Файл: Эксплуатация и обслуживание токарно винторезного станка модели 1П611.docx
Добавлен: 30.11.2023
Просмотров: 354
Скачиваний: 31
ВНИМАНИЕ! Если данный файл нарушает Ваши авторские права, то обязательно сообщите нам.
Перед пуском в ход электродвигателей следует:
-
Измерить сопротивление изоляции, измерение производить мегомметром на напряжении 500 волы. Допустимое сопротивление изоляции обмоток статора должно составлять не менее 0,5 МОм. Электродвигатель, имеющий сопротивление изоляции обмоток ниже 0,5 МОм, должен быть подвергнут сушке. -
Проверить правильность вращения электродвигателей: при включении рукоятки ,вверх должно быть прямое вращение шпинделя. При его неправильном вращении необходимо поменять местами любые две фазы электропитания станка.
2.2 Организация технического обслуживания.
Система технического обслуживания металлорежущего оборудования является частью принятой системы планово – предупредительных ремонтов, целью которой является сведение к минимуму простоя оборудования, обеспечить нормальную работоспособность в течение всего срока службы
В первую очередь профилактическому осмотру нужно подвергать [4]:
-
Винт с гайкой и направляющие колонки; -
Направляющие каретки; -
Направляющие стола и станины; -
Подшипники шпинделя в случае повышенного шума, биения и нагрева; -
Механизм подачи; -
Подшипники электромоторов; -
Пусковую аппаратуру в нише электрооборудования.
Основные положения системы планово – предупредительных ремонтов металлорежущих станков [4]:
1. Объем ремонтных работ определяется условиями работы оборудования, его ремонтными способностями и качеством выполнения ремонтных работ и технического обслуживания. Также этот показатель зависит от отработанного времени каждой единицы оборудования без ремонта.
2. Соблюдение ремонтного цикла – основная потребность станочного оборудования в ремонте, которая может быть удовлетворена путем выполнения плановых ремонтов через периодически повторяющиеся интервалы времени в определенной последовательности.
