Файл: Н. Н. Бенардос и Н. Г. Славянов положили начало автоматизации сварочных процессов. Однако в условиях царской России их изобретения не нашли большого применения. Только после Великой Октябрьской социалистической револ.rtf
ВУЗ: Не указан
Категория: Не указан
Дисциплина: Не указана
Добавлен: 12.01.2024
Просмотров: 98
Скачиваний: 1
ВНИМАНИЕ! Если данный файл нарушает Ваши авторские права, то обязательно сообщите нам.
Введение
Сварка - технологический процесс получения неразъёмного соединения посредством установления межатомных и межмолекулярных связей между свариваемыми частями изделия при их нагреве (местном или общем), или пластическом деформировании.
В 1802 году впервые в мире профессор физики Санкт-Петербургской медико-хирургической академии В.В. Петров (1761-1834 гг.) открыл электрическую дугу и описал явления, происходящие в ней, а также указал на возможность её практического применения.
В 1881 году русский изобретатель Н.Н. Бенардос (1842-1905 гг.) применил электрическую дугу для соединения и разъединения стали. Дуга Н.Н. Бенардоса горела между угольным электродом и свариваемым металлом. Присадочным прутком для образования шва служила стальная проволока. В качестве источника электрической энергии использовались аккумуляторные батареи. Сварка, предложенная Н.Н. Бенардосом, применялась в России в мастерских Риго-Орловской железной дороги при ремонте подвижного состава. Н.Н. Бенардосом были открыты и другие виды сварки: контактная точечная сварка, дуговая сварка несколькими электродами в защитном газе, а также механизированная подача электрода в дугу.
В 1888 году русский инженер Н.Г. Славянов (1854-1897 гг.) предложил дуговую сварку плавящимся металлическим электродом. Он разработал научные основы дуговой сварки, применил флюс для защиты металла сварочной ванны от воздействия воздуха, предложил наплавку и сварку чугуна. Н.Г. Славянов изготовил сварочный генератор своей конструкции и организовал первый в мире электросварочный цех в Пермских пушечных мастерских, где работал с 1883 по 1897 г.
Н.Н. Бенардос и Н.Г. Славянов положили начало автоматизации сварочных процессов. Однако в условиях царской России их изобретения не нашли большого применения. Только после Великой Октябрьской социалистической революции сварка получает распространение в нашей стране. Уже в начале 20-х гг. под руководством профессора В.П. Вологдина на Дальнем Востоке производили ремонт судов дуговой сваркой, а также изготовление сварных котлом, а несколько позже - сварку судов и ответственных конструкций.
Развитие и промышленное применение сварки требовало разработки и изготовления надёжных источников питания, обеспечивающих устойчивой горение дуги. Такое оборудование - сварочный генератор СМ-1 и сварочный трансформатор с нормальным магнитным рассеянием СТ-2 - было изготовлено впервые в 1924 году Ленинградским заводом «Электрик». В том же году советский учёный В.П. Никитин разработал принципиально новую схему сварочного трансформатора типа СТН. Выпуск таких трансформаторов заводом «Электрик» начал с 1927 г.
В 1928 году учёный Д.А. Дульчевский изобрёл автоматическую сварку под флюсом.
Новый этап в развитии сварки относится к концу 30-ых годов, когда коллективом института электросварки АН УССР под руководством академика Е.О. Патона был разработан промышленный способ автоматической сварки под флюсом. Внедрение его в производство началось с 1940 г. Сварка под флюсом сыграла огромную роль в годы войны при производстве танков, самоходных орудий и авиабомб. Позднее был разработан способ полуавтоматической сварки под флюсом.
В конце 40-ых годов получила промышленное применение сварка в защитном газе. Коллективами Центрального научно-исследовательского института технологий машиностроения и Института электросварки имени Е.О. Патонова разработана и в 1952 году внедрена полуавтоматическая сварка в углекислом газе.
Огромным достижением сварочной техники явилась разработка коллективом ИЭС в 1949 году электрошлаковой сварки, позволяющей сваривать металлы практически любой толщины.
Авторы сварки в углекислом газе плавящимся электродом и электрошлаковой сварки К.М. Новожилив, Г.З. Волошкевич, К.В. Любавский и др. удостоены Ленинской премии.
В последующие годы в стране стали применяться: сварка ультразвуком, электронно-лучевая, плазменная, диффузионная, холодная сварка, сварка трением и др. Большой вклад в развитие сварки внесли учёные нашей страны: В.П. Вологдин, В.П. Никитин, Д.А. Дульчевский, Е.О. Патонов, а также коллективы Института электросварки имени Е.О. Патонова, Центрального научно-исследовательского института технологии машиностроения, Всесоюзного научно-исследовательского и конструктивного института автогенного машиностроения, Института металлургии имени А.А. Байкова, ленинградского завода «Электрик» и др.
1. Наименование конструкции
Тяга представляет собой сварную металлоконструкцию, детали изготовлены из листового проката 09Г2С.
Габаритные размеры изделия - 2060 х 278 х 435 мм.
Вес - 337 кг.
Рама состоит из следующих деталей:
деталь «Щека» поз. 1 - 2 шт.;
деталь «Валик» поз. 2 - 1 шт.;
деталь «Накладка» поз. 3 - 2 шт.;
деталь «Ребро» поз. 4 - 1 шт.;
деталь «Ребро» поз. 5 - 1 шт.;
деталь «Ребро» поз. 6 - 2 шт.;
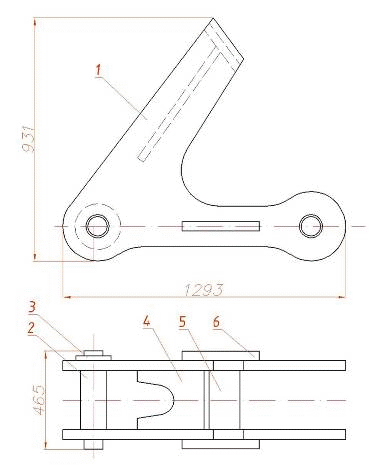
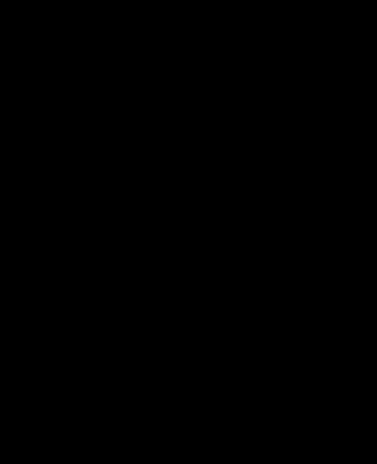
Рис. 1 - Петля
2.
Характеристика металла конструкции. Расчет Сэкв
Конструкция изготавливается из стали 09Г2С, которая обладает хорошей свариваемостью.
Химический состав и механические свойства стали 09Г2С представлены в таблицах 2.1 и 2.2.
Таблица 2.1 - Химический состав стали 09Г2С, %
Марка стали | ГОСТ | С | Si | Mn | Cr | Ni | Cu | S | P |
| | Не более | | | Не более | ||||
09Г2С | 19282-73 | 0,12 | 0,5-0,8 | 1,3-1,7 | 0,30 | 0,30 | 0,30 | 0,040 | 0,035 |
Таблица 2.2 - Механические свойства стали 09Г2С
Марка стали | ГОСТ | ![]() ![]() | | |
| | не менее | не менее | не менее |
09Г2С | 19282-73 | 305 | 460 | 21 |
Температура ковки, 0С: начала 1250, конца 850.
Свариваемость - сваривается без ограничений. Способы сварки - РДС, АДС под флюсом и газовой защитой, ЭШС.
Легирующие элементы Mn, Si, Cr, Cu, Ni - растворяются в феррите, упрочняют его и измельчают перлит. Благодаря этому прочностные характеристики такой стали повышаются и предел прочности доходит до 55 кг/мм
². Наличие в стали Мn повышает ее ударную вязкость и хладноломкость, обеспечивает хорошую свариваемость. Введение в состав стали Мn позволяет получать сварные соединения более высокой прочности, при знакопеременных и ударных нагрузках. Сталь 09Г2С относится к спокойной, так как она получается раскислением Si и Мn и содержит более 0,8% Si. Данная сталь менее склонна к старению и отличается меньшей реакцией на сварочный нагрев.
Влияние углерода и других легирующих элементов на свариваемость определяется по эквиваленту углерода. Величина эквивалентного содержания углерода зависит от химического состава стали и ее толщины.
Эквивалент углерода определяется по формуле:

