Файл: Назначение режимов резания методика назначения режимов резания.docx
ВУЗ: Не указан
Категория: Не указан
Дисциплина: Не указана
Добавлен: 06.12.2023
Просмотров: 42
Скачиваний: 1
ВНИМАНИЕ! Если данный файл нарушает Ваши авторские права, то обязательно сообщите нам.
НАЗНАЧЕНИЕ РЕЖИМОВ РЕЗАНИЯ
-
МЕТОДИКА НАЗНАЧЕНИЯ РЕЖИМОВ РЕЗАНИЯ
-
Роль режимов резания в проектировании технологических процессов.
Уровень выбранных режимов резания определяет интенсивность протекания технологического процесса во времени, его динамическую напряженность и надежность.
Элементы режимов резания (t, B, S, V…) являются основой для расчета усилий резания, используемых при проектировании режущих инструментов и приспособлений. Расчетные уровни крутящего момента Мк и эффективной мощности резания Nе необходимы для проверки соответствия выбранного технологического оборудования по М к и N.
Выбранные режимы определяют также время и стоимость обработки, ресурс инструментов и характеристики потока их износовых отказов.
Технологические карты, оформляемые при курсовом и дипломном проектировании, содержат соответствующие графы для выбираемых элементов режима резания:
-
Методы назначения режимов резания.
В настоящее время получили распространение 3 метода выбора режимов резания:
1. Нормативный (табличный), при котором режимы выбираются из соответствующих нормативов с учетом условий /1-6/. Достоинство метода – простота. Недостатки: приближенность и неоптимальность результата.
2. Автоматизированный на основе ЭВМ /7/. В данном случае ЭВМ работает в режиме автоматизированного справочника с кодированной нормативной базой данных /1-6/.
Достоинство – сокращение времени по назначению режимов, недостатки первого метода.
3. Автоматизированный с оптимизацией /8-12/.
В данном случае с учетом большого количества факторов определяются режимы резания, обеспечивающие минимальную трудоемкость (стоимость) операций и гарантирующих требуемое качество обработки.
Широкое применение метода сдерживается отсутствием развитого программного обеспечения.
В настоящей работе назначение режимов резания выполняется по первому методу.
-
Методика назначения режимов резания.
Выбор режимов резания при лезвийной обработке включает следующие этапы (рис.1.1).
1. Анализ исходных данных.
Этап включает анализ заготовки, детали, выполняемых переходов (операций), приспособлений, оборудования и других условий обработки.
2. Выбор числа ходов (проходов) z.
На данном этапе рассматривается вопрос о делении напуска между отдельными ходами (проходами) и определение глубины сверления без вывода сверла с использованием соответствующих таблиц.
3. Выбор материала инструмента.
В зависимости от группы обрабатываемого материала и условий обработки по таблицам выбирается рациональная марка режущей части инструмента.
4.Выбор конструкции и геометрии инструмента.
В зависимости от условий обработки и инструментального материала выбираются стандартная конструкция, геометрия и другие характеристики режущего инструмента.
5.Выбор СОЖ.
В зависимости от конкретных условий операции по таблицам назначается рациональная марка СОЖ.
6.Выбор глубины резания t.
При нормальных припусках h рационально назначать t = h. В случае напусков обращаемся к блоку 2.
7.Выбор и корректировка подачи S.
Т

абличное значение подачи Sт выбирается по соответствующим нормативам. Затем с помощью поправочных коэффициентов Кi, i = 1… u , учитывающих конкретные условия обработки, выполняется корректировка Sт
где u - количество условий для корректировки Sт.
Расчетная подача S должна принадлежать ряду подач выбранного станка, т.е.
S

8.Выбор стойкости инструмента Т.
Табличное значение Т выбирается с учетом назначенных ранее t, S и других условий обработки.
9.Выбор и корректировка скорости резания V.
Т

абличное значение скорости Vт на основе ранее найденных t, S и T выбирается по соответствующим нормативам. Затем производится корректировка Vт с помощью поправочных коэффициентов Ki , i = 1… u , учитывающих конкретные условия обработки.
10. Расчет и корректировка частоты n. Расчет фактической скорости резания Vф.
Значение частоты при лезвийной обработке определяется выражением
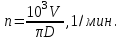
Полученное n должно принадлежать к геометрическому ряду частот станка, т.е. nn
ст.
После этого определяется фактическая скорость резания
Vф=πDn / 103
11.Расчет основного времени .
Для большинства видов механической обработки основное время опреде-
ляется выражением
0=

