Файл: 7 Технические условия на ремонт металлоконструкций птсд машин 1 Общие положения.docx
ВУЗ: Не указан
Категория: Не указан
Дисциплина: Не указана
Добавлен: 01.12.2023
Просмотров: 45
Скачиваний: 1
ВНИМАНИЕ! Если данный файл нарушает Ваши авторские права, то обязательно сообщите нам.
8 Последовательность операций технологического процесса сварки
при ремонте мостового крана
8.1 Общие требования на ремонт металлоконструкций
Для производства ремонта крановых металлоконструкций предприятие, производящее ремонт, должно иметь лицензию (разрешение) РОСТЕХНАДЗОРА на выполнение данного вида работ.
Ремонт крановых металлоконструкций должен производиться в соответствии с требованиями «Правил устройства и безопасной эксплуатации грузоподъёмных машин» и настоящей технологии.
Рабочие всех специальностей, занятые в выполнении работ по ремонту крановых металлоконструкций, должны по своей квалификации соответствовать выполняемой работе.
К производству сварочных работ допускаются сварщики, аттестованные по «Правилам аттестации сварщиков».
Во всех случаях ремонтные работы с заменой или усилением элементов металлоконструкций производятся при положении крана соответствующем наименьшей нагрузке на ремонтируемый узел.
При выполнении ремонтных работ кран должен быть установлен в ремонтную зону и обесточен.
8.2 Материалы и требования к их подготовке
1. Детали из стали Ст3 ГОСТ 535-88 и 09Г2С ГОСТ 19281-89. Качество материалов подтвердить сертификатами заводов-поставщиков и данными входного контроля.
2. Электроды типа Э-50А по ГОСТ 9467-75 марки УОНИ 13/55. Перед сваркой электроды необходимо прокалить в печи. Режим прокалки (температура и время) должен соответствовать указанному на ярлыке упаковки. Качество электродов подтвердить сертификатами заводов-поставщиков и данными входного контроля.
3.Сварку и прихватку производить на постоянном токе обратной полярности.
8.3 Подготовка к выполнению сварочных работ
1. Перед началом работ кран перевести в ремонтное положение.
2. Прихватку и сварку деталей производить сварщикам, аттестованным на право сварки грузоподъемных машин из малоуглеродистых и низколегированных сталей во всех пространственных положениях.
3. Соблюдать правила безопасной работы при резке, монтаже, сварке согласно соответствующим инструкциям.
4. Рабочие, работающие на высоте, должны пройти медицинское освидетельствование, проинструктированы по технике безопасности и особенностях работы.
5. Для выполнения ремонтных работ необходимо применять сварочный аппарат постоянного тока.
6. Электроды должны быть просушены при температуре 300-350 °С в течение 60 мин.
7. В сварных соединениях не допускаются следующие дефекты: подрезание более 0,5 мм, поры в виде сплошной сетки, шлаковые включения, кратеры, наплывы.
8. Контроль качества сварных соединений должен осуществляться в соответствии с требованиями ГОСТ 3242-79.
8.4 Ремонт узлов мостового крана
В качестве ремонтируемого крана примем мостовой электрический грейферный кран Г/П-20т, tст=6 мм
8.4.1 Усиление опорной части концевой балки.
Обнаружена усталостные трещины в результате нарушения режима работы крана.
-
Материалы, требования и их подготовка
-
Детали из стали марки ВСт3сп5 ГОСТ 14637-89 -
Качество материалов подтвердить сертификатами заводов-поставщиков. -
Электроды марки УОНИ 13-65 перед сваркой прокалить в сушильном шкафу Т-2500С, 1 час. Сварку и прихватку произвести на постоянном токе обратной полярности.
-
Подготовка и выполнение сварочных работ.
-
Прихватку и сварку производить сварщикам, аттестованным на право сварки грузоподъемных машин на малоуглеродистых и низколегированных сталях во всех пространственных положениях. -
Соблюдать правила безопасной работы при резке, монтаже, сварке согласно соответствующим инструкциям. -
Рабочие, работающие на высоте, должны пройти медицинское освидетельствование, проинструктированы по технике безопасности и особенностям работы.
