ВУЗ: Не указан
Категория: Не указан
Дисциплина: Не указана
Добавлен: 12.01.2024
Просмотров: 101
Скачиваний: 2
ВНИМАНИЕ! Если данный файл нарушает Ваши авторские права, то обязательно сообщите нам.
МИНИСТЕРСТВО ОБРАЗОВАНИЯ САРАТОВСКОЙ ОБЛАСТИ Государственное автономное профессиональное образовательное учреждение Саратовской области «Энгельсский политехникум»
КУРСОВОЙ ПРОЕКТ
ПМ.01 Организация деятельности производственного подразделения электромонтажной организации
Тема: Электрооборудование станка модели 16К20
Студент группы МЭ-317/20: Коршак Е.Д
Руководитель: С.В. Щербаков
Энгельс 2022г
Содержание:
-
Введение…………………………………………………………………2-3
-
Устройство и органы станка……………………………………………4-6
-
Техническая характеристика……………………………………………7-8
-
Элементарные механизмы и передачи………………………………...9-10
-
Основные характеристики передач…………………………………..11-12
-
Зубчатые передачи, их преимущества и недостатки…………………...13
-
Классификация зубчатых передач……………………………………….14
-
Планетарные передачи, их преимущества и недостатки …………..15-16
-
Червячные передачи и их видов……………………………………...17-19
-
Волновые передачи, их преимущества и недостатки………………20-21
-
Фрикционные передачи и их виды…………………………………..22-25
-
Ременные передачи и их применения ………………………………26-27
-
Цепные передачи, их преимущества и недостатки………………...28-29
-
Передача винт-гайка, и её работа……………………………………30-31
-
Рычажные механизмы……………………………………………………32
-
Правила техники безопасности эксплуатации электрооборудования станка модели 16К20………………………………………………….33-35
Заключение………………………………………………………………..36
Список литературы…………………………………………………….....37
Дополнительная литература……………………………………………...38
1.Введение
Токарный станок модели 16К20 является типичным и наиболее распространенным представителем класса токарно-винторезных станков.
Станки этого класса - универсальные станки токарной группы и предназначены для обработки деталей типа дисков, валов, втулок и обеспечивают обработку точением внутренних и наружных цилиндрических, конических, торцевых, фасонных поверхностей, прорезку канавок и отрезку, сверление, зенкерование и развертывание отверстий, нарезание различных типов наружных и внутренних резьб резцами, метчиками и плашками, а также накатывание рифленых поверхностей, выглаживание и раскатку поверхностей. Станки такого типа применяются в основном в единичном и мелкосерийном, а также в ремонтном производстве.
Характерными размерами станков токарной группы являются наибольший диаметр обработки над станиной (характеризует наибольший диаметр заготовки обрабатываемой на станке) и расстояние между центрами характеризует наибольшую длину обрабатываемой заготовки).
Устройство и органы управления токарного станка 16К20
-
ручка установки подачи и шага резьбы;
-
ручка установки подачи и типа нарезаемой резьбы;
-
установка частоты вращения шпинделя;
-
установка основного или крупного шага резьбы;
-
автоматический выключатель;
-
сигнальная лампа;
-
выключение насоса подачи СОЖ;
-
указатель нагрузки станка;
-
установка направления резьбы (левое, правое);
-
установка ряда чисел оборотов шпинделя;
-
управление фрикционной муфтой главного привода;
-
лампа местного освещения;
-
закрепление и поворот резцовой головки;
-
ручное перемещение резцовых салазок;
-
крепление пиноли задней бабки станка;
-
маховик перемещения пиноли задней бабки;
-
управление фрикционной муфтой главного привода;
-
включение и выключение гайки ходового винта;
-
управление перемещениями каретки и поперечных салазок суппорта;
-
включение и выключение электродвигателя;
-
ручное перемещение салазок суппорта;
-
маховик ручного перемещения каретки;
-
смазка направляющих каретки и поперечных салазок суппорта;
-
установка подачи и шага резьбы и отключения коробки подач при нарезании резьбы напрямую;
-
зажим пиноли задней бабки;
-
станина станка;
-
шпиндельная бабка;
-
задняя бабка;
-
суппорт;
-
резцовая головка;
-
фартук;
-
коробка подач;
-
коробка передач.
2.Устройство и органы станка
Рисунок 1 - Устройство и органы управления токарного станка 16К20
Основание - чугунная отливка прямоугольной формы. В основании расположены приводной электродвигатель, агрегат гидростатики и охлаждения.
Станина - деталь, на которой установлены основные узлы станка. В верхней части станина имеет направляющие, по которым перемещаются суппорт и задняя бабка станка.
В передней бабке собраны коробка скоростей и шпиндельный узел. Шпиндель передает заготовке вращающий момент посредством приспособлений. Для установки и центрирования приспособлений служат фланец , коническая шейка - для установки патронов, а также коническое отверстие – для установки центров. В токарных станках это отверстие выполняют по конусу Морзе. Передние концы шпинделей стандартизованы (для токарных станков с фланцевыми передними концами шпинделей ГОСТ 12593-81).
Гитара служит для настройки цепи подач с помощью подбора сменных зубчатых колес на нарезание метрической , дюймовой , модульной , питчевой резьб, а также для настройки на шаг (ход) резьбы при нарезании нестандартных резьб. В двупарных гитарах расстояние L между валом I; валом II является постоянным. На валу II свободно установлен приклон, который крепится к стенке шпиндельной бабки с помощью болта .
Фартук - механизм для преобразования вращения ходового винта или ходового вала в поступательное перемещение суппорта. Суппорт получает поступательное перемещение от ходового винта посредством разъемной гайки, от
ходового вала - через ряд зубчатых передач посредством зубчато-реечной передачи.
Рисунок 2 - Фартук токарного станка 16к20
Суппорт - служит для установки режущего инструмента и сообщения ему движения подачи. Суппорт состоит (рис. 3) из каретки продольного перемещения 4, поперечных салазок 5, по воротной части 6, резцовой каретки 7 с резцедержателем 8. Резцовая каретка может устанавливаться под углом к оси центров станка для обработки конических поверхностей.
Рисунок 3 - Суппорт токарно-винторезного станка 16к20
3.Техническая характеристика
Техническая характеристика токарно-винторезного станка по металлу модели 16к20
| | |
Введение…………………………………………………………………2-3
Устройство и органы станка……………………………………………4-6
Техническая характеристика……………………………………………7-8
Элементарные механизмы и передачи………………………………...9-10
Основные характеристики передач…………………………………..11-12
Зубчатые передачи, их преимущества и недостатки…………………...13
Классификация зубчатых передач……………………………………….14
Планетарные передачи, их преимущества и недостатки …………..15-16
Червячные передачи и их видов……………………………………...17-19
Волновые передачи, их преимущества и недостатки………………20-21
Фрикционные передачи и их виды…………………………………..22-25
Ременные передачи и их применения ………………………………26-27
Цепные передачи, их преимущества и недостатки………………...28-29
Передача винт-гайка, и её работа……………………………………30-31
Рычажные механизмы……………………………………………………32
Правила техники безопасности эксплуатации электрооборудования станка модели 16К20………………………………………………….33-35
ручка установки подачи и шага резьбы;
ручка установки подачи и типа нарезаемой резьбы;
установка частоты вращения шпинделя;
установка основного или крупного шага резьбы;
автоматический выключатель;
сигнальная лампа;
выключение насоса подачи СОЖ;
указатель нагрузки станка;
установка направления резьбы (левое, правое);
установка ряда чисел оборотов шпинделя;
управление фрикционной муфтой главного привода;
лампа местного освещения;
закрепление и поворот резцовой головки;
ручное перемещение резцовых салазок;
крепление пиноли задней бабки станка;
маховик перемещения пиноли задней бабки;
управление фрикционной муфтой главного привода;
включение и выключение гайки ходового винта;
управление перемещениями каретки и поперечных салазок суппорта;
включение и выключение электродвигателя;
ручное перемещение салазок суппорта;
маховик ручного перемещения каретки;
смазка направляющих каретки и поперечных салазок суппорта;
установка подачи и шага резьбы и отключения коробки подач при нарезании резьбы напрямую;
зажим пиноли задней бабки;
станина станка;
шпиндельная бабка;
задняя бабка;
суппорт;
резцовая головка;
фартук;
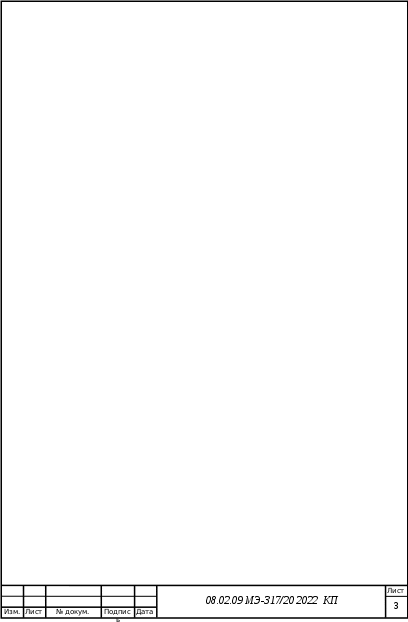
коробка передач.
Основные параметры | 16к20 |
Наибольший диаметр обработки, мм: | |
над станиной | 400 |
над поперечным суппортом | 200 |
Наибольший диаметр обрабатываемого прутка, мм | 50 |
Расстояние между центрами, мм | 710 1400 |
Диапазон частот вращения шпинделя, об/мин | 12.5 |
Диапазон подач, мм/об: | 1600 |
продольных | 0.05-2.8 |
поперечных | 0.025-1.4 |
Мощность главного электродвигателя, кВт | 10 |
Масса станка, кг | 2835 |
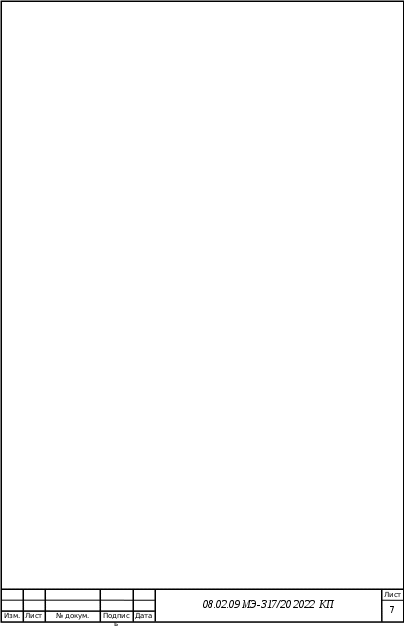
2 означает, что станок второй группы (сверлильный), цифра 1 — вертикальный, 35 — максимально допустимый условный диаметр сверления в стали средней прочности 650 МПа.
Шлифовальная бабка имеет только вертикальную подачу. Вращение и продольная подача стола гидравлические (модель-3740).
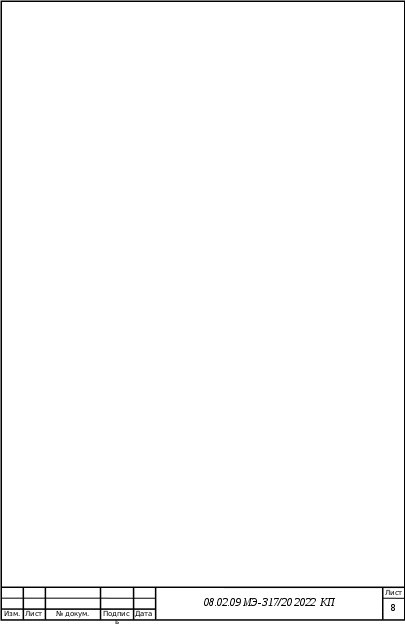
Шлифование плоских поверхностей заготовок производится периферией круга или его торцом. Существуют плоскошлифовальные станки с прямоугольным и круглым столами. Расположение шпинделя шлифовального круга может быть горизонтальным или вертикальным. В единичном, мелкосерийном и среднесерийном производстве наиболее часто используют плоскошлифовальные станки с прямоугольным столом и горизонтальным шпинделем. В массовом производстве наибольшее распространение получили станки с круглым столом, а также двусторонние торце шлифовальные станки с горизонтальным и вертикальным расположением шпинделей.
4. Элементарные механизмы и передачи
Элементарные передающие механизмы (передачи) – ременные, зубчатые, цепные, реечные, кулачковые и др.
Механической передачейназывают устройство для передачи механического движения от двигателя к исполнительным органам машины. Может осуществляться с изменением значения и направления скорости движения, с преобразованием вида движения. Необходимость применения таких устройств обусловлена нецелесообразностью, а иногда и невозможностью непосредственного соединения рабочего органа машины с валом двигателя. Механизмы вращательного движения позволяют осуществить непрерывное и равномерное движение с наименьшими потерями энергии на преодоление трения и наименьшими инерционными нагрузками.
Механические передачи вращательного движения делятся:
- по способу передачи движения от ведущего звена к ведомому на передачи трением (фрикционные, ременные) и зацеплением (цепные, зубчатые, червячные);
- по соотношению скоростей ведущего и ведомого звеньев на замедляющие (редукторы) и ускоряющие (мультипликаторы);
- по взаимному расположению осей ведущего и ведомого валов на передачи с параллельными, пресекающимися и перекрещивающимися осями валов.
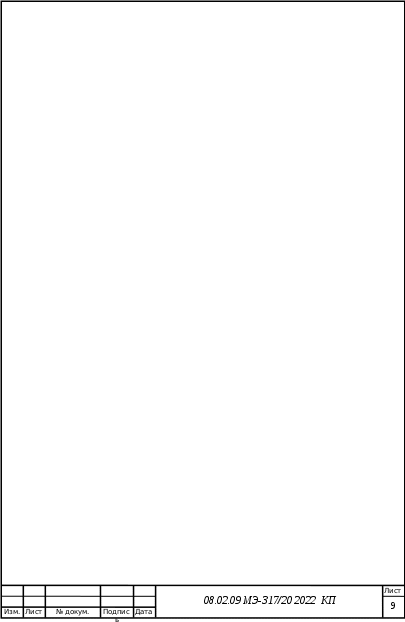
вращения уменьшаются силы и моменты, действующие на детали двигателя. Например, передавать вращение от быстроходной газовой турбины на вал несущего винта вертолета через специальную замедляющую зубчатую передачу (редуктор) значительно выгоднее, чем применять имеющий большие габаритные размеры и массу тихоходный двигатель, вал которого соединялся бы непосредственно с винтом. Из всех типов передач наиболее распространенными являются зубчатые.
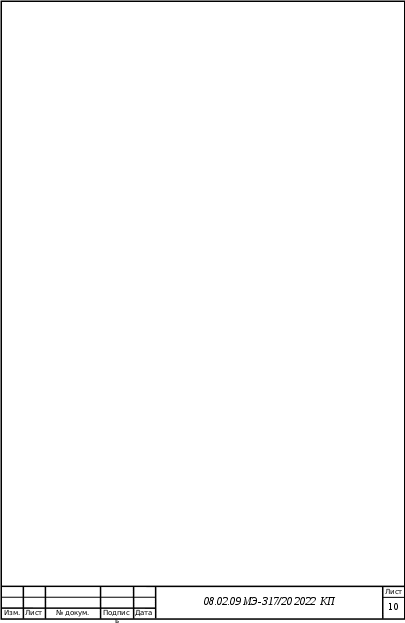
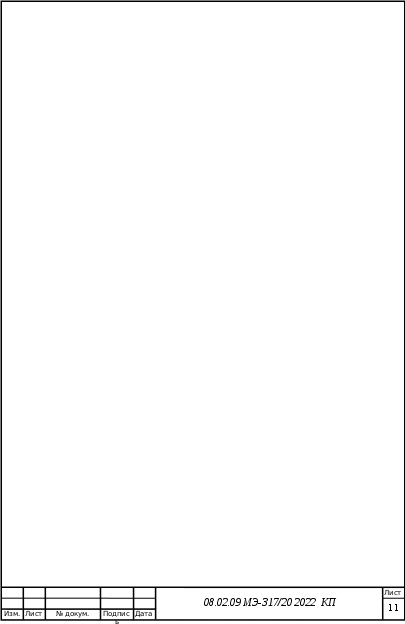
5. Основные характеристики передач
мощность Р1 на входе и Р2 на выходе, Вт; мощность может быть выражена через окружную силу Ft (Н) и окружную скорость V (м/с) колеса, шкива, барабана и т.п.:
Р = Ft×V;
быстроходность, выражающаяся частотой вращения n1 на входе и n2 на выходе, мин–1, или угловыми скоростями ω1 и ω2 , с-1;
передаточное отношение– отношение угловой скорости ведущего звена к угловой скорости ведомого звена: по формуле (1)
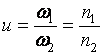
при u > 1, n1 > n2 – передача понижающая, или редуктор,
при u < 1, n1 < n2 – передача повышающая, или мультипликатор;
коэффициент полезного действия(КПД) по формуле (2)


где Рr – мощность, потерянная в передаче.
