Добавлен: 05.12.2023
Просмотров: 120
Скачиваний: 12
ВНИМАНИЕ! Если данный файл нарушает Ваши авторские права, то обязательно сообщите нам.
; резко повышается при перегреве расплава. При затвердевании и последующем охлаждении растворимость газов уменьшается, в результате их выделения в отливке могут образоваться газовые раковины и поры.
Растворимость газов зависит от химического состава сплава, температуры заливки, вязкости сплава и свойств литейной формы.
Ликвация – неоднородность химического состава сплава в различных частях отливки. Ликвация образуется в процессе затвердевания отливки, из-за различной растворимости отдельных компонентов сплава в его твердой и жидкой фазах. В сталях и чугунах заметно ликвируют сера, фосфор и углерод.
Различают ликвацию зональную, когда различные части отливки имеют различный химический состав, и дендритную, когда химическая неоднородность наблюдается в каждом зерне.
4. Перечислите виды листового проката. Перечислите прокатные операции технологического процесса получения листового проката, начиная с указания исходного материала
Ответ
По технологии изготовления листовой прокат делится на прокат листовой горячекатаный, сортамент которого нормируется требованиями ГОСТ 19903-74 и прокат листовой холоднокатаный выпускаемый в соответствие с сортаментом ГОСТ 19904-90.
Листовой металл производится в листах толщиной 0,4 – 160 мм или в рулонах толщиной 1,2 – 12 мм для горячекатаного проката. Для холоднокатаной листовой стали в листах толщиной 0,35 – 5 мм и в рулонах 0,35 – 3,5 мм.
Листовой прокат по точности изготовления выпускается:
Оба вида проката подразделяются:
по плоскостности на: нормальной (ПН), улучшенной (ПУ), высокой (ПВ) и особо высокой (ПО);
по характеру кромки делится – на обрезную (О) и необрезную (НО) кромку;
по качеству отделки поверхности листовой металлопрокат разделяется на особо высокой (I), высокой (II) и повышенной (III) отделки для холоднокатаного; повышенной (III) и обычной (IV) отделки для горячего проката.
Листовой металл горячекатаный производится в листах шириной 500 – 3800 мм, длиной 710 – 12000 мм, а также в рулонах шириною 500 – 2200 мм. Холоднокатаный прокат производится в листах шириной 500 – 2350 мм и длиной 1000 – 6000 мм, ширина выпускаемых рулонов 500 – 2300 мм. Масса рулона должна лежать в пределах 1500 – 20000 кг.
Прокат листовой толщиной до 50 мм производится из катаных или непрерывнолитых заготовок. Листы толщиной свыше 50 мм катают непосредственно из слитков или кованых слябов.
В технологический процесс входят следующие основные операции:
Изделия металлопроката листового могут выглядеть как рулон, полоса, штрипс. Листовой прокат используется в основном в целях промышленного производства, где для скрепления готовых компонентов применяется производство сварочных работ, как пример – автомобилестроение и соответственно такой прокат называется – автолист.
Отдельная категория горячекатаного листа – сталь листовая для судостроения (судосталь). К такому листовому прокату предъявляются повышенные требования по химическим и механическим свойствам.
Толстолистовая сталь применяется в основном в машиностроении для изготовления оснастки и деталей машин и механизмов
Тонколистовая холоднокатаная сталь обычно подлежит дальнейшей обработке, в частности горячим цинкованием или нанесением полимерного покрытия. Такая сталь штампуется или прокатывается в профнастил для увеличения жесткости и получения высококачественного кровельного покрытия.
Изделия, относящиеся к категории металлопроката, могут изготавливаться методом горячей и холодной прокатки на прокатных станах металлургических заводов по следующей технологической схеме (рис. 6).
Рисунок 6 Технологическая схема получения металлопроката
5. По эскизу готовой детали (рис.) разработайте схему технологического процесса получения поковки способом горячей объемной штамповки на паровоздушном молоте. При выполнении работы: 1) описать сущность горячей объемной штамповки и указать область ее применения; 2) изобразить схему молота и описать его работу; 3) установить температурный интервал штамповки и способ нагрева заготовки
; 4) составить чертеж поковки и определить ее высоту; 5) перечислить все технологические отходы, определить объем, массу и длину исходной заготовки (диаметр исходной заготовки указан на чертеже задания); 6) выбрать переходы штамповки и привести эскиз инструмента; 7) перечислить операции технологического процесса, необходимые для получения данной поковки, которые выполняют в кузнечном цехе; 8) описать механизацию технологического процесса штамповки.
