Файл: Катализатор каталитического крекинга и каталитического риформинга.docx
ВУЗ: Не указан
Категория: Не указан
Дисциплина: Не указана
Добавлен: 12.12.2023
Просмотров: 43
Скачиваний: 1
ВНИМАНИЕ! Если данный файл нарушает Ваши авторские права, то обязательно сообщите нам.
«Катализатор каталитического крекинга и каталитического риформинга»
Содержание
1 Описание процессов
-
Каталитический крекинг -
Каталический риформинг
2. Катализаторы
2.1 Катализаторы каталитического крекинга
2.1.1 Строение катализаторов каталитического крекинга
2.1.2 Механизм процессов на катализаторе
2.1.3 Промышленный марки катализаторов каталитического крекинга
2.2 Катализаторы каталитического риформинга
2.2.1 Состав катализаторов каталитического риформинга и механизм
2.2.2 Механизм и химизм процесса каталитического риформинга
2.2.3 Марки катализаторов каталитического риформинга
1 Описание процессов
1.1 Каталитический крекинг
Назначение: производство с максимально высоким выходом (до 50 % и более) высокооктанового бензина и ценных сжиженных газов
Сырье: вакуумный дистиллят (газойль) широкого фракционного состава (350…500 °С). В ряде случаев в сырье крекинга вовлекаются газойлевые фракции термодеструктивных процессов, гидрокрекинга, рафинаты процессов деасфальтизации мазутов и гудронов, полупродукты масляного производства и др На современных зарубежных установках перешли к переработке глубоковакуумных газойлей с температурой конца кипения 540…620 °С. На специально запроектированных установках каталитическому крекингу подвергают остаточное сырье: мазуты и даже гудроны или их смеси с дистиллятным сырьем 643 без или после предварительного облагораживания гидроочисткой, деасфальтизацией или деметаллизацией.
Продукты:
- сжиженный газ - сырья для последующих производств высокооктановых компонентов бензинов изомерного строения: алкилата и метил-трет-бутилового эфира, а также сырья для нефтехимических производств;
- высокооктановый бензин;
- легкий газойль используется обычно как компонент дизельного топлива;
-тяжелый газойль с высоким содержанием полициклических ароматических углеводородов — как сырье для производства технического углерода или высококачественного электродного кокса (например, игольчатого);
- кокс.
Оптимальные технологические параметры каталитического крекинга зависят от выбранной схемы процесса. В большинстве технологических схем температура в реакторе составляет порядка 510-540 0С, давление поддерживается практически постоянным и составляет 0,5-2 атм. Повышение давления несколько ухудшает селективность процесса и приводит к росту газо- и коксообразования.
1.2 Каталический риформинг
Назначение: повышения детонационной стойкости бензинов и получения индивидуальных ароматических углеводородов, главным образом бензола, толуола, ксилолов — сырья нефтехимии. Важное значение имеет получение в процессе дешевого водородсодержащего газа для использования в других гидрокаталитических процессах. Сырье: прямогонные бензиновые фракции, бензины вторичных процессов - гидрокрекинга, термического крекинга и т.д., при условии их специальной подготовки. При получении высокооктанового компонента автомобильного бензина используются широкие фракции, выкипающие в пределах от 60-90°С до 180°С; при получении бензола, толуола, ксилолов – узкие фракции, выкипающие соответственно в интервалах 62-85°С, 85-105°С, 105-140°С. Для предотвращения дезактивации катализатора в сырье ограничивается содержание серы (не более 0,00005÷0,0010 % в зависимости от типа катализатора) и азота (не более 0,0001%).
Продукты:
- компонент высокооктанового бензина
- узкие фракции, являющиеся сырьем установок экстракции ароматических углеводоров
- Водородсодержащий газ, используется в процессах гидроочистки, изомеризации, гидрокрекинга
- углеводородный газ
- головка стабилизации, являющаяся сырьем установок ГФУ
Технологические параметры. Основными технологическими параметрами процесса каталитического риформинга являются: температура, давление, объёмная скорость подачи сырья, мольное соотношение водород: углеводороды (кратность циркуляции водородсодержащего газа), мольное соотношение вода: хлористый водород, определяющее содержание хлора на катализаторе.
