Файл: Минобрнауки россии глазовский инженерноэкономический институт (филиал).docx
ВУЗ: Не указан
Категория: Не указан
Дисциплина: Не указана
Добавлен: 04.12.2023
Просмотров: 111
Скачиваний: 3
ВНИМАНИЕ! Если данный файл нарушает Ваши авторские права, то обязательно сообщите нам.
а) применение взаимозаменяемого инструмента, настраиваемого на размер, что исключает потери времени на первоначальную наладку;
б) использование сил резания для частичного или полного крепления инструмента, что. упрощает конструкции механизма крепления инструмента, обеспечивая более высокую точность установки и, главное, сокращение времени на установку, закрепление, открепление и снятие режущей части или самого инструмента;
в) встройка узлов автоматической подналадки и регулирования инструмента для компенсации систематических погрешностей размеров заготовки, что обеспечивает повышение размерной стойкости инструмента и сокращает указанные выше потери времени;
г) использование принципа обновления режущих участков одной и той же кромки (прерывное или непрерывное), обновления резцов (зубьев) самих режущих инструментов.
Наряду с указанными проблемами большое значение имеет формирование и отвод стружки в условиях работы автоматического станка. В этом направлении также найдены решения, обеспечивающие нормальный стружкоотвод. Ниже приводится описание отдельных конструкций инструментов для автоматизированных производств с указанием их особенностей.
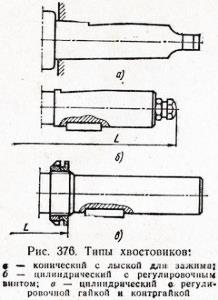
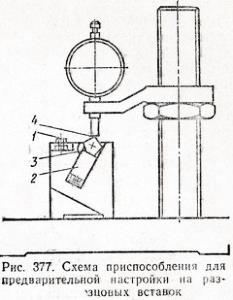
В автоматизированном производстве используется обычный стандартный инструмент (резцы, сверла, зенкеры, развертки, цековки, фрезы, метчики и др.). Однако технические требования к инструментальным материалам и к точности изготовления — повышенные.
Для обеспечения повышенной стойкости и надежности инструмента его изготовляют из наиболее совершенных и целесообразных для конкретных условий обработки инструментальных материалов. Изготовление (и переточка) инструмента осуществляется по специальным техническим условиям, в которых предусмотрено существенное повышение точности размеров и положения режущих кромок относительно оси вращения инструмента. Однако, кроме указанных изменений, ряд стандартных инструментов имеет отличие и в конструктивном оформлении, вызванные необходимостью осуществления быстросменности и взаимозаменяемости (режущей пластинки или самого инструмента).
Например, взаимозаменяемые резцы с твердосплавными многогранными и круглыми (цилиндрическими) пластинками (рис. 374, а), применяемые в автоматизированном производстве, несколько отличаются от аналогичных резцов, используемых на универсальных станках. Державка 1 (короче по длине) имеет скос под углом 15°, предназначенный для крепления резца на станке. Опорные поверхности державки должны быть взаимно перпендикулярны. В державку ввертывается регулировочный винт 8 (резьба по 2-му классу точности), который фиксируется в определенном положении контргайкой 6. Крепление режущей твердосплавной пластинки 4 осуществляется так же, как у стандартных резцов, предназначенных для универсальных станков, т. е. с помощью винта 5, клина 7 и штифта 2. Шероховатость поверхностей режущей пластинки не грубее 9-го, а подкладки 3 — 8-го класса.
Несколько иное крепление режущей пластинки имеют резцы-вставки, представленные на рис. 374, б. Здесь резец-вставка с ромбической’ твердосплавной пластинкой 4 крепится с помощью тяги, планки 9 и пружины 10.
