Файл: 2. Общее устройство мостового крана, технические характеристики, смазка и карта смазки крана.docx
ВУЗ: Не указан
Категория: Не указан
Дисциплина: Не указана
Добавлен: 03.12.2023
Просмотров: 348
Скачиваний: 4
ВНИМАНИЕ! Если данный файл нарушает Ваши авторские права, то обязательно сообщите нам.
б) ограничители: ВУ – 250 (грузоподъемности, перекоса)
в) противоугонные устройства:
г) блокировочные устройства: выключатель ВК – 211 (люка, разъемной части перил и т. п.)
д) указатели:
е) сигнальные приборы: звуковой
Род привода – электрический
Род электрического тока и напряжения.
Цепь – силовая, род тока – переменный, напряжение – 220/380В
Цепь управления:
Цепь рабочего освещения – напряжение 220В
Цепь ремонтного освещения – 36В
Место управления из кабины
Прочие сведения
а) допустимый уклон рельсового подкранового пути 0,001
б) кран допускается для работы при минимальной температуре воздуха до -25˚С
Характеристика канатов
Грузовой канат (главный подъем, вспомогательный подъем); конструкция каната – ЛК-Р6×19+10.с; диаметр каната – 17,5мм; расчетный предел прочности проволоки – 180кг/мм2; суммарное разрывное усиление каната 20 881кг; длина каната 91×2м; коэффициент запаса прочности 6,9.
Характеристика грузозахватного органа
а) крюки однорогие:
Главный крюк:
Грузоподъемность – 10 000 – 2шт.
ГОСТ – 2105-53; 1050-60;
Завод изготовитель – поковки Чебаркульского завода, механическая обработка Узловского завода;
Заводской № 792; 796 серия208022
Траверса:
Грузоподъемность – 10 000 – 4шт. 20 000 – 1шт.
ГОСТ – 8479-57;
Завод изготовитель – поковки Чебаркульского завода, механическая обработка Узловского завода;
Заводской № 786; 787 серия 112067; № 782 серия 208022; № 784 серия 207613 (20т); № 873 серия 11214.
Сведения об основных элементах металлоконструкций крана
-
Пролетная балка – марка стали ст.3 кп. № ГОСТ 500-58; Э – 42, цм – 7 -
Концевая балка – № ГОСТ 9467-60 св. 0,8 -
Стыковые накладки соединения концевых балок - № ГОСТ 2246-54 -
Рабочие и троллейные площадки – Ф 5мм св 0,8 -
Рама тележки в сварке - № ГОСТ 2246-54 -
Кронштейны крепления кабины.
Смазка механизмов мостового крана
Большое влияние на долговечность и надежность деталей, на КПД механизмов и, в конечном итоге, на стоимость эксплуатации оказывают выбор и режим смазки, которая кроме уменьшения трения предохраняет от попадания на сопряженные поверхности абразивных пылевидных частиц, уплотняет зазоры, отводит тепло от трущихся поверхностей, предохраняет от коррозии.
Из систем смазки наиболее прогрессивной является централизованная, однако в ряде случаев (например, для подшипников крюковой подвески) целесообразно применение ручной индивидуальной смазки. Такая система включает ручную станцию для нагнетания смазки, магистральные трубопроводы, питатели и трубопроводы подвода к точкам смазки. На кране монтируют две или три такие установки. Одна из них используется для обслуживания механизмов тележки, а одна или две другие — для обслуживания механизмов передвижения моста.
Н
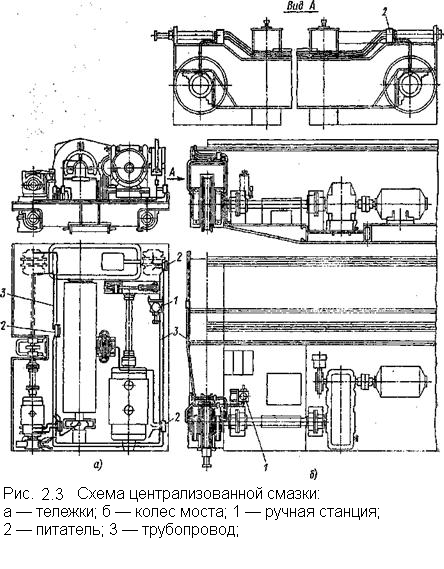
Трубопроводы системы смазки выполняются из стальных бесшовных труб, соединяемых между собой при помощи муфт и тройников. Подвод смазки к подвижным смазочным точкам осуществляется гибкими резиновыми рукавами высокого давления с металлической оплеткой. На рис. 2.3 изображены схемы централизованной смазки механизмов тележки и механизмов передвижения: моста.
