Файл: Минобрнауки россии глазовский инженерноэкономический институт (филиал).docx
ВУЗ: Не указан
Категория: Не указан
Дисциплина: Не указана
Добавлен: 04.12.2023
Просмотров: 116
Скачиваний: 3
ВНИМАНИЕ! Если данный файл нарушает Ваши авторские права, то обязательно сообщите нам.
Простота изготовления оболочковых форм, значительное уменьшение припусков на механическую обработку, высокая точность размеров отливок сложной конфигурации (±0,2 мм на 100 мм длины) являются основными преимуществами этого способа.
Литье под давлением особенно распространено в производстве электро- и радиоаппаратуры и других подобных изделий. Сущность этого способа состоит в том, что жидкий металл подается в металлическую форму под давлением в специальных литьевых машинах, благодаря чему он хорошо заполняет все ее полости. Литье под давлением используют для получения из цветных сплавов литых заготовок сложной формы с различными выступами, приливами и отверстиями.
Литье по выплавляемым моделям основано на использовании моделей, которые изготовляют в металлических пресс-формах заполнением их парафиностеариновой смесью. Полученные таким образом модели покрывают тонким слоем специальной жидкой массы и мелким кварцевым песком, просушивают и прокаливают в электропечи. При этом парафиностеариновая смесь вытекает из формы, которая затем используется для получения точных металлических деталей.
Ковка и горячая штамповка.
При этих процессах нагретый металл обрабатывают ударом или давлением, пользуясь молотами и ковочными машинами. Если нагретый металл обрабатывают без специальных форм (штампов), то процесс называется свободной ковкой, если же в штампах — горячей штамповкой.
При горячей штамповке на изготовление заготовок затрачивается значительно меньше времени, чем при свободной ковке. При этом заготовки получаются более точные по форме и размерам, с меньшими припусками для дальнейшей механической обработки.
Холодная штамповка. Это процесс получения заготовок и деталей из листового, ленточного и полосового материала способом вырубки, гибки, вытяжки, отбортовки в штампах на прессах.
Способ холодной штамповки очень производителен и широко применяется в различных видах производства. При различных способах получения заготовок припуск на их обработку будет различным.
ермообработка металлов – вид обработки металлов и сплавов, который применяется в 100% случаев изготовления изделия, где требуется изменение прочностных и физических свойств исходных материалов. При комбинации различных видов термообработки или обработка изделия зонами позволяет достичь необходимых свойств металлического изделия в целом или в отдельных участках.
Компания «ЭКОИНВЕНТ» готова предложить Вам услуги по термической обработке (термообработке) металлов с высоким качеством результата обработки деталей и узлов, что достигается многолетней работой в данном направлении, наличием высококвалифицированных специалистов и использовании современного оборудования.
Преимущества термической обработки металлов
При проведении термической обработки металлов улучшаются физические свойства металла, что крайне необходимо в рамках современного промышленного производства. Из основных преимуществ термообработки можно выделить следующие:
-
повышение стойкости металла к внешним воздействиям, как следствие увеличение срока эксплуатации обработанных деталей и узлов. -
Возможность использовать металл более дешевого ценового диапазона, для получения характеристик металла более высокой стоимости, что значительно экономит средства при крупносерийном производстве деталей. -
Получение таких физических свойств металла, которых нет у других не обработанных металлов и сплавов. -
Возможность зональной обработки деталей, для получения необходимых свойств металла в различных областях деталей.
Суть термической обработки состоит в соблюдении определенной последовательности технологических операций по нагреву, выдержки и охлаждения металла.
В зависимости от металла и получения определенных свойств деталей термическая обработка (термообработка) делится на следующие основные виды:
-
Отжиг -
Закалка -
Отпуск -
Нормализация
Отжиг
Отжиг — термическая обработка (термообработка) металла, при которой производится нагревание металла, а затем медленное охлаждение. Эта термообработка (т. е. отжиг) бывает разных видов (вид отжига зависит от температуры нагрева, скорости охлаждения металла).
В процессе отжига достигается однородность зернистой микроструктуры металла, снижается количество микровключений, при охлаждении изделия образуется неравновесная структура мартенситного типа. При отжиге достигается снижение твердости металла, увеличение пластичности и ударной вязкости, снимается наклеп.
Закалка
Закалка — термическая обработка (термообработка) металлов, основанная на рекристаллизации при нагреве изделия до температуры выше критической точки; после необходимого времени выдержки при критической температуре для завершения термической обработки следует быстрое охлаждение в воде, масле или других жидкостях.
В процессе закалки происходит увеличение твердости и прочности, ударная вязкость металла снижается.
