Добавлен: 05.12.2023
Просмотров: 2327
Скачиваний: 50
ВНИМАНИЕ! Если данный файл нарушает Ваши авторские права, то обязательно сообщите нам.
СОДЕРЖАНИЕ
1. Безопасные условия труда слесаря и противопожарные мероприятия.
Тема 1: «Плоскостная разметка»
Тема 3: «Правка и рихтовка металла»
Тема 7: «Сверление, зенкование, зенкерование и развёртывание отверстий»
Тема 10: «Пространственная разметка»
Тема 12: «Распиливание и припасовка»
Тема 5: «Резка металла»
Резкой называют процесс разделения заготовки на части заданных размеров и формы. Резку применяют для получения заготовок заданных размеров и формы из сортового и листового проката, а также прорезей и отверстий в заготовках. Современные методы резки обеспечивают высокопроизводительную обработку заготовок практически любых размеров и из материалов с любыми физико-механическими свойствами.
Резка может производиться как вручную, так и механически.
Физическая сущность резки основана на различных способах разрушения материала заготовки в месте реза.
При распиливании и резке на металлорежущих станках сила F, приложенная к режущему клину, направлена под острым углом к обрабатываемой поверхности. Поэтому режущий клин срезает материал и превращает его в стружку. При резке на ножницах сила F, приложенная к режущему клину, перпендикулярна обрабатываемой поверхности. Поэтому инструмент разрезает материал без образования стружки.
Электроискровая резка основана на электрической эрозии (разрушении) материала заготовки. Конденсатор С, включенный в зарядный контур, заряжается через резистор R от источника постоянного тока напряжением 100—200 В. Когда напряжение на электродах (инструменте) и (заготовке) достигнет пробойного, между их ближайшими микровыступами происходит искровой разряд продолжительностью 20—200 мкс. Температура разряда достигает 10 000—12 000 °С. В месте разряда на заготовке мгновенно расплавляется и испаряется элементарный объем материала и образуется лунка. Удаленный материал в виде гранул остается в диэлектрической среде (масле), в которой проходит процесс обработки. Разрядами, следующими непрерывно друг за другом, разрушается весь материал заготовки, находящийся от инструмента на расстоянии 0,01—0,05 мм. Для продолжения процесса обработки электроды необходимо сблизить, что делается автоматически.
При ацетиленокислородной резке металл заготовки в месте реза сначала подогревают ацетиленокислородным пламенем до температуры его воспламенения в кислороде (для стали 1000—1200 °С). Затем в это место направляют струю кислорода и металл начинает гореть. При этом выделяется столько теплоты, что ее достаточно для поддержания непрерывного процесса резки.
Анодно-механическая резка основана на комбинированном разрушении материала заготовки — электрическом, химическом и механическом. Постоянный ток, проходящий в месте реза между заготовкой и инструментом, вызывает электрическую эрозию поверхности заготовки. Образующиеся расплавленные частицы материала выносятся из зоны обработки вращающимся инструментом — диском. Одновременно электролит, подаваемый в зону обработки, под действием электрического тока образует на поверхности заготовки пленки оксидов, которые удаляются тем же вращающимся инструментом.
Инструменты для резки. При распиливании в качестве режущих инструментов применяют ножовочные полотна (для ручной и механической ножовок), ленточные и дисковые пилы. Ножовочные полотна и ленточные пилы представляют собой тонкую ленту из быстрорежущей или легированной (Х6ВФ, В2Ф) стали с мелкими зубьями в виде клиньев на одной или двух сторонах. Ленточные пилы получают путем сгибания ленты в кольцо и спаивания ее концов высокотемпературным припоем. У дисковой пилы зубья расположены на периферии диска. Режущие зубья закаливают до твердости 61 — 64 HRQ. Для того, чтобы инструмент не заклинивал в узком пропиле, его зубья разводят.
При выборе инструмента для распиливания в первую очередь следует учитывать длину пропила и твердость обрабатываемого материала.
При длинных пропилах необходимо выбирать полотна с крупным шагом зубьев, а при обработке тонкостенных заготовок — с мелким. В резании должны одновременно участвовать не менее трех зубьев.