Рис. 7
Решение
Сущность метода горячей объемной штамповки
Горячая объёмная штамповка – это вид обработки материалов давлением, при котором формообразование поковки из нагретой заготовки осуществляют с помощью специального инструмента – штампа. Течение металла ограничивается поверхностями плоскостей, изготовленных в отдельных частях штампа, так что в конечный момент штамповки они образуют единую замкнутую плоскость (ручей) по конфигурации поковки.
В качестве заготовок для горячей штамповки в подавляющем большинстве случаев применяют прокат круглого квадратного, прямоугольного профилей, а также периодический. При этом прутки разрезают на отдельные заготовки, хотя иногда штампуют и от прутка с последующим отделением поковки непосредственно на штамповочной машине. Заготовки отрезают от прутка различными способами: на кривошипных пресс-ножницах, газовой резкой и т д.
По сравнению с ковкой штамповка имеет ряд преимуществ. Горячей объёмной штамповкой можно получать без напусков поковки сложной конфигурации, которые ковкой изготовить без напусков нельзя, при этом допуски на штамповочную поковку в 3 – 4 раза меньше, чем на кованную. В следствие этого значительно сокращается объём последующей механической обработки, штамповочные поковки обрабатывают только в местах сопряжения с другими деталями, и эта обработка может сводиться только к шлифованию.
Производительность штамповки значительно выше – составляет десятки и сотни штамповок в час.
В то же время штамповочный инструмент – штамп – дорогостоящий инструмент и является пригодным только для изготовления какой-то одной, конкретной поковки. В связи с этим штамповка экономически целесообразна лишь при изготовлении достаточно больших партий одинаковых поковок.
Кроме того, для объёмной штамповки поковок требуется гораздо больше усилий деформирования, чем для ковки таких же поковок. Поковки массой в несколько сот килограммов для штамповки считается крупными. В основном штампуют поковки массой 20 – 30 килограмм. Но благодаря созданию мощных машин в отдельных случаях штампуют поковки массой до трёх тонн.
Горячей объёмной штамповкой изготовляют заготовки для ответственных деталей автомобилей, тракторов, сельскохозяйственных машин, самолётов, железнодорожных вагонов, станков и так далее.
Конфигурация поковок чрезвычайно разнообразна, в зависимости от неё поковки обычно разделяются на группы. Например, штампованные поковки, можно разделить на 2 группы: удлинённой формы, характеризующиеся большим отношением длинны к ширине, и круглые или квадратные в плане.
Наличие большого разнообразия форм и размеров штампованных поковок, а также сплавов, из которых их штампуют, обуславливает существование различных способов штамповки.
Так как характер течения металла в процессе штамповки определяется типом штампа, то этот признак можно признать основным для классификации способов штамповки. В зависимости от типа штампа выделяют штамповку в открытых штампах и в закрытых штампах.
Штамповка в открытых штампах характеризуется переменным зазором между подвижным и неподвижным частями штампа. В этот зазор вытекает заусенец (облой), который закрывает выход из полости штампа и заставляет металл целиком заполнить всю полость. В конечный момент формирования заусенец выжимаются излишки металла, находящийся в плоскости, что позволяет не предъявлять особо высоких требований к точности заготовок по массе. Заусенец затем обрезается в специальных штампах. Штамповкой в открытых штампах получают поковки всех типов.
Штамповка в закрытых штампах характеризуется тем, что полость штампа в процессе деформирования остаётся закрытой. Зазор между подвижной и не подвижной частями штампа при этом постоянный и большой, так что образование заусенца в нём не предусматривается. Устройство таких штампов зависит от типа машины, на которых штампуют. Закрытый штамп может быть с одной или двумя взаимно перпендикулярными плоскостями разъёма, то есть состоять из трёх частей.
