Файл: В дальнейшем стали применять метод укладки трубопровода с плавучих средств.docx
ВУЗ: Не указан
Категория: Не указан
Дисциплина: Не указана
Добавлен: 10.01.2024
Просмотров: 36
Скачиваний: 1
ВНИМАНИЕ! Если данный файл нарушает Ваши авторские права, то обязательно сообщите нам.
Введение
Развитие добычи нефти и газа на многих морях привело к необходимости строительства подводных морских трубопроводов различного назначения.
Первые подводные трубопроводы на Каспий начали прокладывать с конца 40-х и начала 1950 годов. Незначительное удаление нефтепромысловых акваторий Каспия от берега, небольшие глубины моря и потребность в трубопроводах малого диаметра предопределили технику и технологию строительства трубопроводов.
Первые трубопроводы диаметром 63-114 мм прокладывали методом протаскивания по дну моря с помощью буровой лебедки.
В дальнейшем стали применять метод укладки трубопровода с плавучих средств.
Начало строительства подводных магистральных трубопроводов связано с открытием газового месторождения Южное в 60-х годах. Для транспортирования газа с этого месторождения на сушу потребовалось строительство магистрального газопровода в условиях открытого моря. Удаленность района добычи газа от берега обусловила разработку новой технологией строительства трубопроводов, по которой заготовка километровых плетей, их антикоррозионная изоляция, балластировка, оснастка транспортными понтонами производятся на береговой монтажно-сварочной площадке. При благоприятной погоде километровые плети с монтажной площадки сбрасывают в море и на плаву транспортируют в район строительства, где вместе с понтонами затапливают по трассе (метод свободного погружения). Отдельные плети трубопровода стыкуют на 40-тонном крановом судне, специально оборудованном для этой цели.
Для транспортировки плетей на плаву институт «Гипроморнефтегаз» разработал специальные понтоны с замковым устройством для автоматического отсоединения понтонов от трубопровода с поверхности воды без участия водолазов.
К настоящему времени по указанной технологии построены сотни километров подводных трубопроводов диаметром до 500 мм на глубинах моря до 30 м.
Практика показала, что укладка подводных трубопроводов методом свободного погружения успешно может быть применена при их строительстве буксировкой плетей на расстояние до 50- 60 км при волнении моря до двух баллов включительно.
1 Трубоукладочные баржи
После извлечения продукта из земли, он должен транспортироваться с моря на берег. Одновременно с монтажом добывающего оборудования, трубоукладочные баржи и бригады занимаются укладкой трубопровода для транспортировки нефти и газа от платформы до места назначения (рисунок 1.1).
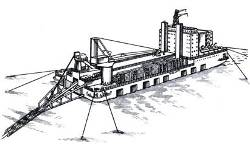
Рисунок 1.1 - Трубоукладочная баржа
Длина этих барж может доходить до 150 метров, а укладываемые ими трубы - до 1525 мм в диаметре. Трубы обычно поставляются длиной 12 метров, и могут быть покрыты бетоном для утяжеления. Трубы привариваются друг к другу вдоль линии сборки, проходящей по длине баржи. Вдоль этой линии расположен ряд сварочных постов, где работают высококвалифицированные сварщики на высокоэффективных сварочных машинах.
По мере перемещения каждой следующей трубы на сварочный участок, она становится частью трубопровода, который проходит через корму баржи ко дну моря, и, наконец, к терминалу, находящемуся на расстоянии в несколько сотен миль. Со сварочного участка трубопровод перемещается на участок рентгеноскопии, где каждый новый сварной шов проверяется на наличие дефектов в соединении. Если дефектов не обнаружено, сварной шов покрывается антикоррозийной изоляцией.
По мере увеличения длины трубопровода баржа перемешается вперед, каждый раз на несколько метров. После каждого перемещения баржи новый участок трубопровода, приваренный, подвергнутый рентгеноскопии и заизолированный, спускается с кормы в воду, вниз по наклонной площадке, называемой стингером. Стингер поддерживает трубу до некоторого расстояния под водой и направляет ее под небольшим углом на морское дно.
По мере движения трубоукладочной баржи, она тянет за собой плуг, который роет траншею на морском дне. Трубопровод укладывается в траншею, где он будет защищен от повреждения путем естественной замывки или засыпки. Морские течения перемещают песок, вырываемый плугом, обратно в траншею, покрывая трубопровод.
