Файл: Контрольная работа По дисциплине Материаловедение студент группы нддбз 183 Наумов М. В.docx
ВУЗ: Не указан
Категория: Не указан
Дисциплина: Не указана
Добавлен: 06.12.2023
Просмотров: 25
Скачиваний: 1
ВНИМАНИЕ! Если данный файл нарушает Ваши авторские права, то обязательно сообщите нам.
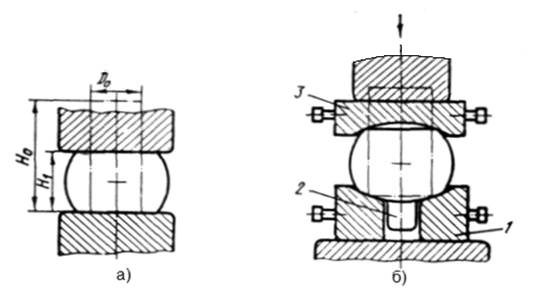
Рис. 4.1. Схемы осадки: а – плоскими бойками, б – слитка с хвостовиком: 1, 3 – плиты, 2 – хвостовик слитка.
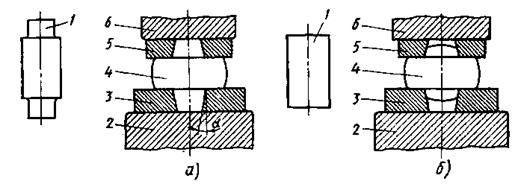
Рис. 4.2. Схемы осадки в подкладных кольцах: а – с предварительной оттяжкой хвостовиков, б – с затеканием металла в отверстия колец; 1, 4 – заготовки до и после осадки; 2, 6 – нижний и верхний бойки; 3, 5 – нижнее и верхнее кольца.
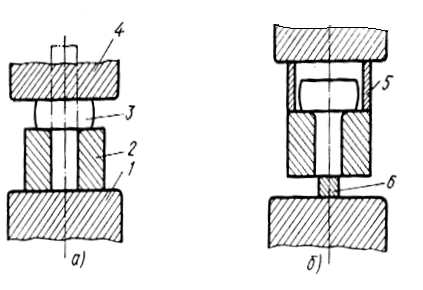
Рис. 4.3. Схемы высадки в штампе (а) и удаление высаженной поковки (б): 1, 4 – нижний и верхний байки; 2, 5 – кольца; 3 – заготовка; 6 – подкладка.
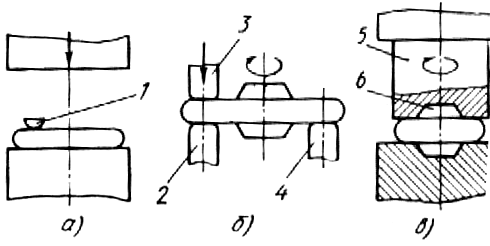
Рис. 4.4. Схемы осадки разгонкой: а – полукруглой раскаткой; б – бойками; в – узким вырезным бойком; 1 – раскатка; 2, 3 – нижний и верхний бойки; 4 – подставка; 5 – узкий боек; 6 – вырез под бобышку.
Протяжка – это кузнечная операция, заключающаяся в удлинении заготовки (или ее части) за счет уменьшения площади поперечного сечения (рис. 4.5) и являющаяся основной формообразующей операцией при ковке гладких, ступенчатых и коленчатых валов, поковок типа шатунов и т. п. При протягивании последовательно деформируют отдельные участки заготовки с кантовкой вокруг оси и подачей вдоль нее (при этом бойки не перекрывают заготовку целиком).
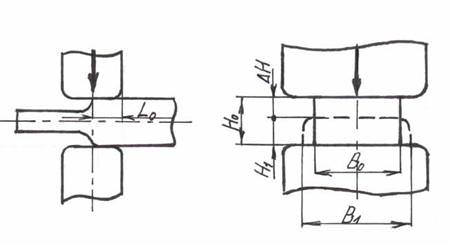
Рис. 4.5. Схема изменения размеров заготовки при протяжке.
Прошивка является основной кузнечной операцией, при которой в заготовке получают отверстие или углубление. Она осуществляется с помощью специального инструмента − прошивня (пуансона, дорна). Заготовку перед прошивкой обязательно осаживают. Основными способами прошивки являются: прошивка сплошным прошивнем, прошивка на подкладном кольце, прошивка пустотелым прошивнем.