-
Ремонт узла опорной части концевой балки.
-
В зоне наложения дополнительной стенки удалить ребра жесткости газовой резкой
-
Зачистить усталостные трещину 1. Засверлить отверстия, ограничивающие трещины диаметром 9 мм (dотв=1,5tст=1,5*6=9), отступив от видимого конца трещины на 10-15 мм.
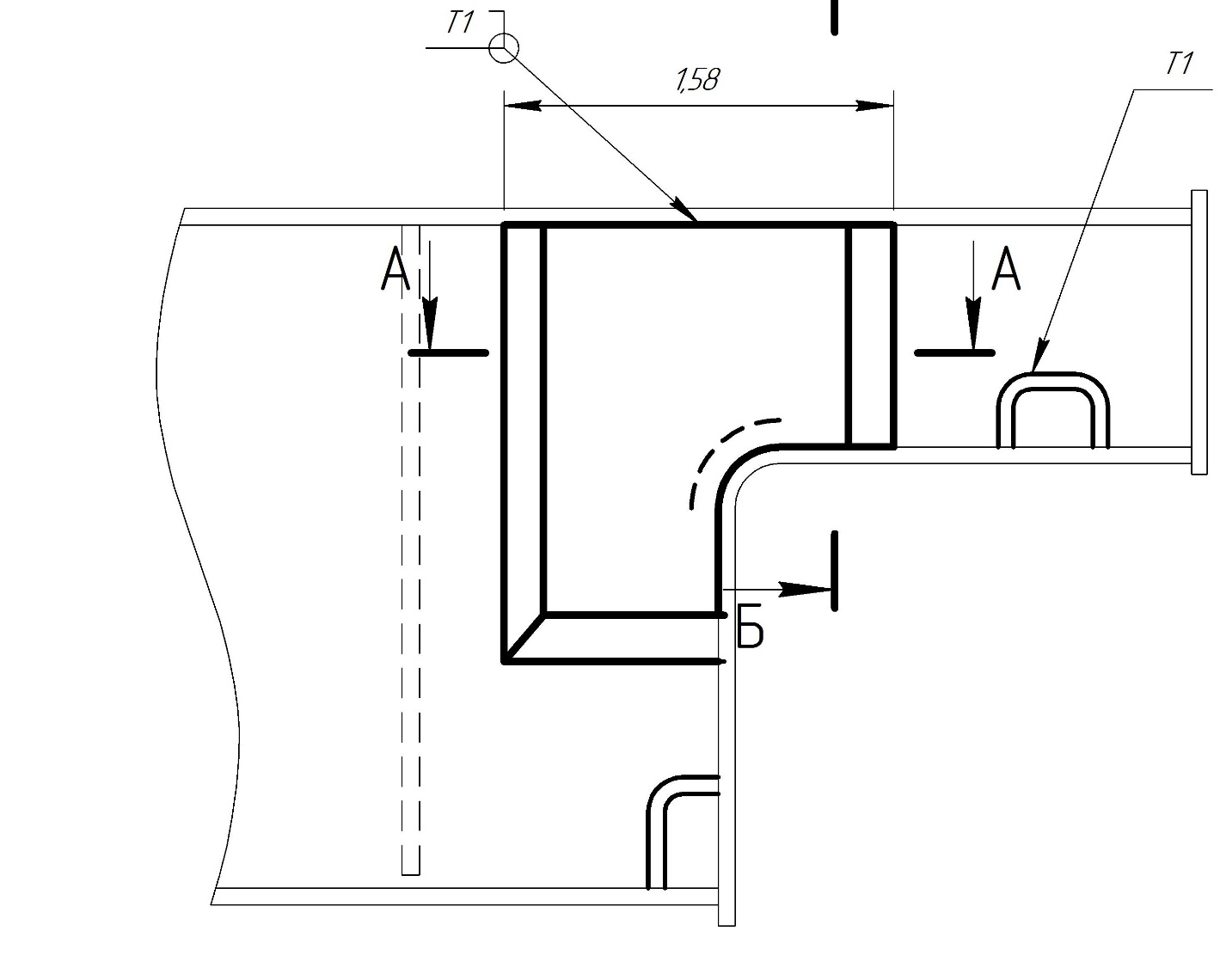
Рисунок 1 - Схема ремонтируемого узла
-
Вырубить трещины (см. рисунок 2) в соответствии ГОСТ 5264-80 под сварочный шов С17.
