Файл: Составление технологической карты на восстановление детали.docx
ВУЗ: Не указан
Категория: Не указан
Дисциплина: Не указана
Добавлен: 11.12.2023
Просмотров: 46
Скачиваний: 1
ВНИМАНИЕ! Если данный файл нарушает Ваши авторские права, то обязательно сообщите нам.
Что касается смешанного метода, то он позволяет с меньшими затратами осуществить ремонтные работы и характеризуется тем, что все виды технического обслуживания и ремонтов, за исключением капитального, выполняет цеховая служба ремонтного хозяйства, а капитальный ремонт – ремонтно-механический цех. При этом можно успешно пользоваться приемами узловой замены изношенных блоков путем их изъятия и ремонта на восстановительной базе, а можно выполнять работы по ремонту во время технологического и междусменного простоя оборудования.
3. Общая компоновка ремонтно-механической мастерской.
Организационно-производственная структура ремонтного хозяйства определяется масштабом предприятия и принятой формой организации ремонта.
К общезаводским подразделениям относятся отдел (управление) главного механика, ремонтно-механический цех, склад оборудования и запасных частей. На небольших заводах в состав ремонтного хозяйства входит и энергохозяйство. К цеховым подразделениям относятся цеховые и корпусные ремонтные базы в производственных цехах (рисунок 3)
Руководит ремонтным хозяйством главный механик завода через отдел главного механика, который состоит из ряда бюро: оборудования (планово-предупредительного ремонта), планово-производственного, технического и др. Отдел главного механика выполняет конструкторскую, технологическую, производственную и планово- экономическую работу для всего ремонтного хозяйства. Ремонтно- механический цех (РМЦ) подчинен главному механику и проводит капитальный ремонт и модернизацию сложного оборудования, изготавливает запасные части и нестандартное оборудование, оказывает помощь цеховым ремонтным службам.
Структура ремонтного цеха имеет комплексный характер и обеспечивает выполнение всех ремонтных работ и их обслуживание. К числу отделений и участков РМЦ относятся демонтажное, заготовительное, механическое, слесарно-сборочное, кузнечное, сварочное, жестяницкое, восстановления деталей, окрасочное и другие отделения.
В состав цеховой ремонтной базы входят механическая мастерская, слесарный участок, ремонтные бригады, кладовая. Руководство ремонтными работами в цехах осуществляют механики цехов через мастеров и бригадиров. На большинстве заводов механики цехов административно подчинены начальникам производственных цехов. Виды и объемы выполняемых ремонтных работ в цехе обусловливаются принятой на заводе формой организации ремонта оборудования.
Техническая база ремонтного хозяйства определяется типовой системой технического обслуживания и ремонта металло- и деревообрабатывающего оборудования, а также общемашиностроительными нормативами технологического проектирования РМЦ и ЦРБ и предусматривает количество и структуру оборудования, производственные площади, средства механизации ремонтных работ и технологию их выполнения. Состав и количество основного оборудованияв ремонтном хозяйстве должны обеспечивать выполнение всех видов ремонтных работ, изготовление запасных частей и нестандартизованного оборудования, а также его модернизацию.
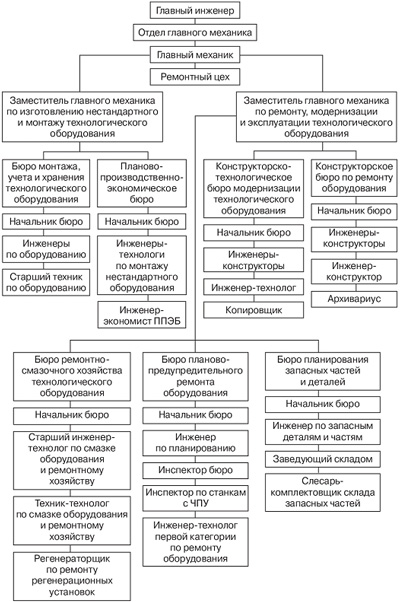
Рисунок 3 – Типовая структура управления отделом главного механика
Основное оборудование ремонтных служб — универсальные станки для обработки металла резанием (токарно-револьверные — 50%, фрезерные — 12, шлифовальные — 16% и др.). Вспомогательное и слесарно-сборочное оборудование определяется в виде комплекта (набора). Общее количество основного оборудования в PMЦ и ЦРБ рассчитывается исходя из трудоемкости станочных работ по ремонту установленного на заводе оборудования и эффективного фонда времени работы одного станка при двухсменной работе, но не должно превышать 2-2,5% оборудования завода.
Площадь определяется на основе компоновки отделений и помещений цеха, а также планировки оборудования и рабочих мест с учетом норм технологического проектирования вспомогательных цехов. Используют и укрупненный метод по удельной площади на единицу основного оборудования (36-46 м2).
На большинстве машиностроительных заводов (за исключением особо крупных) техническая оснащенность ремонтных баз не соответствует современным требованиям. Номенклатура станочного парка ремонтных цехов мало приспособлена для высокопроизводительного и качественного выполнения работ при ремонте сложного и точного оборудования.
Запасные детали изготавливаются в основном на универсальном оборудовании по устаревшей технологии. Слесарные же работы выполняются, как правило, вручную. Практически не используются механические шаберы, переносные шлифовальные приспособления, электрозаклепочники и пневматические ключи.
Основной задачей функционирования ремонтного хозяйства предприятия является обеспечение бесперебойной эксплуатации оборудования. Служба ремонтного хозяйства в системе управления предприятием подчинена главному инженеру. В ее состав входят: ремонтно-восстановительная база предприятия, склады, цехи и общезаводские отделы ремонтного хозяйства (технологический, оборудования, диспетчерский).
В зависимости от масштабов производства ремонтно-восстановительная база предприятия может содержать:
-
