Добавлен: 06.12.2023
Просмотров: 142
Скачиваний: 4
ВНИМАНИЕ! Если данный файл нарушает Ваши авторские права, то обязательно сообщите нам.
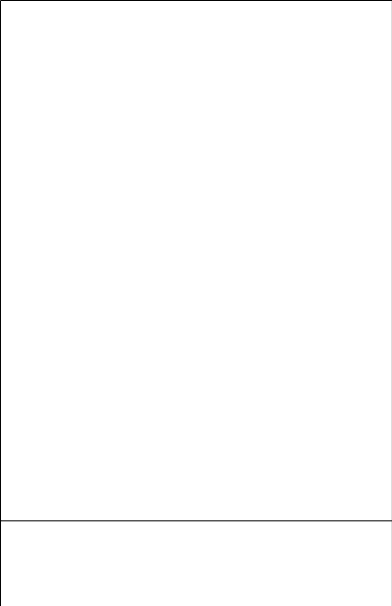
Содержание
Введение | 5 |
1Особенности конструкции автосцепного оборудования | 6 |
2Техническое обслуживание и ремонт автосцепного оборудования | 12 |
3Техническая и технологическая документация при ремонте автосцепного оборудования | 18 |
4Требования техники безопасности и охраны труда | 20 |
Заключение | 24 |
Списокиспользованныхисточников Приложение А Карта эскиза автосцепного оборудования Приложение Б Карта деффектацииавтосцепного оборудования | 25 26 28 |
| |
Введение
Железная дорога, как и любое другое предприятие или завод имеетсвою ремонтную службу, потому что без этого важного звена не возможна перевозка грузов. Выполнить качественный ремонт локомотива не сможет тот, кто непосредственно ведет поезд или осуществляет управление движения этого поезда. Одной из значимых профессий на дороге является слесарь по ремонту подвижного состава. Это тот, кто непосредственно осуществляет, обслуживание и ремонт локомотивов
Слесарные работы выполняются главным образом при сборке машин на промышленных предприятиях, а также в процессе ремонта, сборки и регулировки машин и их узлов на ремонтных предприятиях, а иногда на месте работы машины.
Во время производственной практики происходит закрепление и конкретизация результатов теоретического учебно – практического обучения, приобретение студентами умения и навыков практической работы по присваиваемой квалификации и избранной специальности или профессии.
Производственная практика, пройденная учащимся, оценивается в ряду сданных ими экзаменов и зачётов.
Назначение и конструкция детали. Условия работы детали
Парк подвижного состава железнодорожного транспорта характеризуется многообразием типов и конструкций вагонов, используемых в перевозочном процессе грузов и пассажиров. Условия эксплуатации вагонов связаны со значительными статическими и динамическими нагрузками, а в отдельных случаях – с воздействием высоких и низких температур перевозимого груза, повышенной влажности, агрессивных сред на конструкцию вагонов. При малой дальности перевозок значительно возрастает интенсивность ведения погрузочно-разгрузочных работ, как правило, с использованием различных средств механизации. Таким образом, многофункциональное и интенсивное использование вагонов железнодорожного транспорта требует их качественного технического обслуживания и ремонта квалифицированными специалистами.
Ударно – тяговые приборы предназначены для сцепления вагонов между собой и с локомотивом, удержания их на определенном расстоянии друг от друга, восприятия, передачи и смягчения действия в поезде и при маневрах.
Современным ударно – тяговым прибором является автосцепное устройство, выполняющее основные функции ударных и тяговых приборов.
Автосцепка СА – 3 обеспечивает:
– автоматическое сцепление при соударении вагонов;
– автоматическое запирание замка у сцепленных автосцепок;
– расцепление подвижного состава без захода человека между вагонами и удержание механизма в расцепленном положении до разведения автосцепок;
– автоматическое возвращение механизма в положение готовности к сцеплению после разведения автосцепок;
– восстановление сцепления случайно расцепленных автосцепок, не разводя вагоны;
– производство маневровых работ, когда при соударении автосцепки не должны соединяться.
До сцепления автосцепки могут занимать различные взаимные положения:
– оси их находятся на одной прямой;
– оси могут быть смещены по вертикали или горизонтали.