3. Объем ремонтных работ, необходимых для конкретного оборудования определяется его ремонтосложностью.
4. Кроме периодических ремонтов планируется техническое обслуживание оборудования ремонтной службой.
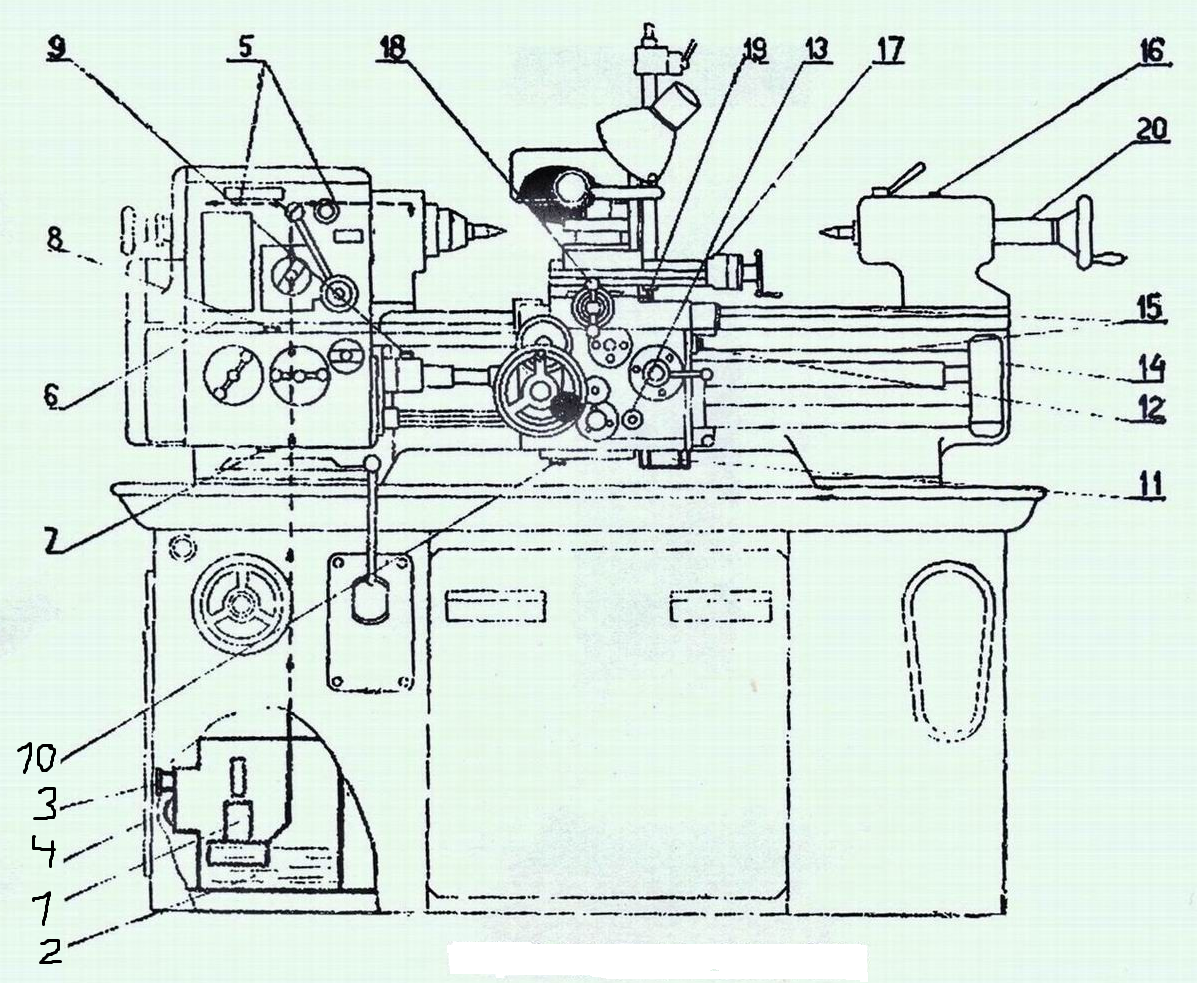
Рис. №2 Карта смазки токарно – винторезного станка 1П611 [3].
Таблица №3. Спецификация к карте смазки токарно – винторезного станка 1П611 [3].
№ позиции | Наименование смазочных устройств | Режим смазки | Марка смазочного материала по ГОСТ |
1 | Плунжерный насос | Через 3 месяца | Индустриальное 20 по ГОСТ 1707-51 |
2 | Резервуар редуктора | Через 3 месяца | Индустриальное 20 по ГОСТ 1707-51 |
3 | Маслоуказатель | - | - |
4 | Залив масла | - | - |
5 | Маслопровод к передней и задней опорам шпинделя | - | - |
6 | Слив масла из передней бабки | - | - |
7 | Слив масла | - | - |
8 | Залив масла | - | - |
Продолжение таблицы №3.
9 | Масленка для смазки опоры винта | Ежедневно | Индустриальное 20 по ГОСТ 1707-51 |
10 | Слив масла | - | - |
11 | Плунжерный насос с ручным приводом | Через 3 месяца | Индустриальное 20 по ГОСТ 1707-51 |
12 | Контрольный глазок | - | - |
13 | Уровень маслованны фартука | Через 3 месяца | Индустриальное 20 по ГОСТ 1707-51 |
14 | Масленка опоры винта и валика | Ежедневно | Солидол ГОСТ 1033-51 |
15 | Поверхности направляющих станины, ходового винта, ходового валика и рейки | Ежедневно | Солидол ГОСТ 1033-51 |
16 | Масленка пиноли винта задней бабки | Ежедневно | Солидол ГОСТ 1033-51 |
17 | Масленка опоры винта верхней каретки | Ежедневно | Солидол ГОСТ 1033-51 |
18 | Масленка опоры винта поперечной каретки суппорта | Ежедневно | Индустриальное 20 по ГОСТ 1707-51 |
19 | Залив масла | - | - |
20 | Масленка опоры винта задней бабки | Ежедневно | Индустриальное 20 по ГОСТ 1707-51 |
До первоначальной заливки маслом необходимо промыть все масляные емкости бензином, либо осветительным керосином, заполнив их затем сортом масла. Смену масла рекомендуется производить первый раз после 10-ти дней работы, во второй раз после 20-ти дней работы, а затем через каждые 3 месяца.
