Файл: Материала, пример маркировки с указанием нормативного документа по которому он изготавливается, расшифровку буквенно цифрового обозначения.docx
Добавлен: 29.10.2023
Просмотров: 182
Скачиваний: 2
ВНИМАНИЕ! Если данный файл нарушает Ваши авторские права, то обязательно сообщите нам.
СОДЕРЖАНИЕ
СОДЕРЖАНИЕ
Введение 3
1.Фарфор 6
2.Алюмель 13
3.Йод 18
4.Технически чистое железо (низкоуглеродистая сталь) 21
Заключение 30
Список используемой литературы. 31
Введение
Цель курсовой работы: провести исследования в области свойств и применения диэлектриков, проводников, полупроводников и магнитных материалов.
Задачи:
В работе для каждого рассматриваемого материала необходимо последовательно описать:
1. Название материала, пример маркировки с указанием нормативного документа по которому он изготавливается, расшифровку буквенно цифрового обозначения.
2. Группу, к которой относится данный вид электротехнического материала (магнитный, проводник, полупроводник, диэлектрик). Указать область применения данного материала, специфические свойства данного материала. Описать достоинства и недостатки, обусловленные специфическими свойствами данного материала.
3. Привести химический состав материала с указанием ссылки на литературный или нормативный источник информации.
4. Описать технологию получения материала, обуславливающие его специфические свойства.
5. Расписать характеристики свойств материала (физические, электрические, магнитные, диэлектрические, механические, технологические, эксплуатационные) с указание группы, к которой они относятся
Диэлектрики – вещества, обладающие малой электропроводностью, т.к. у них очень мало свободных заряженных частиц – электронов и ионов. Эти частицы появляются в диэлектриках только при нагреве до высоких температур. Существуют диэлектрики газообразные (газы, воздух), жидкие (масла, жидкие органические вещества) и твердые (парафин, полиэтилен, слюда, керамика и т.п.).
Проводники – вещество, среда, материал, хорошо проводящие электрический ток.
В проводнике имеется большое число свободных носителей заряда, то есть заряженных частиц, которые могут свободно перемещаться внутри объёма проводника и под действием приложенного к проводнику электрического напряжения создают ток проводимости. Благодаря большому числу свободных носителей заряда и их высокой подвижности значение удельной электропроводности проводников велико.
Полупроводни́к – материал, по
удельной проводимости занимающий промежуточное место между проводниками и диэлектриками, и отличающийся от проводников сильной зависимостью удельной проводимости от концентрации примесей, температуры и воздействия различных видов излучения. Основным свойством полупроводников является увеличение электрической проводимости с ростом температуры.
Полупроводниками являются кристаллические вещества, ширина запрещённой зоны которых составляет порядка электрон-вольта (эВ). Например, алмаз можно отнести к широкозонным полупроводникам (около 7 эВ), а арсенид индия – к узкозонным (0,35 эВ). К числу полупроводников относятся многие химические элементы (германий, кремний, селен, теллур, мышьяк и другие), огромное количество сплавов и химических соединений (арсенид галлия и др.).
Магнитные материалы, Магнетики – материалы, вступающие во взаимодействие с магнитным полем, выражающееся в его изменении, а также в других физических явлениях – изменение физических размеров, температуры, проводимости, возникновению электрического потенциала и т. д. В этом смысле к магнетикам относятся практически все вещества (поскольку ни у какого из них магнитная восприимчивость не равна нулю), большинство из них относится к классам диамагнетиков (имеющие небольшую отрицательную магнитную восприимчивость – и несколько ослабляющие магнитное поле) или парамагнетиков (имеющие небольшую положительную магнитную восприимчивость – и несколько усиливающие магнитное поле); более редко встречаются ферромагнетики (имеющие большую положительную магнитную восприимчивость – и намного усиливающие магнитное поле), о ещё более редких классах веществ по отношению к действию на них магнитного поля.
-
Фарфор
1.1. Изоляторы должны изготовляться классов: 10, 20 и 35 (ГОСТ 1232-82 Группа Е35 [9]), что соответствует значениям номинальных электрических напряжений линий электропередачи (или электроустановок) в киловольтах. Каждому классу могут соответствовать изоляторы нескольких конструктивныхисполнений.
Каждое конструктивное исполнение изолятора должно определяться стандартом или техническими условиями на конкретный тип изолятора.
В условном обозначении изоляторов буквы и цифры означают:
Ш - штыревой;
С и Ф - стеклянный или фарфоровый;
10, 20, 35 - классы изоляторов;
А, Б, В и т.д. - конструктивные исполнения;
О, ТС и т.д. - климатические исполнения изоляторов.
