значительной степени зависит от надёжности и безопасности технических устройств, входящих в них.
Под техническими устройствами понимаются: технологическое оборудование, машины и агрегаты, технические системы (комплексы), аппаратура, приборы, их узлы и составные части, применяемые на опасных производственных объектах. Они изготовляются из металлов и сплавов, пластмассы, композитов, керамики и т.д.
Технические устройства опасных производственных объектов в основном изготовлены из металлов. В процессе изготовления они проходят сложный технологический цикл, включающий:
-
плавку; -
литье; -
обработку давлением; -
термическую и механическую обработку; -
соединение с другими деталями.
Большинство технических устройств имеют составные части, соединённые разными способами. В основном это неразъёмные соединения полученные сваркой плавлением.
Из всех технических устройств по изготовлению и условиям эксплуатации можно выделить четыре основные группы:
-
силовые металлоконструкции (стрелы грузоподъёмных машин, установщиков, несущие форменные конструкции, силовые элементы агрегатов обслуживания); -
сосуды, теплообменные аппараты, трубопроводы (сосуды и ёмкости, влагомаслоотделители и холодильники компрессорных установок, теплообменные аппараты, камеры нейтрализации, магистрали газов и жидкостей и др.); -
механизмы и машинное оборудование (гидроприводы, редукторы, насосы, компрессоры, вентиляторы и приводные электродвигатели, дизельные электростанции); -
конструкции строительных сооружений (металлические конструкции, бетонные и железобетонные конструкции, каменные и армокаменные конструкции).
-
Виды контроля
В реальности любое изделие или конструкция имеют дефекты, возникающие на всех стадиях процесса изготовления, начиная от получения самого материала (прокат, литье, ковка) и заканчивая этапом окончательной сборки всего изделия (конструкции). На каждой стадии изготовления и при последующей эксплуатации для обеспечения требуемого качества (надёжности) изделия проводится контроль – проверка соответствия объекта установленным техническим требованиям.
Существует три вида контроля:
-
входной – контроль продукции поставщика, поступившей к потребителю или заказчику, и предназначаемый для использования при изготовлении, ремонте или эксплуатации продукции; -
операционный – контроль продукции или процесса во время выполнения или после завершения технологической операции; -
приёмочный – контроль продукции, по результатам которого принимается решение о её пригодности к поставкам и (или) исполнению.
Отдельно существует эксплуатационный контроль – контроль, осуществляемый на стадии эксплуатации. В эксплуатационном контроле различают: входной, профилактический (необязательный) и текущий (обязательный) виды контроля.
По характеру воздействия на технологический процесс различают пассивный и активный контроль. В последнем случае предусматривают использование результатов контроля для корректировки изготовления продукции. Полнота охвата контролем продукции уменьшается по мере возрастания иерархии контролируемой инстанции. Отдел или лаборатория проводят сплошной контроль (контроль каждой единицы продукции) только для продукции ответственного назначения, в остальных случаях они проводят выборочный контроль. Более высокие контролирующие инстанции осуществляют инспекционный контроль (проверка эффективности ранее выполненного контроля) который обычно бывает выборочным. Доля выборочно контролируемых изделий (объем контроля) тем меньше, чем выше контролирующая инстанция. Инспекционный контроль, проводимый в случайное время, называют летучим. Он позволяет более эффективно проверять работу службы контроля, чем периодический.
При выборочном контроле могут применяться разрушающие методы, нарушающие пригодность продукции к применению. В некоторых случаях после такого контроля продукция может оказаться пригодной к использованию, однако контроль этого не гарантирует. Как правило, неразрушающими методами контролируют всю продукцию, что повышает её эксплуатационную надёжность.
-
Изготовление технических устройств
Технические устройства опасных производственных объектов в основном изготовлены из металлов. В процессе изготовления они проходят сложный технологический цикл .
Литье — это технологический процесс изготовления заготовок и изделий путём заполнения жидким металлом изложницы или формы с последующим затвердеванием металла.