Чтобы простои оборудования автоматических линий, связанные с заточкой затупившегося режущего инструмента, были минимальными, линии должны быть оснащены быстросменной инструментальной оснасткой. При этом быстросменным элементом может быть режущая пластинка (рис. 375, а) (многогранная неперетачиваемая твердосплавная пластинка); резцовая вставка (рис, 375,6); осевой режущий инструмент с цилиндрическим хвостовиком (рис. 375, е); удлинитель с цилиндрическим хвостовиком (рис. 375, г), в котором закреплен режущий инструмент, и т. д. Для замены режущего инструмента с помощью этих способов крепления затрачивается от 20 до 30 с на каждый инструмент. В связи с этим сверла, зенкеры, развертки, цековки и другой осевой инструмент, применяемый в автоматизированном производстве, отличаются хвостовика.
На рис. 376 показаны различные типы хвостовиков. Конический хвостовик имеет лыску для дополнительного зажима с помощью винта (рис. 376, а). Часто применяемые конструкции цилиндрических хвостовиков служат для быстрого закрепления инструмента (рис. 376, б). Регулировочный винт позволяет обеспечить настройку на длину L вне станка. Для регулирования длины инструментов в рабочем положении переднюю резьбовую часть делают с регулировочной гайкой и контргайкой (рис. 376, в).
Часто при обработке корпусных деталей в линии требуется совместить в одну операцию сверление отверстия и снятие фаски или сверление ступенчатых отверстий под головку болта.
Для этой цели применяют ступенчатые сверла двух видов: переточенные из стандартных и специальные четырехленточные. Ружейными сверлами сверлят глубокие отверстия. Для обработки ступенчатых отверстий и канавок на торцовых поверхностях используют комбинированные инструменты. Целесообразность применения сложного комбинированного инструмента в каждом отдельном случае должна быть проверена экономическим расчетом.
Для нарезания резьбы на автоматических линиях, применяют метчики, резьбонарезные и резьбонакатные головки; для фрезерных операций— различные фрезы (торцовые, цилиндрические, концевые, дисковые и т. д.). Наибольшее применение на автоматических линиях обработки корпусных деталей получили торцовые фрезы сборных конструкций с ножами, оснащенными твердым сплавом. Рекомендуется снабжать торцовые фрезы одним широким зачистным ножом, выступающим на небольшую величину (0,02—0,04 мм) относительно других ножей, что позволяет при больших минутных подачах получить высокий класс шероховатости поверхности.
Настройка инструмента на нужный размер осуществляется вне станка на специальных приспособлениях. В зависимости от вида инструмента и выполняемой им операции применяют различные конструкции приспособлений для предварительной настройки. На рис. 377 приведена схема приспособления конструкции ВНИИ, предназначенного для предварительной настройки на размер регулируемых быстросменных резцовых вставок. Приспособление в виде стального кубика, на боковых сторонах которого имеются точные пазы 2 для установки в них резцовых вставок 3, устанавливают на стандартный индикаторный столик. Резцовая вставка располагается относительно измерительного наконечника индикатора 4 так же, как она устанавливается в рабочем положении на станке. Настройку индикатора на нулевой отсчет осуществляют по эталонному резцу либо по сферической головке 1 регулировочного эталонного винта. Длина резцовой вставки регулируется с помощью регулировочного винта. Точность настройки 0,02—0,03 мм.
- 1 2 3 4 5
Устройства приспособлений для закрепления заготовок при обработке на станках, установка на станке.
Универсальные приспособления (прихваты, угловые плиты, призмы, машинные тиски и др.) предназначены для закрепления заготовок. Их применяют главным образов в единичном и мелкосерийном производствах.
Прихваты используют для закрепления заготовок сложной формы или больших габаритов непосредственно на столе станка. На рис. 1 показаны различные типы прихватов: плиточные (рис. а), вилкообразные (рис. б), корытообразные (рис. в), изогнутые универсальные. Все прихваты имеют овальные отверстия или выемки для перемещения прихвата относительно обрабатываемой заготовки. На рис. 2, а показано закрепление обрабатываемой заготовки на столе станка плиточным прихватом, который одним концом опирается на заготовку, а другим — на подкладку. Головка болта заводится в Т-образный паз. стола через отверстие прихвата. При завертывании ключом гайки прихват прижимается к заготовке, закрепляя ее. В качестве подкладки под прихваты используют ступенчатые подставки (рис. 2, б), различные бруски требуемой высоты или специальные опоры для плиточных прихватов (рис. 2, в).