При штамповке в закрытых штампах надо строго соблюдать равенство объёмов заготовки и поковки, иначе при недостатке металла не заполняются углы полости штампа, а при избытке размер поковки по высоте будет больше нужного. Значит, процесс получения заготовки усложняется, поскольку отрезка заготовок должна сопровождаться высокой точностью. Существенным преимуществом штамповки в закрытых штампах является уменьшение расхода металла, поскольку нет отхода заусениц. Поковки, полученные в закрытых штампах, имеют более благоприятную микроструктуру, так как волокна обтекают контур поковки, а не прорезаются в месте выхода металла заусениц. При штамповке в закрытых штампах металл деформируется в условиях всестороннего неравномерного сжатия при больших зажимающих напряжениях, чем в открытых штампах. Это позволяет получить большие степени деформации и штамповать малопластичные сплавы.
К закрытой штамповке можно отнести штамповку выдавливанием и прошивкой, так как штамп в этих случаях выполняют по типу закрытого и отхода металла заусениц не предусматривает. Деформирование металла при горячей штамповке вдавливанием и прошивкой происходит так же, как при холодном прямом и обратном выдавливании.
Технологический процесс горячей объёмной штамповки
1. Транспортирование заготовки со склада. Для этого используют любой транспорт.
2. Отрезка заготовки выполняется гидравлическими ножницами усилием 10000 кН при температуре 700 – 4500С.
3. Наладка оборудования. Ручей штампа смазывают специальным раствором.
4. Выборочный контроль размеров заготовки. Проверяют размеры заготовки с помощью измерительных средств.
5. Нагрев. Нагрев производится в печи с газопламенным способом нагрева до температуры 13000С.
6. Горячая объемная штамповка производится после нагрева заготовки в печи до температуры 13000С, а затем подается на ковочные вальцы для предварительной штамповки, после чего получившуюся заготовку кладут в ручей при температуре 1250 – 8000С.
7. После объемной штамповки идет операция обрезки заусенца. Эту операцию производят специальными обрезными прессами с обрезными штампами (например, пресс КА 9536 усилием 4000 кН).
8. Для стали 45 в роли термообработки можно произвести отжиг при температуре 850 – 870 0С, охлаждение с печью. Отжиг снижает твердость и прочность, улучшает обрабатываемость резанием. Измельчая зерно, снижая внутренние напряжения и уменьшая структурную неоднородность, способствует повышению пластичности и вязкости.
9. Правка поковки. Эту операцию выполняют для устранения искривлений осей и искажения поперечных сечений, образующихся при затруднённом извлечении поковок из штампа, после обрезки заусенца, а также после термической обработки. Крупные поковки и поковки из высокоуглеродистых и высоколегированных сталей правят в горячем состоянии, либо в чистовом ручье штампа, либо на обрезном прессе, либо на отдельной машине. Мелкие поковки можно править в холодном состоянии после термической обработки на специальном оборудовании (обычно на фрикционных молотах с доской), в правочных штампах, ручьи которых изготовляют по чертежу холодной поковки.
10. Очистка поковок от окалины. Очистка обеспечивает условие работы режущего инструмента при последующей механической обработке, а также контроль поверхности поковок. Очистку производят несколькими способами: в барабанах, дробью, травлением.
Растворимость газов зависит от химического состава сплава, температуры заливки, вязкости сплава и свойств литейной формы.
Ликвация – неоднородность химического состава сплава в различных частях отливки. Ликвация образуется в процессе затвердевания отливки, из-за различной растворимости отдельных компонентов сплава в его твердой и жидкой фазах. В сталях и чугунах заметно ликвируют сера, фосфор и углерод.
Различают ликвацию зональную, когда различные части отливки имеют различный химический состав, и дендритную, когда химическая неоднородность наблюдается в каждом зерне.
4. Перечислите виды листового проката. Перечислите прокатные операции технологического процесса получения листового проката, начиная с указания исходного материала
Ответ
По технологии изготовления листовой прокат делится на прокат листовой горячекатаный, сортамент которого нормируется требованиями ГОСТ 19903-74 и прокат листовой холоднокатаный выпускаемый в соответствие с сортаментом ГОСТ 19904-90.
Листовой металл производится в листах толщиной 0,4 – 160 мм или в рулонах толщиной 1,2 – 12 мм для горячекатаного проката. Для холоднокатаной листовой стали в листах толщиной 0,35 – 5 мм и в рулонах 0,35 – 3,5 мм.