В процессе укладки труб водолазы постоянно инспектируют стингер и трубопровод. Они следят за отсутствием препятствий на морском дне, правильной укладкой трубопровода и надлежащим положением стингера.
Затем, после завершения укладки трубопровода к платформе, водолазы подсоединяют его к стояку, участку трубопровода, который поднимается с морского дна к палубе и крепится к конструкции.
До эксплуатации трубопровода он должен быть спрессован и проверен на плотность. Аналогично, все оборудование на палубе, трубопровод и проводка, клапаны и переключатели, насосы и системы, извлекающие сырую нефть из земли, очищающие ее и проталкивающие ее в сторону берега, должны быть многократно испытаны, чтобы убедиться в безотказной работе и отсутствии опасности для человека или окружающей среды.
Позже укладка глубоководных трубопроводов была выполнена по новой технологии, сущность которой заключается в том, что для регулирования напряжения в трубопроводе в процессе его погружения на дно моря были применены разгружающие понтоны взамен направляющего устройства - стингера. Это позволило значительно уменьшить изгиб трубопровода и тем самым обеспечить безаварийную его укладку в жестких гидрометеорологических условиях.
Трубопроводы могут быть проложены в различные места. Одни ведут к морским сборочным станциям, где нефть и газ подвергаются дальнейшему разделению, направляются обратно в трубопровод и к берегу для дополнительной переработки.
Другие трубопроводы заканчиваются на берегу в больших нефтебазах, где жидкие углеводороды хранятся для последующего распределения по нефтеперерабатывающим заводам. Углеводороды могут транспортироваться по подземному трубопроводу прямо на нефтеперерабатывающий завод, или к морскому терминалу для погрузки на танкеры, направляющиеся в другие части света.
Несколько танкеров могут загружаться и разгружаться с многопричального терминала, или один танкер может загружаться и разгружаться в системе с заякориванием буя.
Многопричальные терминалы находятся в зонах, укрытых от суровой погоды. Они погружают или разгружают нефтепродукты с помощью гигантских стрел, спроектированных с целью компенсации перемещения судна, вызванного приливами и отливами или меняющейся нагрузкой.
При системе с заякориванием буя танкер соединяется шлангами крупного диаметра с шарнирным соединением. Свободное перемещение соединения обеспечивает возможность загрузки нефти независимо от перемещения судна вследствие течений и волн.
С танкеров или береговых нефтебаз, сырая нефть и природный газ поступают на береговой завод, где они перерабатываются в продукты для нефтяной, газовой и химической промышленности. На этих заводах углеводороды становятся ингредиентами для многочисленных продуктов, с которыми мы ежедневно соприкасаемся. Они превращаются в бензин и моторное масло, в синтетические ткани и пластмассы, в асфальт и другие промышленные продукты, и в топливо для промышленности и наших домов.
2 Укладка трубопроводов с применением
наклонных стингеров и j-методом
При способе укладки морских трубопроводов, включающем буксировку плетей трубопровода на плаву или по дну моря, для изготовления плетей на берегу моря используют две схемы организации работ. Первая схема — секции труб изготовляют в базовых условиях, а затем перевозят на береговую монтажно-сварочную площадку для сварки их в длинномерные плети (до 2 км). Вторая схема предусматривает доставку труб непосредственно на береговую площадку, где их
стыкуют и сваривают, в плети.
Подобная технология была использована при строительстве четырех ниток (протяженностью 18 км каждая) морского газопровода Апшерон — о. Жилой на Каспийском море. На береговой монтажной площадке было организовано массовое производство секций труб длиной 100 м с применением автоматической сварки поворотных стыков труб под флюсом. Использовалась полевая сварочная установка ПАУ-500 для сварки труб диаметром 219—1020 мм, включающая сварочный агрегат АСДП-500, торцевой вращатель, шесть роликовых опор и сварочную головку ПТ-56. При изготовлении плетей трубопровода применялась неповоротная сварка межсекционных стыков вручную — электродами УОНИ 13/45.
Монтаж трубопровода на трубоукладочном судне проводится конвейерным способом на его палубе (рисунок 2.1). Технологический процесс начинается с подачи труб с трубных стеллажей на поперечный конвейер краном грузоподъемностью 100 т. Поперечный конвейер является начальным звеном технологической линии, расположенной вдоль правого борта судна. С него труба подается на две центровочные тележки с вращающимися роликоопорами.