Смазка играет важную роль в повышении долговечности стальных канатов. Заводская (наносимая в процессе изготовления канатов) и эксплуатационная смазки предупреждают износ не только канатов, но блоков и барабанов и препятствуют образованию высокоабразивной коррозии на этих деталях и проволоках каната. Смазка улучшает условия скольжения, что, в свою очередь, снижает напряжения в канате. Органический сердечник нового каната содержит 12—15% смазки, с течением времени она окисляется и выдавливается, в результате чего, при отсутствии ее своевременного восстановления, содержание смазки в сердечнике снижается примерно до 2,5%. В регулярно смазываемых канатах,’ сердечники которых имели около 15% смазки, она постоянно поддерживается на уровне примерно 12%.
З
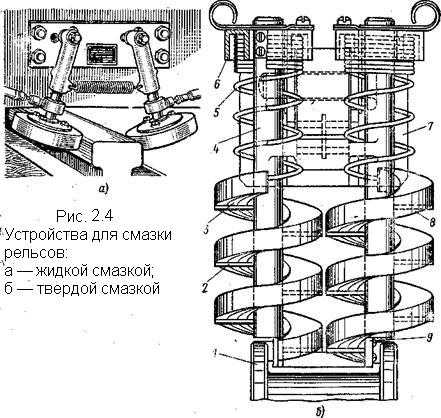
Система для смазки боковых поверхностей рельсов показана на рис, 2.3, а. Она включает насос, приводимый в движение через эксцентрик, и шатун от вала механизма передвижения, резервуар, трубопроводы и смазывающие ролики. Последние устанавливаются по обе стороны головки рельса и прижимаются к ней пружинами. Ролики изготавливают из синтетического материала. С их помощью на поверхности головки наносится тонкий слой смазки, расход которой на каждую пару роликов составляет около 8 г за 1 ч работы крана. Насос этой же системы может быть использован и для смазки подшипников ходовых колес.
Снижается в 1,6 раза износ рельсов и в 1,3 раза износ реборд при использовании твердого смазочного материала, содержащего 83—84% дисульфида молибдена, 12—13% эпоксидной смолы и 4—5% малеинового ангидрида. В одном из устройств, для его нанесения на реборды колес, применяются два круглых диаметром 20—25 мм брикета из смазочного материала, которые размещаются в трубках, закрепленных на кронштейне. Последний расположен в диаметральной плоскости колеса и установлен на торце концевой балки. Внутри труб размещены пружины, которые с усилием 7—10 кгс постоянно поджимают брикеты к внутренней стороне реборд.
Другое устройство такого же назначения (патент США № 3896903) обеспечивает постоянную подачу смазки на реборды колеса (рис. 10.7, б). Оно закрепляется на торце концевой балки. На стойках 4 установлены пружины, концы которых воздействуют на торцовые пластины брикетов, выполненных в виде спиралей. Желоб на нижней стороне брикета взаимодействует с соответствующей направляющей, прикрепленной на кронштейне к стойке, а его нижний конец проходит через окно в рамке. При закладке смазки головку поворачивают, заводя пружину. Во время работы устройства брикет под действием пружины перемещается по направляющей и постоянно поджимается к внутренней стороне реборды.
3.Материалы, из которых изготовлены детали крана.
Металлические конструкции кранов являются наиболее металлоемкими частями. Их масса составляет 60…80% массы крана, а стоимость металла – до 65% стоимости изготовленной конструкции, поэтому рациональный выбор материала имеет важное значение.
Основным материалом для изготовления частей подъемного крана: моста, тележки, крюка, канатов, колес и валов – является сталь.
Сталь – это ковкий сплав железа с углеродом (0,04 – 2%) и другими элементами.
В зависимости от назначения материалом для изготовления металлоконструкций служит прокат углеродистых и низколегированных сталей. Углеродистая сталь обыкновенного качества по ГОСТ 380-81 в зависимости от назначения подразделяется на три группы: А – поставляется по механическим свойствам. Б – по химическим составу. В – по механическим свойствам и химическому составу.