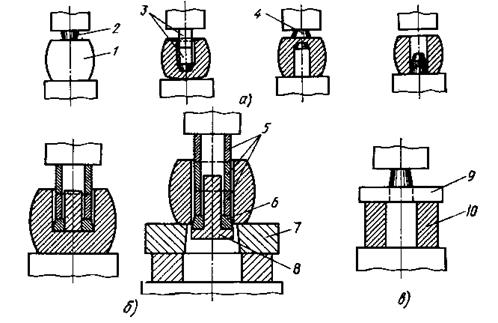
Рис. 4.6. Схемы образования отверстий прошивкой сплошным (а) и полым (б) прошивнями и пробивкой сплошным прошивнем (в): 1, 9 – заготовки; 2, 4, 6 – прошивни; 3, 5 – надставки; 7, 10 – кольца; 8 – отход
Отрубка − это кузнечная операция, в результате которой происходит полное отделение части заготовки путем внедрения в нее деформирующего инструмента (топора, зубила). Отрубку применяют для разделения прутков и болванок на мерные заготовки, удаления концевых излишков на поковках, прибыльной и донной частей слитка. Отрубку под молотами и прессами осуществляют только в горячем состоянии заготовок по одному из нижеследующих способов.
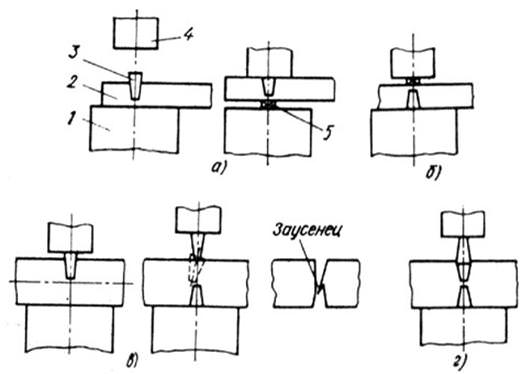
Рис. 4.7. Схемы отрубки заготовки: а − с одной стороны топором и квадратом, б − с одной стороны топором и квадратом с кантовкой заготовки на 180°, в − с двух сторон без оставления перемычки, г − с двух сторон с оставлением перемычки: 1, 4 − нижний и верхний бойки, 2 – заготовка, 3 – топор, 5 – просечка
Гибка – операция, при которой исходной заготовке придается изогнутая форма по заданному контуру. Процесс гибки сопровождается изменением формы поперечного сечения заготовки за счёт растяжения (утяжки) наружных слоев металла и сжатия внутренних (рис.4.8).
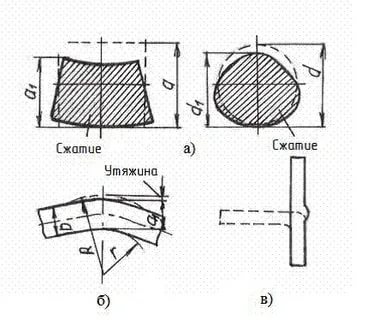
Рис. 4.8. Схема к расчету длины исходной заготовки при гибке
Закручивание − операция, с помощью которой одну часть заготовки поворачивают по отношению к другой на определённый угол (рис. 4.9).
Закручивание применяют при изготовлении коленчатых валов, крупных свёрл, бурильных инструментов и т. п. Операция закручивания сопровождается некоторым уменьшением длины шейки и увеличением её диаметра. Чтобы избежать образования трещин и разрывов, закручиваемая часть должна быть равномерно прогрета до максимально допустимой температуры, угол закручивания должен быть выбран возможно меньшим (для коленчатых валов не более 60° и в крайнем случае 90°), после закручивания необходимо медленное охлаждение.
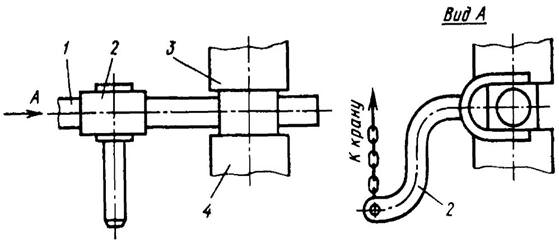
Рис. 4.9. Схемы гибки: 1 – упор, 2 – заготовка, 3, 4 – верхний, нижний байки
-
Особенности получения отливок из титановых сплавок
Титан — молодой металл. Он был открыт в конце 18 века. Титан обладает высокой температурой плавления (1670 °C), малым удельным весом (4.5 г/см3) и высокой прочностью и коррозионной стойкостью.
