Файл: Н. Н. Бенардос и Н. Г. Славянов положили начало автоматизации сварочных процессов. Однако в условиях царской России их изобретения не нашли большого применения. Только после Великой Октябрьской социалистической револ.rtf
ВУЗ: Не указан
Категория: Не указан
Дисциплина: Не указана
Добавлен: 12.01.2024
Просмотров: 99
Скачиваний: 1
ВНИМАНИЕ! Если данный файл нарушает Ваши авторские права, то обязательно сообщите нам.
При сварке проволокой св-08Г2С стали 09Г2С, получаем необходимые механические свойства металла шва.
Для защиты зоны сварки при полуавтоматической сварки используем углекислый газ (СО2). Углекислый газ бесцветен, не ядовит, тяжелее воздуха. При давлении 760 мм рт. ст и при температуре 0ºС плотность углекислого газа равна 1,97686 г./л, что в 1,5 раза больше плотности воздуха.
Углекислый газ поставляется согласно ГОСТ 8050-85. Для сварки используется сварочная углекислота или пищевая с дополнительной осушкой. В соответствии с ГОСТ содержание двуокиси углерода в углекислом газе должно быть не менее 99,5%; содержание водяных паров - не более 0,184 мг/м³, содержание минеральных масел должно быть не более 0.1 мг/кг. Кислород для сварки поставляется в соответствии с ГОСТ 5383-78, согласно которому содержание кислорода в объеме должно быть не менее 99,5%, а содержание водяных паров - не более 0,07 г/м³.
Таблица 3.2 - Химический состав углекислоты.
Состав | Сорт | ||
| Сварочная, 1 сорт | Сварочная, 2 сорт | |
СО2, (не меньше), % СО, (не более), % Водяных паров при 760 мм.рт. ст. и 20 °С (не более), г/м³ | 99,5 0 0,178 | 99,0 0 0,515 |
В углекислом газе не должны содержаться минеральные масла, глицерин, сероводород, соляная, серная и азотная кислоты, спирты; эфиры, органические кислоты и аммиак.
В качестве защитного газа целесообразно применение смеси углекислого газа с кислородом (СО2+О2).
Смесь СО2+О2 оказывает более интенсивное окисляющее действие на жидкий металл, чем чистый углекислый газ. Благодаря этому повышается жидко текучесть металла, что улучшает формирование шва и снижает привариваемость капель металла к поверхности изделия. Кроме того, кислород дешевле углекислого газа, что делает смесь экономически выгодной.
При сварке в чистом углекислом газе потери металла на разбрызгивание может достигать 10 ÷ 12%. Это снижает эффективность этого способа сварки, ухудшает формирование сварочного шва, вызывает дополнительные трудовые затраты на очистку поверхности изделия и сопла сварочной горелки от брызг.
Для повышения стабильности дуги, уменьшения разбрызгивания снижения себестоимости защитного газа рекомендуется применение смеси углекислого газа (70..80)% и кислорода (20..30)%.
4. Выбор сварочного оборудования
Для полуавтоматической сварки и постановки прихваток в среде защитных газов используем полуавтомат ПДГ-508, технические характеристики которого приведены в таблице 4.1.
Таблица 4.1 - Технические характеристики полуавтомата ПДГ-508
Диаметр электродной проволоки, мм | 1,6-2,0 |
Номинальный сварочный ток, А | 500 |
Скорость подачи проволоки, м/ч | 100-960 |
Масса аппарата, кг | 56 |
При полуавтоматической сварке механизирована только подача проволоки, а перемещение дуги вдоль свариваемого стыка осуществляется вручную.
Высокие эксплуатационные характеристики сварочного полуавтомата ПДГ-508 достигаются за счет применения тонкой проволоки, подаваемой к электрической дуге по гибкому направляющему каналу, который позволяет разместить относительно тяжелый механизм для подачи проволоки на значительное расстояние от зоны сварки, где расположен только рабочий орган - сварочная горелка.
Полуавтомат имеет плавно-ступенчатое регулирование скорости подачи электродной проволоки. В состав полуавтомата входят две сварочные горелки, комплект газовой аппаратуры, токоведущие кабеля и шланги. Подающее устройство оформлено в виде небольшого блока, внутри которого расположены электродвигатель с редуктором, кассета и газовый клапан.
При дуговой сварке в среде СО2
сварочная дуга имеет возрастающую вольтамперную характеристику. Для стабильности процесса и устойчивости работ, требуется источник с жесткой внешней характеристикой, одним из которых является выпрямитель ВДУ-506, он имеет следующие преимущества по сравнению с преобразователями и генераторами: широкие пределы регулирования сварочного тока, высокие динамические свойства и технико-экономические показатели, высокий К.П.Д.
Таблица 4.2 - Технические данные выпрямителя ВДУ-506.
