Файл: Разработка технологии изготовления детали Палец из порошковой легированной стали.docx
ВУЗ: Не указан
Категория: Не указан
Дисциплина: Не указана
Добавлен: 02.12.2023
Просмотров: 142
Скачиваний: 7
ВНИМАНИЕ! Если данный файл нарушает Ваши авторские права, то обязательно сообщите нам.
Для калибрования детали выберем Пресс калибровочный ДК 30 (усилие 30 т)
Масса навески рассчитывается по формуле: m = Vρ к1к2,
где V – объем готовой заготовки=5,249 см^3
ρ – плотность изделия;
к1 = 1,01);
к2 = 1,02.
M = 5.249 cм 3*6,8 г/см3 * 1,01 * 1,02 = 36.77 г
3.Технологическая часть
3.1ОПЕРАЦИОННАЯ КАРТА ПРИГОТОВЛЕНИЯ ШИХТЫ
Шифр детали | Название детали | Марка материала ПК40Н2Д2М-6.8 |
Компоненты шихты | Масса, кг, (на 100 кг шихты) | Содержание, % |
Порошок железа ПЖР3.200.28 ГОСТ 9849-86 | 94,9 | Основа |
Порошок меди ПМС-1 ГОСТ 4960-75 | 2 | 1-3 |
Порошок никеля ПНЭ-1 ГОСТ 9722-97 | 2 | 1-3 |
Графит ГК-1 | 0,6 | 0,4 |
Порошок молибдена | 0,5 | 0,3-0,7 |
Стеарат цинка ТУ 6-09-17- 316-96 – 0,8 кг. | 0,8 | 0,8(сверх 100кг) |
Продолжительность смешивания: 45