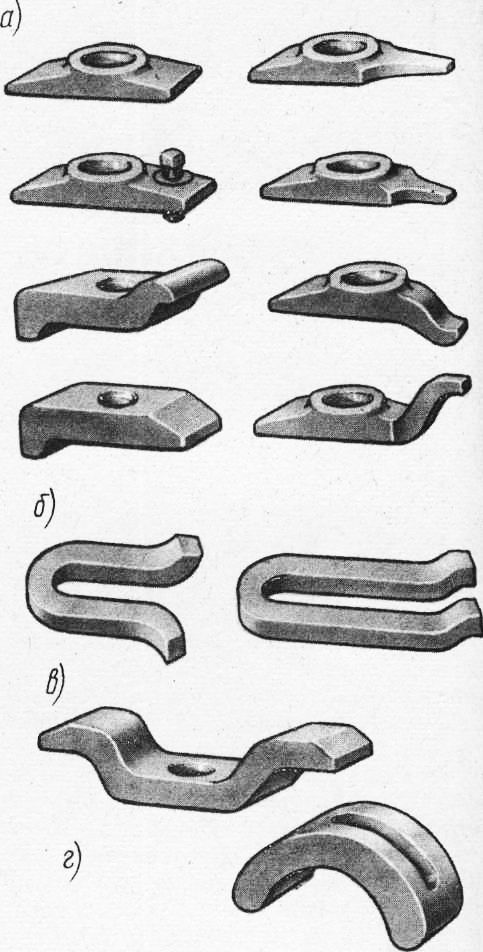
Заготовки небольших по высоте размеров могут быть закреплены непосредственно на столе станка прихватами (рис. 20, г и д). В некоторых случаях удобно пользоваться подпружиненным прихватом с достаточно большим диапазоном регулирования по вылету и закреплением заготовки рукояткой. Весьма удобным в работе является регулируемый по высоте изогнутый универсальный прихват (рис. 2, е).
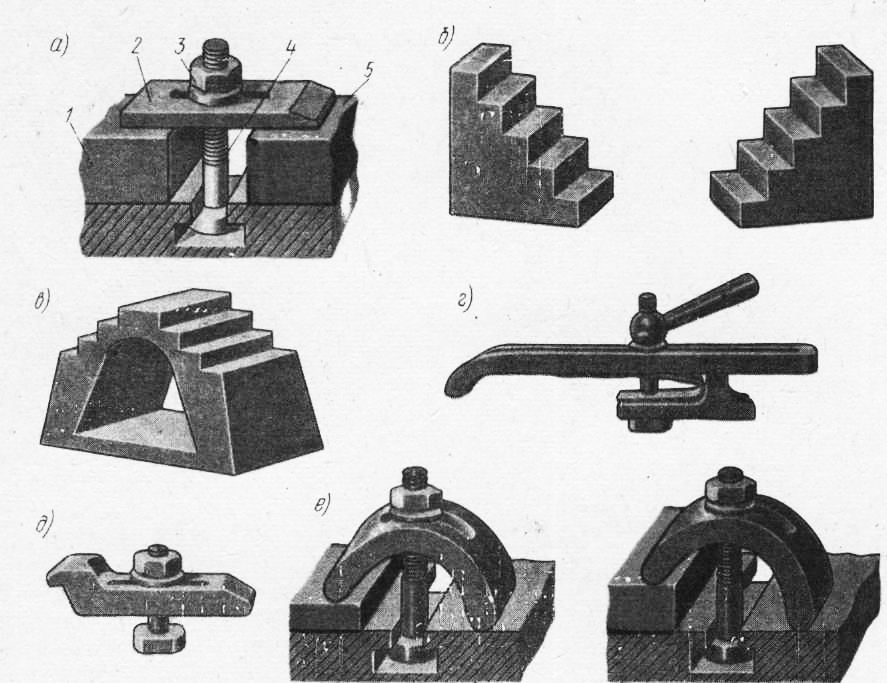
Разные по высоте заготовки можно закреплять универсальными прижимами. В прижиме, показанном на рис. 3, а, заготовка крепится прихватом Г-образной формы с выемкой, в которую устанавливается сухарь. Заготовка закрепляется болтом и гайкой. Ступенчатый прижим (рис. 3, б) состоит из корпуса, в котором имеются уступы (ступени), расположенные по выемке корпуса на разной высоте. На уступы опирается подкладка, входящая своим шлицем в прорезь прихвата, и прижимается к нему пружиной. Прихват может переворачиваться на 180°. В корпусе прижима имеется сквозное резьбовое отверстие для прижимного болта и для крепления всего прижима к Т-образным пазам станка. Прижим позволяет закреплять заготовки разной высоты в некотором диапазоне.