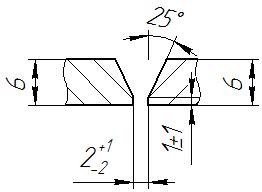
Рисунок 2 - Схема разделки кромок
-
Зачистить кромки и прилегающую поверхность к кромкам трещин 1,2 и 3 шириной не менее 20 мм до металлического блеска с обеих сторон. -
Качество кромок перед сваркой проконтролировать визуально. Заварить трещины 1,2 и 3 швом С17. Технологические размеры сварки см. Рис.3
Электроды ф 4мм, 1св=110-130 А
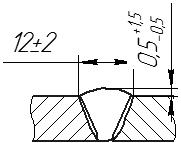
Рисунок 3 - Схема заварки трещин
-
Зачистить сварочные швы заподлицо с плоскость стенки. -
Проверить качество сварочных швов ультразвуком по ГОСТ 14782-86. -
Подготовить дополнительную стенку 1. Основные размера см.
Рисунок 4
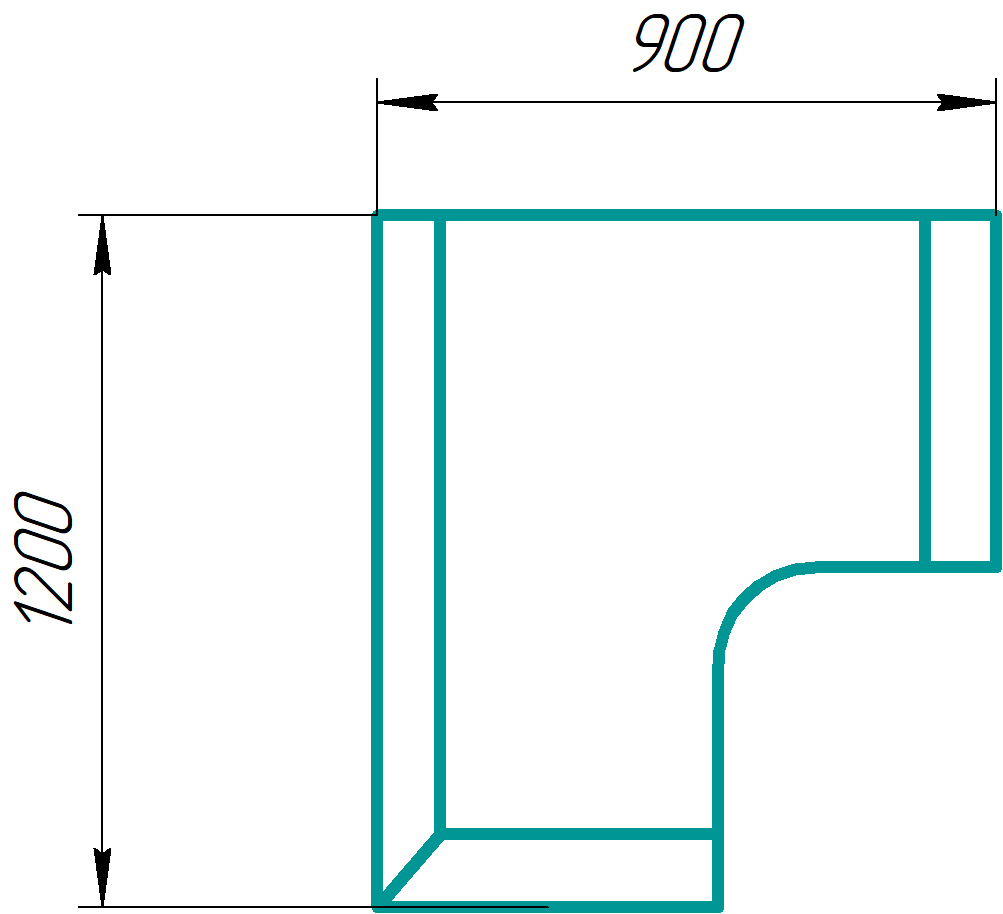
Рисунок 4 - Эскиз фигурной накладки
-
Установить накладку 5 в проектное положение, выдерживая технологические зазоры, и прихватить.
