Файл: Методическое пособие по практическим занятиям для студентов специальности Технология машиностроения.doc
ВУЗ: Не указан
Категория: Не указан
Дисциплина: Не указана
Добавлен: 04.02.2024
Просмотров: 201
Скачиваний: 2
ВНИМАНИЕ! Если данный файл нарушает Ваши авторские права, то обязательно сообщите нам.
Э
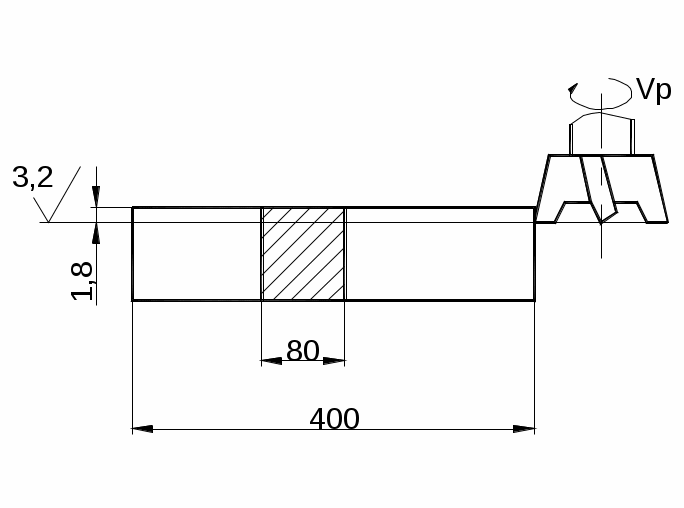
скиз обработки
Рис. 3
1. Выбор инструмента.
Для фрезерования на вертикально-фрезерном станке заготовки из чугуна выбираем торцевую фрезу с пластинками из твердого сплава ВК6 [2] или [3], диаметром D=(1,251,5)В=(1,251,5)80=100120 мм. Принимаем D=100 мм; z=10, ГОСТ 9473-71 [2] или [3].
Геометрические параметры фрезы: =60, =12, =10, =20, 1=5.
Схема установки фрезы – смещенная.
-
2. Режим резания.
2.1 Глубина резания.
Заданный припуск на чистовую обработку срезают за один проход, тогда
t=h=1,8 мм
2.2 Назначение подачи.
Для получения шероховатости Ra=6,3 мкм подача на оборот S0=1,00,7 мм/об [4].
Тогда подача на зуб фрезы
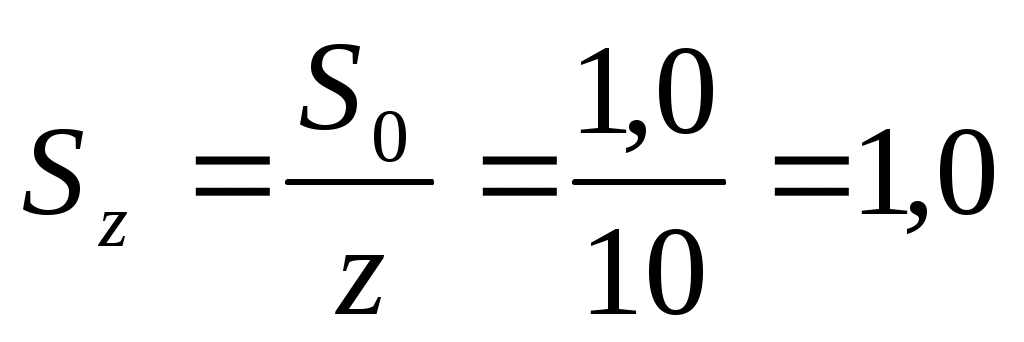
2.3 Период стойкости фрезы.
Для фрез торцевых диаметром до 110 мм с пластинками из твердого сплава применяют период стойкости
Т=180 мин [4],
2.4 Скорость резания , допускаемая режущими свойствами инструмента.
Для обработки серого чугуна фрезой диаметром до 110 мм, глубина резания t до 3,5 мм, подаче до 0,1 мм/зуб.