Отпуск
Отпуск — термическая обработка (термообработка) металлов, производится после закалки для значительного уменьшения или полного снятия остаточных напряжений.
В процессе отпуска достигается повышение вязкости, уменьшение твердости и хрупкости металла.
Нормализация
Нормализация — термическая обработка (термообработка), близкая по своим результатам с отжигом. Различия этих термообработок (нормализации и отжига) заключается в том, что при нормализации металл охлаждается на воздухе (при отжиге — плавно в печи).
- 1 2 3 4 5
Материальная часть металлорежущих станков, их наладка на выполняемую работу и обслуживание.
Эффективность работы металлорежущих станков во многом зависит от способов их настройки и наладки.
Под наладкой подразумевается целый комплекс мероприятий, подготавливающих станок к работе, а именно к обработке деталей заданных размеров и форм, которые указаны в чертежах.
В большинстве случаев наладка металлорежущего станка состоит из следующих процедур:
-
Изучения технологической документации, а также обеспечения станка необходимыми инструментами и оснасткой; -
Монтажа приспособлений, необходимых для закрепления деталей; -
Регулировки загрузочных устройств и механизмов, которые подают материал; -
Смены зубчатых колес подачи или кулачков; -
Предварительной установки и фиксации режущих инструментов; -
Установки передач, на которых вращение шпинделей будет происходить с необходимой скоростью; -
Предварительной расстановки упоров, с помощью которых устанавливается последовательность движения суппортов, длина их перемещения, а также последовательность изменения скоростного режима вращения шпинделей.
Следующим этапом подготовки металлорежущего станка к работе является его настройка, которая предусматривает действия, позволяющие достичь нужной точности обработки деталей. В процессе настройки станка устанавливается относительное положение режущих инструментов, упоров и самой детали, подлежащей обработке. Процесс резки может повлечь за собой сбой первоначальной настройки. Такое случается либо за счет износа режущих инструментов, либо по какой-либо другой причине. Поэтому необходимо восстанавливать настройки металлорежущего станка, если есть вероятность получения размеров, не вписывающихся в установленные пределы.
Таким образом, наладку оборудования проводят один раз, а настройку — многократно. При этом настройка станка занимает много времени, а в процессе ее осуществления работа станка невозможна.
Добавим к вышесказанному, что для металлорежущих станков также необходимо проводить поднастройку, которая подразумевает незначительное внесение корректировок в положение инструментов, упоров или кулачков. Проведение этих действий является необходимой процедурой, если данные элементы (инструменты, упоры, кулачки) располагаются таким образом, что не позволяют получить нужный размер детали, подвергающейся обработке.
-
Конструкция инструментов, применяемых при резании, способах настройки на выполняемый размер.
Производительность автоматической линии или автоматического станка зависит от применяемого режущего инструмента. Последний должен удовлетворять не только обычным условиям, предъявляемым к режущему инструменту, как-то: обеспечению определенного класса шероховатости и точности обрабатываемых заготовок, необходимой стойкости и прочности, экономичности, — но также и специфическим условиям, обусловленным автоматическим оборудованием. К таким условиям относится обеспечение размерной стойкости инструмента, стабильность его работы, быстросменность и взаимозаменяемость. Указанные условия, обеспечивающие непрерывность процесса обработки и влияющие на производительность и эффективность работы автоматизированного производства (в том числе автоматических линий, станков-автоматов, станков с программным управлением, многооперационных станков), зависят от конструкции режущего инструмента.
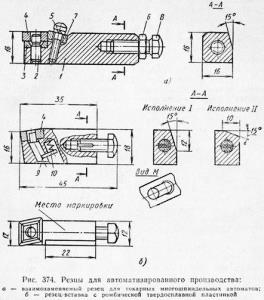
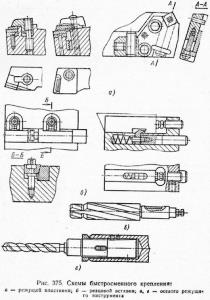
Для обеспечения наибольшей непрерывности работы режущего инструмента в условиях автоматизированного производства необходимо исключить потери времени, складывающиеся из времени, необходимого на установку и закрепление инструмента; на настройку инструмента для получения требуемых размеров обрабатываемой заготовки как в начале, так и в процессе работы инструмента до. момента снятия его. на переточку; на снятие изношенного инструмента.
Учитывая специфику работы в условиях автоматизированного производства и стремясь сократить потери времени, конструкторы разработали большое количество разнообразных конструкций, в которых нашли отражение следующие идеи: