Файл: 1 Анализ способов обработки глубоких отверстий, конструкций инструментов для глубокого сверления, сил, действующих на сверло, факторов, оказывающих влияние на силы, моделей контакта при трении.docx
ВУЗ: Не указан
Категория: Не указан
Дисциплина: Не указана
Добавлен: 12.12.2023
Просмотров: 127
Скачиваний: 1
ВНИМАНИЕ! Если данный файл нарушает Ваши авторские права, то обязательно сообщите нам.
Таким образом, в эксперименте участвовали сверла со следующим видом микрорельефа, созданным на поверхности направляющих элементов:
- параллельный микрорельеф, наносимый торцом чашечного круга перпендикулярно оси сверла,
- перпендикулярный микрорельеф, наносимый торцом чашечного круга параллельно оси сверла,
- скрещивающийся микрорельеф, наносимый торцом чашечного круга под углом 45˚ к оси сверла.
Кроме того, в качестве контрольного в эксперименте участвовали сверла с микрорельефом поверхности направляющих элементов наносимым по существующей технологии периферией шлифовального круга прямого профиля под углом 90˚ к оси сверла.
Обработку отверстий в роликах и клапанах, используемых в дальнейшем в конструкции машин непрерывного литья заготовок, и гидравлической продукции соответсвенно производили на специальном сверлильно-расточном станке модели РТ 60418 (рисунок 37) при рабочих режимах резания: nинстр = 160…200 мин־¹, nдет = 40…60 мин־¹, изменяя значение подачи согласно матрице планирования эксперимента в пределах S = 8…12 мм/мин. Обработку отверстий производили с учетом опыта работ [26].
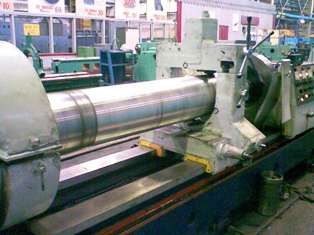
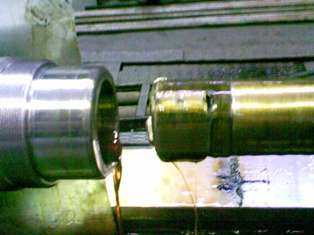
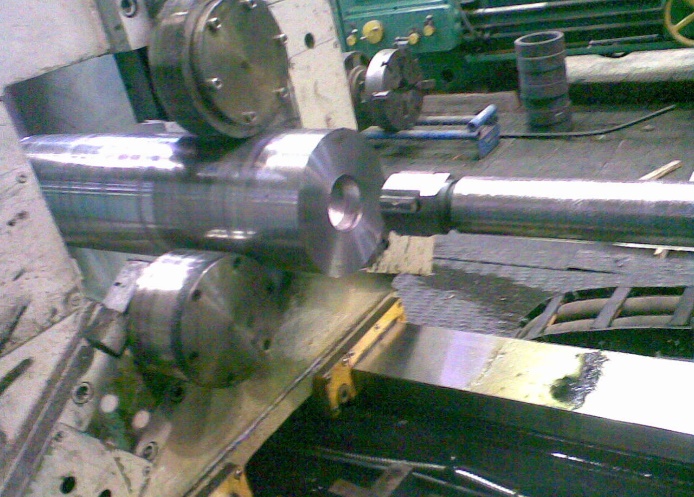
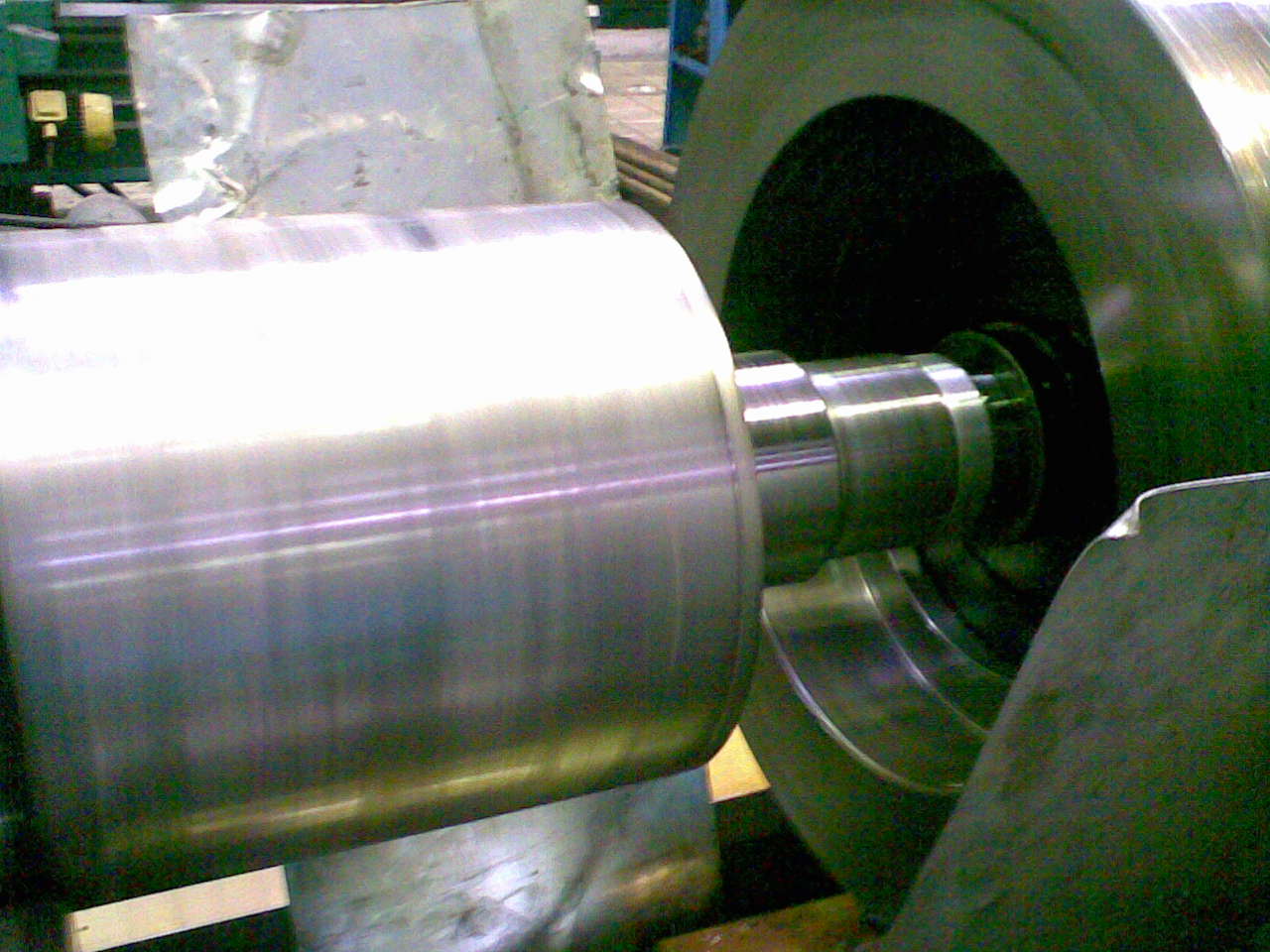
Рисунок 37–Обработка отверстий на сверлильно-расточном станке РТ 60418
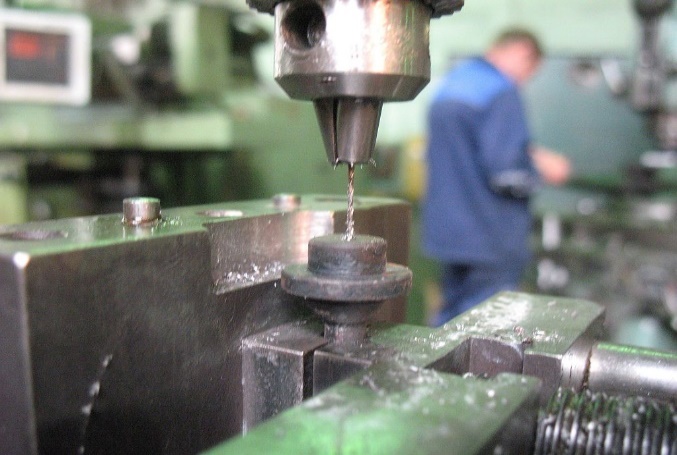
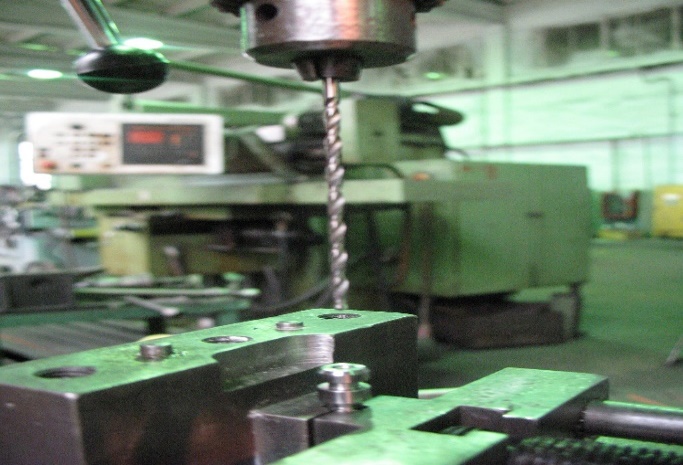
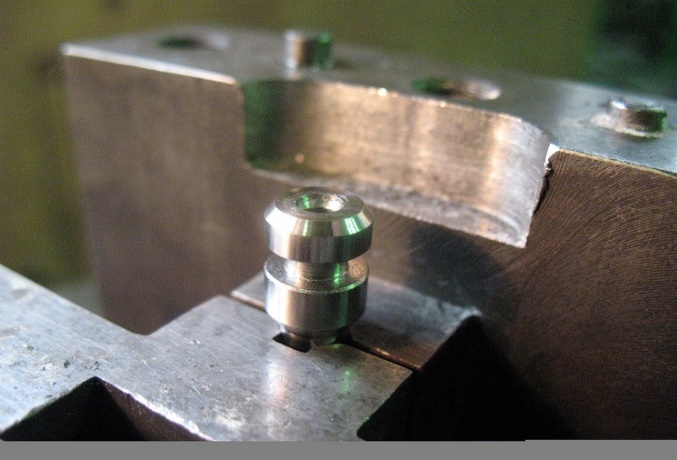
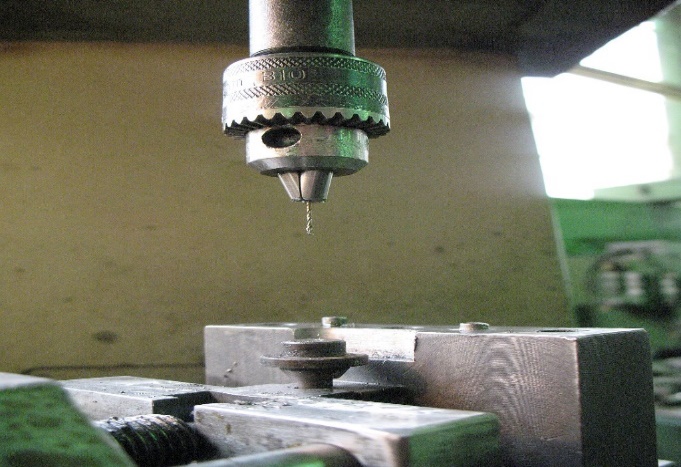
Рисунок 38–Обработка отверстий на вертикально-расточном станке
Подвод смазочно-охлаждающей жидкости – наружный, отвод стружки по внутренним каналам. Тип смазочно-охлаждающей жидкости, применяемой при глубоком сверлении – В-3 (сульфофрезол).
У всех подготовленных образцов были измерены и зафиксированы первоначальные параметры микрогеометрии поверхности. Параметры микрогеометрии поверхности направляющих контролировали в течение всего эксперимента. Замеряли износ инструмента после каждого просверленного ролика. Результаты измерений сведены в табл. 11 и показаны на рисунке 38.
Обработка отверстий на рабочих режимах резания характеризовалась нормальной работой инструмента при всех видах микрорельефов поверхности направляющих. При этом показания приборов контроля: момента привода вращения детали, момента привода вращения стебля, осевого усилия, носили постоянный характер и находились в пределах: момент привода вращения детали: 18…20 mV, момент привода вращения стебля 12…15 mV, осевое усилие 16…18 mV. Увеличение подачи до 0,12 мм/об характеризовалось увеличением осевого усилия до 23…25 mV, что не превышало уставки прибора и также характеризовалось нормальной работой станка. При дальнейшем увеличении подачи нагрузка на стебель превышала уставки прибора.
При изучении процесса стружкообразования на рабочих режимах резания видно, что усадка стружки на различных участках режущей кромки не одинакова. Увеличение подачи вызывает рост всех составляющих сил резания. По мере увеличения подачи наблюдается некоторое изменение стружки. Отличается и значение осевой силы. При увеличенной подаче стружка характеризуется большей толщиной профиля поперечного сечения.
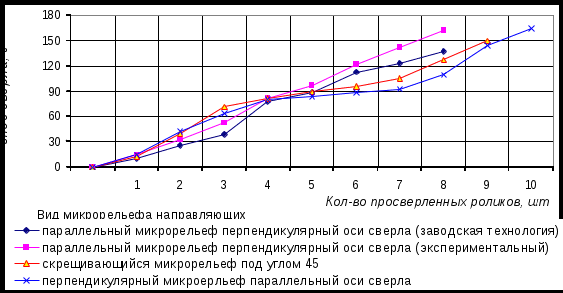
Рисунок 39–Износ сверла
Анализ полученных табличных данных и графика изменения износа (рисунок 39) показывает, что сверла с перпендикулярным микрорельефом параллельным оси сверла и скрещивающимся под углом 45º микрорельефом характеризуются более высокими эксплуатационными показателями, чем сверла с параллельным типом направлений неровностей поверхности направляющих перпендикулярным оси сверла.
Так в период плановой компании сверления (период времени между началом и окончанием работы сверлильной головки вследствие потери параметрических характеристик поверхности направляющих) на сверлах малого диаметра с параллельным микрорельефом перпендикулярным оси сверла наступал параметрический отказ по износу поверхности направляющих, в то время как для перпендикулярного микрорельефа параллельного оси сверла и скрещивающегося под углом 45º микрорельефов признаков отказов на наблюдалось.
Наибольший эффект достигался при сверлении сверлильными головками, сверлами с перпендикулярным микрорельефом параллельным оси сверла поверхности направляющих. Износостойкость таких сверл на 20 % выше, чем обработанных периферией шлифовального круга прямого профиля по существующей на заводе технологии с получением параллельного микрорельефа перпендикулярного оси сверла.
Повышение стойкости сверлильных головок и сверл после сверления нескольких роликов и клапанов, приводит и к повышению точности обрабатываемых отверстий.
Оценку точности обработанных отверстий производили измерением диаметра отверстий после каждого просверленного ролика участвующего в эксперименте при каждом типе микрорельефа поверхности направляющих элементов сверлильных головок. Измерения производили индикаторным нутрометром НИ 100 ГОСТ 868 – 72 на расстоянии 250 мм от торца детали, через 120°. Пределы измерений нутрометра составляют 50…100 мм, цена деления 0,01 мм, допустимая погрешность ± 0,018 мм (рис. 40).
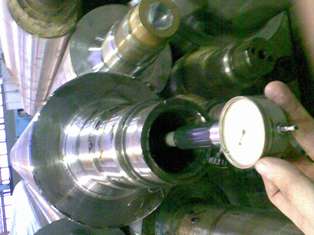
Рисунок 40–Измерение отклонений диаметра обработанных отверстий
индикаторной головкой
Таблица 8–Результаты измерений отверстий, просверленных в роликах сверлильными головками с различным типом направлений неровностей направляющих элементов.
Вид микрорельефа направляющих | Отклонения диаметра обработанных отверстий при количестве просверленных роликов, мм | |||||||
1 | 2 | 3 | 4 | 5 | 6 | 7 | 8 | |
Параллельный перпендикулярный оси сверла (заводская технология) | 0,15 | 0,17 | 0,2 | 0,23 | 0,29 | 0,33 | 0,37 | 0,44 |
Параллельный перпендикулярный оси сверла (экспериментальный) | 0,15 | 0,18 | 0,2 | 0,24 | 0,3 | 0,35 | 0,41 | 0,45 |
Скрещивающийся под углом 45° | 0,14 | 0,16 | 0,19 | 0,23 | 0,25 | 0,29 | 0,32 | 0,41 |
Перпендикулярный параллельный оси сверла | 0,13 | 0,14 | 0,18 | 0,2 | 0,24 | 0,27 | 0,32 | 0,38 |
На рисунке 41 показано изменение отклонений диаметра обработанных отверстий в зависимости от количества просверленных роликов.
Анализ табличных данных и построенных по их результатам графиков показывает, что отверстия, обработанные сверлильными головками с перпендикулярным микрорельефом параллельным оси сверла и скрещивающимся под углом 45° микрорельефом направляющих при нескольких просверленных роликах обладают несколько более высокой точностью, чем отверстия, обработанные сверлильными головками с параллельным микрорельефом направляющих перпендикулярным оси сверла. Повышение точности глубоких отверстий после сверления нескольких роликов объясняется более длительным износом направляющих.
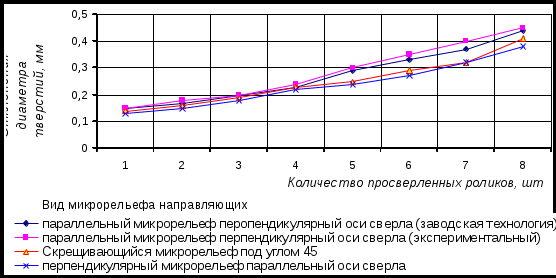
Рисунок 41–Изменение отклонений диаметра обработанных отверстий
Таким образом, можно считать, что увеличение фактической площади контакта направляющих в 2…4 раза приводит к увеличению стойкости сверл на 20 %, характеризуется наибольшей маслоемкостью контакта направляющих поверхностей сверла и способствует повышению точности обрабатываемых отверстий.
Выводы
1. На основании проведенных исследований можно сделать вывод, что способ повышения износостойкости направляющих элементов сверла глубокого сверления, за счет использования резерва микрогеометрии поверхностей, путем изменения угла наклона микронеровностей по отношению к оси инструмента повышает эффективность обработки глубоких отверстий.
2. Предложенный инструмент обладает широкими технологическими возможностями и обеспечивает повышение износостойкости сверл, что повышает эффективность технологии глубокого сверления.
3. Проведенные исследования подтвердили правомерность теоретических результатов и создали основу для широкого использования в машиностроении разработанной технологии сверления глубоких отверстий.
Выводы по работе
Исследованием механизма действия направления микронеровностей на фактическую площадь контакта, маслоемкость стыка направляющих поверхностей сверла с обрабатываемым отверстием и износостойкость сверлильных головок решена актуальная задача повышения эффективности обработки глубоких отверстий, в том числе в труднообрабатываемых материалах. Созданы и внедрены инструменты для обработки глубоких отверстий с повышенной стойкостью.
Выводы:
1. Установлены закономерности влияния топологии направляющих поверхностей сверла на фактическую площадь контакта, маслоемкость стыка с обрабатываемым отверстием и износостойкость сверл малого диаметра, позволяющие на 20 % повысить стойкость сверл.
3. Получены зависимости для определения фактической площади контакта, что позволило установить взаимодействие направляющих сверла и обрабатываемого отверстия при глубоком сверлении с учетом режимов резания и направлений неровностей направляющих поверхностей.
4. Принята конструкция устройства разработанная на ПАО НЛМК для шлифования направляющих сверлильных головок, позволяющая создавать на поверхности направляющих сверла для глубокого сверления микрорельеф с требуемым направлением и отработать режимы подготовки инструмента с различной топологией направляющих поверхностей.
5. Результаты исследования использованы на ОАО «Гидропривод» (г. Елец).