По степени раскисленности стали бывают спокойные (СП), полуспокойные (ПС) и кипящие (КП). Например, Ст3сп – сталь Ст3, спокойная.
Наиболее распространенной сталью в металлоконструкциях является сталь Ст3, обладающая достаточно высокими механическими свойствами, большой пластичностью, хорошей свариваемостью, и не подвергается закалке.
Углеродистая сталь на ряду с железом и углеродом содержит марганец (0,1 – 1%), кремний (до 0,4%), а также вредные примеси – серу (не более 0,08%) и фосфор (не выше 0,09%).
Кипящие стали значительно дешевле спокойных сталей, однако вследствие неоднородности структуры они обладают худшей свариваемостью и имеют склонность к образованию трещин при низких температурах. Их применяют в металлоконструкциях, работающих в условиях статических нагрузок и при температуре не ниже -25оС для изготовления перил, лестниц, площадок и различного рода ограждений.
Для металлоконструкций кранов большой грузоподъемности, а также кранов северного использования применяются низколегированные стали 19ХСНД, 15ХСНД, 10ХГСНД, 10Г2Сд, 14ХГС, по ГОСТ 19282-73 и др., имеющие по сравнению со сталью Ст3 более высокие механические свойства, повышенную стойкость против атмосферной коррозии и меньшую хладноломкость. Применение низколегированных сталей приводит к уменьшению массы металлоконструкции до 15%.
Важное значение в технике имеет также легированная сталь.
Количество углерода в углеродистой стали определяет ее свойства: чем больше содержание углерода, тем выше её прочность и твердость, чем меньше углерода, тем мягче сталь. Фосфор и сера ухудшают качество стали, эти примеси попадают из руды в чугун, а при выплавке стали из чугуна они переходят в сталь.
Для повышения качества стали подвергаются термической обработке: закалке, отпуску, отжигу и нормализации.
В зависимости от назначения, стали делятся на: конструкционные, инструментальные, жаростойкие, кислотоупорные и др.
Конструкционные стали, применяемы для изготовления машин и сооружений, подразделяют на углеродистые качественные и легированные стали, а инструментальные стали на углеродистые, легированные и быстрорежущие.
В обозначенных марках стали буквы указывают способ получения стали, например:
М – мартеновская сталь;
Б – бессемеровская сталь.
Цифры обозначают среднее содержание углерода, сталь 45 – 0,45% углерода обозначение легированных сталей производится побуквенно – цифровой системе. Первые две цифры показывают содержание углерода, например: сталь 20 содержит 0,2% углерода, сталь 45 – 0,45% углерода. Обозначение легированных сталей производится побуквенно – цифровой системе.
Содержание легирующих элементов свыше 1% указывая после соответствующих букв. Например марка 12ХН2 означает, что сталь содержит 0,12% углерода, менее 1% хрома и около 2% никеля.
Другой материал, применяемый в краностроение – чугун. Чугун – это нековкий сплав железа с углеродом (более 2% углерода, обычно 3 – 4,5%), содержащий марганец (до 3%), кремний (до 4,5%), серу (не более 0,08%) и фосфор (до 2,5%).
По назначению, различают предельный чугун, служащий материалом для переработки в сталь (белый чугун), и литейный (серый чугун), предназначенный для получения фасонных отливок. Литейный чугун сравнительно мягок, легко поддается механической обработке. Из него отливают корпуса редукторов и электродвигателей, маховичьки контроллеров, станины станков, из него изготавливают ряд других деталей.
Из цветных металлов и сплавов в краностроении применяют медь, латунь, олово, свинец и алюминий. Медь идет на изготовление приводов электрического аппарата (рубильника), магнитного пускателя и контактов всех типов.
Медь – разово-красный метал плотностью 8,952/См3, с температурой плавления 1083оС, обладает хорошей электропроводимостью, хорошо обрабатывается.
Латунь – сплав меди с цинком (до 50%), иногда с добавками в небольшом количестве других элементов. Из латуни делают щеткодержатели и контактные кольца.
Олово – серебристо белый метал с температурой плавления 232оС. Олово в чистом виде и в сплавах со свинцом применяют для пайки. На кранах кабельные наконечники как правило паяют сплавом ПОС – 30 или ПОС – 40 (припай олово – свинцовый).