Смещение осей по вертикали допускается в грузовом поезде до 100 мм и пассажирском скоростном до 50 мм, а в горизонтальном направлении до 175 мм, при которых обеспечивается надежное автоматическое сцепление вагонов в эксплуатации.
При соударении вагонов малый зуб корпуса одной автосцепки скользит по направляющей поверхности малого или большого зубьев в зависимости от отклонения головок в горизонтальной плоскости в одну или другую сторону.
Затем малый зуб входит в зев и нажимает на выступающую часть замка. При совпадении продольных осей автосцепок замки нажимают друг на друга. В результате этого замки уходят внутрь карманов корпуса, а вместе с
ними перемещаются предохранители замков, верхние плечи 3 которых скользят по полочкам и проходят над упорами противовесовзамкодержателей.Продвигаясь в зевах дальше, малые зубья нажимают на лапызамкодержателей, заставляя их поворачиваться. В этот момент противовесызамкодержателей размещаются под верхними плечами предохранителей, создавая для них опору.Когда малые зубья займут крайнее правое положение в упор к большим зубьям, замки освобождаются от нажатия и под действием собственного веса выпадают снова в зевы, заполняя образовавшееся пространство в контуре зацепления, и обеспечивают запирание автосцепок.
Вновь войти внутрь карманов корпуса замки не могут, так как верхние плечи предохранителей, соскользнув с противовесов замкодержателей на полочки, располагаются против упоров противовесов замкодержателей, обеспечивая удержание замка в этом положении. Противовес замкодержателя в этот момент находится в верхнем положении и опуститься не может, так как на его лапу нажимает малый зуб соседней автосцепки. Такое положение деталей предотвращает саморасцеп автосцепок при движении поезда. Сигнальные отростки замков сцепленных автосцепок находятся внутри кармана корпуса и не видны снаружи.
Чтобы расцепить автосцепки, достаточно увести внутрь кармана корпуса хотя бы один из замков, что освобождает пространство и дает возможность выхода малых зубьев из зевов. Для этого необходимо поворотом рычага расцепного привода посредством цепочки повернуть валик подъемника. Тогда подъемник, посаженный на квадратную часть валика, приподнимется и своим широким пальцем нажмет на нижнее фигурное плечо предохранителя и поднимет верхнее его плечо выше упора противовесазамкодержателя.Таким образом происходит выключение предохранителя от саморасцепа. При дальнейшем вращении валика широкий палец подъемника, упираясь в выступ замка, нажмет на него и уведет замок внутрь кармана.
Узкий палец подъемника при этом нажмет снизу на горизонтальную грань расцепного угла замкодержателя.Благодаря наличию овального отверстия в замкодержателе он приподнимается вверх, пропуская узкий палец подъемника мимо вертикальной грани расцепного угла.Освобожденный от нажатия снизу, замкодержатель под действием собственной тяжести благодаря овальному отверстию опустится вниз. При этом узкий палец подъемника упрется в вертикальную грань расцепного угла и будет удерживаться в вертикальном положении, не позволяя замку выйти в зев.При этом положении сигнальный отросток замка будет выступать из корпуса, указывая на то, что автосцепки расцеплены.
В таком состоянии механизм будет находиться до разведения вагонов. При разведении вагонов малые зубья смежных автосцепок выходят из зевов, лишая лапу замкодержателя упора. Замкодержатель под действием противовеса поворачивается, его лапа выходит в зев, а расцепной угол освобождает подъемник и замок, которые под действием собственной тяжести опускаются в нижнее положение, обеспечивающее готовность механизма к последующему сцеплению.
Автосцепное устройство типа СА – 3 грузовых вагонов размещается в консольной части хребтовой балки рамы кузова и состоит из корпуса автосцепки с деталями механизма сцепления, ударно – центрирующего прибора, упряжного устройства с поглощающим аппаратом и опорных частей.