Листовой прокат по точности изготовления выпускается:
-
повышенной (А) или нормальной (Б) точности для горячекатаного листа; -
высокой, повышенной и нормальной толщины (ВТ, АТ и БТ), ширины (ВШ, АШ и БШ) и длины (ВД, АД и БД) соответственно, для холоднокатаной стали.
Оба вида проката подразделяются:
по плоскостности на: нормальной (ПН), улучшенной (ПУ), высокой (ПВ) и особо высокой (ПО);
по характеру кромки делится – на обрезную (О) и необрезную (НО) кромку;
по качеству отделки поверхности листовой металлопрокат разделяется на особо высокой (I), высокой (II) и повышенной (III) отделки для холоднокатаного; повышенной (III) и обычной (IV) отделки для горячего проката.
Листовой металл горячекатаный производится в листах шириной 500 – 3800 мм, длиной 710 – 12000 мм, а также в рулонах шириною 500 – 2200 мм. Холоднокатаный прокат производится в листах шириной 500 – 2350 мм и длиной 1000 – 6000 мм, ширина выпускаемых рулонов 500 – 2300 мм. Масса рулона должна лежать в пределах 1500 – 20000 кг.
Прокат листовой толщиной до 50 мм производится из катаных или непрерывнолитых заготовок. Листы толщиной свыше 50 мм катают непосредственно из слитков или кованых слябов.
В технологический процесс входят следующие основные операции:
-
подача слябов со склада к нагревательным печам; -
нагрев; -
подача к рабочей клети стана и прокатка в несколько проходов (пропусков между валками), причем в первые проходы для получения листов требуемой ширины сляб иногда подается в валки поперек или под углом; -
правка на роликовых правильных машинах; охлаждение на холодильниках; контроль и разметка; -
обрезка продольных кромок; -
обрезка концов; -
разрезка на листы определенной длины; -
термическая обработка (по требованию заказчика или обязательно по технологии); -
отправка на склад готовой продукции.
Изделия металлопроката листового могут выглядеть как рулон, полоса, штрипс. Листовой прокат используется в основном в целях промышленного производства, где для скрепления готовых компонентов применяется производство сварочных работ, как пример – автомобилестроение и соответственно такой прокат называется – автолист.
Отдельная категория горячекатаного листа – сталь листовая для судостроения (судосталь). К такому листовому прокату предъявляются повышенные требования по химическим и механическим свойствам.
Толстолистовая сталь применяется в основном в машиностроении для изготовления оснастки и деталей машин и механизмов
Тонколистовая холоднокатаная сталь обычно подлежит дальнейшей обработке, в частности горячим цинкованием или нанесением полимерного покрытия. Такая сталь штампуется или прокатывается в профнастил для увеличения жесткости и получения высококачественного кровельного покрытия.
Изделия, относящиеся к категории металлопроката, могут изготавливаться методом горячей и холодной прокатки на прокатных станах металлургических заводов по следующей технологической схеме (рис. 6).
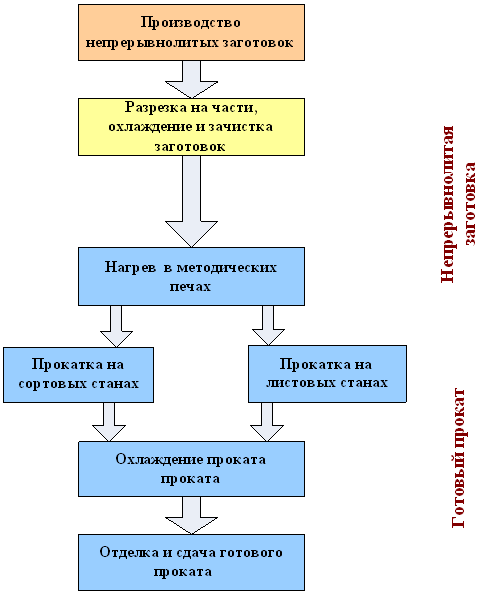
Рисунок 6 Технологическая схема получения металлопроката
5. По эскизу готовой детали (рис.) разработайте схему технологического процесса получения поковки способом горячей объемной штамповки на паровоздушном молоте. При выполнении работы: 1) описать сущность горячей объемной штамповки и указать область ее применения; 2) изобразить схему молота и описать его работу; 3) установить температурный интервал штамповки и способ нагрева заготовки
; 4) составить чертеж поковки и определить ее высоту; 5) перечислить все технологические отходы, определить объем, массу и длину исходной заготовки (диаметр исходной заготовки указан на чертеже задания); 6) выбрать переходы штамповки и привести эскиз инструмента; 7) перечислить операции технологического процесса, необходимые для получения данной поковки, которые выполняют в кузнечном цехе; 8) описать механизацию технологического процесса штамповки.
