Добавлен: 23.11.2023
Просмотров: 119
Скачиваний: 4
ВНИМАНИЕ! Если данный файл нарушает Ваши авторские права, то обязательно сообщите нам.
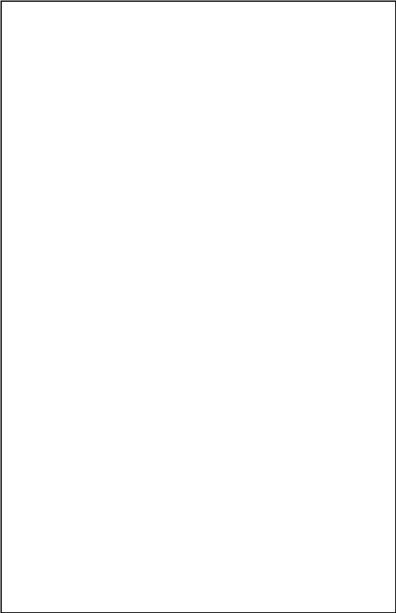
СОДЕРЖАНИЕ
Введение | 3 |
1 Постановка задачи | 5 |
1.1 История предприятия | 5 |
1.2 Характеристика производимой продукции | 6 |
1.3 Описание технологии производства диаммонийфосфата | 8 |
1.4 Прототип системы | 20 |
1.5 Постановка цели дипломного проектирования | 21 |
2 Описание автоматизированного процесса первой стадии | |
нейтрализации фосфорной кислоты | 24 28 |
3 Требования к автоматизации процесса первой стадии | |
нейтрализации фосфорной кислоты | 28 |
4 Расчет скоростного аммонизатора-испарителя | 30 |
5 Выбор и расчет элементов системы | 35 |
Список использованных источников | 44 |
| |
| |
| |
| |
| |
| |
| |
| |
| |
| |
| |
| |
| |
ВВЕДЕНИЕ
В химической промышленности комплексной механизации и автоматизации уделяется большое внимание. Это объясняется сложностью и высокой скоростью протекания технологических процессов, а также чувствительностью их к нарушению режима, вредностью условий работы, взрыво- и пожароопасностью перерабатываемых веществ и так далее.
Под механизацией понимают мероприятия по внедрению механизмов и машин, направленные, как правило, на облегчение физического труда. В механизированном технологическом процессе человек продолжает принимать непосредственное участие, но его физическая работа сводится лишь к нажатию кнопок, повороту рычагов и тому прочее. Здесь на человека возложены функции управления механизмами и машинами. Ограниченные возможности человеческого организма (утомляемость, недостаточная скорость реакции на изменение окружающей обстановки и на большое количество одновременно поступающей информации и так далее) являются препятствием для дальнейшей интенсификации производства. Наступает новый этап машинного производства — автоматизация, когда человек освобождается от непосредственного участия в производстве, а функции управления технологическими процессами, механизмами, машинами передаются автоматическим устройствам.
Автоматизация приводит к улучшению основных показателей эффективности производства: увеличению количества, улучшению качества и снижению себестоимости выпускаемой продукции, повышению производительности труда. Внедрение автоматических устройств обеспечивает высокое качество продукции, сокращение брака и отходов, уменьшение затрат сырья и энергии, уменьшение численности рабочих, удлинение сроков межремонтного пробега оборудования.
Комплексная автоматизация процессов химической технологии предполагает не только автоматическое обеспечение нормального хода этих процессов, но и автоматическое управление пуском и остановом аппаратов для ремонтных работ и в критических ситуациях.
В автоматизированном производстве человек переключается на творческую работу - анализ результатов управления, составление заданий и программ для автоматических приборов, наладку сложных автоматических устройств и так далее.
Для обслуживания агрегатов, оснащенных сложными системами автоматизации, требуются специалисты с высоким уровнем знаний. От специалистов требуются знания не только устройства различных приборов, но и общих принципов составления систем автоматического управления.
В каждом производственном процессе, наряду с «вещественными потоками», существуют и «информационные потоки». Они представляют собой некоторую первичную информацию и необходимы для контроля и управления. Эта информация передается на соответствующие пункты управления (операторную, диспетчерскую и так далее), где подвергается обработке и используется для принятия решений при управлении процессом.
Системы автоматического регулирования оказываются не достаточно эффективными, если они спроектированы только на основании общих положений теорем автоматического регулирования.Для наиболее эффективной работы таких систем их необходимо проектировать с учетом особенностей технологических процессов, для которых они предназначены и максимально знать требования, предъявляемые к химико-технологическим процессам.
Целью работы дипломного проекта является автоматизация процесса первой стадии нейтрализации фосфорной кислоты в производстве минеральных удобрений, путем разработки системы автоматического регулирования расходов кислоты и аммиака; выполнить технико–экономическое описание: получить технико–экономические показатели и рассчитать себестоимость системы; рассмотреть работоспособность системы со стороны охраны труда и безопасности жизнедеятельности, а также работу процесса в возможных чрезвычайных ситуациях.
-
ПОСТАНОВКА ЗАДАЧИ
1.1 История предприятия
История предприятия ООО «Балаковские минеральные удобрения» начинается с ввода в эксплуатацию Балаковского химического завода.
Территориально завод был построен с расчетом на поставку фосфорсодержащих удобрений сельскому хозяйству. Уже в восьмидесятые годы Балаковский химический завод становится одним из крупнейших в отрасли.
На производстве налажен выпуск серной кислоты, фосфорной кислоты, двойного суперфосфата, аммофоса, диаммонийфосфата, сульфоаммофоса, NPK-удобрений.
