Файл: Разработка технологии изготовления детали Палец из порошковой легированной стали.docx
ВУЗ: Не указан
Категория: Не указан
Дисциплина: Не указана
Добавлен: 02.12.2023
Просмотров: 140
Скачиваний: 7
ВНИМАНИЕ! Если данный файл нарушает Ваши авторские права, то обязательно сообщите нам.
Министерство образования и науки Российской Федерации
Федеральное государственное бюджетное образовательное учреждение
высшего образования
«Поволжский государственный технологический университет»
(ФГБОУ ВО «ПГТУ»)
Институт механики и машиностроения
Направление подготовки
Материаловедение и технологии материалов
курсовоЙ проект на Тему:
«Разработка технологии изготовления детали «Палец» из порошковой легированной стали»
по дисциплине: Теория и технология процессов производства, обработки и переработки материалов и нанесения покрытий
Студент Губин Никита Андреевич
(Ф.И.О.)
Группа МТМ-41
Руководитель Крашенинникова Н.Г
(Должность, звание, Ф.И.О.)
Йошкар-Ола

Содержание
Введение……………………………………………………………………………….…………3
1. Теоретические сведения………………………………………………………..…………….7
1.1Классификация порошковых сталей…………………………………………..……………7
1.2 Материал ПК40Н2Д2М-68….………………………………………………………………8
1.3 Влияние легирующих элементов на свойства материала………………………..………..8
1.4 Методы получения порошков……………………………………………………………….9
1.5 Основные операции технологического процесса……………………………..………….11
2. Расчетная часть………………………………………………………………………..……..13
2.1. Расчет размеров технологической оснастки……………………………..………………13
2.2. Расчет навески…………………………………………………………………….……….15
2.3. Расчет усилия прессования и калибрования, выбор прессового оборудования………16
3. Технологическая часть……………………………………………………………..………..17
3,1. Операционная карта приготовления шихты……………………….…………………….17
3,2 Операционная карта прессования…………………………………………….…………..18
3,3. Операционная карта спекания………………………………………………….…………20
3,4. Операционная карта калибрования…………………………………………...…………..22
3,5. Дополнительная механическая доработка(нарезание резьбы)………………….………23
3.6. Выходной контроль………………………………………………………………………..24
3.7. Упаковка………………………………………………………………………………...….24
3.8. Расчет трудоемкости…………………………………………………………..…………..24
Заключение…………………………………………………………………………….……….26
Список используемой литературы………………………………………...…………………..27
Введение
Целью выполнения курсовой работы является разработка технологии изготовления детали «Палец» из порошковой легированной стали ПК40Н2Д2М-68
Задачами выполнения курсового проекта являются:
1. Обзор научно-технической литературы, касающейся заданного класса порошковых материалов, с указанием типовых составов, структур, уровня достигнутых физико-механических и эксплуатационных характеристик и областей применения.
2. Анализ технических требований к детали; разработка эскиза порошковой заготовки с учетом конструкционных требований к порошковым изделиям и материалу детали; выбор и обоснование технологической схемы изготовления изделия.
3. Выполнение необходимых расчетов:
- расчет усилия прессования, а, в случае необходимости, – и калибрования изделия, выбор прессового оборудования;
- расчет размеров формообразующих элементов пресс-формы для прессования и, при необходимости, калибрования.
4. Разработка схемы прессования изделия.
5. Разработка технологического процесса изготовления детали: описание технологии изготовления, выбор технологического оборудования, расчет необходимых технологических параметров, разработка технологических карт основных операций, определение объема и методов контроля.
6. Расчет трудоемкости изготовления детали.
Тема порошковой металлургии особенно актуальна в наши дни. Порошковой металлургией называют область техники, охватывающую совокупность методов изготовления порошков металлов и металлоподобных соединений, полуфабрикатов и изделий из них или их смесей с неметаллическими порошками без расплавления основного компонента.
Из имеющихся разнообразных способов обработки металлов порошковая металлургия занимает особое место, так как позволяет получать не только изделия различных форм и назначений, но и создавать принципиально новые материалы, которые другим путем получить или очень трудно или невозможно. У таких материалов можно получить уникальные свойства, а в ряде случаев существенно повысить экономические показатели производства. При этом способе в большинстве случаев коэффициент использования материала составляет около 100%.