Допускается для районов с умеренным и холодным климатом обозначение климатических исполнений УХЛ не указывать.
Пример условного обозначения штыревого стеклянного изолятора класса 10, исполнения Г:
ШС 10-Г (обозначение стандарта или технических условий на конкретный тип изолятора)
То же, климатического исполнения ТС:
ШС 10-ГТС (обозначение стандарта или технических условий на конкретный тип изолятора).
1.2. Электротехнический фарфор относится к группе диэлектриков и предназначен для электрической изоляции деталей распределительных устройств и аппаратов, находящихся под различными потенциалами, а также для механического поддерживания токоведущих деталей. Фарфоровые изоляторы выпускаются самых разнообразных форм, типов и размеров в связи с разнообразием условий их службы.
Фарфор имеет высокий предел прочности на сжатие (400-700 Мпа), значительно меньший предел прочности на растяжение (45-70 Мпа) и при изгибе (80-150 МПА). Электроизоляционные свойства фарфора при нормальной температуре позволяют использовать его при низких частотах; Тангенс угла диэлектрических потерь электротехнического фарфора, однако, быстро растет при увеличении температуры, что затрудняет его использование при высоких температурах и на высоких частотах. Основными составными частями фарфора являются стекловидная фаза (50-64 объемн.%), муллит (15-30 объемн.%), кварц (14-30 объемн.%), сравнительно небольшое количество пор и кристобалит. Фазовый состав фарфора и его структура определяются исходным составом массы, технологией ее приготовления (прежде всего дисперсностью) и условиями обжига (238с [2]).
1.3. Состав и структура фарфора (328 с. [5]).Фарфор имеет типичную гетерогенную структуру (рис. 1). Основная масса нормально обожженного фарфора представлена стеклом и мелкозернистым муллитом в виде округлых или изометричных иголочек. Псевдоморфозы стекла по полевому шпату имеют четкие контуры или сливаются с основной массой его. Кристаллы муллита в них игольчатые, взаимно переплетенные в виде сетки. Длина их достигает 10-40 мкм.
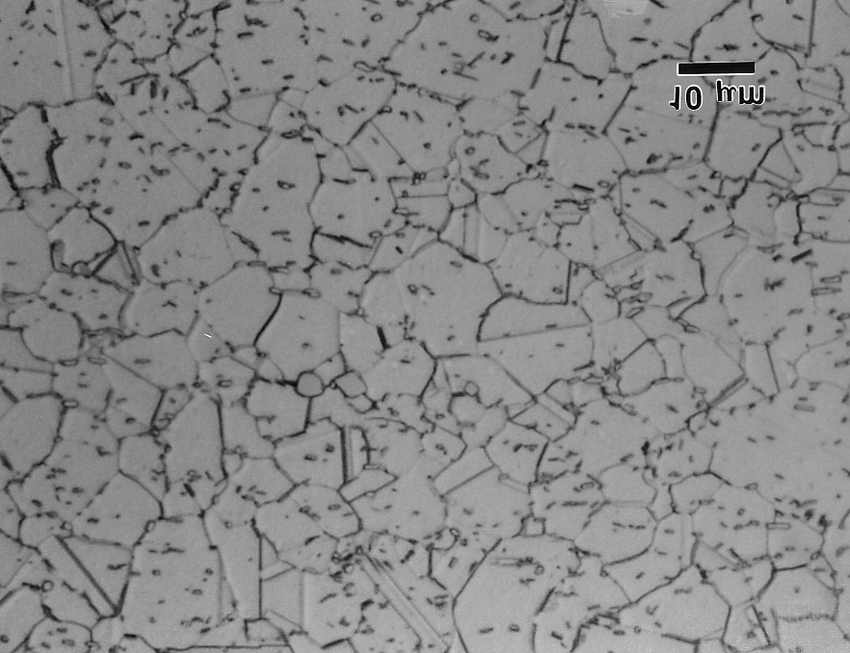
Рис. 1
Зерна кварца, распределенные в основной массе, имеют остроугольную или округлую форму; зона оплавления их равна обычно 1-3 мкм. Размер зерен кварца колеблется в широких пределах. Средний размер составляет примерно 15-20 мкм, максимальный достигает 100 мкм. Фазовый состав отечественного фарфора колеблется примерно в следующих пределах (объемн.%): муллит – 21–22; кварц – 16–18; стекловидная фаза – 60–64. Свойства фарфора определяются как его фазовым составом, так и структурой (384 с. [7]).