V=203 м/мин [4],
С учетом поправочных коэффициентов Kmv=1; Knv=1; при
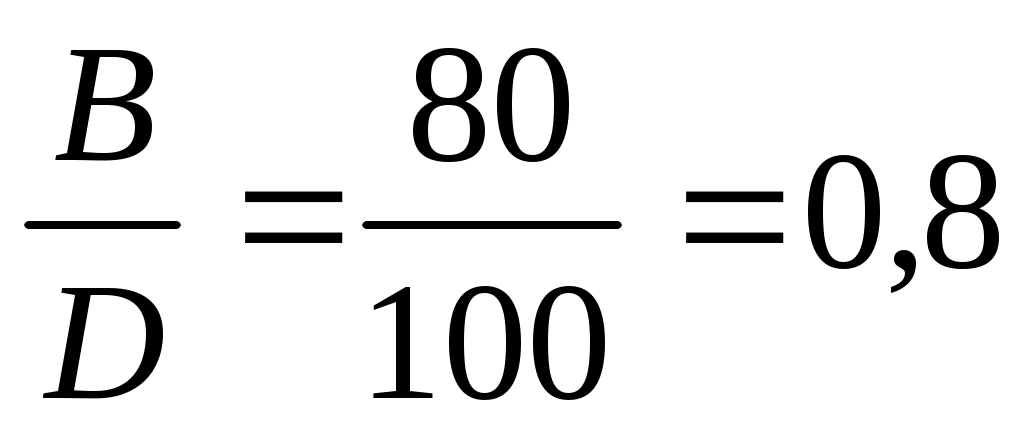
V=V Kmv Knv КБV K=2031=203 м/мин.
Частота вращения шпинделя, соответствующая найденной скорости резания

Корректируем по паспорту станка
n=630 об/мин.
Действительная скорость резания

2.5 Минутная подача Sм=Szzn=0,110630=630 мм/мин. Это совпадает с паспортными данными станка.
3. Мощность, затрачиваемая на резание.
При фрезеровании чугуна с твердостью до НВ229, ширине фрезерования до 85 мм, глубине резания до 1,8 мм, подаче на зуб до 0,13 мм/зуб, минутной подаче до 660 мм/мин
Np=3,8 кВт [4],
3.1 Проверка достаточности мощности станка
Мощность на шпинделе станка Nшп=Nд
Nд=7,5 кВт; =0,8 (по паспорту станка)
Nшп=7,50,8=6 кВт.
Так как Nшп=6 кВт Np=3,8 кВт, то обработка возможна.
4. Основное время
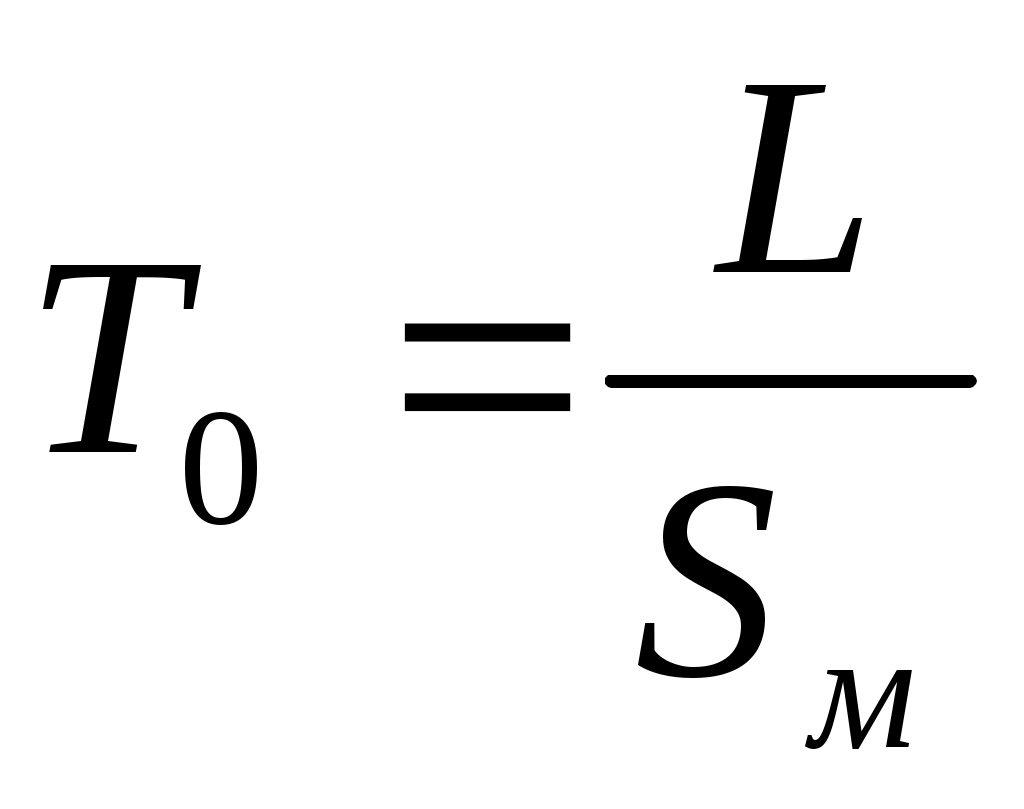
где L=l+l1.