Все вращающиеся поверхности, смазка которых специально не оговорена, должны быть заполнены солидолом при сборке
Для смазки необходимо применять масла следующих характеристик:
Жидкая смазка: Индустриальное 20 по ГОСТ 1707-51, вязкость 2,6 – 3,31 в условных градусах Энглера при 50оС;
Густая смазка: Солидол по ГОСТ 1033-51, температура каплепадения 70оС.
Раздел 3. Организация ремонта токарно – винторезного станка 1П611
3.1 Структура технологического процесса ремонта токарно – винторезного станка 1П611.
Ремонт – комплекс операций по восстановлению работоспособности станков и другого оборудования. В свою очередь, подразделяется на текущий, средний, и капитальный ремонты [4].
Текущий ремонт – ремонт, выполняемый для обеспечения или восстановления работоспособности изделия и состоящий в замене или восстановлении отдельных частей оборудования.
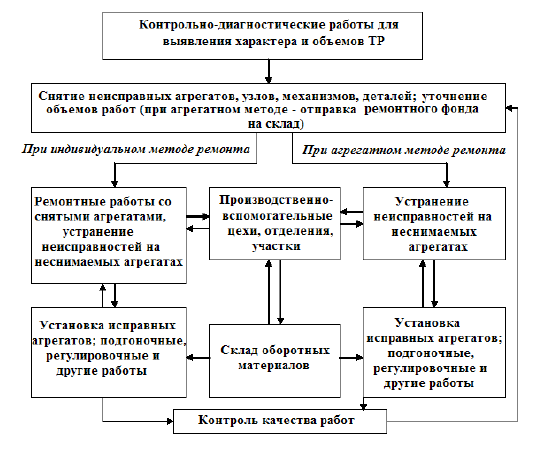
Рис. №3 Схема текущего ремонта [4].
В зависимости от конструктивных особенностей оборудования, характера и объема производимых работ, текущие ремонты могут подразделяться на первый, второй и т.д. текущие ремонты. Выполняются такие мероприятия как [4]:
1) Работы регламентированного технического обслуживания;
2) Замена отдельных узлов и деталей;
3) Сварочно – слесарные работы;
4) Регулировка соединений и сопряжений;
5) Нанесение противокоррозийных покрытий;
6) Ревизия оборудования;
7) Измерение на точность.
Средний ремонт проводят для восстановления неисправности и частичного восстановления ресурса изделия с заменой или восстановлением составных частей ограниченной номенклатуры и контролем технического состояния, выполняемым в полном объеме, установленном нормативной технической документацией [4].
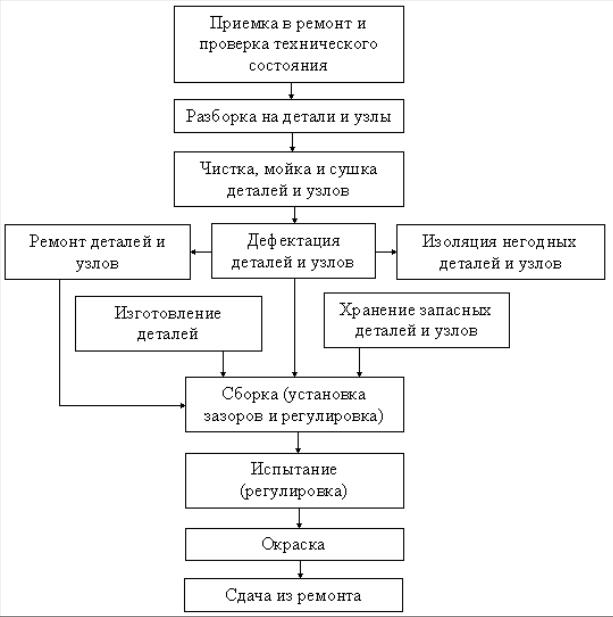
Рис. №4 Схема капитального ремонта [4].
Капитальный ремонт – ремонт, выполняемый для восстановления исправности и полного или близкого, к полному восстановлению ресурса изделия с заменой любых его частей, включая базовые элементы. Для выполнения данного ремонта на предприятии должны иметься технические условия на каждую единицу ремонтируемого оборудования. В него входят следующие работы [4]:
1. Объем работ текущего ремонта;
2. Замена или восстановление всех изношенных узлов и деталей;
3. Выверка и центровка оборудования;
4. Послеремонтные испытания.