Одноступенчатые передачи имеют следующие КПД: фрикционные – 0,85…0,9; ременные – 0,90…0,95; зубчатые – 0,95…0,99; червячные – 0,7…0,9; цепные – 0,92…0,95;
моменты на валах. Моменты Т1 (Н·м) на ведущем и Т2 на ведомом валах определяют по мощности (кВт) и частоте вращения (об./мин) или угловой скорости (с-1):
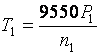
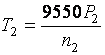

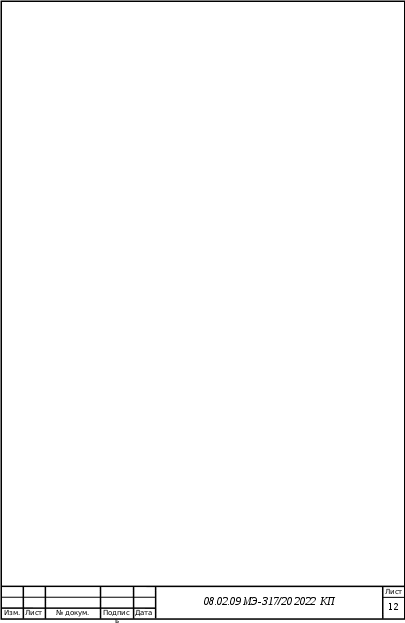

Связь между вращающими моментами на ведущем Т1 и ведомом Т2 валах выражается через передаточное отношение u и КПД η:по формуле (5)
Т2 = Т1 η u. (5)

6. Зубчатые передачи, их преимущества и недостатки
Зубчатой передачей называется трехзвенный механизм, в котором два подвижных звена являются зубчатыми колесами, или колесо и рейка с зубьями, образующими с неподвижным звеном (корпусом) вращательную или поступательную пару.
Зубчатая передача состоит из двух колес, посредством которых они сцепляются между собой. Зубчатое колесо с меньшим числом зубьев называют шестерней, с большим числом зубьев – колесом.
Термин «зубчатое колесо» является общим. Параметрам шестерни приписывают индекс 1, а параметрам колеса – 2.
Основными преимуществами зубчатых передач являются:
- постоянство передаточного числа (отсутствие проскальзывания);
- компактность по сравнению с фрикционными и ременными передачами;
- высокий КПД (до 0,97…0,98 в одной ступени);
- большая долговечность и надежность в работе (например, для редукторов общего применения установлен ресурс 30 000 ч);
- возможность применения в широком диапазоне скоростей (до 150 м/с), мощностей (до десятков тысяч кВт).
Недостатки:
- шум при высоких скоростях;
- невозможность бесступенчатого изменения передаточного числа;
- необходимость высокой точности изготовления и монтажа;
- незащищенность от перегрузок;
- наличие вибраций, которые возникают в результате неточного изготовления и неточной сборки передач.
7. Классификация зубчатых передач.
По расположению осей валов различают передачи с параллельными, с пересекающимися и перекрещивающимися геометрическими осями.
По форме могут быть цилиндрические, конические, эллиптические, фигурные зубчатые колеса и колеса с неполным числом зубьев (секторные).
По форме профилей зубьев различают эвольвентные и круговые передачи, а по форме и расположению зубьев – прямые, косые, шевронные и круговые.
В зависимости от относительного расположения зубчатых колес передачи могут быть с внешним или внутренним их зацеплением. Для преобразования вращательного движения в возвратно поступательное и наоборот служит реечная передача.
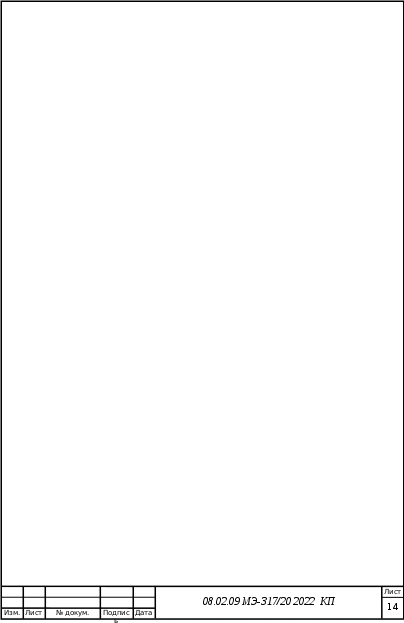
распространение имеют передачи с цилиндрическими колесами, как наиболее простые в изготовлении и эксплуатации, надежные и малогабаритные. Конические, винтовые и червячные передачи применяют лишь в тех случаях, когда это необходимо по условиям компоновки машины.
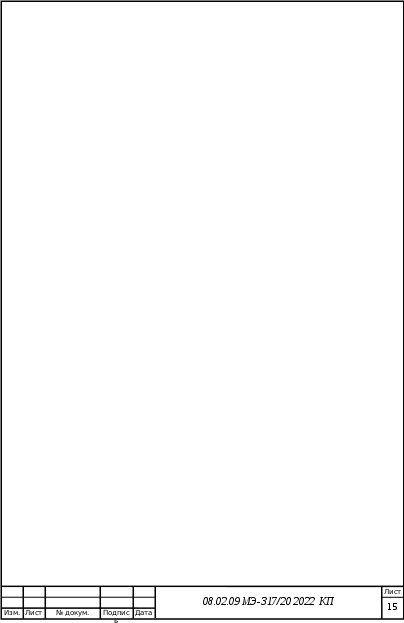