Для торцового фрезерования фрезой диаметром 100 мм, ширине фрезерования 80 мм
l1=23 мм [4],
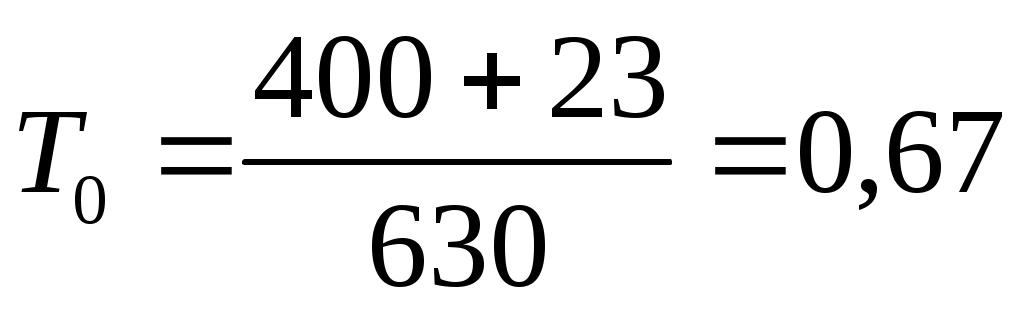
Задание на практическое занятие №5
Выполнить расчет режима резания по таблицам нормативов по заданному варианту.
Исходные данные приведены в таблице 5.
Порядок работы аналогичен предыдущим.
Таблица 5
№ | Вид заготовки и ее характеристика | В, мм | l, мм | h, мм | Вид обработки и параметр шероховатости, мкм | Модель станка |
1 | 2 | 3 | 4 | 5 | 6 | 7 |
1 | Серый чугун СЧ30, НВ200 | 100 | 600 | 5 | Торцовое фрезерование, Ra=12,5 | 6Р12 |
2 | Серый чугун СЧ20, НВ210 | 150 | 500 | 4 | Торцовое фрезерование, Ra=1,6 | 6Р12 |
3 | Сталь 38ХА, в=680 Мпа | 80 | 400 | 6 | Торцовое фрезерование, Ra=12,5 | 6Р12 |
4 | Сталь 35, в=360 Мпа | 90 | 480 | 3,5 | Торцовое фрезерование, Ra=1,6 | 6Р12 |
5 | Серый чугун СЧ15, НВ170 | 50 | 300 | 3,5 | Цилиндрическое фрезерование, Ra=3,2 | 6Р82Г |
6 | Серый чугун СЧ10, НВ160 | 80 | 250 | 1,5 | Цилиндрическое фрезерование, Ra=3,2 | 6Р82Г |
7 | Сталь 40ХН, в=700 Мпа | 70 | 320 | 4 | Цилиндрическое фрезерование, Ra=12,5 | 6Р82Г |
8 | Сталь Ст3, в=600 Мпа | 85 | 600 | 1,5 | Цилиндрическое фрезерование, Ra=3,2 | 6Р82Г |
9 | Сталь 40Х, в=750 Мпа | 10 | 100 | 5 | Фрезеровать паз, Ra=6,3 | 6Р12 |
10 | Сталь Ст5, в=600 Мпа | 12 | 80 | 8 | Фрезеровать паз ,Ra=6,3 | 6Р12 |
11 | Серый чугун СЧ20, НВ180 | 20 | 120 | 10 | Фрезеровать паз ,Ra=6,3 | 6Р12 |
12 | Серый чугун СЧ20, НВ200 | 15 | 75 | 8 | Фрезеровать паз ,Ra=6,3 | 6Р82Г |
13 | Сталь 20Х, в=580 Мпа | 8 | 110 | 8 | Фрезеровать паз ,Ra=6,3 | 6Р82Г |
14 | Сталь 50, в=750 Мпа | 12 | 120 | 6 | Фрезеровать паз ,Ra=6,3 | 6Р82Г |
15 | Бронза Бр АЖН 10-4 НВ170 | 100 | 300 | 4 | Торцовое фрезерование, Ra=12,5 | 6Р12 |
16 | Латунь ЛМцЖ 52-4-1, НВ220 | 60 | 180 | 1,5 | Торцовое фрезерование, Ra=1,6 | 6Р12 |
17 | Серый чугун СЧ30, НВ220 | 180 | 200 | 4,5 | Торцовое фрезерование, Ra=12,5 | 6Р12 |
18 | Серый чугун СЧ20, НВ220 | 110 | 280 | 2,5 | Торцовое фрезерование, Ra=3,2 | 6Р12 |
19 | Сталь 30ХНЗА, в=800 Мпа | 80 | 320 | 5 | Цилиндрическое фрезерование, Ra=12,5 | 6Р82Г |
20 | Сталь 30ХН, в=780 МПа | 115 | 300 | 3 | Цилиндрическое фрезерование, Ra=3,2 | 6Р82Г |
21 | Сталь 45, в=650 МПа | 40 | 280 | 1,8 | Цилиндрическое фрезерование, Ra=1,6 | 6Р82Г |
22 | Сталь 20, в=500 МПа | 35 | 400 | 3,5 | Цилиндрическое фрезерование, Ra=6,3 | 6Р82Г |
Продолжение табл. 5
1 | 2 | 3 | 4 | 5 | 6 | 7 |
23 | Силумин АЛ4, НВ50 | 55 | 250 | 4 | Торцовое фрезерование, Ra=6,3 | 6Р12 |
24 | Сталь 30ХМ, в=950 МПа | 70 | 310 | 4,5 | Торцовое фрезерование, Ra=12,5 | 6Р12 |
25 | Сталь 18ХГТ, в=700 МПа | 85 | 350 | 2,5 | Торцовое фрезерование, Ra=3,2 | 6Р12 |
26 | Чугун ВЧ60, НВ250 | 120 | 300 | 5 | Торцовое фрезерование, Ra=12,5 | 6Р12 |
27 | Сталь 50, в=900 МПа | 60 | 250 | 6 | Торцовое фрезерование, Ra=6,3 | 6Р12 |
28 | Чугун КЧ60, НВ169 | 200 | 450 | 5,5 | Торцовое фрезерование, Ra=3,2 | 6Р12 |
29 | Сталь 18ХГТ, в=700 МПа | 85 | 300 | 4,5 | Цилиндрическое фрезерование, Ra=12,5 | 6Р82Г |
30 | Чугун ВЧ38, НВ170 | 65 | 200 | 3 | Цилиндрическое фрезерование, Ra=3,2 | 6Р82Г |
ПРАКТИЧЕСКОЕ ЗАНЯТИЕ №6
Расчет режима резания при нарезании зубьев зубчатых колес