Порошковая металлургия находит широчайшее применение для различных условий работы деталей изделий. Методами порошковой металлургии изготовляют изделия, имеющие специальные свойства: антифрикционные детали узлом трения приборов и машин (втулки, вкладыши, опорные шайбы и т.д.), конструкционные детали (шестерни, кулачки и др.), фрикционные детали (диски, колодки и др.), инструментальные материалы (резцы, пластины резцов, сверла и др.), электротехнические детали (контакты, магниты, ферриты, электрощетки и др.) для электронной и радиотехнической промышленности, композиционные (жаропрочные и др.) материалы.
Основные преимущества использования порошковой металлургии:
- снижает затраты на дальнейшую механическую обработку, которая может быть исключена или существенно уменьшена. Получает готовое изделие точное по форме и размерам. Обеспечивает высокое качество поверхности изделия.
- использует энерго и ресурсосберегающие технологии. Уменьшает количество операций в технологической цепи изготовления продукта. Использует более чем 97% стартового сырья. Реализует многие последующие сборочные этапы ещё на стадии спекания.
- позволяет получать изделия с уникальными свойствами, используя многокомпонентные смеси, объединяя металлические и не металлические компоненты. Изделия различной пористости (фильтры) с регулируемой проницаемостью; Подшипники скольжения с эффектом самосмазывания.
- получает более высокие экономические, технические и эксплуатационные характеристики изделий по сравнению с традиционными технологиями.
- упрощает зачастую изготовление изделий сложной формы.
- обеспечивает прецизионное производство. Соответствие размеров в серии изделий.
Основным документом, регламентирующим марки и свойства применяемых в России конструкционных материалов на основе железа, является ГОСТ 28378-89. Согласно этому нормативному документу, все материалы на основе железа делятся на:
• стали малоуглеродистые, углеродистые и медистые;
• стали никельмолибденовые, медьникелевые, медьникельмолибденовые;
• стали хромистые, марганцовистые, хромникельмарганцовистые;
• стали нержавеющие, предназначенные для деталей, применяемых в различных отраслях техники.
Исходные данные курсового проекта
1)ПК40Н2Д2М-68(порошковый конструкционный материал С-0.4%;Ni-2%;Cu-2%;Mo-1% p=6,4 г/см^2) Vизд=5191+1179-807-157*2=5249мм^2
2)Упругие последействия, %:
-при прессовании
D | d | h |
0.3 | 0.1 | 0.4 |
-при калибровке
D | d | h |
0.4 | 0.2 | 0.5 |
3)Рост при спекании, %:
D | d | h |
0,4 | 0.1 | 0.5 |
4)Изменение размеров при оксидировании-0.01мм(максимум)
5)Осадка при калибровке 1-3%(2%)
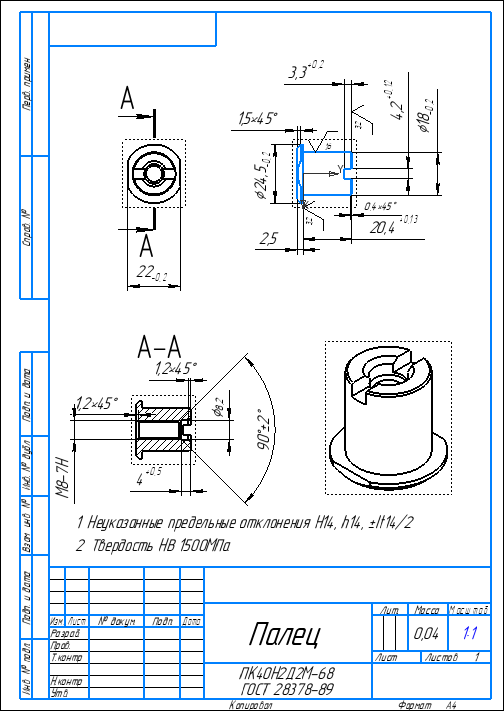
1.Теоретические сведения.