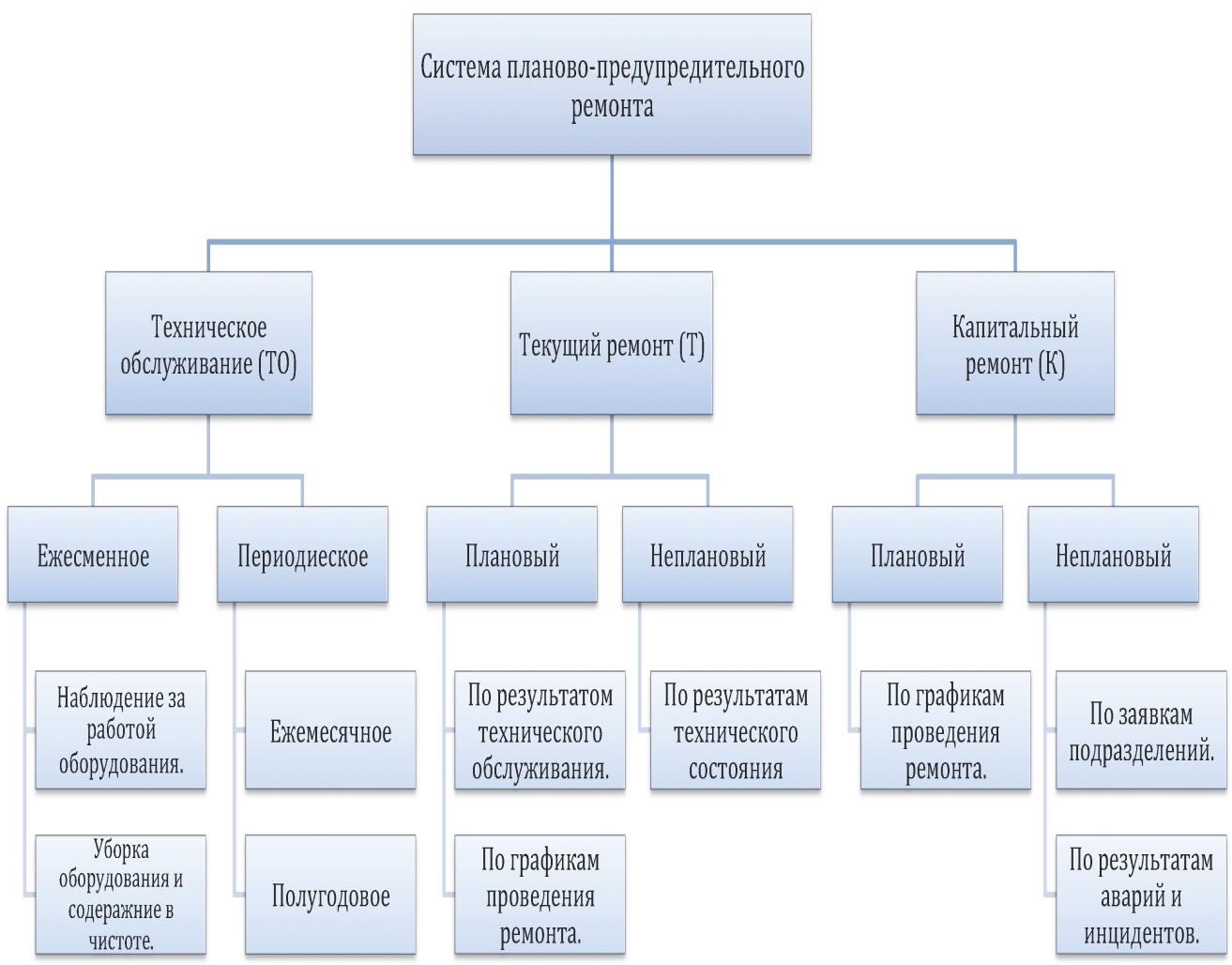
Рис. №5 Содержание системы ППР [4].
3.2 Визуальный и инструментальный контроль.