Напряжение питающей сети, В | 380; 220 |
Номинальный сварочный ток, А | 500 |
Пределы регулирования сварочного тока, А для жестких характеристик для падающих характеристик | 60-500 50-500 |
Пределы регулирования рабочего напряжения, В для жестких характеристик для падающих характеристик | 18-50 22-46 |
Напряжение холостого хода, В, не более | 85 |
Продолжительность цикла сварки, мин | 10 |
Габаритные размеры, мм | 820х620х1100 |
Масса, кг | 300 |
5. Расчет режимов сварки
При выборе параметров применяем методику расчета режимов механизированной сварки, соединений различных типов. Режимы сварки выбираем в зависимости от свариваемости металла, толщины, типа шва, выбранного способа сварки и сварочных материалов.
Рассчитаем параметры режимов для полуавтоматической сварки в среде СО2.
Принимаем диаметр сварочной проволоки dэ = 1,6 мм. Сварочный ток определится из допустимой плотности тока j = 110..130 А/мм²

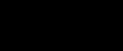
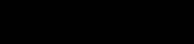
Механизированные способы сварки позволяют применять значительно большие плотности тока по сравнению с ручной сваркой. Это объясняется меньшей длиной вылета электрода.
Напряжение на дуге определим по формуле:
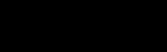
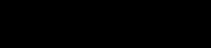
Определим скорость подачи электродной проволоки:
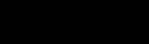
где ρ=7.85 г./мм² - плотность стали,
αН - коэффициент наплавки, равный
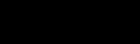

Тогда скорость подачи проволоки равна:
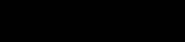
Таблица 5.1 - Режим полуавтоматической сварки швов стали 09Г2С
Сила сварочного тока, А | 240 |
Напряжение на дуге, В | 25 |
Скорость подачи проволоки, м/ч | 206 |
Диаметр электродной проволоки, мм | 1,6 |
Расход газа, л/мин | 18-20 |
6. Подготовка металла под сварку
Изделия из металлопроката должны быть отрихтованы, очищены от загрязнений, ржавчины, окалины, заусенцев, наплывов любым способом, не снижающим прочность. Изделия из металлопроката без обработки плоскостей листа не должны иметь раковин, трещин, вкатанной окалины. На поверхности допускаются без зачистки отдельные забоины, риски, царапины, отпечатки. Если глубина их залегания не выводит толщину листов за предельные отклонения. Местные поверхностные дефекты на необрабатываемых плоскостях должны быть удалены пологой вырубкой или зачисткой наждачным кругом на глубину не большую минусового допуска на прокат, и по ширине быть не менее пятикратной глубины.
7. Общие требования к основным и вспомогательным материалам
Материалы основные и вспомогательные должны соответствовать требованиям чертежей, 0СТ24.940.0 1 - 75 и ТУ. Соответствие материалов должно подтверждаться сертификатами. Основные элементы должны изготавливаться из стали 09Г2С не ниже 10 категории по ГОСТ 5520-79, допускается использование стали марки 1 6ГС не ниже 10 категории по ГОСТ 5520-79, стали марки 16 Г2С по ГОСТ 19282-73 с полистным испытанием на ударную вязкость.
Предельные отклонения свободных поверхностей, не ограниченных допусками на чертеже не должна превышать допусков по 7-му классу точности ОСТ 1010 для размеров до 500 мм и ГОСТ 2689 - 54 для размеров свыше 500 мм.
Разметку производить с помощью рулеток соответствующей точности 2-го класса по ГОСТ 7502-69, и линеек измерительных металлических по ГОСТ 427-56. При разметке учитывают припуски на мехобработку.
Детали, полученные газовой резкой должны соответствовать чертежам и требованиям настоящих ТУ. Размеры должны находится в пределах допусков, установленных рабочими чертежами. Параметры шероховатостей поверхностей должны соответствовать параметрам установленным в чертежах. Кромки, не отвечающие по шероховатости поверхности допускается исправлять плавной зачисткой.
Сборка элементов конструкции производится в соответствии с требованиями 0СТ24.04.01 - 75. Сопрягаемые детали должны быть промаркированы. Зазоры в стыках под сварку устанавливаются в зависимости от способа сварки и должны соответствовать требованиям стандартов и чертежей. Смещение кромок под сварку, форма и размеры должны соответствовать требованиям ГОСТ 5264-80, ГОСТ 8713-70, ГОСТ 11533-75 и чертежей.
Допускается замена указанного чертежами способа сварки другим способом, обеспечивающим равнопрочность сварного соединения и не нарушающего, заданные чертежом, внешнюю формы и размеры шва. Сварка должна производится квалифицированными сварщиками, имеющими право сварки ответственных конструкций. Место сварки должно быть защищено от сильного ветра, атмосферных осадков, сквозняков, в открытых помещениях сварка производится при плюсовой температуре.
Форма, размеры и смещения кромок соединений под сварку должны отвечать требованиям ГОСТ 5264 - 69, гост 8713 - 70 и соответствовать чертежу. Отклонения размеров сварных швов:
8. Дефекты и контроль качества сварных швов