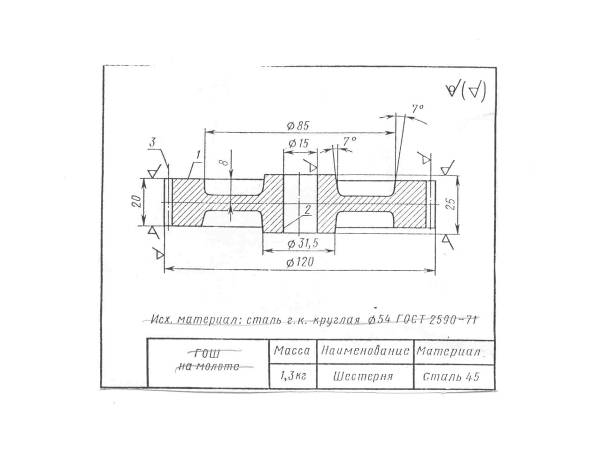
Рис. 7
Решение
Сущность метода горячей объемной штамповки
Горячая объёмная штамповка – это вид обработки материалов давлением, при котором формообразование поковки из нагретой заготовки осуществляют с помощью специального инструмента – штампа. Течение металла ограничивается поверхностями плоскостей, изготовленных в отдельных частях штампа, так что в конечный момент штамповки они образуют единую замкнутую плоскость (ручей) по конфигурации поковки.
В качестве заготовок для горячей штамповки в подавляющем большинстве случаев применяют прокат круглого квадратного, прямоугольного профилей, а также периодический. При этом прутки разрезают на отдельные заготовки, хотя иногда штампуют и от прутка с последующим отделением поковки непосредственно на штамповочной машине. Заготовки отрезают от прутка различными способами: на кривошипных пресс-ножницах, газовой резкой и т д.
По сравнению с ковкой штамповка имеет ряд преимуществ. Горячей объёмной штамповкой можно получать без напусков поковки сложной конфигурации, которые ковкой изготовить без напусков нельзя, при этом допуски на штамповочную поковку в 3 – 4 раза меньше, чем на кованную. В следствие этого значительно сокращается объём последующей механической обработки, штамповочные поковки обрабатывают только в местах сопряжения с другими деталями, и эта обработка может сводиться только к шлифованию.
Производительность штамповки значительно выше – составляет десятки и сотни штамповок в час.
В то же время штамповочный инструмент – штамп – дорогостоящий инструмент и является пригодным только для изготовления какой-то одной, конкретной поковки. В связи с этим штамповка экономически целесообразна лишь при изготовлении достаточно больших партий одинаковых поковок.
Кроме того, для объёмной штамповки поковок требуется гораздо больше усилий деформирования, чем для ковки таких же поковок. Поковки массой в несколько сот килограммов для штамповки считается крупными. В основном штампуют поковки массой 20 – 30 килограмм. Но благодаря созданию мощных машин в отдельных случаях штампуют поковки массой до трёх тонн.
Горячей объёмной штамповкой изготовляют заготовки для ответственных деталей автомобилей, тракторов, сельскохозяйственных машин, самолётов, железнодорожных вагонов, станков и так далее.
Конфигурация поковок чрезвычайно разнообразна, в зависимости от неё поковки обычно разделяются на группы. Например, штампованные поковки, можно разделить на 2 группы: удлинённой формы, характеризующиеся большим отношением длинны к ширине, и круглые или квадратные в плане.
Наличие большого разнообразия форм и размеров штампованных поковок, а также сплавов, из которых их штампуют, обуславливает существование различных способов штамповки.
Так как характер течения металла в процессе штамповки определяется типом штампа, то этот признак можно признать основным для классификации способов штамповки. В зависимости от типа штампа выделяют штамповку в открытых штампах и в закрытых штампах.
