Файл: 1 анализ конструкции автосцепного оборудования применяемого на электорвозах серии 3ЭС5К.docx
Добавлен: 09.01.2024
Просмотров: 481
Скачиваний: 3
ВНИМАНИЕ! Если данный файл нарушает Ваши авторские права, то обязательно сообщите нам.
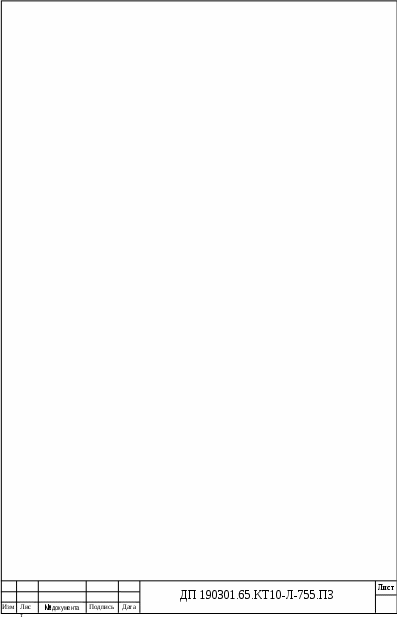
СОДЕРЖАНИЕ
ВВЕДЕНИЕ…………………………………………………………………… 6
1 АНАЛИЗ КОНСТРУКЦИИ АВТОСЦЕПНОГО ОБОРУДОВАНИЯ ПРИМЕНЯЕМОГО НА ЭЛЕКТОРВОЗАХ СЕРИИ 3ЭС5К………………. 8
1.1 Краткая характеристика автосцепки СА-3………………………….. 8
1.2 Установочные размеры автосцепного устройства…………………. 10
1.3 Назначение автосцепного устройства СА-3………………………… 13
1.4 Устройство и конструкция автосцепки СА-3…..…………………… 16
1.5 Работа автосцепки СА-3 (принцип действия)………………………. 20
2 АНАЛИЗ НЕИСПРАВНОСТЕЙ АВТОСЦЕПНОГО
ОБОРУДОВАНИЯ ЭЛЕКТРОВОЗОВ СЕРИИ 3ЭС5К……………….......... 23
2.1 Действующие силы, виды трения и изнашивания
взаимодействующих поверхностей……………………………………... 23
2.2 Основные неисправности автосцепного устройства……………….. 24
2.2.1 Неисправности предохранителя от саморасцепа……………... 27
2.2.2 Неисправности замкодержателя……………………………….. 29
2.2.3 Неисправности замка автосцепки…………………………….... 29
2.2.4 Неисправности валика подъемника……………………………. 30
2.2.5 Неисправности расцепного привода………………………….... 30
2.2.6 Неисправности корпуса автосцепки…………………………… 30
2.2.7 Неисправности поглощающего аппарата……………………… 31
2.2.8 Неисправности корпуса автосцепки…………………………… 33
2.3. Подготовка к ремонту………………………………………………... 35
2.3.1 Разборка механизма автосцепки СА-3………………………… 36
2.3.2 Ремонтные работы по восстановлению автосцепки СА-3…… 36
2.3.3 Сборка автосцепки СА-3……………………………………….. 39
3 РАЗРАБОТКА ТЕХ. КАРТЫ (ТЕХПРОЦЕССА) РЕМОНТА
УСТАНОВКИ АВТОСЦЕПКИ ЭЛЕКТРОВОЗА 3ЭС5К,
ПОЗВОЛЯЮЩЕЙ ОПТИМИЗИРОВАТЬ ПРОИЗВОДСТВО, С ПРИМЕНЕНИЕМ ЭЛЕМЕНТОВ БЕРЕЖЛИВОГО ПРОИЗВОДСТВА…. 41
3.1 Организация рабочего места при внедрении бережливого
производства……………………………………………………………….… 41
3.2 Правила содержания рабочего места……………………………….. 41
3.3 Пути повышения эксплуатационной надежности автосцепных устройств с внедрением бережливого производства…………………. . 42
3.4 Инструменты бережливого производства………………………….. 47
4 ОЦЕНКА ЭКОНОМИЧЕСКОЙ ЭФФЕКТИВНОСТИ ПРИ
ВНЕДРЕНИИ НОВОЙ ТЕХНОЛОГИЧЕСКОЙ КАРТЫ И
ПРИНЦИПОВ БЕРЕЖЛИВОГО ПРОИЗВОДСТВА ДЛЯ
РЕМОНТНОГО ЛОКОМОТИВНОГО ДЕПО «ПРИМОРСКОЕ»………… 49
4.1 Расчет себестоимости при ремонте трещины хвостовика автосцепки СА-3………………………………………………………….. 49
5 БЕЗОПАСНОСТЬ ЖИЗНЕДЕЯТЕЛЬНОСТИ ПРИ РЕМОНТЕ АВТОСЦЕПНОГО УСТРОЙСТВА ЭЛЕКТРОВОЗА 3ЭС5К…………….. 59
5.1 Общие требования безопасности…………………………………… 59
5.2 Требования безопасности перед началом работы…………………. 62
5.3 Требования безопасности во время работы………………………… 63
5.4 Требования безопасности в аварийных ситуациях………………… 65
5.5 Требования безопасности по окончании работы…………………... 67
5.6 Проектирование и расчет естественного освещения КПА отделения локомотивного депо.
ЗАКЛЮЧЕНИЕ………………………………………………………………. 71
ЛИТЕРАТУРА……………………………………………………………….. 73
ВВЕДЕНИЕ
Разработка любого технологического процесса является комплексной задачей, для решения которой в конкретных условиях производства нужно найти оптимальный вариант процесса изготовления или ремонта заданного изделия. Oптимальным является такой вариант прoцесса, который обеспечивает выполнение всех требований конструкторской документации на данное изделие при наименьших производственных затратах.
Pазработка технологических процессов в общем случае включает комплекс взаимосвязанных работ: анализ исходных данных, определение типа производства, выбор действующего процесса-аналога, выбор исходной заготовки и метода ее получения, выбор технологических баз, разработка технологического маршрута, выбор технологического оборудования, разработка технологических операций, выбор инструмента и приспособлений, нормирование технологического процесса, его тарификация, определение техники безопасности, оформление технологических документов, расчеты основных параметров производства, разработка цеховой планировки. Любой технологический процесс может существовать в двух формах: в виде совокупности определенных действий людей и технологического оборудования и в виде комплекта документов, определяющих эти действия. Технологический процесс как комплект документов записывают на специальных бланках. Правила оформления технологической документации установлены стандартами Единой системы технологической документации (ЕСТД), согласно которым документы подразделяют на виды и выполняют строго по определенной форме. К технологическим документам относятся графические и текстовые документы, которые отдельно или в совокупности определяют технологический процесс изготовления изделия и содержат необходимые данные для организации производства.
Настоящий технологический процесс дипломной работы предназначается для ремонта автосцепного устройства электровоза 3ЭC5K и устанавливает порядок ремонта и последовательность выполнения работ.
Целью данного дипломного проекта является разработка тех. карты (техпроцесса) ремонта установки автосцепки электровоза 3ЭC5К. А также оптимизация производства с применением элементов и принципов бережливого производства.
1 АНАЛИЗ КОНСТРУКЦИИ АВТОСЦЕПНОГО ОБОРУДОВАНИЯ ПРИМЕНЯЕМОГО НА ЭЛЕКТОРВОЗАХ СЕРИИ 3ЭС5К
1.1 Краткая характеристика автосцепки СА-3
Для прицепки электровоза к составу служит автоматическая сцепка (автосцепка) СА-3, через которую передается вагонам тяговое или тормозное усилие локомотива.
Автосцепное устройство предназначено для автоматического сцепления единиц подвижного состава и передачи продольных сил. Оно состоит из автосцепки с расцепным приводом, поглощающего аппарата, тягового хомута, ударной розетки, упоров и центрирующего механизма.
Поглощающий аппарат предназначен для амортизации ударов и демпфирования продольных колебаний. Тяговый хомут обхватывает поглощающий аппарат и шарнирно соединен клином с автосцепкой. Он передает силу тяги от автосцепки поглощающему аппарату; от него сила тяги через упоры передается на раму кузова или тележки. При полном срабатывании поглощающего аппарата продольные сжимающие силы от автосцепки передаются непосредственно через розетку на раму.
Автосцепка CA-3 (рисунок 1.1) состоит из двуплечего рычага (6) и цепи (5), соединяющей рычаг с балансиром (4) валика подъемника. Двуплечий рычаг удерживается в фиксированном положении специальным кронштейном. Ударно-центрирующий прибор состоит из ударной розетки (9), двух маятниковых подвесок (8) и балочки (7). Балочка поддерживает автосцепку на определенной высоте от головок рельсов. Подвески, балочка и ударная розетка автоматически центрируют автосцепку относительно продольной оси электровоза.
Автосцепка СА-3 - автоматическое сцепное устройство, применяемое на железнодорожном транспорте России, стран СНГ, Монголии для сцепления
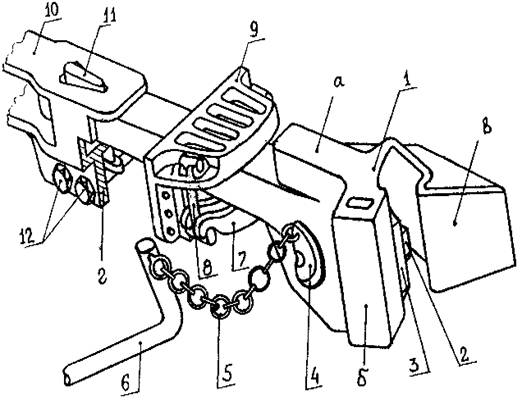
Рисисунок 1.1 - Автосцепка СА-3
между собой единиц подвижного состава с минимальным участием сцепщика. Аббревиатура названия означает «Советская автосцепка, 3-й вариант». При использовании автосцепки СА-3 участие сцепщика сводится лишь к соединению тормозных рукавов и электрических кабелей. Разрывное статическое усилие 200 т.
Автосцепное устройство состоит из:
- корпуса автосцепки с деталями механизма;
- расцепного привода, включающего в себя расцепной рычаг, кронштейн, державку и цепь;
- центрирующего прибора, который включает в себя ударную розетку, две маятниковые подвески и центрирующую балочку;
- упряжного устройства, включающего в себя поглощающий аппарат, тяговый хомут, клин тягового хомута, упорную плиту;
- опорных частей, передних и задних упоров, поддерживающей планки.
Применяемое на российских железных дорогах автосцепное устройство СА-3 изобретено в 1932 г. коллективом авторов под руководством В.Ф. Егорченко. Перевод подвижного состава железных дорог России на автосцепку начался в 1935 г. и был полностью завершен в 1957 г.
Внедрение автосцепного устройства позволило значительно сократить время на формирование подвижных составов, снизить количество травм на железных дорогах за счет ликвидации тяжелого труда сцепщиков.
1.2 Установочные размеры автосцепного устройства
Для надежной работы автосцепного устройства и взаимозаменяемости узлов и деталей основные установочные размеры стандартизированы.
Автосцепка типа СА-3 Стальная литая рама тележки электровоза в передней части имеет специальный карман, в котором размещается поглощающий аппарат. Передние опорные поверхности в кармане для поглощающего аппарата и упорной плиты расположены от передней плоскости концевой балки рамы тележки на расстоянии 390 мм. Между передними и задними упорами кармана расстояние сохранено равным 625 мм Ударная розетка с маятниковым центрирующим устройством укрепляется на концевой балке рамы тележки сваркой или шестью болтами с гайками.
Для обеспечения надежной работы узлов и деталей автосцепного устройства, а также их взаимозаменяемости основные установочные размеры должны отвечать ГОСТ 3475—81. Этот стандарт распространяется на подвижной состав железных дорог (колеи 1520 мм как вновь строящихся, так и существующих, за исключением специального, например автомотрис, а также вагонов электропоездов).
Основные размеры при прилегании автосцепки (2) к упорной плите (3) приведены на (рисунке 1.2)
Расстояние (L) от нижней перемычки переднего упора до тягового хомута и расстояние (l) между опорными поверхностями розетки и упора зависят от размера хода (сжатия) поглощающего аппарата и соответственно при ходе 70 мм равны не менее 80 мм и не более 575 мм, а при ходе более 70 мм устанавливаются в соответствии с выбранным ходом. Такое соотношение размеров позволяет уменьшить длину ударной розетки (8) при установке поглощающего аппарата с увеличенным ходом до 120 мм.