Длина прихваток 30-50 мм через 150-200 мм.
Электроды ф 3 мм, 1св=80-100 А
-
Зачистить сварные швы прихваток и прилегающие к ним поверхности шириной не менее 20 мм от шлака, брызг и наплывов металла. -
Приварить накладку швами Т1 6 ГОСТ 5264-80
Электроды ф 4 мм, 1св=110-130 А.
Технологические размеры сварки см. рисунки 5
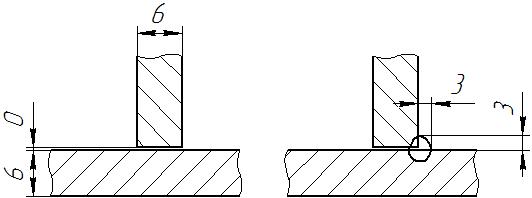
Рисунок. 5 Схема сварочного шва Т1
-
Контроль качества сварки
-
Контроль качества сварки осуществлять внешним осмотром.
Не допускается:
– поры в количестве более четырех на участке шва длиной 100 мм. (максимальный размер пор не более 1 мм).
Подрезы, трещины и прочие дефекты не допускаются.
8.4.2 Замена опорной части концевой балки
В результате многочисленных ремонтов произошло разрушение металлоконструкции концевой балки в зоне установки ходового колеса
-
Материалы, требования и их подготовка
-
Детали из стали марки ВСт3сп5 ГОСТ 14637-89 -
Качество материалов подтвердить сертификатами заводов-поставщиков. -
Электроды марки УОНИ 13-65 перед сваркой прокалить в сушильном шкафу Т-2500С, 1 час. Сварку и прихватку произвести на постоянном токе обратной полярности.
-
Подготовка и выполнение сварочных работ.
-
Прихватку и сварку производить сварщикам, аттестованным на право сварки грузоподъемных машин на малоуглеродистых и низколегированных сталях во всех пространственных положениях. -
Соблюдать правила безопасной работы при резке, монтаже, сварке согласно соответствующим инструкциям. -
Рабочие, работающие на высоте, должны пройти медицинское освидетельствование, проинструктированы по технике безопасности и особенностям работы.
-
Замена опорной части концевой балки.