Конструкционные порошковые стали – это спеченные материалы, используемые для замены литых и кованых сталей при изготовлении деталей машин и приборов методами порошковой металлургии. Условное обозначение таких материалов состоит из букв и цифр, например: сталь порошковая конструкционная медьникелевая со средней массовой долей углерода 0,4 %, никеля 2 %, меди 2 % и минимальной плотностью 6400 кг/м3 в соответствии с ГОСТ 28378-89 будет иметь следующее обозначение: ПК40Н2Д2-64.Основным документом, регламентирующим марки и свойства применяемых в России конструкционных материалов на основе железа, является ГОСТ 28378-89. Согласно этому нормативному документу, все материалы на основе железа делятся на:
· стали малоуглеродистые, углеродистые и медистые;
· стали никельмолибденовые, медьникелевые, медьникельмолибденовые;
· стали хромистые, марганцовистые, хромникельмарганцовистые;
· стали нержавеющие, предназначенные для деталей, применяемых в различных отраслях техники.
1.1Классификация порошковых сталей
Классификация порошковых сталей подчиняется тем же правилам, что и принятым для сталей традиционных методов получения.
Основой порошковых сталей служит железо, свойства которого при спекании оказывают большое влияние на формирование структуры и свойств стали.
В связи с низкой прочностью и твердостью спеченного железа, для повышения его механических свойств в железный порошок при приготовлении порошковой смеси вводят легирующие добавки (фосфор, медь, хром, никель, молибден)
В зависимости от химического состава стали подразделяются на простые углеродистые и легированные.
В простых углеродистых сталях помимо углерода, содержание которого колеблется от 0,08 до 1,7%, могут находиться элементы, наличие которых обусловлено либо особенностями технологического процесса (марганца до 0,7%, кремния до 0,5%), либо невозможностью их полного удаления из металла (серы до 0,04%, фосфора до 0,05%, кислорода, азота, водорода). Кроме того, в углеродистой стали могут встречаться случайные примеси (хром, никель, медь и др.).
Легированной называется сталь, для получения требуемых свойств которой в ее состав вводятся специальные легирующие элементы.
В зависимости от назначения порошковые стали делятся на конструкционные общего машино- и приборостроительного назначения, высокопрочные, нержавеющие, инструментальные, а также специальные.
По равновесной структуре порошковые стали классифицируются на доэвтектоидные, имеющие в структуре избыточный феррит; эвтектоидные с перлитной структурой; заэвтектоидные, содержащие в перлитной структуре избыточные (вторичные) карбиды, и ледебуритные, имеющие в структуре первичные карбиды, которые выделились из жидкой фазы, например при распылении. В зависимости от структуры, получаемой после нагрева выше точек Ас3 и охлаждения на спокойном воздухе, стали могут быть подразделены на перлитные, мартенситные и аустенитные.
Стали перлитного класса характеризуются относительно малым содержанием легирующих элементов, мартенситного – более значительным, а аустенитного класса — высоким содержанием легирующих элементов.
Кроме приведенной классификации порошковые стали необходимо разделять по пористости и технологии их производства. В зависимости от объемного содержания пор порошковые стали подразделяются на непроницаемые (пор менее 5-8%), полупроницаемые (пор 8-14%) и проницаемые (пор более 12-14%).
В зависимости от технологий производства их можно подразделить на однократно и многократно прессованные в условиях статических нагрузок в закрытых пресс-формах при обычных и высоких температурах; стали, полученные при совмещении холодного прессования и спекания высокопористых заготовок с последующим динамическим горячим прессованием или горячей штамповкой; стали, полученные экструзией, прокаткой, взрывным прессованием.
1.2 Материал ПК40Н2Д2М-68
Материал ПК40Н2Д2М-68-порошковый конструкционный материал С-0.4%;Ni-2%;Cu-2%;Mo-1% p=6,4 г/см^2. Он относится к группе Порошковых конструкционных материалов на основе железа. Область применения – изделия пористые нагруженные.
У данного материала существует два подвида ПК40Н2Д2М-6.8 и ПК40Н2Д2М-7.4 они отличаются только разной плотностью
Свойства материала ПК40Н2Д2М:
-Плотность 6.8-7.4 г/см ³. .
-Твердость НВ 1500-1800 Мпа.
-Временное сопротивление при растяжении 440-780 Мпа.
-Относительное удлинение 3-6 %
Известен способ получения порошков легированных сплавов путем диффузионного насыщения порошка основного металла или сплава легируюш,ими элементами из газовой фазы в присутствии хлористого аммония при температуре 1050-11-50 С.