Температура является основным регулируемым параметром процесса. Процесс риформирования проводят в реакторе в интервале температур 480—530 °С.Увеличение температуры процесса приводит к увеличению глубины ароматизации парафиновых углеводородов. Снижение температуры ниже 480 °С приводит к увеличению селективности, что объясняется изменением соотношения скоростей реакций ароматизации и гидрокрекинга в пользу первых. Однако работа в области высоких температур, обеспечивающих более высокие глубины и селективность ароматизации парафиновых углеводородов, затруднена высокой скоростью дезактивации катализатора вследствие его закоксовывания. Давление является вторым по значимости технологическим параметром процесса каталитического риформинга. Снижение давления приводит к увеличению селективности процесса риформинга.с увеличением выхода жидкого продукта и водорода, уменьшением выхода лёгких углеводородов С1-С4. Вместе с тем, снижение давления приводит к увеличению скорости дезактивации катализатора, уменьшению межрегенерационного периода, особенно в области давлений ниже 1,5 МПа. Увеличение объёмной скорости подачи сырья приводит к увеличению выхода жидкого продукта при одновременном снижении выхода ароматических углеводородов. Мольное соотношение водород / углеводороды, характеризуемое в промышленной практике кратностью циркуляции водородсодержащего газа, оказывает существенное влияние на стабильность работы катализатора риформинга.
2. Катализаторы
2.1 Катализаторы каталитического крекинга
2.1.1 Строение катализаторов каталитического крекинга
Промышленные катализаторы крекинга представляют собой в этой связи сложные многокомпонентные системы, состоящие:
1) из матрицы (носителя);
2) активного компонента — цеолита;
3) вспомогательных активных и неактивных добавок.
Матрица катализаторов крекинга выполняет функции как носителя — поверхности, на которой затем диспергируют основной активный компонент — цеолит и вспомогательные добавки, так и слабого кислотного катализатора предварительного (первичного) крекирования высокомолекулярного исходного нефтяного сырья. В качестве материала матрицы современных катализаторов крекинга преимущественно применяют синтетический аморфный алюмосиликат с высокой удельной поверхностью и оптимальной поровой структурой, обеспечивающей доступ для крупных молекул крекируемого сырья.
Аморфные алюмосиликаты являлись основными промышленными катализаторами крекинга до разработки цеолитсодержащих катализаторов. Синтезируются они при взаимодействии растворов, содержащих оксиды алюминия и кремния, например жидкого стекла Na2O · 3SiO2 и сернокислого алюминия Al2(SO4)3. Химический состав аморфного алюмосиликата может быть выражен формулой
Na2O(Al2O3 · xSiО2)
где х — число молей SiO2 на 1 моль Al2O3. Обычно в промышленных аморфных алюмосиликатах содержание оксида алюминия находится в пределах 6…30 % мас.
Аморфные алюмосиликаты обладают ионообменными свойствами, а для придания каталитической активности обрабатывают их раствором сернокислого алюминия для замещения катионов Na+ на Аl3+. Высушенные и прокаленные аморфные алюмосиликаты проявляют протонную и апротонную кислотности. При этом по мере повышения температуры прокаливания происходит превращение протонных кислотных центров в апротонные.
Активным компонентом катализаторов крекинга является цеолит,который позволяет осуществлять вторичные каталитические превращения углеводородов сырья с образованием конечных целевых продуктов.
Цеолиты (от греч. цео — кипящий, литос — камень) представляют собой алюмосиликаты с трехмерной кристаллической структурой следующей общей формулы:
Me2/nO · Аl2О3 · xSiO2 · уН2О ,
где n — валентность катиона металла Me; х — мольное соотношение оксидов кремния и алюминия, называемое силикатным модулем;
у — число молей воды.
В настоящее время насчитывается несколько десятков разновидностей природных и синтетических цеолитов, отличающихся структурой, типом катионов Me, силикатным модулем и числом молекул кристаллизационной воды. Структура цеолитов характеризуется наличием большого числа полостей, соединенных между собой окнами, или микроканалами, размеры которых сравнимы с размерами реагирующих молекул. Обычно полости имеют больший диаметр, чем каналы (или окна).