-
Концевую балку в районе разрушения вывесить с помощью домкрата до образования зазора в 5 мм между ходовым колесом и рельсом. -
На подкрановой балке установить опорный столик из пластин и опустить концевую балку. -
Выкатить ходовое колесо. -
Отрезать поврежденный участок балки газовой резкой. С последующей правкой -
Удалить поясные швы на длину 60 мм от кромки реек вертикальной стенки. -
Изготовить новую часть нижнего пояса см. рисунок 6

К вновь изготовленной части нижнего пояса приварить подкладки швом Н1 4 размером 4 x 40 для формирования корня сварного шва. Электроды ф 4мм, 1св=110-130 А Технологические размеры сварки см. рисунки 7
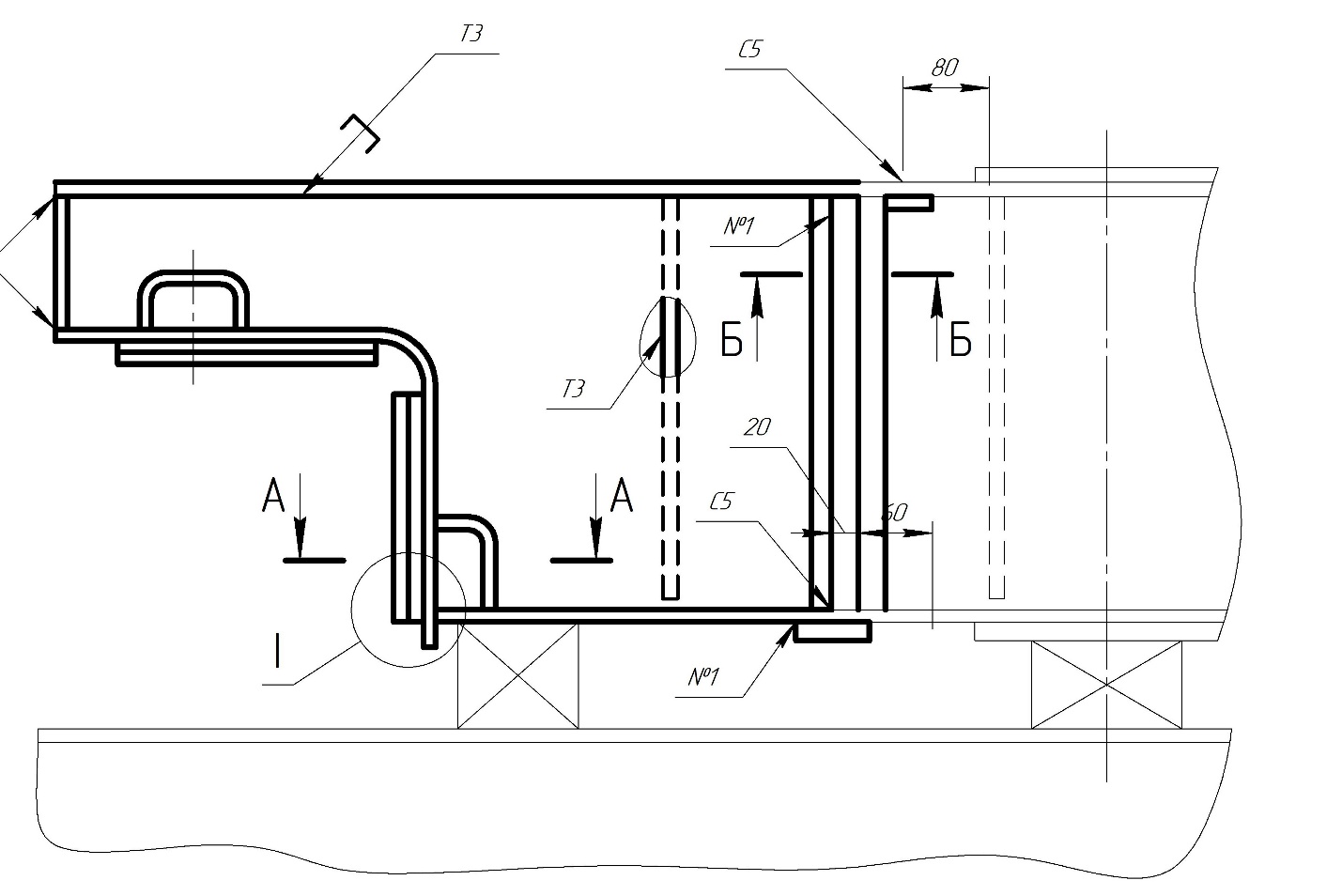
Рисунок 6 – схема новой части нижнего пояса

-
Приварить нижний пояс швом С5 6 Электроды ф 4мм, 1св=110-130 А Технологические размеры сварки см. рисунки 10 -
Установить под него второй опорный столик. -
Установить, выверить и прихватить верхнюю часть концевой балки. Длина прихваток 30-50 мм через 150-200 мм.
