Файл: Задача Аналитический обзор оборудования и его узлов Общее описание агрегатов и его характеристика.docx
Добавлен: 03.12.2023
Просмотров: 63
Скачиваний: 1
ВНИМАНИЕ! Если данный файл нарушает Ваши авторские права, то обязательно сообщите нам.
- Снижения риска возникновения «усталости» металла.
Широкое распространение получили двухкамерные дробеструйные аппараты модели 334М, изготовляемые Усманским механическим заводом. Конструкция аппарата обеспечивает возможность одновременной работы двумя соплами.
В процессе поступления абразива, на поверхности предмета формируется слой с высоким сжимающим напряжением. Изделие после дробеметной обработки надежно защищено от зарождения трещин, сколов, коррозийных зарождений, механического растрескивания и других повреждений металла.
Имеется возможность выбора как стандартных дробеструйных установок, так и их разработка и монтаж под конкретные особенности выполняемой работы. В последнем случае возможна оптимизации работы такого оборудования под нужды заказчика. Можно подобрать обитаемые и необитаемые установки, а также камеры дробеструйной обработки, которые функционируют в автоматическом или полуавтоматическом режиме. Только лишь правильно подобрав конкретную линию дробеструйной очистки и грамотно её смонтировав, можно в последующем обеспечить эффективность обработки металлических изделий, сократив издержки на проведение таких работ.
Несмотря на то, что чугунная дробь хорошо справляется с очисткой поверхностей от ржавчины или окалины, она не может в полном объеме удалять такие загрязнения, как мясные пятна, клейкие агломераты, плотные наслоения. Для этих целей применяют стальную дробь, которая может использоваться многократно при помощи автоматических систем сбора и рекуперации абразива.
Сферы применения: трубопрокатная промышленность, машиностроение, литейные производства, сборочные цеха.Проходные установки дробеструйной обработки представляют собой целый комплекс собранного в единую систему оборудования, которое обеспечивает автоматизацию очистки металлических изделий. Используемые линии различаются своей производительностью, габаритами, соответственно их можно использовать для работы с крупными по размерам металлоконструкциями.
Также распространение получили дробеструйные установки, которые имеют подвесной транспортер. Использование таких комплексов позволяет автоматизировать процесс дробеструйной обработки металлоконструкций, в которых очищаемые изделия передвигаются на специальной линии транспортера. Размеры таких установок, а также их назначение могут существенно различаться.
В дробеструйных установках часто используется специальная система, которая позволяет выполнять сбор и последующую рекуперацию используемого абразива. В подобном случае используются специальные скребковые полы, конструкция которых подбирается в зависимости от особенностей используемого дробеструйного оборудования и конкретных линий очистки. Собранные абразивные материалы очищаются с помощью воздушного сепаратора или специальных фильтров, после чего вновь используются в работе для обработки металлических изделий.
Современные модели оснащаются камерой, стенки которой изготовлены из высокопрочных марок стали или металлических сплавов с упрочнением из армированной резины или других материалов. Производительность по выбросу дроби может составлять до 1000 кг в минуту и выше.
Стандартная комплектация установок включает:
- Камеры очистки,
- Системы вентиляции,
- Рольганги подающие и принимающие,
- Щеточно-сдувная система
- Системы рециркуляции дроби,
- Воздуховоды,
- Камеры очистки воздуха,
- Системы метания дроби,
- Системы управления.
Дробемётная обработка изделий подразделяется по типам дробеметных установок с возможностью вращения,проходного,транспортного, ленточного, барабанного и камерного типов.
Обработка изделий в рабочей камере цилиндрической формы выполняется за счет непрерывной подачи воздушной струи с дробью на очищаемые предметы. При этом изделия сдвигаются и перемешиваются как в барабане стиральной машины, за счет чего очистка происходит со всех сторон. Назначение: для предметов, которые не боятся кантования и трения друг о друга.
Установки дробеметные проходного типа с вертикальной или горизонтальной камерой.
Различают следующие виды оборудования: аппараты для обработки листового проката, дробеметы для профильного проката, а также – проходные установки дробеметного типа для обработки труб. Используются для обработки труб, стального проката, сварных конструкций.
Дробометы подвесного типа, в которых предметы подвешиваются на вращающиеся крюки конвейера.Метатели, расположенные сверху и снизу камеры, одновременно подают дробь, что позволяет за один цикл обработать предметы со всех сторон. Используется для эффективного удаления окалин, наклепов на крупногабаритных изделиях, которые не подлежат кантованию.
Установка дробеметная с ленточным транспортером замкнутого типа предназначена для обработки больших объемов мелких деталей или заготовок. Высокое качество обработки достигается за счет того, что помимо использования дроби, выполняется перемешивание изделий между собой в лотках. Таким образом, происходит равномерное очищение всей поверхности изделия.