Изложница — это форма простых геометрических очертаний обычно с малой конусностью. Отлитый в изложницу металл (слиток) является заготовкой для дальнейшей обработки давлением. Литейная форма имеет конфигурацию, приблизительно или даже точно (точное литье) повторяющую конфигурацию изделия. В ней получают заготовки, называемые отливками. Для получения пустотелых отливок в форму вставляют стержни, воспроизводящие конфигурацию внутренних полостей. Изложницы и формы делают разъёмными для удобства извлечения слитка или отливки. Их снабжают литниковой системой, через которую заливают расплавленный металл, обеспечивают возможность выхода образующихся газов
Обработку давлением металлов осуществляют: свободной ковкой (ударным воздействием), прессованием (неударным воздействием), штамповкой (ковкой или прессованием в форму-штамп), высадкой (продавливанием сквозь отверстие), волочением (протаскиванием металла через отверстие-оправку для получения прутка, проволоки), прокаткой (обжатием между вращающимися валками) и др.
Прокатку слитка производят, как правило, в два этапа: сначала получают заготовку квадратного (блюмс) или прямоугольного (сляб) сечения, а потом из этой заготовки прокатывают листы, трубы, рельсы и другие профили. Прогрессивной технологией является прокатка заготовки непосредственно из застывающего металла (непрерывная разливка). Обработка давлением позволяет получить металл требуемой формы, уплотняет его, измельчает структуру, улучшает механические свойства.
Термическая обработка состоит в нагреве и последующем охлаждении металлов и сплавов по определённому закону и направлена на изменение их свойств в результате изменения внутренней структуры. Цель термообработки состоит в снятии внутренних напряжений, в повышении прочности, твёрдости, пластичности и вязкости металла (см. выше). Специфическими видами термообработки являются поверхностная электротермическая и химико-термическая. В этом случае локальному воздействию (закалке) подвергают поверхностные зоны металла.
Способы соединений, заготовок и деталей
Соединения деталей бывают подвижные, и неподвижные, здесь рассматривает только некоторые типы последних. Неподвижные соединения делят на разъёмные (разборные) и неразъёмные. Способы получения неразъёмных соединений — сварка, пайка, клейка, клёпка. Практически все разъёмные соединения основаны на использовании сил трения (резьбовые соединения и прессовые посадки). В газо- и гидроплотных конструкциях к соединениям предъявляют требования герметичности. В этих случаях в дополнение или вместо рассмотренных ниже методов контроля соединения проверяют методами течеискания.
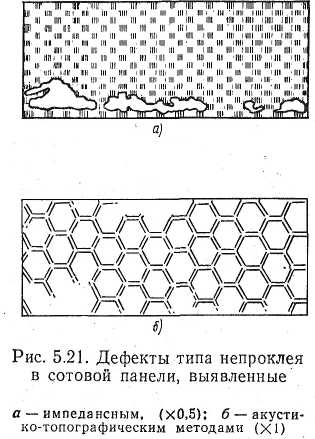
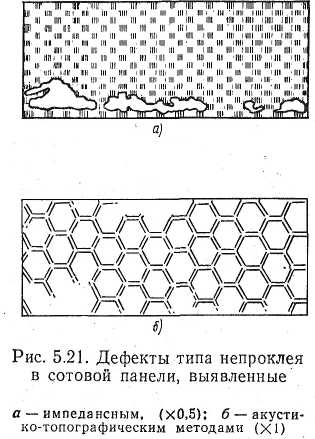
Рис. 1. Дефекты типа непроклея в сотовой панели, выявленные
а — импедансным, ( 0,5); б — акустико-топографическим методами ( 1)
Сварка. Все многочисленные виды сварки разделяют на две группы: сварку плавлением и давлением. В первом случае свариваемые заготовки располагают на некотором расстоянии друг от друга и осуществляют расплавление кромок заготовок и заполнение разделки присадочным (обычно из электрода) или оплавленным основным металлом. Во втором случае также возможно расплавление кромок, но сварку осуществляют при сдавливании свариваемых заготовок.