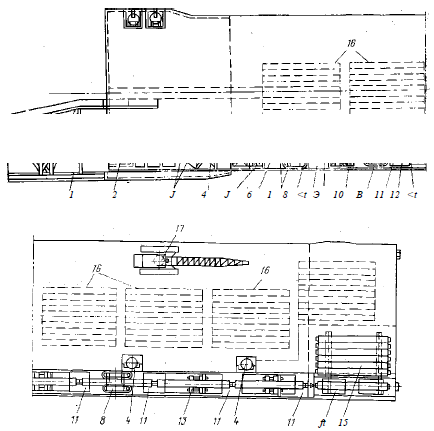
Рисунок 2.1 - Монтажно-сварочная линия на трубоукладочном судне «Сулейман Везиров»:
1 - стингер; 2 - поворотный кран; 3 - бетономешалка; 4 - кранбалки;
5 - пункт обетонирования стыков; 6 - монорельс; 7 - котлы для варки битума; 8 - натяжные устройства; 9 - пункт изоляции стыков; 10 - помещение для контрольных приборов; 11- сварочные посты; 12 - пункт рентгеноскопии стыков труб; 13 - роликовые опоры; 14 – центровочные тележки;
15 - поперечный конвейер; 16 - стеллажи для труб; 17 - гусеничный кран (грузоподъемность 100 т)
Центровочные столы тележек могут перемещать трубу в вертикальной и горизонтальной плоскостях. Когда труба становится соосной с трубопроводом, на стыке устанавливается центратор, затем производится сварка двух первых слоев. После этого стык очищается металлической щеткой и нейлоновым шлифовальным кругом. По сигналу оператора весь трубопровод с помощью натяжного устройства перемещается на 12 м. По мере перемещения трубопровода на следующих трех сварочных постах происходит накладывание очередных слоев шва. На пятом посту осуществляется контроль качества сварного шва методом рентгеноскопии, на следующих постах — изоляция и обетонирование стыков труб.
Для работы в мелководных районах шельфа, а также на внутренних водных переходах (водохранилища, реки) может использоваться специальное трубоукладочное судно, разработанное во ВНИИСТе, отличительной особенностью которого является способность без демонтажных работ передислоцироваться из одного водного бассейна в другой по внутренним водным путям (например, с Азовского моря в Куйбышевское водохранилище). Ширина судна не превышает 16 м, а осадка в рабочем положении составляет 1,5—2 м. Для улучшения мореходных свойств на судне дополнительно на каждом борту предусмотрены понтоны, которые в рабочем положении представляют собой как бы дополнительные корпуса, увеличивают ширину судна и инерцию при качке. В транспортном положении эти понтоны с помощью гидродомкратов устанавливают на основном корпусе, уменьшая его ширину до минимальной. В кормовой части судна имеется короткий разгрузочный стингер с одной опорой на конце, а в средней части — натяжной механизм небольшой мощности.
В морях с суровыми гидрометеорологическими условиями применяют полупогружные трубоукладочные суда, конструкция которых позволяет работать при сильных волнении, ветре и течении. Одним из новых судов подобного типа является судно-трубоукладчик «Castoro-VI» (рисунок 2.2). Оно имеет понтон, колонны и верхнюю рабочую площадку. Колонны поддерживают верхнюю рабочую площадку, на которой расположены оборудование для укладки труб, трубы и жилые помещения. Во время транспортировки к месту работы судно плавает с минимальным балластом в корпусе (лишь для дифферентовки). На месте работы оно принимает балласт в отсеки понтонов и погружается на заданную глубину. В рабочем положении понтоны находятся под водой, при укладке трубопроводов верхняя рабочая площадка — над водой вне зоны волнового воздействия, понтоны и нижняя часть колонн — под водой (в зоне ослабленного волнового воздействия). Широко расставленные колонны, большая инерция подводных частей корпуса судна создают большую устойчивость при волнении. Судно способно работать при высоте волны 5,4 м, скорости ветра 25 м/с, скорости течения 1 м/с. При отстое без проведения трубоукладочных работ оно выдерживает волны высотой до 24 м и скорость ветра 50 м/с. Таких высоких показателей не имеют трубоукладочные суда других конструкций.
Судно «Castoro-VI» помимо якорной системы удержания, состоящей из 12 якорей, имеет четыре гребных винта с приводом от электродвигателей мощностью 2060 кВт каждый. Винты установлены по углам понтонов на поворотных рулевых насадках. Имеющаяся на судне ЭВМ позволяет управлять процессом укладки труб и движителями, т. е. использовать гребные винты для динамического позиционирования в процессе укладки.