Установка дробеметная с поворотным столом. В камере аппарата установлен вращающийся стол, на который кладутся предметы. После начала цикла происходит вращение стола и одновременная подача дроби на очищаемые предметы. Таким образом, происходит полное очищение поверхностей изделий, кроме самого низа.
Во всех установках используется принцип повторного использования дроби: весь используемый абразив очищается и подается обратно в камеру.
При очистке в случае необходимости тележка с отливкой выкатывается из камеры, отливка переворачивается, и процесс очистки повторяется.
Вместо тележки может использоваться конструкция на рисунке 3.
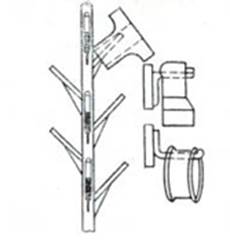
Рисунок 3 - Подвесная конструкция
Отработанная дробь и продукты очистки проваливаются через отверстие настила в бункер. На дне бункера установлен шнек, который транспортирует дробь в барабанный сепаратор. Вал шнека и сита приводится в действие от нижнего барабана элеватора через цепную передачу. Скорость вращения шнека и сита 27 об/мин. В барабанном сепараторе отделяются крупные частицы, а просеянный материал подается к элеватору, который поднимает его и выдает в приемный лоток магнитного сепаратора. Магнитный сепаратор представляет собой ленточный транспортер, приводной шкив которого является электромагнитным шкивом. Последний отделяет дробь от неметаллических включений (песка, пыли). Под сепаратором установлен бункер, разделенный на два отсека. В один отсек падают неметаллические материалы, а в другой - дробь, проходящая сквозь катушку размагничивания. Из этого отсека дробь по трем дробепроводам попадает к дробеметным и дробеструйному аппаратам.
При дробеструйной очистке струя дроби образуется под действием сжатого (4-6 атм.) воздуха, а при дробеметной дробь направляется на поверхность отливки лопастями быстро вращающегося ротора дробеметного аппарата. В качестве абразивного материала при дробеструйной и дробеметной очистке применяется металлический песок и дробь, изготовляемые следующим образом.
Струя чугуна по выходе из вагранки или ковша раздробляется на мелкие капельки струей воздуха или воды. Капли металла в виде мелких шариков падают в ванну с проточной водой. Быстро охлаждаясь в воде, дробь приобретает большую твердость. Выгруженная из ванны дробь просушивается и просеивается через сито-классификатор: годная (размером 0,5--3,5 мм) направляется в производство, а с размером более 3,5 мм дробится и затем добавляется к просеянной.
Расход дроби при использовании пневматических пескоструйных аппаратов составляет 2,5-3,5 кг на одну тонну очищенных отливок.
Применяют дробь, приготовленную из стальной проволоки. Такая дробь служит значительно больше чугунной, так как она менее хрупка.
Для отливок из мягких сплавов применяют алюминиевую дробь.
Дробеструйный метод очистки основан на использовании кинетической энергии металлических частиц (песка, дроби), выбрасываемых с большой скоростью из сопла дробеструйного аппарата струей сжатого воздуха. Дробеструйные установки, как правило, состоят из следующих узлов:
1) струйного аппарата;
2) рабочей камеры;
3) транспортного механизма, подающего отливку в рабочую зону;
4) системы возврата отработанной дроби или песка для повторного использования;
5) системы очистки и сепарации дроби.
У двухкамерного струйного аппарата (рисунок 4) верхняя зарядная камера 3 соединена с загрузочной воронкой 1 при помощи обратного клапана 2, нижняя рабочая камера 5 соединена с зарядной посредством второго обратного клапана 4. Сжатый воздух подается через трубку 9 и кран 10 в трубу 8 под дном бункера, смешивается здесь с поступающей через отверстие в дне бункера дробью и по шлангу через сопло выбрасывает струю на обрабатываемую отливку. Камеры 3 и 5 соединены с трубой 8 так, что рабочая камера 5 все время находится под давлением сжатого воздуха, а зарядная 5 - только в момент зарядки рабочей. Для наполнения дробью зарядной камеры надо понизить в ней давление. Для этого служит специальный клапан 13, через который зарядная камера сообщается с атмосферой.