Штамповка в открытых штампах характеризуется переменным зазором между подвижным и неподвижным частями штампа. В этот зазор вытекает заусенец (облой), который закрывает выход из полости штампа и заставляет металл целиком заполнить всю полость. В конечный момент формирования заусенец выжимаются излишки металла, находящийся в плоскости, что позволяет не предъявлять особо высоких требований к точности заготовок по массе. Заусенец затем обрезается в специальных штампах. Штамповкой в открытых штампах получают поковки всех типов.
Штамповка в закрытых штампах характеризуется тем, что полость штампа в процессе деформирования остаётся закрытой. Зазор между подвижной и не подвижной частями штампа при этом постоянный и большой, так что образование заусенца в нём не предусматривается. Устройство таких штампов зависит от типа машины, на которых штампуют. Закрытый штамп может быть с одной или двумя взаимно перпендикулярными плоскостями разъёма, то есть состоять из трёх частей.
При штамповке в закрытых штампах надо строго соблюдать равенство объёмов заготовки и поковки, иначе при недостатке металла не заполняются углы полости штампа, а при избытке размер поковки по высоте будет больше нужного. Значит, процесс получения заготовки усложняется, поскольку отрезка заготовок должна сопровождаться высокой точностью. Существенным преимуществом штамповки в закрытых штампах является уменьшение расхода металла, поскольку нет отхода заусениц. Поковки, полученные в закрытых штампах, имеют более благоприятную микроструктуру, так как волокна обтекают контур поковки, а не прорезаются в месте выхода металла заусениц. При штамповке в закрытых штампах металл деформируется в условиях всестороннего неравномерного сжатия при больших зажимающих напряжениях, чем в открытых штампах. Это позволяет получить большие степени деформации и штамповать малопластичные сплавы.
К закрытой штамповке можно отнести штамповку выдавливанием и прошивкой, так как штамп в этих случаях выполняют по типу закрытого и отхода металла заусениц не предусматривает. Деформирование металла при горячей штамповке вдавливанием и прошивкой происходит так же, как при холодном прямом и обратном выдавливании.
Технологический процесс горячей объёмной штамповки
1. Транспортирование заготовки со склада. Для этого используют любой транспорт.
2. Отрезка заготовки выполняется гидравлическими ножницами усилием 10000 кН при температуре 700 – 4500С.
3. Наладка оборудования. Ручей штампа смазывают специальным раствором.
4. Выборочный контроль размеров заготовки. Проверяют размеры заготовки с помощью измерительных средств.
5. Нагрев. Нагрев производится в печи с газопламенным способом нагрева до температуры 13000С.
6. Горячая объемная штамповка производится после нагрева заготовки в печи до температуры 13000С, а затем подается на ковочные вальцы для предварительной штамповки, после чего получившуюся заготовку кладут в ручей при температуре 1250 – 8000С.
7. После объемной штамповки идет операция обрезки заусенца. Эту операцию производят специальными обрезными прессами с обрезными штампами (например, пресс КА 9536 усилием 4000 кН).
8. Для стали 45 в роли термообработки можно произвести отжиг при температуре 850 – 870 0С, охлаждение с печью. Отжиг снижает твердость и прочность, улучшает обрабатываемость резанием. Измельчая зерно, снижая внутренние напряжения и уменьшая структурную неоднородность, способствует повышению пластичности и вязкости.
9. Правка поковки. Эту операцию выполняют для устранения искривлений осей и искажения поперечных сечений, образующихся при затруднённом извлечении поковок из штампа, после обрезки заусенца, а также после термической обработки. Крупные поковки и поковки из высокоуглеродистых и высоколегированных сталей правят в горячем состоянии, либо в чистовом ручье штампа, либо на обрезном прессе, либо на отдельной машине. Мелкие поковки можно править в холодном состоянии после термической обработки на специальном оборудовании (обычно на фрикционных молотах с доской), в правочных штампах, ручьи которых изготовляют по чертежу холодной поковки.
10. Очистка поковок от окалины. Очистка обеспечивает условие работы режущего инструмента при последующей механической обработке, а также контроль поверхности поковок. Очистку производят несколькими способами: в барабанах, дробью, травлением.