Корпус автосцепки с механизмом сцепления предназначен для сцепления и расцепления вагонов, восприятия и передачи ударно-тяговых усилий упряжному устройству. Корпус автосцепки представляет собой пустотелую фасонную отливку, состоящую из головной части и хвостовика.Внутри головной части размещены детали механизма сцепления. Она имеет большой и малый зубья, которые соединяясь образуют зев. На вертикальной стенке зева, возле малого зуба имеется окно для замка, а рядом – окно для замкодержателя.
В верхней части отлит выступ, который воспринимает жесткие удары при полном сжатии поглощающего аппарата. Внутри корпуса со стороны малого зуба отлита полочка для верхнего плеча предохранителя, а со стороны большого зуба имеется шип для навешивания замкодержателя. В нижней части выполнено горизонтальное отверстие для постановки валика подъемника. В пустотелом хвостовике сделано продолговатое отверстие для соединения корпуса автосцепки с тяговым хомутом. Торец хвостовика служит для передачи ударных нагрузок и имеет цилиндрическую поверхность.Большой зуб имеет три усиливающих ребра верхнее, среднее и нижнее, плавно переходящие в хвостовик и соединенные между собой перемычкой. Голова автосцепки заканчивается сзади упором, предназначенным для передачи при неблагоприятном сочетании допусков на основные размеры жесткого удара на хребтовую балку через концевую балку рамы вагона и ударную розетку.
Корпус удерживается маятниковым подвешиванием, состоящим из ударной розетки, двух подвесок, центрирующей балочки.
Центрирующий прибор воспринимает от корпуса автосцепки избыточную энергию удара после полного сжатия поглощающего аппарата и центрирует корпус автосцепки. Состоит из ударной розетки, двух маятниковых подвесок и центрирующей балочки. Ударная розетка отлита за одно целое с передними упорами и приклепано или приварено к концевой балке рамы. Розетка имеет окно для постановки корпуса автосцепки и отверстия для маятниковых подвесок.
Маятниковые подвески имеют вид стержня диаметром 25 мм с двумя Т образными головками (верхней более широкой и нижней).
Верхняя головка подвески опирается на ударную розетку, а на нижнюю уложена центрирующая балочка омегообразной формы. На расстоянии 625 мм от упорных плоскостей переднего упора к хребтовой балке приклепан или приварен задний упор, который также представляет собой П образную отливку с ребрами жесткости.
У четырехосных вагонов с укороченными консольными частями (крытые вагоны и цистерны) задние упоры отливают заодно целое с надпятниковыми коробками. Для предупреждения истирания вертикальных стенок хребтовой балки поглощающим аппаратом на них между упорами приклепывают по две предохранительные планки.
Упряжное устройство передает упорам продольные силы от корпуса автосцепки и смягчает их действие. Оно размещено между передними и задними упорами автосцепного устройства и состоит из тягового хомута 6, поглощающего аппарата, клина, упорной плиты и крепежных деталей клина и поддерживающей планки.
Нижней опорой тягового хомута и поглощающего аппарата является поддерживающая планка, прикрепляемая восемью болтами снизу к хребтовой балке. Тяговый хомут представляет собой раму, внутри которой размещен поглощающий аппарат и упорная плита.В головной части хомута имеется отверстие для клина. Внизу головной нижней части расположены приливы с отверстиями для болтов, предохраняющих клин от выпадения.
Опорная площадка хомута снабжена усиливающими ребрами. Клин тягового хомута прямоугольного сечения с округленными кромками в нижней части имеет заплечики, которыми он опирается на болты, удерживающие его от выжимания. Выемки в верхней части боковых поверхностей клина сделаны для уменьшения его массы.
Расцепной привод состоит из расцепного рычага, цепочки, полочки, кронштейна.
Детали расцепного привода:
–расцепной рычаг;
– державка;
– кронштейн;
– цепь расцепного привода;
Расцепной рычаг, предназначенный для расцепления автосцепки, имеет короткое плечо с отверстием для регулировочного болта, стержень и рукоятку, соединенные плоской частью, поперечное сечение которой 20 × 35 мм.Между стержнем и коленом приварен ограничитель продольных перемещений.Если на подвижном составе в зоне расположения стержня рычага размещены какие – либо детали, препятствующие его монтажу, например детали ручного тормоза, то стержень рычага выгибают для обхода этих деталей.