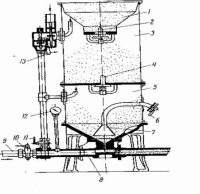
Рисунок 4-Двухкамерный дробеструйный аппарат
1-загрузочная воронка; 2- обратный клапан; 3- верхняя зарядная камера; 4- обратный клапан; 5- рабочая камера; 6 – клапан; 7- дно бункера;8- труба сжатого воздуха; 9– трубка; 10– кран; 11– кран; 12– манометр;13– клапан;
При снижении давления в камере обратный клапан 2 откроется, и поступающая по элеватору дробь через воронку 1 наполнит зарядную камеру. Как только камера наполнится, клапаном 13 снова открывают доступ сжатого воздуха в зарядную камеру, давление в ней поднимается, и обратный клапан воронки 1 закрывается. Когда давление в верхней и нижней камерах сравняется, открывается обратный клапан 4, и дробь или металлический песок заполняет рабочую камеру.
Аппарат может работать без перерыва на время зарядки. Однако отверстие в дне бункера для выхода песка часто засоряется. Прочищают его сжатым воздухом. Для этого с помощью крана 11 прекращают подачу сжатого воздуха в камеры. После этого продувают отверстие, открывая клапан 6 на изогнутом колене трубы, которая заканчивается воронкой 7 над отверстием в дне бункера. Сжатый воздух из трубы 8 через отверстие, воронку и изогнутую трубу удаляет все застрявшие в отверстии частицы. Закрыв клапан 6 и открыв кран 11, продолжают работу. Давление сжатого воздуха измеряется манометром 12.
Из многочисленных конструкций дробеструйных машин для очистки отливок наиболее распространены барабаны, столы и камеры.
2 РАСЧЕТ ОСНОВНЫХ ТЕХНОЛОГИЧЕСКИХ И ПРОЧНОСТНЫХ ПАРАМЕТРОВ
Рассмотрим рабочий процесс типового дробеметного колеса, имеющего подачу дроби 130 кг/мин, диаметр 500 мм, частоту вращения 2250 об/мин (w =235,6 с-1), число рабочих лопатой и лопаток импеллера по 8 штук, ширину окна во втулке импеллера 50 мм и размеры втулки импеллера и зазоров, как показано на рисунке 5.
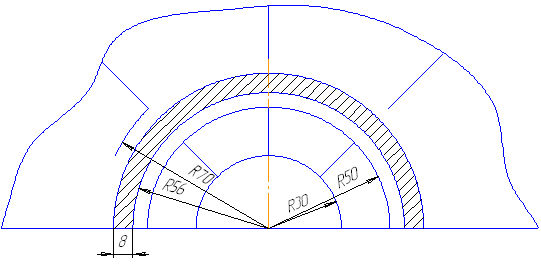
Рисунок 5 - Размеры импеллера типового дробеметного колеса
Примем, что поток дроби выбрасывается по касательной из зазора в точке 0 на радиусе r0 = 53 мм (рисунок 6). Скорость выбрасывания составит
где w - частота вращения дробеметного колеса;
r0 - радиус вращения.
При возможном сечении 50?6 мм и плотности укладки в нем дроби 2,5 г/см3 максимальная подача дроби в минуту будет составлять 0,05·0,006·12,5·60·2,5·103 = 560 кг/мин, что в несколько раз превышает действительную подачу дроби, с которой работает данное колесо.
От этого выбрасываемого импеллером потока дроби очередная (сорадиальная с началом окна в распределительной втулке) рабочая лопатка А, повернувшись с колесом в положение А' (рисунок 2), отсечет и примет на себя некоторый отрезок 1 - 2 потока. Для точки 1 этого отрезка, в которой помещается его хвостовая (задняя) дробинка, можно написать: l20-1 + 532 = 702 откуда расстояние между точками 1 и 2 l0-1 = 46 мм, а угловая координата точки 1:

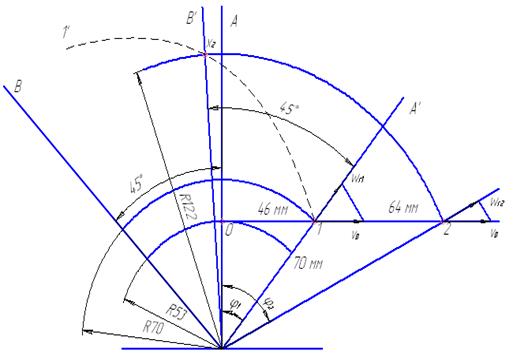
Рисунок 6 - Расчет рабочего процесса дробеметного колеса
Для нахождения положения точки 2 отсекаемого отрезка потока, в которой помещается головная (передняя) дробинка данного отрезка, рассмотрим относительное движение начала отрезка, следующего заданным, т.е. точки 1. Для этого, пользуясь изложенной выше общей методикой, построим по точкам траекторию 1 - 1' движения точки 1 относительно колеса, исходя из полярных координат2,

где v0 - абсолютная скорость дробинки;
t - промежуток времени от момента начала движения в точке 1;
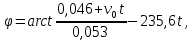