где S0 - подача в мм/об.;
L - путь обработки в мм с подачей S0 и частотой n.
-
Расчет усилия резания Р.
Усилия резания Рz, Po необходимые для расчета зажимных устройств приспособлений, определяются по соответствующим эмпирическим зависимостям
Рz, Po = f (t, S, V, B, z, D), постоянные для которых выбираются из таблиц нормативов.
13.Расчет крутящего момента Мк.
Крутящий момент, необходимый для расчета зажимных устройств приспособлений, определяется по соответствующим эмпирическим зависимостям (осевая обработка) или через найденное ранее значение Рz.
14.Расчет мощности резания Ne.
Эффективная мощность резания определяется через Мк (осевая обработка) или через Рz. Знание ее необходимо для проверки соответствия выбранного технологического оборудования по мощности.
Рассмотренная последовательность назначения режимов резания относится к наиболее распространенной лезвийной обработке. В случае абразивной обработки имеются следующие отличия.
-
После выбора СОЖ назначается по соответствующим нормативным таблицам припуск h на шлифование (если он не определен операционной технологией). -
После выбора h назначается по нормативным таблицам скорость вращения детали V∂, определяется частота вращения детали n∂ , затем назначается скорость вращения шлифовального круга Vk и определяется nк. -
Выбираются подачи S в долях ширины круга, не определяющие точность обработки. -
Выбираются и корректируются по условиям шлифования малые подачи, определяющие точность получаемых размеров.
Рассчитывается основное время o.
-
НАЗНАЧЕНИЕ РЕЖИМОВ РЕЗАНИЯ ДЛЯ ТОКАРНЫХ
ОПЕРАЦИЙ
Рассмотрим токарную операцию (рис.2.1), содержащую наиболее распространенные переходы: подрезку, обточку, расточку, фасонное точение и проточку канавок.
-
Анализ исходных данных.
2.1.1 Заготовка.
Прокат из низколегированной, хромистой, улучшенной токами высокой частоты стали 40Х. Термическая обработка: отжиг, в = 395-492 МПа,
НВ = 116-146.
-
Деталь.
Согласно рис.2.1 представляет собой втулку, обрабатываемую по внутреннему диаметру.
-
Выполняемый переход.
Операция включает следующие переходы получистовой обработки:
растачивание ( резец 5 ).
2.1.4. Приспособление.
Заготовка закрепляется в 3-х кулачковом пневматическом патроне с упором в левый торец.
2.1.5. Оборудование.
В качестве оборудования согласно табл.9, с.15 /2/ выбран токарный станок мод.16К20, имеющий следующие параметры:
1) число частот вращения шпинделя zn= 22;
2) пределы частот n = 12,5 - 1600 1/мин.;
3) пределы продольных подач Sпр = 0,05-2,8 мм/об.;
4) пределы поперечных подач Sпп = 0,025-1,4 мм/об.;
5)мощность привода главного движения Nст = 11 кВт.
2.2. Выбор инструментального материала.
Для условий получистового точения стали 40Х, относящейся к VI гр. обрабатываемых материалов, табл.13, с.53 /1/ рекомендует твердый сплав Т15К6.
2.3. Выбор геометрии режущих инструментов.
В данном случае геометрия характеризуется следующими параметрами:
-
задним углом =10 -
передним углом =10 -
радиусом при вершине r =1, мм -
величиной фаски f=0,2 мм.
Значение главного угла в плане φ для резца представлено на рис.2.1.
Для обработки сталей гр. VI табл.1, с.211 /1/ рекомендует следующую геометрию табл.2.1.
2.4. Выбор смазочно-охлаждающего жидкости (СОЖ).
Согласно табл.24, с.233 /1/ для проведенных выше (п.2.1) условий рекомендуется 5-10% раствор Аквол – 10 м.
2.5. Назначение глубины резания t.
Согласно операционным размерам и размерам заготовки (рис.2.1) определяем глубину резания для резца 5 и результат заносим в сводную табл.2.1.
2.6. Назначение подач S.
Согласно табл.28 /1/ с.238 при Ra = 12,5, r =1 для резца 5 рекомендуется табличная подача
ST5 = 0,6 мм/об.
Таблица 2.1.
Основные параметры токарной операции (рис.2.1)
№№ резца | П а р а м е т р ы | |||||||||||||
α | γ | φ | r | f | t | S | hз | T | nст | Vф | τ0 | Ρz | ΡzV | |
грд | грд | грд | мм | мм | мм | мм/ об | мм | мин | 1/мин | м/ мин | мин | кг | кгм/мин | |
2 | 3 | 4 | 5 | 6 | 7 | 8 | 9 | 10 | 11 | 12 | 13 | 14 | 15 | |
5 | 10 | 10 | 60 | 1 | 0,2 | 1 | 0,27 | 0,6 | 60 | 252 | 15,16 | 0,95 | 72,2 | 11.41 |
Значения поправочных коэффициентов на подачи выбираются согласно табл. 30 /1/ с.239. Их значения приведены в табл. 2.2. Здесь же приведены значения полных поправочных коэффициентов
Кsј=


для 5-го резца, j =5.
Поправочные коэффициенты Кi и Ksj на подачи
Условия обработки | Корка | Матер. инструмента | Диам. обработки | Матер. заготовки | Термообработка | Вид поверх. обработки | KSj |
Р \ Кi | КI | К2 | К3 | К4 | К5 | К6 | КS |
5 | I | I | 0,45 | I | I | 1 | 0,45 |