Электроды ф 3 мм, 1св=80-100 А;


-
Наложить швы соединения участков верхнего пояса швом С5 6 и швом Н1 6 Электроды ф 4мм, 1св=110-130 А Технологические размеры сварки см. рисунки 7 и 10 -
Наложить швы Т3 6 соединения вертикальных стенок Электроды ф 4мм, 1св=110-130 А. Технологические размеры сварки см. рисунки 8 -
Выполнить поясные швы Т3 6 соединения вертикальных стенок с нижним поясом; Электроды ф 4мм, 1св=110-130 А. Технологические размеры сварки см. рисунки 9 -
Выполнить верхний поясной шов Т3 6, удаленный при резке и не выполненный при изготовлении участка балки. Электроды ф 4мм, 1св=110-130 А. Технологические размеры сварки см. рисунки 9 -
Нижний пояс приварить к гнутому подбуксовому листу. Швами Т1 6 и Т2 8 Электроды ф 4мм, 1св=110-130 А; -
Зачистить сварные швы прилегающие к ним поверхности шириной не менее 20 мм от шлака, брызг и наплывов металла. -
Установить, выверить и закрепить ходовое колесо
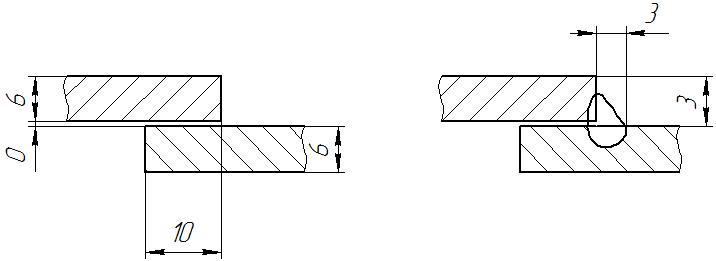
Рисунок 7 - Схема сварочного шва Н1

Рисунок 8 - Схема сварочного шва Т1
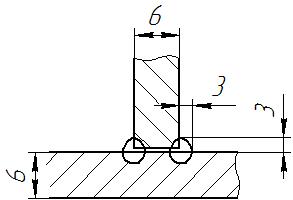
Рисунок 9 - Схема сварочного шва Т3
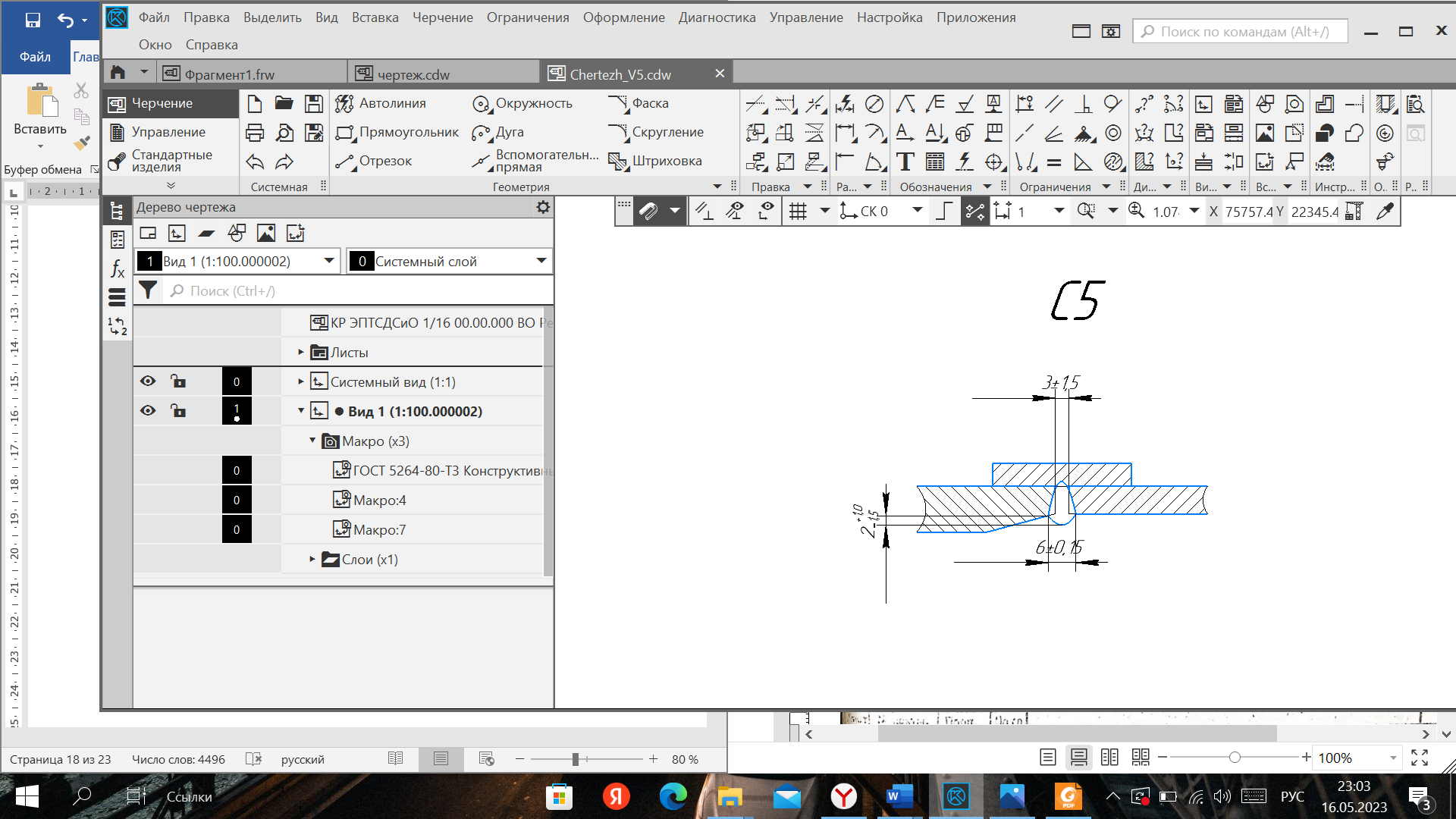
Рисунок 10 - Схема сварочного шва С5
-
Контроль качества сварки
-
Контроль качества сварки осуществлять внешним осмотром.
Не допускается:
– поры в количестве более четырех на участке шва длиной 100 мм. (максимальный размер пор не более 1 мм).
Подрезы, трещины и прочие дефекты не допускаются.
8.4.3 Замена опорной части концевой балки