Образующаяся в фарфоре стекловидная фаза в силу гетерогенного состава массы и незавершенности процессов в обжиге неоднородна. Различают следующие ее разновидности: полевошпатовое стекло в пределах зерен полевого шпата, в котором растворились кварц и каолинит (псевдоморфозы стекла по полевому шпату), кремнеземистое стекло вокруг зерен кварца, стекло, образующееся за счет растворения кварца в полевошпатовом стекле, стекло, образующееся за счет взаимодействия каолинитового остатка с полевошпатовым расплавом.
1.4. Из фарфора изготовляют линейные (подвесные и штыревые) изоляторы, стационарные (опорные и проходные) изоляторы, аппаратные изоляторы, установочные фарфоровые изделия (ролики, детали предохранителей, патронов, штепселей и тому подобные). Широкое применение в качестве электроизоляционного материала находит электротехнический фарфор, который является основным керамическим материалом, используемым в производстве широкого ассортимента низковольтных и высоковольтных изоляторов и других изоляционных элементов с рабочим напряжением до 1150 кВ переменного и до 1500 кВ постоянного тока.
Электротехнический фарфор, как и любая керамика, состоит из кристаллической, аморфной и газовой фаз. Его свойства определяются химическим и фазовым составом, микро- и макроструктурой и технологией изготовления.
Основными материалами изготовления фарфора являются сырьевые материалы минерального происхождения – глинистые вещества (каолин и глина, полевой шпат, гипс). Глинистые вещества в сыром виде при замешивании с водой обладают пластичностью, котокая дает возможность формировать из них изделия различных форм.
Изделия из фарфоровой массы получают различными способами: обточкой, прессовкой, отливкой в гипсовые формы, выдавливанием через отверстие нужной конфигурации. После оформления изделия производится сушка полуфабриката для удаления воды, вводимой для придания пластичности. Следующая операция – глазурование фарфоровых изоляторов – производится для предохранения от загрязнения. При обжиге глазурное покрытие плавится и покрывает поверхность изолятора тонким стекловидным слоем. Глазурь увеличивает механическую прочность, заглаживает трещины и уменьшает ток утечки по по верхности изоляторов. Фарфоровые изедлия помещаются в печь в специальных коробках – капселях из огнеупорной глины, чтобы предохранить издлелия от топочных газов. Обжиг производится в горнах – печах прерывного действия – или в туннельных печах непрерывного действия. При обжиге происходит усадка изделий.
1.5. Диэлектрические свойства. С учетом условий службы изоляторов к фарфору предъявляются высокие требования в отношении его диэлектрических, механических и термических свойств.
Наиболее важной диэлектрической характеристикой фарфора является прочность на пробой (кВ/мм). Величина прочности на пробой преимущественно зависит от количества стекловидной фазы.
Сравнительно высокая проводимость стекловидной фазы фарфора объясняется, таким образом, наличием в ней ионов щелочных металлов. Последние способствуют разрыхлению структуры стекловидной фазы, в связи с чем облегчается движение носителей тока. Подвижность ионов определяется их валентностью и ионным радиусом.
Щелочные ионы наименее прочно связаны; они обусловливают повышенную проводимость фарфора. Интенсивность движения их усиливается под действием электрического поля с увеличением температуры. Электрическая прочность фарфора при нормальной температуре мало зависит от соотношения К2О к Na2O в стеклофазе. Однако от этого соотношения весьма существенно зависит температура, при которой наблюдается заметное снижение пробивной напряженности. Уменьшение в фарфоре отношения К2О : Na2 Oснижает эту температуру. Наиболее высокая температура наблюдалась у фарфора на микроклине (135ºС), наиболее низкая у фарфора на альбите (50ºС). Температуры, соответствующие заметному снижению пробивной напряженности, оказались близкими к температурам, при которых наблюдалось резкое возрастание tgδ. Следовательно, снижение пробивной напряженности при нагреве вызвано резким возрастанием диэлектрических потерь.
Механическая прочность. Механическая прочность фарфора, как и всякого керамического материала, определяется свойствами наиболее слабой составляющей его структуры – стекловидной фазы. Прочность и упругость кристаллического кварца, муллита и фарфора характеризуются следующими (табл.1) величинами (кгс/см2 ):
Таблица 1. Механические свойства кварца, муллита и фарфора
Свойства | Наименование кристаллической фазы | ||
Кварц | Муллит | Фарфор | |
Предел прочности при сжатии, кгс/см2 | 22000 | 8300 | 4000-5500 |
Предел прочности при разрыве, кгс/см2 | 850 | 820 | 250-500 |
Предел прочности при изгибе, кгс/см2 | 1200 | 980 | 600-850 |