Осмотр является первым в списке органолептических методов, который начинает диагностирование и заканчивает его визуальным подтверждением поставленного диагноза.
Нормативно-технической документации предписывается проведение осмотра как основного источника получения информации о состоянии оборудования. Осмотр является составной часть любого комплекса диагностирования, проводится при приёмке смены, при подготовке ремонта, при появлении необычного шума и повышенной вибрации механизма.
Задача эксплуатационного осмотра – выявление повреждений (дефектов) и поиск неисправностей оборудования при проведении технического обслуживания в сроки, регламентированные эксплуатационной документацией и регистрация результатов осмотров в эксплуатационной документации. Проводится эксплуатационным персоналом при проведении регламентного технического обслуживания.
Одной из разновидностей осмотра является наблюдение – периодический осмотр мест возможных повреждений элементов, деталей, узлов оборудования с целью регистрации развития повреждений или поведения элементов системы (возникновение деформации, вибрации, ослабление крепежа, ударов и т.п.) во время работы оборудования.
Процесс осмотра, как и все технологические операции, имеет три стадии: подготовительную, рабочую и завершающую.
Подготовительная стадия осмотра включает [1]:
-
предварительный обзор места установки оборудования; -
опрос эксплуатационного персонала, а при необходимости представителей монтажных, наладочных и других предприятий, участвующих в проведении работ на данном оборудовании, о ранее обнаруженных неисправностях, проведенных заменах деталей и т.п.; -
подготовку технических средств и регистрационных форм, инструктаж лиц, участвующих при производстве работ.
Рабочая стадия – выполнение заранее разработанного алгоритма детального осмотра элементов оборудования.
Задачей инструментального контроля является определение изменение размеров и формы деталей (овальность, конусность, бочкообразность, неплоскостность, изгиб и т.д.), относительного взаимного положения деталей (не параллельность, перекос осей, несоосность, торцевое и радиальное биение, несимметричность).
Инструментальный контроль проводится в соответствии с планом-графиком контроля, утвержденным руководителем предприятия и согласованным природоохранными органами. Планы – графики составляются отдельно для каждого вида контролируемых сред: промышленных выбросов, сточных и природных вод, почв с указанием точек отбора проб, способах пробоотбора, его периодичности, перечня контролируемых веществ и перечня применяемых методик выполнения измерений или анализов. Применяемые методики должны быть аттестованы согласно ГОСТ Р 8.563 - 96 ГСИ.
Результатыинструментального контроля оформляются в соответствии с требованиями ГОСТ Р 8.563 - 96 ГСИ. Методики выполнения измерений и отраслевыми нормативными документами и передаются экологической службе предприятия (или специалисту-экологу) для организации природоохранной деятельности.
3.3 Техническое диагностирование.
Техническая диагностика – процесс определения технического состояния объекта или получения оценки состояния, включающего диагнозы наиболее важных субъектов, составляющих объект диагностирования и определяющих полноту диагностирования объекта [4].
Основной задачей технической диагностики является организация эффективной проверки исправности, работоспособности, правильности функционирования технических объектов, то есть, организация процессов диагностирования технического состояния объектов при их изготовлении и эксплуатации, в том числе во время, до и после применения, ремонте и хранении [4].
Объектами технической диагностики являются сложные агрегаты и механизмы, для которых необходимо определять техническое состояние, их остаточный ресурс и риски эксплуатации.
Рассмотрим некоторые методы технической диагностики [5]:
Кинематический метод диагностирования характеризуется изменением положения, движения деталей и их сопряжений с геометрической точки зрения. Сюда следует отнести изменение некруглости, непрямолинейности, несоосность, шероховатость и т.п. Один из таких приборов показан на рисунке №6.
Метод нормированных параметров основан на сравнении экспериментально установленных значений параметров объекта с их паспортными значениями или с нормами технических условий. Например, сравнить показания производимого шума оборудованием шумомером (рисунок №7).
Тепловой метод заключается в анализе теплового излучения элементов, деталей или всего объекта в целом. Работоспособное оборудование имеет определенную картину теплового излучения. Изменения в этой картине свидетельствуют об изменении режима работы или неисправности в узлах трения и сопряжения деталей. Любые скачки можно зафиксировать инфракрасным термометром (рисунок №8).