В результате многочисленных аварий произошло разрушение металлоконструкции концевой балки в зоне установки ходового колеса
1.Материалы, требования и их подготовка
-
Детали из стали марки ВСт3сп5 ГОСТ 14637-89 -
Качество материалов подтвердить сертификатами заводов-поставщиков. -
Электроды марки УОНИ 13-65 перед сваркой прокалить в сушильном шкафу Т-2500С, 1 час. Сварку и прихватку произвести на постоянном токе обратной полярности.
-
Подготовка и выполнение сварочных работ.
-
Прихватку и сварку производить сварщикам, аттестованным на право сварки грузоподъемных машин на малоуглеродистых и низколегированных сталях во всех пространственных положениях. -
Соблюдать правила безопасной работы при резке, монтаже, сварке согласно соответствующим инструкциям. -
Рабочие, работающие на высоте, должны пройти медицинское освидетельствование, проинструктированы по технике безопасности и особенностям работы.
-
Замена опорной части концевой балки
-
С помощью шаблона вырезать по контору поврежденный участок газовой резкой. -
Поврежденное место опорной части разогреть пламенем резака до температуры 900-1100 0 С (от красного до оранжевого каления). Нагрев проводить интенсивно, путем плавного перемещения горелки вдоль нагреваемого участка, не допуская общих местных перегревов. После этого править молотком. -
Провести контроль правки струной и штангенциркулем. -
Зачистить края -
Подготовить изготовленную часть опорного узла концевой балки, собранного с ходовым колесом. См. Рисунок 11.