Чем выше твердость обрабатываемого материала, тем больше должен быть угол заострения. Образующаяся в этом случае стружка имеет форму запятой и плотно укладывается в небольшом пространстве. При обработке мягких материалов следует применять инструменты с большим пространством для стружки. Положительный передний угол повышает производительность, так как в этом случае зуб режет, а не скоблит материал заготовки.
Для обработки высокопрочных материалов применяют ножовочные полотна с синтетическими алмазами на рабочей поверхности.
Для резки листового материала применяют режущие инструменты в виде ножей, которые чаще всего выполняются съемными. Ножи бывают с прямолинейными, криволинейными и круглыми (роликовыми и дисковыми) режущими кромками.
При анодно-механической резке в качестве инструмента используют тонкие диски из мягкой стали. На электроискровом станке в качестве инструмента для вырезания применяют непрерывно перемещающуюся проволоку.
Оборудование и приспособления для резки. В условиях инструментального цеха небольшие заготовки режут ручной ножовкой. Ножовочное полотно крепят в рамке так, чтобы зубья были направлены от рукоятки.
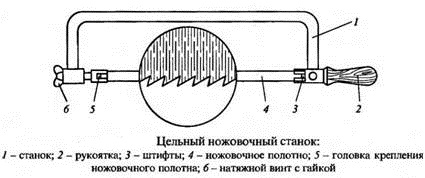
Рисунок 4. Ручная ножовка
Ручные рычажные ножницы предназначены для резки листового материала. В инструментальных цехах используют небольшие переносные ножницы. На них можно разрезать листовую сталь толщиной до 4 мм, алюминий и латунь — до 6 мм.
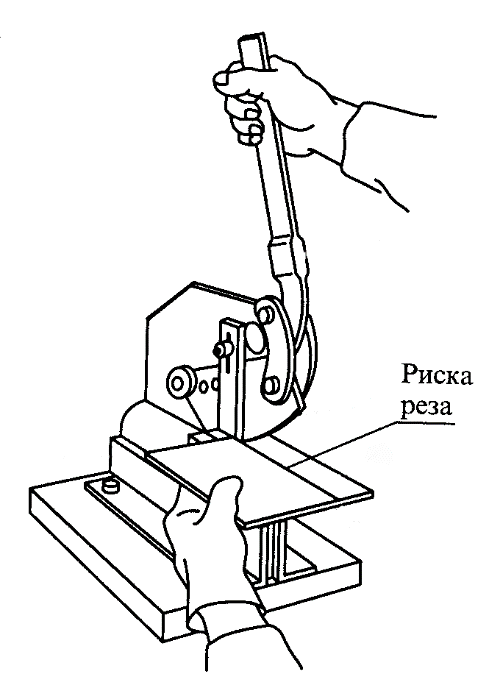
Рисунок 5. Рычажные ножницы
Ручные ножницы предназначены для резки листового материала, изготовления заготовок с криволинейным контуром, вырезания в заготовках отверстий сложного контура. Для прямолинейного реза применяют ножницы с прямыми широкими ножами. Если верхняя режущая кромка расположена справа относительно нижней, то ножницы называются правыми, а если слева — левыми. Для получения наружных криволинейных резов используют ручные ножницы с изогнутыми широкими ножами. Вырезание внутренних криволинейных контуров производят ножницами с узкими изогнутыми ножами.
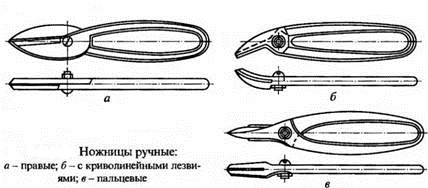
Рисунок 6. Ручные ножницы
Механическую резку листового материала выполняют ручными электроножницами, виброножницами, а также на роликовых, многодисковых и листовых ножницах.
Последовательность и приемы работ при резке. Резке предшествует разметка. Затем выбирают метод резки, оборудование и инструмент.
Большое значение для качественной обработки имеет правильное выполнение приемов резки. Расположение заготовки и инструмента при ручной резке должно быть таким, чтобы разметочная риска постоянно была доступна для наблюдения. При большой длине реза нажим на ножовку увеличивают, при малой — уменьшают. Так как зубья ножовки особенно легко ломаются в начале и в конце реза, в эти моменты нажим на нее должен быть минимальным.