1.3 Влияние легирующих элементов на свойства материала
Медь: • увеличивает предел текучести и временное сопротивление материала за счет эффекта дисперсионного твердения, образуя с железом твердый раствор с предельной растворимостью 8%. При этом несколько снижается его пластичность и вязкость. Максимальная прочность на растяжение достигается при массовой доле меди 5–7 %.
• повышает сопротивляемость порошкового материала атмосферной коррозии.
• активирует процесс спекания, поскольку температура спекания порошковых сталей обычно превышает температуру плавления меди (1083 оС).
• При содержании в стали до 1 % меди она способствует усадке при спекании, при дальнейшем повышении ее концентрации наблюдается рост спеченного изделия.
Никель • Повышает механические свойства материала, что связано как с повышением прочности феррита, так и с благоприятным воздействием никеля на состояние межчастичных границ.
• Способствует «рассасыванию» межчастичных границ, увеличению протяженности металлического контакта, повышает усадку и плотность изделий.
• При спекании вызывает большую усадку, поэтому при одновременном легировании медью и никелем возможно получение безусадочньх изделий. Наиболее благоприятное сочетание прочности и пластичности наблюдается в сплавах содержащих от 1 до 5 % каждого из этих элементов.
Молибден: • повышает прокаливаемость,
• снижает склонность к росту зерна при нагреве,
• повышает устойчивость к отпуску. В порошковые стали вводится в количестве (0,2–1,0) % в составе порошков, полученных распылением и другими методами, реже в виде чистого порошка молибдена. Чаще вводится вместе с никелем и другими легирующими элементами. Лучшими свойствами обладают стали, содержащие 1- +3 % никеля 0,25-1 % молибдена, 0,4-0,8 % углерода.
1.4 Методы получения порошков
К основным механическим методам получения порошков относятся:
1. Дробление и размол твердых материалов. Измельчение стружки, обрезков и компактных материалов проводят в шаровых, вихревых, молотковых и других мельницах, к.п.д. которых сравнительно невелик. Получают порошки Fe, Cu, Mn, латуни, бронзы, хрома, алюминия, сталей.
2. Диспергирование расплава. Струю расплавленного металла диспергируют механическим способом (воздействием центробежных сил и др.) или действуя на нее потоком энергоносителя (газа или жидкости). Получают порошки алюминия, свинца, цинка, бронзы, латуни, железа, чугуна, стали.
3. Грануляция расплава. Порошок образуется при сливании расплавленного металла в жидкость (например, в воду). Получают крупные порошки железа, меди, свинца, олова, цинка.
Диспергирование расплавленного металла или сплава струей сжатого газа, жидкости или механическим способом позволяет получать порошки, называемые распыленными. Процесс характеризуется высокими производительностью, технологичностью, степенью автоматизации и сравнительно малыми энергозатратами, экологически чистый. Промышленное производство порошков в нашей стране составляет в соотношении 4-5 : 1 в пользу распыленных порошков.
В настоящее время метод распыления широко используют для получения не только порошков железа, сталей и других сплавов на основе железа, но и порошков алюминия, меди, свинца, цинка, тугоплавких металлов (титана, вольфрама и др.), а также сплавов на основе этих цветных металлов. Распыление весьма эффективно при получении порошков многокомпонентных сплавов и обеспечивает объемную равномерность химического состава, оптимальное строение и тонкую структуру каждой образующейся частицы. Это связано с перегревом расплава перед диспергированием, что приводит к высокой степени его однородности на атомарном уровне из-за полного разрушения наследственной структуры твердого состояния и интенсивного перемешивания, и кристаллизацией дисперсных частиц с высокими скоростями охлаждения – от 103 – 104 до нескольких десятков и даже сотен миллионов градусов в секунду.
Методы распыления металлического расплава различаются по виду затрачиваемой энергии (нагрев индукционный или косвенный, электродуговой, электронный, лазерный, плазменный и др.), виду силового воздействия на расплав при диспергировании (механическое воздействие, энергия газовых и водяных потоков, силы гравитационные, центробежные, воздействия ультразвука и т.д.) и по типу среды для его создания и диспергирования (восстановительная, окислительная, инертная или какая-либо иная среда заданного состава, вакуум).
