Файл: Дневникотчет по производственной практике (по профилю специальности).docx
Добавлен: 05.12.2023
Просмотров: 543
Скачиваний: 4
ВНИМАНИЕ! Если данный файл нарушает Ваши авторские права, то обязательно сообщите нам.
7 Анализ функциональных возможностей системы автоматического регулирования технологическим процессом
Система автоматического регулирования (САР) — это замкнутая автоматическая система, основанная на принципе обратной связи (ОС) — управлении объектом с использованием информации о результатах управления.
Основной задачей автоматического управления является поддержание определенного закона изменения одной или нескольких физических величин, характеризующих процессы, протекающие в ОУ, без непосредственного участия человека. Эти величины называются управляемыми величинами.
Контроль и сигнализация осуществляется контроллером. Это происходит следующим образом. Токовый сигнал с датчика поступает на вход аналогового модуля ввода контроллера. При помощи программы процессор принимает сигнал и сравнивает его заранее с заданным значением уставки. В случае равенства или превышения входной величиной предельного значения на соответствующем выходе дискретного модуля вывода формируется логическая единица. В соответствии с этим на щите оператора срабатывает световая и звуковая сигнализация.
Описание работы автоматического переключения газораспределительной станции (ГРС) на безопасный режим:
На рисунке 2 приведена упрощенная схема ГРС.
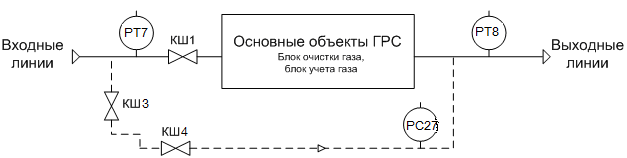
Рисунок 2- Описание управления объектом
При нормальном режиме работы ГРС газ поступает через входные линии через открытую входную задвижку КШ 1. В это время задвижки КШ 3, КШ 4 закрыты.
Переключение на безопасный режим работы производится в случаях неисправности основных объектов ГРС, что контролируется манометрами РT7 и РT8.
При обнаружении отклонений давлений от заданных параметров, переключение ГРС на безопасную линию начинается с полного открытия задвижки КШ 3. Далее на 10% приоткрывается регулирующая задвижка КШ 4 и, после того, как появляется давление в обводной линии, контролируемое манометром РC27 и выдержки времени 30 секунд, полностью закрывается задвижка КШ 1. После этого необходимо регулирующей задвижкой КШ 4 выставить необходимое для выхода линии значение давления, контролируемого манометром РC27 (приоткрыть задвижку КШ 4 до момента достижения заданного давления PC27). После этого выдается сигнал оператору о нормальном переключении на безопасную линию.
Если после выдержки времени 30 секунд, давление в обводной линии не появляется, включается аварийная сигнализация, и закрывается задвижка КШ 3.
8 Монтаж и ремонт и наладка средств и систем автоматического управления, а также мехатронных систем, применяемых на объекте практики с учетом действующей отраслевой нормативной и производственной документацией
Монтаж систем автоматизации — это работа, от качества которой зависит не только функционирование самих систем управления, но и работа технологических систем, и связанных с технологией систем
Монтаж систем автоматизации выполняют в соответствии с проектно-сметной документацией, передаваемой проектной организацией через заказчика монтажной организации. Заказчик или генеральный подрядчик (строительная организация) согласно заявочным спецификациям и ведомостям обеспечивает монтажную организацию основными материалами (металлопрокатом, трубами, кабелем, проводом), запорной арматурой, приборами и средствами автоматизации. Оборудование и приборы, необходимые для монтажа систем автоматизации, рабочие чертежи и сметы, а также техническую документацию заводов-изготовителей, материалы и изделия Заказчик или генеральный подрядчик передают монтажной организации в порядке и в сроки, установленные соответствующими правилами и согласованными графиками.
К началу монтажных работ должны быть выполнены в необходимом объеме строительная и технологическая части объекта, а также в соответствии со строительными чертежами — проемы, отверстия, проходы в стенах, перегородках, перекрытиях с установкой в них закладных частей для крепления приборов и средств автоматизации и прокладки трубных и электрических проводок.