Оборудование: смеситель двухконусный на 100 кг
Контролируемые параметры
1. Равномерность смешивания: шихта должна быть однородной, без включений и комков, видимых невооруженным глазом.
2. Насыпная плотность: нас. = (2,8+0,1) г/см3
3.2ОПЕРАЦИОННАЯ КАРТА ПРЕССОВАНИЯ
Эскиз порошковой заготовки
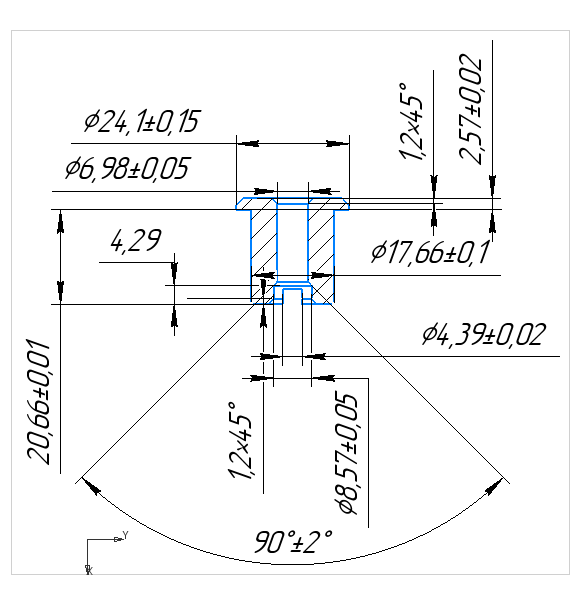
Марка материала: ПК40Н2Д2М-68 ГОСТ 28378-89
Пресс-форма:
Пресс: ТРА 50
Усилие прессования: 38,15Т
Контролируемые параметры
Контролируемый параметр | Средство контроля | Периодичность контроля и объем контроля |
Геометрические параметры: ![]() ![]() ![]() ![]() ![]() ![]() ![]() ![]() ![]() ![]() ![]() ![]() | Микрометр МК 0-25 ГОСТ 6507-90 Микрометр МК 0-25 ГОСТ 6507-90 Микрометр МК 0-25 ГОСТ 6507-90 Штангенциркуль ШЦЦ 1- 125-001 ГОСТ166-89 Штангенциркуль ШЦЦ 1- 125-001 ГОСТ166-89 Штангенциркуль ШЦЦ 1- 125-001 ГОСТ166-89 Индикатор ИЧ10 ГОСТ 577- 68 Индикатор ИЧ10 ГОСТ 577- 68 Индикатор ИЧ10 ГОСТ 577- 68 Индикатор ИЧ25 ГОСТ 577-68 | 2 раза в смену и при замене оснастки на 3-5 деталях 2 раза в смену и при замене оснастки на 3-5 деталях 2 раза в смену и при замене оснастки на 3-5 деталях Через 50 ходов пресса на 3-5 деталях Через 50 ходов пресса на 3-5 деталях Через 50 ходов пресса на 3-5 деталях Через 50 ходов пресса на 3-5 деталях Через 50 ходов пресса на 3-5 деталях Через 50 ходов пресса на 3-5 деталях Через 50 ходов пресса на 3-5 деталях |
Масса прессовки (36,77+0,5) г | Весы EWEW00-2 | Через 50 ходов пресса на 3-5 деталях |
Плотность 6,7±0,1 г/см | Весы гидростатические GХ1000 | 2-3 детали от партии Лаборатория |
Внешний вид: не допускаются сколы, трещины, набросы порошка на поверхности детали | Визуально | постоянно |
3.3ОПЕРАЦИОННАЯ КАРТА СПЕКАНИЯ
Эскиз порошковой заготовки
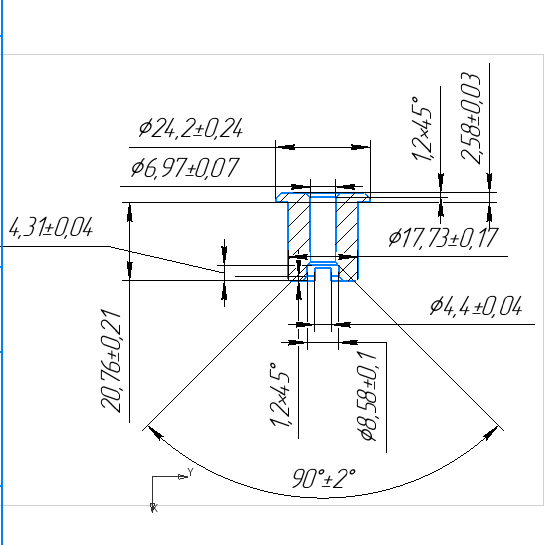
Деталь: палец
Материал: ПК40Н2Д2М-68 ГОСТ 28378-89
Среда спекания: эндогаз
Оборудование | Режим спекания |
Печь конвейерная для спекания в среде эндогаза Cremer CBS200-115/e Печь конвейерная для спекания в среде эндогаза Cremer CBS100-115/e Печь конвейерная для спекания в среде эндогаза Антарес-М | Зона нагрева– 650±5˚С, Зона спекания – 1120±5˚С, Зона охлаждения – 900±5 оС Скорость ленты 50 мм/мин. |
Способ укладки заготовок | |
Детали укладывать на ленту в 1 слой. Расстояние между деталями не менее 3 мм, от края не менее 5 мм. |
Контролируемые параметры
Контролируемый параметр | Средство контроля | Периодичность и объем контроля |
Внешний вид На поверхности деталей не допускаются наличие вспучиваний, оплавлений, сажистого налета | визуально | 4 раза в смену на 10 деталях |
Микроструктура на соответствие ГОСТ 28378- 89 | Микроскоп MICRODUROMAT 400 | 2 детали от партии Лаборатория |
Геометрические параметры: ![]() ![]() ![]() ![]() ![]() ![]() ![]() ![]() ![]() ![]() ![]() ![]() | Микрометр МК 0-25 ГОСТ 6507-90 Микрометр МК 0-25 ГОСТ 6507-90 Микрометр МК 0-25 ГОСТ 6507-90 Штангенциркуль ШЦЦ 1- 125-001 ГОСТ166-89 Штангенциркуль ШЦЦ 1- 125-001 ГОСТ166-89 Штангенциркуль ШЦЦ 1- 125-001 ГОСТ166-89 Индикатор ИЧ10 ГОСТ 577- 68 Индикатор ИЧ10 ГОСТ 577- 68 Индикатор ИЧ10 ГОСТ 577- 68 Индикатор ИЧ25 ГОСТ 577-68 | 2 раза в смену на 3-5 деталях 2 раза в смену на 3-5 деталях 2 раза в смену на 3-5 деталях 2 раза в смену на 3-5 деталях 2 раза в смену на 3-5 деталях 2 раза в смену на 3-5 деталях 2 раза в смену на 3-5 деталях 2 раза в смену на 3-5 деталях 2 раза в смену на 3-5 деталях 2 раза в смену на 3-5 деталях |