Ручные ножницы при резке следует раскрывать на 2/3 длины режущих кромок. В этом случае они легко захватывают заготовку и хорошо режут. Плоскость резания всегда должна быть перпендикулярна разрезаемой поверхности заготовки. Перекос ведет к заеданию, смятию кромок и появлению заусенцев.
Большое значение имеет правильная регулировка инструмента. Так, при слабом натяжении ножовочного полотна в ручной ножовке рез получается косым. Большой зазор между ножами ведет к образованию заусенцев. Появление заусенцев при правильно отрегулированных ножах является сигналом об их затуплении.
Выполняя резку ручной ножовкой, следует стоять свободно и прямо, вполоборота к тискам.
Техника безопасности при резке металла:
-
Резание необходимо производить в рукавицах во избежание пореза рук. -
Разрезание следует производить острозаточенными ножницами. -
Не держать левую руку близко к ножницам и кусачкам, чтобы пальцы не попали под лезвие. -
Подавать ножницы и кусачки товарищу нужно ручками от себя, а класть на стол ручками к себе. -
Если кусачками отрезается небольшой кусок проволоки, откусываемую часть направлять в -
сторону защитного экрана верстака. -
Необходимо следить за состоянием оси-винта ножниц. Если ножницы начинают «мять» металл, -
нужно слегка подтянуть винт. -
Следить за положением пальцев левой руки, поддерживая лист снизу. -
Оберегать руки от ранения о режущие кромки или заусенцы на металле. -
Не сдувать опилки и не удалять их руками во избежание засорения глаз или ранения рук. -
При резании материала толщиной более 0,5мм (или при затрудненном нажатии на ручки ножниц) -
необходимо одну из ручек прочно закрепить в тисках. -
Не загромождать рабочее место ненужными инструментами и деталями.
Тема 6: «Опиливание металла»
Опиливание — это операция по удалению с поверхности заготовки слоя материала при помощи режущего инструмента — напильника, целью которой является придание заготовке заданных формы и размеров, а также обеспечение заданной шероховатости поверхности. В большинстве случаев опиливание производят после рубки и резания металла ножовкой, а также при сборочных работах для пригонки детали по месту. В слесарной практике опиливание применяется для обработки следующих поверхностей:
-
плоских и криволинейных; -
плоских, расположенных под наружным или внутренним углом; -
плоских параллельных под определенный размер между ними; -
фасонных сложного профиля.
Кроме того, опиливание используется для обработки углублений, пазов и выступов.
Различают черновое и чистовое опиливание. Обработка напильником позволяет получить точность обработки деталей до 0,05 мм, а в отдельных случаях и более высокую точность. Припуск на обработку опиливанием, т. е. разница между номинальным размером детали и размером заготовки для ее получения, обычно небольшой и составляет от 1,0 до 0,5 мм.
Инструменты, применяемые при опиливании:
Основными рабочими инструментами, применяемыми при опиливании, являются напильники, рашпили и надфили.
Напильники представляют собой стальные закаленные бруски, на рабочих поверхностях которых нанесено большое количество насечек или нарезок, образующих режущие зубья напильника. Эти зубья обеспечивают срезание с поверхности заготовки небольшого слоя металла в виде стружки. Напильники изготавливают из инструментальных углеродистых сталей марок У10, У12, У13и инструментальных легированных сталей марок ШХ6, ШХ9, ШХ12.
Насечки на поверхности напильника образуют зубья, причем чем меньше насечек на единицу длины напильника, тем крупнее зубья. По виду насечек различают напильники с одинарной (рис. 7, а), двойной (перекрестной) (рис. 7, б) и рашпильной (рис. 7, в) насечками.
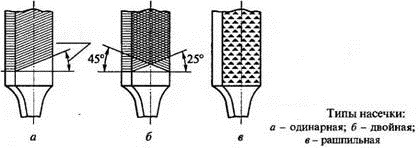
Рисунок 7. Типы насечки.
Напильники с одинарной насечкой срезают металл широкой стружкой, равной всей длине зуба, что требует приложения больших усилий. Такие напильники