Файл: Курсовой проект по дисциплине Технология ремонта машин.docx
ВУЗ: Не указан
Категория: Не указан
Дисциплина: Не указана
Добавлен: 07.11.2023
Просмотров: 97
Скачиваний: 1
ВНИМАНИЕ! Если данный файл нарушает Ваши авторские права, то обязательно сообщите нам.
Федеральное государственное бюджетное образовательное учреждение
высшего образования
«Ульяновский государственный аграрный университет
имени П. А. Столыпина»
Факультет Инженерный
Направление подготовки / специальность 35.03.06 «Агроинженерия»
Специализация/профиль/программа Технические системы агробизнесе
Кафедра Сервис и механика
КУРСОВОЙ ПРОЕКТ
по дисциплине: «Технология ремонта машин»
на тему: «Разработка технологического процесса восстановления корпуса сцепления трактора МТЗ-82.1»
Выполнил: студент 4 курса
очной формы обучения
Ураков Амирбек Ганиевич
Подпись
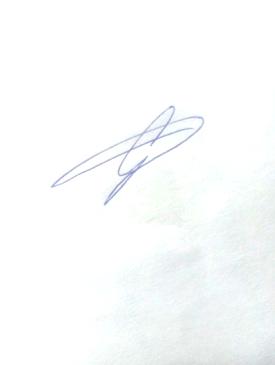
Руководитель работы:
Должность, звание: к.т.н., доцент
Еремеев Анатолий Николаевич
Оценка________________________ Подпись_______________________ «___»____________20________г.
г. Ульяновск
Задание
на курсовой проект по дисциплине «Технология ремонта машин»
Студент Ураков Амирбек Ганиевич 4 Курс, группа 41 Вариант № 49
Тема: «Разработка технологического процесса восстановления корпуса сцепления трактора МТЗ-82.1»
Исходные данные:
1. Рисунок, наименование и обозначение детали
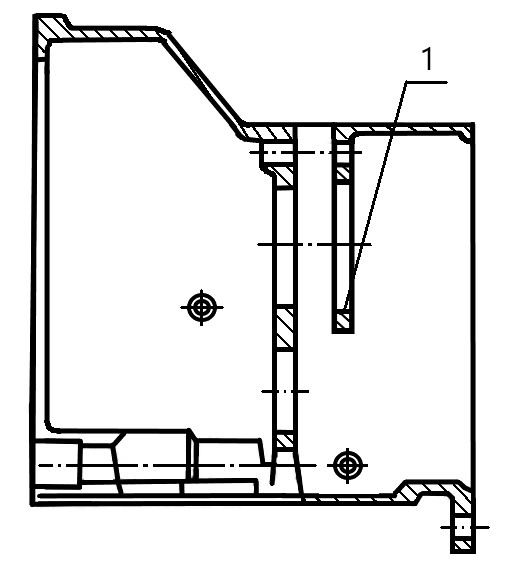
Корпус коробки передач 04.37.101-1
Контролируемый дефект | Размеры, мм. | ||
Номер позиции на рис. | Наименование | По чертежу | допустимый |
4 | Износ поверхности отверстий под стакан подшипника первичного вала | 145−0,028 +0,012 | 145,08 |
Разработать технологический процесс восстановления детали.
Дополнительные указания:
Материал – СЧ 20
Твердость - 170…241 НВ
Задание выдал:_________________
Срок сдачи законченного проекта на проверку:___________________________
Содержание:
Стр.
Введение
1 Устройство, анализ работы и сцепления.....………..4
2. Работа и техническое обслуживание сцепления ….……………5
3. Обоснование рационального способа восстановления ….……….…………….6
4. Разработка маршрута восстановления детали……………….………………….8
5. Расчет режимов основных технологических операций восстановления …......9
6. Механическая обработка детали………………………..……………………….12
7. Расчет норм времени при выполнении операций………………………..….…13
8. Определение экономической эффективности восстановления деталей.….…16
Заключение……………………………………………………………………….…18
Библиографический список……………………….…………………………….…19
Приложение:……………………………………………………………..…………20
Приложение А. Карта эскизов………………………….…….……………...21
Приложение Б. Маршрутная карта……………………….………………….22
Приложение В. Операционная карта очистки детали….………………..…23
Приложение Г. Карта технологического процесса дефектации….………..24
Приложение Д. Операционная карта восстановления детали …..……….…25
Приложение Е. Операционная карта механической обработки детали
после восстановления …………………………………………………..……26
Приложение Ж. Ведомость оборудования……………….….…………..…..27
1 Устройство, анализ работы и сцепления
Белорусский трактор МТЗ-82.1 являются самыми массовыми тракторами не только на постсоветском пространстве, но и во всей мировой истории. Эти неприхотливые, долговечные и надёжные, как автомат Калашникова, машины прочно заняли ведущие места в сельском хозяйстве и других отраслях многих
стран мира. В чём отличия трактора «Беларус МТЗ – 82.1» от других тракторов 80-го семейства; каковы особенности его конструкции и технических характеристик.
Свободный ход муфты выключения сцепления проверять перемещением вручную рычага вала вилки. При этом отсоединить пружину от рычага. Если свободный ход рычага, измеренный на радиусе 90 мм, окажется менее 3мм, отрегулировать его сферической гайкой толкателя до величины 3,7...4,6мм, что соответствует свободному ходу муфты выключения сцепления 3,2...4мм.