ремонтно-механический цех, выполняющий ремонт технологического оборудования; -
ремонтно-строительный цех, выполняющий ремонт зданий, сооружений, производственных, складских и служебных помещений; -
электроремонтный цех, подчиненный главному энергетику и выполняющий ремонт энергооборудования, а также склады оборудования и запасных частей.
Кроме того, в цехах целесообразно создание ремонтных баз, подчиненных цеховому механику, главной задачей которых является поддержание в работоспособном состоянии технологического оборудования, осуществление профилактических осмотров, разнообразных ремонтных работ.
Общезаводские отделы ремонтного хозяйства подчиняются главному механику наряду с ремонтно-механическим и ремонтно- строительным цехами. Вместе с этими подразделениями в его службе можно организовать бюро планово-предупредительного ремонта и планово-производственное бюро.
Характерными работами для ремонтного хозяйства предприятия являются:
-
паспортизация и аттестация оборудования; -
разработка технологических процессов ремонта и их оснащения; -
планирование и выполнение работ по техническому обслуживанию и ремонту оборудования; -
модернизация оборудования.
4. Составление технологической карты на восстановление детали.
Составляем маршрут обработки детали.
№ операции | Наименование и краткое содержание операции | Оснастка | Тип оборудования |
005 | Замеры распределительной тарелки | - | - |
010 | Контроль распределительной тарелки на наличие повреждений | - | - |
015 | Предварительная механическая обработка распределительной тарелки под наплавку | - | - |
020 | Наплавка 1) Наплавить на трещины распределительной тарелки 2) Наплавка в отверстия распределительной тарелки | - | Ручная дуговая сварка |
025 | Круглошлифовальная Шлифовать распределительную тарелку и отверстия | | Круглошлифовальная машина |
Продолжение таблицы 1
030 | Полировочная 1) Полировать отверстия и распределительную тарелку | - | Полировочная машина |
035 | Контрольная | - | Стол контроля |
По маршруту обработки детали разрабатали карту технологического процесса, которая представлена в приложении А.
4.1. Ручная дуговая сварка
Под ручной дуговой сваркой понимается сварка, при которой дуга горит
между плавящимся металлическим электродом и сварочной ванной, поверхность которой защищается от воздуха за счет расплавления электродного покрытия. Подача электрода в сварочную ванну и его перемещение вдоль стыка производится сварщиком вручную.
Преимущества ручной дуговой сварки:
1) Возможность произведения сварочных работ в любых пространственных положениях;
2) сравнительно быстрый переход от одного свариваемого материала к другому;
3) возможность сварки в местах с ограниченным доступом;
4) возможность сварки самых различных сталей благодаря широкому
выбору выпускаемых марок электродов;
5) простота и мобильность сварочного оборудования.
Недостатками ручной дуговой сварки является следующее:
1) наиболее низкий КПД и производительность в сравнении с другими
способами сварки;
2) достаточно вредные условия работы в процессе сварки;
3) для получения качественного сварного соединения необходимы наиболее квалифицированные рабочие-сварщики.
Не смотря на все свои минусы ручная дуговая сварка, покрытая металлическими электродами в данный момент времени, является одним из самых популярных методов, которые используются для изготовления сварных конструкций.
4.2 Расчет режимов сварки
Режимом сварки называют совокупность основных характеристик
сварочного процесса, обеспечивающих получение сварных швов заданных
размеров, формы и качества. При РДС диаметр электроды, сила сварочного
тока, напряжение дуги, площадь поперечного сечения шва, выполняемого за
один проход дуги, число проходом, род тока и полярность.
Расчёт режимов сварки будем проводить по рекомендациям, описанным в методическом указании.
На рисунке 2 представлены конструктивные элементы разделки и сварного соединения Т3 по ГОСТ 5264-80.
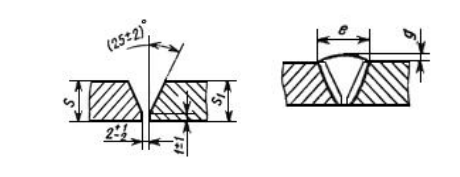
Рисунок 2 – Конструктивные элементы разделки и сварного соединения
Конструктивные элементы разделки и сварного соединения:

Диаметр электрода для стыковых соединений выбираем в зависимости от толщины свариваемого металла в нашем случае выбираем электроды толщиной 4 мм.
Расчёт силы сварочного тока при сварке покрытыми электродами
производится по диаметру электрода и допускаемой плотности тока. Для электрода с основным покрытием и диаметром 4 мм j = 14 А/мм2

Принимаем сварочный ток равный 175 А.
При использовании ручной дуговой сварки покрытыми электродами можно получить напряжение в диапазоне 20 – 34 В. При проектировании
технологических процессов сварки напряжение выбирается на основании рекомендаций справочников и паспорта на марку электродов.
Для приближенного расчёта напряжения на дуге воспользуемся эмпирической зависимостью:

Далее необходимо определить число проходов. Общая площадь поперечного сечения наплавленного металла:

где

Для обеспечения оптимальных условий формирования необходимая площадь поперечного сечения металла, который наплавляется за один проход, должна быть меньше данного значения:

Число проходов определяют по формуле:
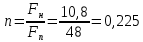
Назначаем число проходов равное 1.
При определении числа проходов следует учитывать, что при сварке стыковых соединений за один проход выполняются швы высотой не более 9 мм.
Скорость сварки определяем по формуле:

где