Цель работы: изучить методику расчета режима резания при зубонарезании по таблицам нормативов. Приобрести навыки работы по нормативам.
ОБЩИЕ СВЕДЕНИЯ
Профиль зубьев зубчатого колеса образуется путем удаления материала впадины следующими способами обработки: фрезерованием, строганием, долблением, протягиванием, шевингованием и шлифованием.
Различают два метода нарезания зубьев:
копирования – когда форма режущей кромки инструмента соответствует форме впадины зубчатого колеса (дисковые, пальцевые модульные фрезы
, зубодолбежные головки);
обкатки – поверхность зуба получается в результате обработки инструментом, режущие кромки которого представляют собой профиль сопряженной рейки или профиль зуба сопряженного колеса и во время обработки инструмент с заготовкой образуют сопряженную зубчатую пару (червячные фрезы, долбяки, шеверы и др.).
Метод обкатки имеет следующие преимущества по сравнению с методом копирования:
одним и тем же инструментом данного модуля можно нарезать зубчатые колеса с любым числом зубьев;
обеспечивается более высокая точность и низкая шероховатость поверхности зубьев нарезаемого колеса;
достигается более высокая производительность обработки благодаря непрерывности процесса и участию в работе одновременно большего количества лезвий.
Дисковая и пальцевая модульные фрезы представляют собой фасонные фрезы, профиль зуба которых повторяет профиль впадины нарезаемого колеса. Обработка производится по методу копирования. Пальцевые модульные фрезы применяют для получения шевронных и зубчатых колес большего модуля. Главным движением (движением резания) является вращение фрезы вокруг своей оси. Движением подачи является движение фрезы вдоль оси заготовки.
При обработке червячной фрезой (метод обкатывания) движение резания – вращение фрезы, движение подачи – поступательное движение фрезы вдоль оси заготовки.
Зуборезный долбяк выполнен в виде зубчатого цилиндрического колеса и снабжен режущими кромками. Главное движение (движение резания) при зубодолблении – возвратно-поступательное движение долбяка, движений подачи два: движение обкатывания по делительным окружностям долбяка и нарезаемого колеса и радиальное перемещение. Зубодолбление применяют для нарезания наружных и внутренних зубьев прямых и косозубых колес.
Глубина резания при черновом нарезании зубьев (Ra=12,5 мкм), как правило, принимается равной глубине впадины t=h=2,2m, где m – модуль нарезаемого колеса, мм.
Обычно черновые червячные фрезы профилируются такими, чтобы ими можно было нарезать зубья на полную глубину, но оставляя припуск на окончательную обработку лишь боковым сторонам зуба. Если мощности и жесткости станка недостаточно, припуск на черновую обработку срезают за два прохода: первый проход h=1,4m, второй проход , h=0,7m.
Чистовую обработку в два прохода применяют только при зубодолблении цилиндрических колес дисковыми долбяками с модулем 6 мм и выше при шероховатости выше Ra=1,6 мкм.
Подачи выбирают с учетом качества и точности нарезаемого колеса, мощности станка, модуля и числа зубьев нарезаемого колеса [5].
Скорость резания устанавливают в зависимости от режущих свойств инструмента. Размеров нарезаемого зуба. Глубины резания, подачи и других факторов по таблицам нормативов [5], или по эмпирической формуле [3].