При чистовом фрезеровании затяжка болтов не должна вызывать деформаций обрабатываемой заготовки.
Угловые плиты применяют для установки и крепления заготовок, имеющих две плоскости, расположенные под углом 90°. На рис. 5, а показана обычная угловая плита Она имеет одно или два ребра жесткости и две полки (равнобокие или неравнобокие, широкие или узкие), расположенные под углом 90°. На рис. 5, б показана поворотная угловая плита, полку которой можно поворачивать вокруг оси после освобождения гайки и устанавливать на требуемый угол по шкале. Такие плиты применяют при обработке наклонных плоскостей.
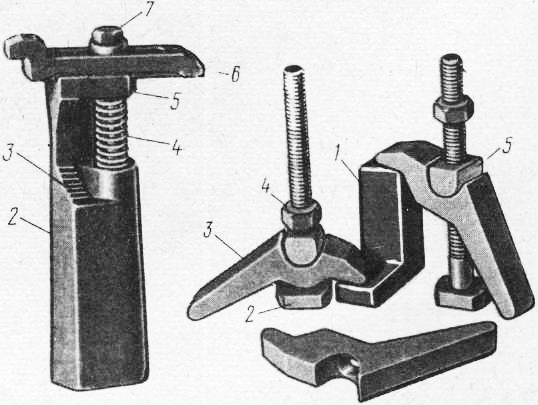
Машинные тиски по конструкции подразделяют на простые, поворотные и универсальные. Они представляют собой упрощенную модификацию пневматических машинных тисков с высокой степенью модификации (80%). Для питания гидропривода машинных гидрофицированных или пневматических тисков используется индивидуальная гидростанция типа ГМТ или пневмогидро-преобразователь типа ПМТ, работающий от заводской пневмосети. Применение специальных съемных губок и подкладок к машинным тискам приводит к значительному сокращению затрат времени на установку заготовок.
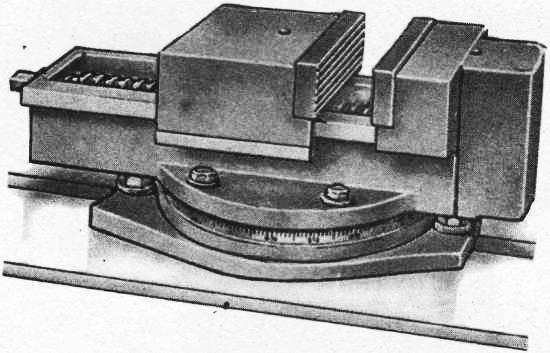
-
Механизация и автоматизация технологических процессов.
Механизация и автоматизация производственных процессов — это комплекс мероприятий, предусматривающих широкую замену ручных операций машинами и механизмами, внедрение автоматических станков, отдельных линий и производств.
Механизация производственных процессов означает замену ручного труда машинами, механизмами и другой техникой.
Механизация производства непрерывно развивается, совершенствуется, переходя от низших к более высоким формам: от ручного труда к частичной, малой и комплексной механизации и далее к высшей форме механизации — автоматизации.
В механизированном производстве значительная часть трудовых операций выполняется машинами и механизмами, меньшая — вручную. Это частичная (некомплексная) механизация, при которой могут быть отдельные слабомеханизированные звенья.
Комплексная механизация — это способ выполнения всего комплекса работ, входящих в данный производственный цикл, машинами и механизмами.