Высокая реакционная способность титана не позволяет проводить процесс плавления его в атмосфере воздуха, так как в расплавленном состоянии он активно взаимодействует с кислородом и азотам. Первоначально плавку титана и его сплавов вели в атмосфере аргона и гелия, позже появились вакуумные печи, которые в настоящее время являются основным типом плавильного оборудования. Для получения фасонных отливок из титана применяют вакуумные электродуговые гарнисажные плавильно-литейные установки, в которых совмещены процессы плавления металла, приготовления расплава, заливки литейных форм и формирования отливки (см. рис. 5).
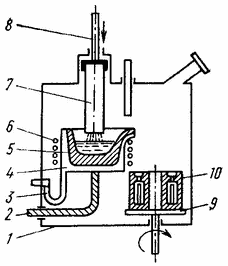
Рис. 5. Схема вакуумно-дуговой печи с расходуемым электродом для плавки титановых сплавов:
1 — вакуумная камера, 2 — электрическим кабель, 3 —шланги водяного охлаждения.
4 — водоохлаждаемый тигель, 5 — гарнисаж, б — соленоид, 7 — расходуемый электрод, 8 — держатель, 9 — вращающийся стол, 10 — литейная форма
Расплавленный титан реагирует практически со всеми известными огнеупорными материалами (оксидами алюминия, магния, кремния и др.), что затрудняет выбор удовлетворительного материала для плавильных тиглей. В гарнисажной печи расплавленный титан находится в контакте со слоем твердого титана толщиной 5—50 мм, называемым гарнисажем и постоянно поддерживаемым на стенках и дне водоохлаждаемого тигля. При вакуумной гарнисажной плавке исключается взаимодействие расплава с атмосферой и материалом тигля, что повышает однородность металла и предупреждает появление в отливке тугоплавких включений. Вакуумная дуговая печь (рис. 8.4) с расходуемым электродом имеет вакуумную камеру 1, в которой расположен медный водоохлаждаемый тигель 4 со шлангами водяного охлаждения 3 и электрическим кабелем 2. Для фокусирования дуги и перемешивания ванны жидкого металла служит расположенный вокруг тигля соленоид 6. Футеровкой тигля служит гарнисаж 5. Расходуемый электрод 7, прикрепленный к держателю 8, изготовляют из сплава, подлежащего плавлению.
После расплавления расходуемого электрода печь поворачивают и производят заливку расплава во вращающуюся на столе 9 форму 10, Под действием центробежных сил расплав хорошо заполняет форму, отливка получается плотной
, без газовых раковин. Прибыли устанавливают не на верхнюю, а на боковую часть питаемого узла, при этом металл под действием центробежных сил двигается от прибыли к отливке.
Литейные формы, изготовленные из обычно применяемых огнеупорных материалов, не могут быть применены для получения отливок из титана по отмеченным ранее причинам. Широко распространены графитовые формы. Их изготовляют из смесей, в состав которых входят в качестве основы графит, в качестве связующего — смолы, пеки. Смеси уплотняют на встряхивающих или прессовых машинах под давлением 0,2—0,8 МПа. Изготовленные формы после выдержки на воздухе от 8 ч до 3 сут подвергают сушке при температуре 120°С и обжигу в восстановительной атмосфере при 700—980 °С в течение 1—24 ч. При этой температуре связующее коксуется и из формы практически полностью удаляются все летучие вещества.
Применяются и оболочковые графитовые формы с фенолоформальдегидной смолой в качестве связующего. Мелкие сложные тонкостенные отливки из титановых сплавов получают в неразъемных формах, изготовленных по выплавляемым моделям. В состав суспензии входит высокодисперсный графитовый порошок и связующее на основе фенолоформальдегидных смол, в качестве обсыпочного материала — зернистый графит.
В настоящее время разрабатываются процессы изготовления форм на основе использования обычных огнеупорных материалов (Al2O3, MgO) с применением защитных углеродных, карбидных и металлических покрытий, повышающих инертность форм к расплавленному титану и его сплавам.