Например, в цеолите типа шабазит имеется 3 · 1020 полостей диаметром 11,4 Å, в каждую полость которого может поместиться 24 молекулы воды. Диаметр окон шабазита составляет 4,9 Å. При нагреве цеолита вода удаляется и образуется ячеистая структура. Удельная поверхность цеолитов достигает 700…1000 м/г. Обезвоженные цеолиты способны избирательно адсорбировать молекулы различных веществ в зависимости от размеров каналов. Разумеется, если диаметр адсорбируемого вещества больше, чем сечение канала, то оно не может проникнуть во внутренние поры цеолита (ситовой эффект). Так, при диаметре канала (окна) 4 Å цеолит не может адсорбировать углеводороды нормального строения, диаметр молекул которых равен = 4,9 Å.
Обычно тип структуры синтетического цеолита обозначают буквами латинского алфавита А, X, Y, ... L и т. д. Перед буквами ставят химическую формулу катиона металла, компенсирующего отрицательный заряд алюминия в алюмосиликате. Например, СаХ означает цеолит типа X в кальциевой обменной форме; LaY, ReY — соответственно лантановая и редкоземельная форма цеолита Y.
Цеолиты типа А, имеющие малые размеры окон (3,3…5 Å) и небольшой силикатный модуль (1,8…2,0), как правило, не используются в каталитических процессах и применяются в качестве адсорбентов. В каталитических процессах, в том числе крекинга нефтяного сырья, наибольшее применение нашли цеолиты типа X и Y — оба аналоги природного фожазита. В последние годы широкое распространение получают высококремнеземные трубчатые цеолиты L с силикатным модулем более 30 (например, ZSM).
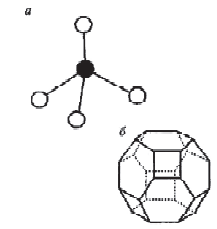

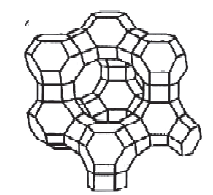
а — тетраэдр; б — содалитовая клетка; в — суперклетка; г — элементарная ячейка
Рисунок 1- Строение цеолитов типа фожазита
Первичной основой (структурной единицей) кристаллической решетки цеолитов X и Y является тетраэдр, состоящий из четырех анионов кислорода, которые окружены значительно меньшими по размерам ионами кремния или алюминия (рисунок 1). 24 тетраэдра образуют вторичную структурную единицу —усеченный октаэдр (кубооктаэдр, который содержит восемь шестиугольных и шесть квадратных поверхностей), так называемую содалитовую клетку.
На следующей ступени структурирования четыре кубооктаэдра объединяются в тетраэдрическую конфигурацию вокруг пятого при помощи шестиугольных призм, образуя суперклетку (рисунок 1).
В результате объединения множества суперклеток (в фожазите их восемь) в регулярную систему формируется элементарная ячейка цеолита (рисунок 1).
Тетраэдры из оксидов кремния и алюминия расположены так, что цеолиты имеют открытые участки структуры. Это и создает систему пор с высокой удельной поверхностью. Химическую формулу первичной структурной единицы — тетраэдров кремния и алюминия — можно представить в виде:
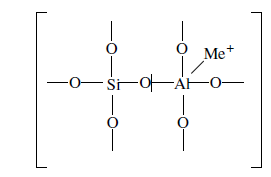
Тетраэдры с ионами Si4+ электрически нейтральны, а тетраэдры с ионами трехвалентного алюминия Аl3+ имеют заряд минус единица, который нейтрализуется положительным зарядом катиона Ме+ (сначала катионом Na+, поскольку синтез чаще ведется в щелочной среде, затем в результате катионного обмена — катионами других металлов, катионом NH4 или протоном Н+).
Наличие заряженных ионов алюминия на поверхности цеолита (центры Бренстеда) и обусловливает кислотные свойства и, следовательно, его каталитическую активность.
Натриевая форма цеолитов каталитически малоактивна и наименее термостабильна. Оба эти показателя существенно улучшаются при увеличении силикатного модуля цеолитов, а также степени ионного обмена на двухвалентные и особенно на трехвалентные металлы. Среди них более термостабильны цеолиты типа ReY, обладающие к тому же важным свойством — высокой каталитической активностью. Благодаря этим достоинствам цеолиты серии ReY как активный компонент катализаторов крекинга получили исключительно широкое применение в мировой нефтепереработке.
Важным этапом в области дальнейшего совершенствования цеолитных катализаторов крекинга явилась разработка (в 1985 г. Фирмой 654 «Юнион карбаид») нового поколения цеолитов