Сварку плавлением разделяют на виды по способу подвода энергии: газовая (горение газов типа ацетилена, пропана; этот способ сварки в настоящее время применяют все реже), электродуговая (электрической дугой), электрошлаковая (нагревание шлака-флюса протекающим через него током), электронно-лучевая, плазменная, лазерная и др. Кроме того, виды сварки различают по способам защиты от атмосферного воздуха зоны дуги и металлической ванны: с помощь плавящегося покрытия электрода, флюса (покрытия, растворяющего окислы), оттесняющих воздух газов (аргона, углекислого газа), вакуумирования. Наиболее распространёнными видами сварки являются электродуговая сварка под флюсом и аргонно-дуговая сварка, а для больших толщин — электрошлаковая сварка. Быстро развивается электронно-лучевая сварка.
Наиболее распространённым видом сварки давлением является контактная стыковая электросварка, в которой расплавления металла кромок достигают за счёт пропускания сильного тока через свариваемые детали и повышенного электросопротивления в месте контакта. Затем свариваемые заготовки сильно сдавливают — осаживают. Её варианты — точечная сварка, когда сваривают отдельные точки двух заготовок (пропускают ток через сжимающие металл электроды в виде металлических стержней); роликовая сварка, при которой вместо стержневых электродов для сдавливания металла и пропускания тока применяют катящиеся вдоль шва ролики. К сварке давлением относят также сварку трением (вращение деталей с последующей осадкой), диффузионную сварку (сдавливание в вакууме хорошо пришлифованных и очищенных поверхностей), высокочастотную сварку (нагрев сдавленных кромок токами высокой частоты) и другие виды.
Каждому виду сварки свойственны свои характерные дефекты. Особенно сильно отличаются дефекты сварки плавлением и давлением. Для сварки плавлением (ГОСТ 2601-84) свойственны некоторые дефекты, характерные для литого металла: усадочные раковины, поры (иногда поры располагаются цепочками, группами), включения (шлаковые, флюсовые, окисные, сульфидные, металлические). Специфическими дефектами сварки являются: непровар — местное несоединение вследствие неполного расплавления кромок основного металла или поверхности ранее выполненных валиков; вогнутость или превышение проплавления корня сварного шва (корнем называют участок в сечении шва, с которого начинают процесс сварки); подрез — углубление в основном металле вдоль линии сплавления; большое превышение верхней выпуклости шва (её иногда называют валиком усиления); смещение кромок сварного шва из-за недоброкачественной сборки; прожог в виде сквозного отверстия, образовавшегося в результате вытекания сварочной ванны.
Особенно опасными дефектами являются сварочные трещины, возникающие обычно в процессе остывания сварного соединения. Они могут появиться не только в наплавленном металле, но также в основном металле соединения в зоне влияния на него сварочного процесса (зона термического влияния). Различают трещины продольные и поперечные относительно оси шва (рис. 2), разветвлённые (паукообразные), образующие сетку.
Причинами возникновения перечисленных дефектов могут быть: неправильный состав сварочных материалов (электродов, флюсов); неправильная подготовка к сварке (неверная форма разделки; неверно выбрано расстояние между свариваемыми заготовками); нарушение режима сварки.
Трещины могут возникать также в результате неправильной конструкции сварного изделия, неправильного термического режима сварки, наличия включений, расслоений и других дефектов в основном металле.
Многие крупногабаритные изделия в процессе сварки подогревают до 200... 300°С, а непосредственно после сварки помещают в печь для отжига или отпуска, чтобы снять внутренние напряжения. Захолаживание изделий, как правило, приводит к образованию трещин.
Дефекты формирования сварного шва (смещения кромок, подрезы, неправильная форма выпуклостей) проверяют визуально или с помощью шаблонов. Поверхностные несплошности обнаруживают поверхностными методами. Для выявления внутренних и некоторых поверхностных несплошностей применяют радиационные и ультразвуковые методы (см. рис. 2, б). Эти же методы используют при контроле сварки пластмасс.