Сущность получения металлических порошков из расплава заключается в нарушении сплошности его потока (струи или пленки) под действием различных источников возмущений с возникновением дисперсных частиц.
Центробежное распыление представляет собой один из основных видов диспергирования расплава. По методу вращающегося электрода распыление происходит в момент формирования расплава. Образовавшаяся на торце расходуемого электрода, вращающегося со скоростью 2000-20000 об/мин, пленка расплава толщиной 10-30 мкм под действием центробежных сил перемещается к его периферии и срывается с его кромки в виде частиц-капель преимущественно размером 100-200 мкм (увеличение диаметра расходуемого электрода и скорости его вращения приводит к уменьшению размера частиц-капель) Кристаллизация капель со скоростью охлаждения порядка 104°С/сек происходит в атмосфере инертного газа.
При других схемах диспергирования плавление металла проводят автономно, вне зоны распыления. Когда струю расплава подают на вращающийся со скоростью до 24000 об/мин диск, на его вогнутой поверхности образуется пленка жидкого металла, от которой затем отрываются капли-частицы преимущественно размером <100 мкм и кристаллизуются в атмосфере инертного газа со скоростью 105 – 106 °С/сек.
В последнее время активно развиваются методы распыления расплавов, обеспечивающие очень высокие скорости охлаждения частиц. Один из вариантов, обеспечивающий затвердевание жидкой капли со скоростью 107 – 108 °С/с, позволяет получать так называемые РИБЗ – (распыленные и быстрозакаленные порошки), когда на пути летящей капли устанавливают охлаждаемый экран под углом 15-45° к направлению ее движения; при ударе об экран капля перемещается по его поверхности и последовательно кристаллизуется в виде частицы пластинчатой формы.
На установке для сверхбыстрого охлаждения в вакууме или инертном газе капли расплава выдуваются аргоном из отверстия в графитовом тигле, находящемся в трубчатой индукционной печи, и попадают на медный крылообразный кристаллизатор, вращающийся со скоростью до 104 об/мин (встречная скорость движения капли и кристаллизатора до 500 м/с).
Высокоскоростное затвердевание расплава обеспечивает извлечение малых объемов металла кромкой быстровращающегося (2000-5000 об/мин) в вертикальной плоскости диска из высокотеплопроводного материала. При контакте с расплавом на кромке диска затвердевает некоторый слой металла, затем он выходит из расплава и охлаждается, после чего частица отделяется от кромки диска (скорость охлаждения 106-108 °С/с).
В любом случае методы распыления при кристаллизации капли расплава со скоростью более 106 °С/с приводят к получению порошков, частицы которых имеют аморфную структуру, придающую им чрезвычайно специфические свойства, позволяющие создавать уникальные материалы для различных отраслей техники.
100>
1.5 Операции технологического процесса
Технологические процессы порошковой металлургии включают следующие операции.
1. Приготовление шихты и дозировка. Порошки различных компонентов смешивают при помощи смесителя( в нашем случае будет использован двухконусный смеситель на 100кг)
2. Формование в стальных пресс-формах применяют для мелких деталей. Для изготовления крупных изделий из тугоплавких металлов (труб, стержней) применяют гидростатическое прессование. Для получения листов, полос и лент применяют прокатку. На обычных же прессах возможно прессование только простых по форме деталей. Специальные прессы применяются для изготовления сложных изделий; они имеют до 4-6 независимых рабочих перемещений.
3.Механическая доработка позволяет получить на изделии сложные фасонные элементы, невозможные для прессования (резьба).
4.Спеканиетехнологический процесс получения твердых и пористых материалов (изделий) из мелких порошкообразных или пылевидных материалов при повышенных температурах; часто при спекании меняются физико-химические свойства и структура материала.
Спекание обеспечивает сцепление частиц порошка вследствие диффузии атомов. Спекание производят при температуре примерно равной (0,65-0,79) t пл основного компонента сплава в водородных,в защитных средах эндогаза или вакуумных печах для защиты от окисления.
5. Горячее прессование заключается в одновременном прессовании и спекании, что сокращает время операции в 20-30 раз. Оно выполняется при меньшей температуре. Но недостатком этого процесса является низкая стойкость дорогих пресс-форм. Например, графитовые пресс-формы выдерживают 3-5 прессовок при температуре 1500°С.