Свободный ход педали, соответствующий началу работы главного цилиндра, должен составлять 6...15мм. Измерять его надо в средней части площадки педали сцепления. Если свободный ход выходит за пределы, указанные выше, отрегулировать зазор А между поршнем и толкателем поршня главного цилиндра эксцентриковым пальцем 6 который соединяет верхнюю проушину толкателя 7 с рычагом 5 педали. Регулировать зазор при положении, когда оттяжная пружина 8 прижимает педаль сцепления к верхнему упору 4. Повернуть эксцентриковый палец так, чтобы перемещение педали от верхнего упора до момента касания толкателем поршня составило 6…15мм, затем затянуть и зашплинтовать корончатую гайку. Полный ход педали сцепления должен составлять 185...195мм.
В сцеплении могут быть следующие основные неисправности: нарушение регулировки привода, вызывающее неполное выключение и неплавное включение сцепления, пробуксовку дисков; износ фрикционных накладок ведомого диска, подшипника муфты выключения сцепления, манжеты рабочего цилиндра привода сцепления.
2 РАБОТА И ТЕХНИЧЕСКОЕ ОБСЛУЖИВАНИЕ СЦЕПЛЕНИЯ
Исходное положение. Педаль привода сцепления находится в исходном положении, шток главного цилиндра - в верхнем положении. Поршень под действием пружины прижат к перегородке корпуса. Между штоком и поршнем имеется зазор, полости главного цилиндра сообщаются между собой. В трубопроводе, соединяющем главный цилиндр с гидроусилителем, давление отсутствует.
Толкатель гидравлического поршня гидроусилителя под действием возвратной пружины рычага вала вилки прижимается к гидравлическому поршню, который через другой толкатель удерживает пневматический поршень в исходном положении.
Нажимной диск 4 сцепления под действием нажимных пружин 16 прижимает ведомые диски к среднему ведущему диску 2 и маховику 21. Муфта выключения сцепления под действием пружин отведена от упорного кольца 14 на 3,2...4мм, обеспечивая тем самым полноту включения сцепления.
Крутящий момент, развиваемый двигателем, от коленчатого вала передается на маховик, средний ведущий и нажимной диски и далее за счет трения на ведомые диски. От ведомых дисков крутящий момент через демпфер передается на ступицы ведомых дисков и далее на первичный вал 23 коробки передач.
Выключение сцепления. При нажатой педали привода сцепления толкатель 1 главного цилиндра (закрывает отверстие в поршне 3, предотвращая перетекание жидкости из нижней полости в верхнюю, и перемещает поршень, сжимая пружину. При перемещении поршня в цилиндре повышается давление, которое передается по шлангам и трубопроводам к входному отверстию пневмогидроусилителя.
Рабочая жидкость под давлением поступает в полость цилиндра гидравлического поршня усилителя и далее по каналу в заднем корпусе подводится к следящему поршню.
При отсутствии сжатого воздуха в пневматической системе автомобиля сцепление можно выключить за счет давления только в гидравлической части усилителя. При этом для создания необходимого давления водитель должен увеличить усилие на педаль сцепления до 600Н (60кгс).
3 Обоснование рационального способа восстановления
Осуществляем выбор рационального способа восстановления детали по трем критериям:
1) технологический критерий или критерий применимости;
2) критерий долговечности;
3) технико-экономический критерий (определяется как отношение себестоимости восстановления детали к коэффициенту долговечности выбранного способа).
В соответствии с технологическим критерием, по таблице 1 Методических указаний определяем, что для устранения износа поверхности отверстия под стакан подшипника первичного вала корпуса коробки передач трактора МТЗ 82.1 могут применяться следующие способы: железнение, электроконтактная приварка стальной ленты.
Для дальнейшего определения рационального метода восстановления из числа выбранных способов используем критерий долговечности. Находим коэффициент долговечности КД для ранее выбранных способов.
КД = f(КИ, КВ, КСЦ) (1)
где: КИ - коэффициент износостойкости;
КВ - коэффициент выносливости;
КСЦ - коэффициент сцепляемости.
Для всех выбранных ранее способов выписываем указанные коэффициенты из таблицы 2 Методических указаний, подставляем в формулу 1 и принимаем значение КД по наименьшему значению коэффициента в формуле. Учитывая характер работы сопряжения, коэффициент сцепляемости при расчете можно принять по максимальному значению:
Железнение: КД = f(1,1; 0,8; 0,8) = 0,8.
Электроконтактная приварка стальной ленты: КД = f(1,0; 0,8; 0,9) = 0,8.
Из перечисленных способов восстановления оставляем способы, обеспечивающие коэффициент долговечности равный или не менее 0,8 (КД ≥ 0,8).
Этому условию соответствуют способы: железнение, электроконтактная приварка стальной ленты.
Так как способов несколько, то для окончательного выбора используем технико-экономический критерий:
СВ/КД → min, (2)
где КД – рассчитанный ранее коэффициент долговечности поверхности, подлежащей восстановлению;
СВ - себестоимость восстановления изношенной поверхности детали, руб.
Для определения величины себестоимости восстановления СВ используем формулу 3:
СВ = СУ ∙ S / 10 000 (3)
где Су - удельная себестоимость восстановления, руб./дм2 (берем среднее значение из таблицы 3 Методических указаний);
S - площадь поверхности, подлежащей восстановлению, мм2.
Определяем общую площадь внешней цилиндрической, подлежащих восстановлению:
S= C ∙ l = π ∙ D ∙ l = 3,14 ∙ 145 ∙ 35 = 15935,5 мм2, (4)
где С – длина окружности шейки вала, мм;
D – диаметр шейки вала, мм;
l – длина шейки вала, мм.
Себестоимость восстановления при железнении:
СВ = 96 ∙ 15935,5 / 10 000 = 152,9 руб.
Аналогичным образом производим расчет для всех выбранных способов, полученные данные заносим в таблицу.
Наименование способа восстановления | СУ | СВ | ![]() |
Железнение | 96 | 152,9 | 160,9 |
Электроконтактная приварка стальной ленты | 280 | 375 | 469 |