Монтаж систем автоматизации производят в соответствии с рабочей документацией с учетом требований предприятий — изготовителей приборов, средств автоматизации агрегатных и вычислительных комплексов, предусмотренных техническими условиями или инструкциями по эксплуатации этого оборудования.
Работы по монтажу систем автоматизации должны осуществляться в две стадии.
На первой стадии выполняются: заготовка монтажных конструкций, узлов и блоков, элементов электропроводок и их укрупнительная сборка вне зоны монтажа; проверка наличия закладных конструкций, проемов, отверстий в строительных конструкциях и элементах зданий, закладных конструкций и отборных устройств на технологическом оборудовании и трубопроводах, наличия заземляющей сети; закладка в сооружаемые фундаменты, стены, полы и перекрытия труб и глухих коробов для скрытых проводок.
На второй стадии выполняются: разметка трасс и установка опорных и несущих конструкций для электрических и трубных проводок, исполнительных механизмов, приборов и т. д.; прокладка трубных и электрических проводок по установленным конструкциям, установка щитов, штативов, пультов, приборов и средств автоматизации, подключение к ним трубных и электрических проводок, индивидуальные испытания.
Смонтированные приборы и средства автоматизации электрической ветви Государственной системы приборов (ГСП), щиты и пульты, конструкции, электрические и трубные проводки, подлежащие заземлению согласно рабочей документации, должны быть присоединены к контуру заземления. При наличии требования предприятий-изготовителей средства агрегатных и вычислительных комплексов должны быть присоединены к контуру специального заземления.
Завершение работ по монтажу средств измерения и автоматизации оформляется актом рабочей комиссии по приемке смонтированного оборудования.
К приемке рабочей комиссией предъявляются системы автоматизации, смонтированные в объеме, предусмотренном рабочей документацией, и прошедшие индивидуальные испытания в соответствии со СНиП
К акту приемки оборудования прилагается производственная документация, оформляемая на протяжении всего периода производства монтажных работ
В системах автоматического управления (САУ) чаще всего выходят из строя пультовые переключатели, датчики, диоды, триоды, проводка вторичной коммутации пультов, особенно в случаях заниженного сечения проводов коммутации, предохранители, цепи вторичной коммутации, исполнительные механизмы, электромагнитные приводы клапанов, защитная аппаратура приводов задвижек и механизма задвижек.
Поэтому нужно проводить ремонт систем автоматического управления, средств измерений и мехатронных систем.
Средний ремонт предусматривает частичную или полную разборку и настройку измерительной, регулирующей или других систем приборов; замену деталей, чистку контактных групп, узлов и блоков.
При ремонте измерительной части средств измерений они обязательно подвергаются поверке.
Капитальный ремонт регламентирует полную разборку прибора или регулятора с заменой деталей и узлов, пришедших в негодность, градуировку, изготовление новых шкал и опробование прибора после ремонта на испытательных стендах с последующей поверкой (государственной или ведомственной).
Капитальный ремонт средств измерения и автоматизации может включать часть работ, предусмотренных при среднем ремонте, и дополнительные работы:
- проверку измерительной схемы средств измерения, регулировку и подгонку показаний прибора по контрольным точкам, подготовку средств измерения для сдачи поверителю;
- разборку и сборку механизмов записи средств измерения, их ревизию, чистку и замену;
- ремонт реле, датчиков, исполнительных механизмов, регуляторов электрической и электронной аппаратуры.
Ремонт средств измерения и автоматизации проводится, как правило, при остановке и ремонте технологического оборудования.
9 Характеристика и эксплуатационные возможности системы управления технологическим процессом объекта газовой промышленности. Архитектура построения системы управления объекта, изученного на практике.
Назначение АСУТП. АСУТП предназначена для выработки к реализации управляющих воздействий на технологический объект управления.