В 1998 году химическое производство, входящее в ОАО «Иргиз», было полностью остановлено. После смены собственника теперь уже ООО «Балаковские минеральные удобрения» возобновило промышленное производство с 1 июня 1999 года.
Становление производства можно разбить на несколько этапов:
-
восстановление основного и вспомогательного оборудования; -
восстановление проектных объемов производства и реализации, полная загрузка производственных мощностей; -
реконструкция производства, направленная на интенсификацию существующих мощностей, повышение технологий, снижение экологической нагрузки на окружающую среду.
В 2000 году реконструкция цеха фосфорных удобрений, позволившая вывести качество производимой продукции на новый уровень, снизить выбросы вредных веществ в атмосферу, уменьшить расход сырьевых и энергоресурсов на производство минеральных удобрений.
В 2001 году начались работы по монтажу импортной установки по фасовке удобрений в Биг-Бэги. Внедрена автоматизированная система учета электрической энергии (АСКУЭ), которая позволила снизить на 3 ÷ 5 % объем потребления электроэнергии, благодаря повышению надежности работы системы электроснабжения, повышению оперативности в управлении потоками электроэнергии и мощности.
Режим работы предприятия: непрерывный, круглосуточный, 310 рабочих дней в году (7200 часов).
1.2 Характеристика производимой продукции
Вся перечисленная ранее продукция выпускается по одной технологической схеме. Поэтому рассмотрим схему производства диаммонийфосфата.
Диаммонийфосфат удобрительный – сокращенно ДАФ, представляет собой сложное водорастворимое удобрение, содержащее два действующих вещества – азот и фосфор. Производство ДАФ основано на двух стадиях нейтрализации экстракционной фосфорной кислоты аммиаком с последующей грануляцией и сушкой аммонизированной пульпы.
Основные реакции нейтрализации протекают с выделение большого количества тепла. Взаимодействие аммиака (NH3) с фосфорной кислотой (Н3РО4) на первой стадии идет по уравнению
Н3РО4(ж.) + NH3(ж.) = NH4H2PO4(тв.) + 147,0 кДж (моноаммонийфосфат).
Для получения диаммонийфосфатной пульпы проводят вторую стадию
NH4H2PO4(тв.) + NH3(г.) = (NH4)2HPO4(тв.) + 75,4 кДж (диаммонийфосфат).
Образованный двух замещенный фосфат аммония позволяет увеличить содержание азота в продукте до требуемой величины.
Диаммонийфосфат термически малоустойчив и начинает разлагаться уже при температуре 70 ºС с выделением аммиака, превращаясь в моноаммонийфосфат.
(NН4)2НРО4 → NН4Н2РО4 + NН3
Стадия нейтрализация фосфорной кислоты обязательна. Без нее не возможны последующие стадии обработки и выпуска диаммонийфосфата. Степень нейтрализации фосфорной кислоты на первой стадии определяется ее концентрацией (уровнем pH) и технологической схемой производства.
На вторую стадию нейтрализации пульпа должна поступать с минимальной влажностью и уровнем pH=4÷5. Для предотвращения загустевания пульпы во время ее упаривания первую стадию нейтрализации следует вести до мольного отношения, при котором существует максимальная растворимость образующихся фосфатов аммония. Наибольшая растворимость фосфатов при мольном отношении 1,4
÷ 1,5
Оптимальная степень нейтрализации кислоты на первой стадии определяется тремя факторами: сохранение подвижности пульпы при ее упаривании, сохранение термической стабильности при ее упаривании и обеспечение минимальной влажности пульпы на выходе с выпарной установки.
Товарный ДАФ выпускается согласно требованиям ТУ 113-08-556-93 с изм.1,2,3 – и должен соответствовать требованиям (таблица 1).
Таблица 1 - Требования, предъявляемые к ДАФ
-
Наименование показателей
Норма
Массовая доля общих фосфатов, %, не менее
47 1
Массовая доля общего азота, азот аммонийный, %, не менее
18 1
Массовая доля воды, %, не более
1,50,3
Гранулометрический состав. Массовая доля гранул размером менее 1 мм, %, не более
3
Гранулометрический состав. Массовая доля гранул размером от 2 мм до 5 мм, %, не менее
97
Гранулометрический состав. Массовая доля гранул размером более 6 мм, %
100
Статическая прочность гранул, МПа (кгс/см2), не менее
3,0 (30)
Рассыпчатость, %
100
Пылимость, г/т, не более
60
Внешний вид
Гранулы от белого до черного цвета с различными оттенками
Образование комплексных соединений происходит при низких значениях рН. Поэтому, чтобы избежать образования неусвояемых солей, процесс нейтрализации фосфорной кислоты необходимо вести при рН более 3.
ДАФ применяется в сельском хозяйстве как концентрированное гранулированное азотно-фосфорное удобрение.
1.3 Описание технологии производства диаммонийфосфата
Получение гранулированного ДАФ производится по технологической схеме (рисунок 1) и состоит из следующих стадий (рисунок 2):
-
прием, хранение и снабжение производства сырьем; -
первая стадия нейтрализация фосфорной кислоты аммиаком; -
вторая стадия нейтрализации фосфорной кислоты. -
гранулирование и сушка продукта в аппарате БГС; -
классификация продукта и дробление крупной фракции; -
очистка отходящих газов; -
омасливание диаммонийфосфата; -
дообработка и подготовка диаммонийфосфата. -
фасовка диаммонийфосфата.