6. Калибрование. При обычном процессе порошковой металлургии можно получить детали сравнительно невысокой точности 10-12 кв и шероховатостью RZ=20-10 мкм. Для повышения точности таких деталей выполняют калибрование в специальных пресс-формах при давлении до 100кПа и при условии достаточной пластичности материала. При этом точность размеров повышается до 8-9кв и RA 2,5-6,3мкм.
Каждая из указанных операций вносит свой важный вклад в формирование всех свойств конечных порошковых изделий.
В своей работе я буду использовать следующий порядок технологического процесса:
1.Подготовительные операции:
-смешивание компонентов нужного нам состава
2.Прессование
3.Спекание
4.калибрование
5.Механическая доработка(нарезание резьбы М8)
6.Выходной контроль
7.Упаковка
2.Расчетная часть
2.1.Расчет размеров технологической оснастки.
| D | D | D | d | d | d | h | h | h | h |
Размер по чертежу | ![]() | ![]() | ![]() | ![]() | ![]() | ![]() | ![]() | ![]() | ![]() | ![]() |
В калибровочной П\Ф | ![]() | ![]() | ![]() | ![]() | ![]() | ![]() | ![]() | ![]() | ![]() | ![]() |
После спекания | ![]() | ![]() | ![]() | ![]() | ![]() | ![]() | ![]() | ![]() | ![]() | ![]() |
В прессовке | ![]() | ![]() | ![]() | ![]() | ![]() | ![]() | ![]() | ![]() | ![]() | ![]() |
В прессовочной П\Ф | ![]() | ![]() | ![]() | ![]() | ![]() | ![]() | ![]() | ![]() | ![]() | ![]() |






























Расчет высоты матрицы:
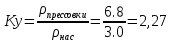


2.2Расчет навески
Масса навески рассчитывается по формуле: m = Vρ к1к2,
где V – объем готовой заготовки=5,249 см^3
ρ – плотность изделия;
к1 = 1,01);
к2 = 1,02.
M = 5.249 cм 3*6,8 г/см3 * 1,01 * 1,02 = 36.77 г
ОПЕРАЦИОННАЯ КАРТА ПРИГОТОВЛЕНИЯ ШИХТЫ
Шифр детали | Название детали | Марка материала ПК40Н2Д2М-6.8 |
Компоненты шихты | Масса, кг, (на 100 кг шихты) | Содержание, % |
Порошок железа ПЖР3.200.28 ГОСТ 9849-86 | 94,9 | Основа |
Порошок меди ПМС-1 ГОСТ 4960-75 | 2 | 1-3 |
Порошок никеля ПНЭ-1 ГОСТ 9722-97 | 2 | 1-3 |
Графит ГК-1 | 0,6 | 0,4 |
Порошок молибдена | 0,5 | 0,3-0,7 |
Стеарат цинка ТУ 6-09-17- 316-96 – 0,8 кг. | 0,8 | 0,8(сверх 100кг) |
Продолжительность смешивания: 45

Оборудование: смеситель двухконусный на 100 кг
Контролируемые параметры
1. Равномерность смешивания: шихта должна быть однородной, без включений и комков, видимых невооруженным глазом.
2. Насыпная плотность: нас. = (2,8+0,1) г/см3
2.3Расчет усилия прессования и калибрования, выбор прессового оборудования
Максимальная площадь сечения Smax= 3.14 (24,5^2 -6.7^2 ) /4= 436 мм2
Ориентировочная плотность прессовки – 6,7 г/см3 .
С учетом данных справочной таблицы 1, давление прессования, обеспечивающее получение такой плотности, составляет 700 Мпа.
Следовательно, усилие прессования: Р = р Smax =700*10^6*436*10^-6= 305.2 кН
Принимая коэффициент запаса к = 1,25, получаем усилие пресса
Рпр. = 1,25*305.2 = 381.5 кН (38.15 т).
Для прессования детали выберем Пресс-автомат ТРА 50 (усилие 50 т)
Усилие калибрования:
Р = р Smax =300*10^6*436*10^-6= 130.8 кН
С учетом коэффициента запаса к = 1,25, получаем усилие калибровочного пресса
Ркал. = 1,25*130.8 = 163.5 кН (16.35 т).