Технологический объект управления (АСУТП) представляет собой совокупность технологического оборудования и реализованного на нем по соответствующим инструкциям или регламентам технологического процесса производства продуктов, полупродуктов, изделий или энергии
При построении средств современной промышленной автоматики (обычно в виде АСУ ТП) используется иерархическая информационная структура с применением на разных уровнях вычислительных средств различной мощности. Примерная общая современная структура АСУ ТП показана на рисунке 3.
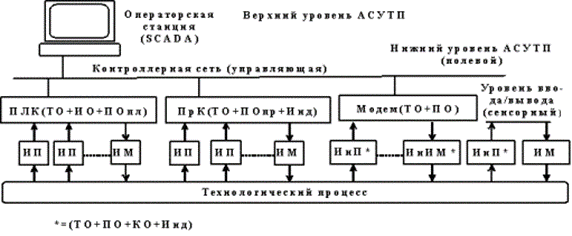
Рисунок 3
ИП - измерительные преобразователи (датчики),
ИМ - исполнительные механизмы,
ПЛК - программируемый логический контроллер,
ПрК - программируемый (настраиваемый) контроллер,
ИнП- интеллектуальные измерительные преобразователи,
ИнИМ - интеллектуальные исполнительные устройства,
Модем - модулятор/демодулятор сигналов,
ТО - техническое обеспечение (аппаратная часть, «железо»),
ИО - информационное обеспечение (базы данных),
ПО - программное обеспечение,
КО - коммуникационное обеспечение (последовательный порт и ПО).
ПОпл - программное обеспечение пользователя,
Опр - программное обеспечение производителя,
В настоящее АСУ ТП обычно реализуются по схемам:
1. 1-уровневой (локальная система), содержащей ПЛК, или моноблочный настраиваемый контроллер (МНК) обеспечивающие индикацию и сигнализацию состояния, контролируемого или регулируемого ТП на передней панели,
2. 2-уровневой (централизованная система), включающих:
1. На нижнем уровне несколько ПЛК с подключенными к ним датчиками и исполнительными устройствами,
2. На верхнем уровне – одна (возможно несколько) операторских (рабочих) станций (автоматизированных рабочих мест (АРМ) оператора).
Обычно рабочая станция или АРМ - это ЭВМ в специальном промышленном исполнении, со специальным программным обеспечением, – системой сбора и визуализации данных (SCADA-системы).
Типовая функциональная схема одноуровневой АСУ ТП показана на рисунке 4.
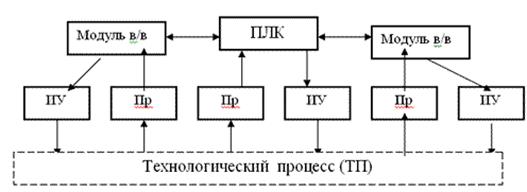
Рисунок 4
К технологическим объектам управления относятся:
- технологические агрегаты и установки (группы станков), реализующие самостоятельный технологический процесс;
- отдельные производства (цехи, участки), если управление этим производством носит, в основном, технологический характер, то есть заключается в реализации рациональных режимов работы взаимосвязанного технологического оборудования (агрегатов, участков).
Совместно функционирующие ТОУ и управляющая ими АСУТП образуют автоматизированный технологический комплекс (АТК). В машиностроении и других дискретных производствах в качестве АТК выступают гибкие производственные системы (ГПС).
Термины АСУТП, ТОУ и АТК должно употребляться только в приведенных сочетаниях. Совокупность других систем управления с управлением ими технологическим оборудованием не является АТК. Система управления в других случаях (не в АТК) не является АСУТП и т.д. АСУТП - это организационно-техническая система управления объектом в целом в соответствии с принятым критерием (критериями) управления, в которой сбор и обработка необходимой информации осуществляется с применением средств вычислительной техники.
Критерий управления в АСУТП - это соотношение, характеризующее степень достижения целей управления (качество функционирования технологического объекта управления в целом) и принимающее различные числовые значения в зависимости от используемых управляющих воздействий. Отсюда следует, что критерий обычно является технико-экономическим (например, себестоимость выходного продукта при заданном его качестве, производительность ТОУ при заданном качества выходного продукта и т.п.) или техническим показателем (параметра процесса, характеристики выходного продукта).