3.4ОПЕРАЦИОННАЯ КАРТА КАЛИБРОВАНИЯ
Эскиз порошковой заготовки
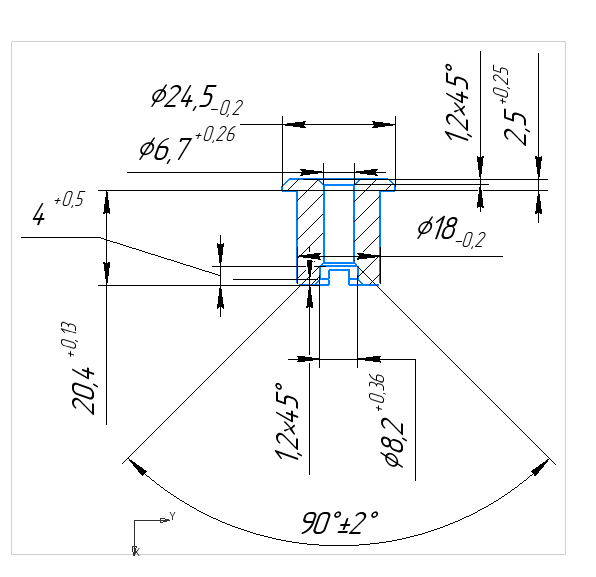
Пресс-форма:
Пресс: ДК 30
Усилие калибрования: 16,35 т
Контролируемые параметры
Контролируемый параметр | Средство контроля | Периодичность и объем контроля |
Геометрические параметры: ![]() ![]() ![]() ![]() ![]() ![]() ![]() | Калибр-скоба Калибр-скоба Калибр-пробка Калибр-пробка Индикатор ИЧ10 ГОСТ 577- 68 Индикатор ИЧ10 ГОСТ 577- 68 Штангенциркуль ШЦ 1 | Через 10 минут работы пресса на 3-5 деталях Через 10 минут работы пресса на 3-5 деталях Через 10 минут работы пресса на 3-5 деталях Через 10 минут работы пресса на 3-5 деталях Через 10 минут работы пресса на 3-5 деталях Через 10 минут работы пресса на 3-5 деталях Через 10 минут работы пресса на 3-5 деталях |
Плотность 6,8+0,1 г/см | Весы гидростатические GХ1000 | 2-3 детали от партии Лаборатория |
Внешний вид На поверхности деталей не допускаются наличие вспучиваний, оплавлений, сажистого налета | визуально | 4 раза в смену на 10 деталях |
Микроструктура на соответствие ГОСТ 28378- 89 | Микроскоп MICRODUROMAT 400 | 2 детали от партии Лаборатория |
3.5.Дополнительная механическая доработка.
Необходимо нарезать резьбу М8 на глубину 18.9 мм в отверстии диаметром 6.7 мм
3.6Выходной контроль
Контролируемый параметр | Средство контроля | Периодичность и объем контроля |
Геометрические параметры: ![]() ![]() ![]() ![]() ![]() ![]() ![]() | Калибр-скоба Калибр-скоба Калибр-пробка Калибр-пробка Индикатор ИЧ10 ГОСТ 577- 68 Индикатор ИЧ10 ГОСТ 577- 68 Штангенциркуль ШЦ 1 | 20 детали от партии |
Плотность 6,8+0,1 г/см | Весы гидростатические GХ1000 | |
Внешний вид На поверхности деталей не допускаются наличие вспучиваний, оплавлений, сажистого налета | визуально | |
Микроструктура на соответствие ГОСТ 28378- 89 | Микроскоп MICRODUROMAT 400 |
3.7 Упаковка
Детали упаковать по технологической инструкции…
3.8.Расчет трудоемкости.
1.Приготовление шихты:

Н1=60кг/час
2.Прессование:


Число ходов=5

3.Спекание



4.Калибрование:


Число ходов=20

5.Дополнительная механическая доработка(нарезание резьбы)
Т5=0.003
6.Упаковка:


Н6=80кг/час
7.Контроль:

8.Полная трудоемкость

Заключение
В ходе выполнения КП были выполнены следующие задачи:
1. Обзор научно-технической литературы, касающейся заданного класса порошковых материалов, с указанием типовых составов, структур, уровня достигнутых физико-механических и эксплуатационных характеристик и областей применения.
2. Анализ технических требований к детали; разработка эскиза порошковой заготовки с учетом конструкционных требований к порошковым изделиям и материалу детали; выбор и обоснование технологической схемы изготовления изделия.
3. Выполнение необходимых расчетов:
- расчет усилия прессования, и калибрования изделия, выбор прессового оборудования;