где C, Mn, Cr, Ni, Mo - элементы, содержащиеся в стали 09Г2С,
, 18, 13 - эмпирические коэффициенты.

Определим полный эквивалент углерода с учетом толщины по формуле (2.2):

где


S - толщина металла;
; 0,005 - эмпирические коэффициенты.

Так как С’э < 0,45%, то сталь Ст. 09Г2С сваривается хорошо всеми способами сварки в широких диапазонах режимов и не требует дополнительных технологических приемов.
Подводя итог, можно сделать вывод, что в целом конструкция технологична, как с точки зрения сборки, так с точки зрения сварки. Следует отметить простоту форм заготовок, рациональное расположение сварных швов, возможность выполнения заготовительных и сборочно-сварочных операций по типовым технологиям. При изготовлении конструкции возможно применение высокопроизводительных способов сварки и прогрессивных приемов изготовления.
3. Выбор сварочных материалов
Принцип выбора сварочных материалов характеризуется следующими основными условиями:
а) обеспечение требуемой эксплуатационной прочности сварного соединения или наплавленного металла;
б) обеспечение необходимой сплошности сварного шва или наплавленного металла;
в) отсутствие холодных и горячих трещин;
г) получение комплекса специальных свойств наплавленного металла или метала шва.
Стальная проволока 08Г2С должна изготавливаться по ГОСТ 2246-70.
В соответствии с данным стандартом устанавливают диаметр сварочной проволоки, ее химический состав, правила приемки и методы испытания, требования к упаковке, маркировке, транспортированию и хранению.
В сертификате, сопровождающем партию проволоки, должны быть указаны следующие данные: товарный знак предприятия-изготовителя, условное обозначение проволоки согласно стандарту, номер плавки и партии, состояние поверхности проволоки (омедненная или неомедненная), химический состав в процентном содержании каждого элемента, результаты испытания на растяжение, масса проволоки в килограммах (нетто).
Проволока для автоматической и полуавтоматической сварки должна быть чистой от грязи, масла, ржавчины, без трещин, клейм и расслоений, не должна иметь резких перегибов и жучков. Бухта должна состоять из одного отрезка проволоки и легко разматываться.
На поверхности сварочной проволоки допускаются риски, царапины и отдельные вмятины, глубиной не более ¼ от предельного отклонения по диаметру.
Наличие бирки, прикрепленной к бухте сварочной проволоки, на которой указаны наименование и товарный знак предприятия-изготовителя, условное обозначение проволоки согласно стандарту и номер партии, а также сертификата на проволоку является гарантией того, что она пригодна для сварочных работ.
Таблица 3.1 - Химический состав сварочной проволоки Св-08Г2С, %.
Марка проволоки | С | Mn | Si | Cr | Ni | S | P |
Св-08Г2С | 0,05-0,11 | 1.80-2.10 | 0,70-0,95 | ≤0,20 | ≤0,25 | не более 0,025 | не более 0,030 |