Файл: Задача соединения различных металлов и сплавов стоит перед человечеством очень давно. В процессе развития научной мысли удалось достигнуть многого в этом направлении..doc
Добавлен: 23.11.2023
Просмотров: 55
Скачиваний: 1
ВНИМАНИЕ! Если данный файл нарушает Ваши авторские права, то обязательно сообщите нам.
Недостатки:
-
необходимы меры по снижению разбрызгивания; -
сквозняки ухудшают газовую защиту дуги, поэтому сварка на открытом воздухе затруднена; -
необходимость применения защитных мер против световой и тепловой радиации дуги.
4.Выбор сварочных материалов
4.1. Для полуавтоматической сварки плавящимся электродом в углекислом газе следует применять следующие сварочные материалы:
- сварочную стальную проволоку по ГОСТ 2246-70;
- двуокись углерода по ГОСТ 8050-76.
4.2. Каждая партия сварочной проволоки должна иметь сертификат с указанием предприятия-изготовителя, условного обозначения проволоки, номера плавки и партии, состояния поверхности проволоки и химического состава. К каждому мотку (бухте, катушке, кассете) проволоки должна быть прикреплена бирка с указанием предприятия-изготовителя, номера партии, условного обозначения проволоки и клейма технического контроля, удостоверяющего соответствие проволоки требованиям стандарта.
4.3. При отсутствии сертификата необходимо проверять химический состав проволоки в соответствии с ГОСТ 2246-70 «Проволока стальная сварочная». При отклонениях в химическом составе проволоки бухта этой проволоки не должна быть использована для сварки.
4.4. Поверхность проволоки должна быть чистой и гладкой, без трещин, расслоений, плен, закатов, раковин, забоин, окалины, ржавчины, масла и других загрязнений.
4.5. Проволоку необходимо хранить в сухом закрытом помещении, защищающем ее от воздействия атмосферных осадков и почвенной влаги, от коррозии, загрязнения и механических повреждений.
4.6. Для сварки следует применять сварочную двуокись углерода. Допускается использование пищевой двуокиси углерода.
4.7. Перед сваркой пищевая двуокись углерода, поставляемая в баллонах, должна отстояться в течение 1 - 2 ч, затем следует открыть вентиль на 8 - 10 с.
4.8. Для уменьшения содержания влаги в зоне сварки пищевую двуокись углерода рекомендуется пропускать через осушитель. Реагенты, заполняющие осушитель (силикагель, алюмогель или медный купорос), необходимо периодически (не реже одного раза в месяц) прокаливать в течение 2 ч при температуре регенерации: для силикагеля - 150 °С, для алюмогеля - 280 °С и для медного купороса - 250 °С.
4.9. Перед сваркой необходимо проверять качество углекислого газа в каждом баллоне. Для этого следует произвести наплавку сварочного валика длиной 100 - 150 мм на пластину или трубу и проверить внешним осмотром по ГОСТ 3242-79 «Соединения сварные. Методы контроля качества» поверхность наплавки и излома шва. При наличии пор в металле шва газ, находящийся в данном баллоне, бракуют.
Присадочный металл и другие вещества, используемые при сварке плавлением с целью получения непрерывного, неразъёмного соединения, удовлетворяющего определённым требованиям, принято называть сварочными материалами.
Сварочная проволока
Сварочная проволока служит для подвода электрического тока в зону сварки, а также является дополнительным металлом, участвующим в образовании шва.
В своей работе применил проволоку Св-08ГС ГОСТ 2246-70. Химический состав проволоки соответствует ГОСТ 2246-70 «Проволока стальная сварочная» и указан в таблице 6.
Таблица 6.
Химический состав проволоки Св-08ГС по ГОСТ 2246-70
Обозначение | Массовая доля элементов, % | ||||||||
C | Mn | Si | Cr | Ni | Mo | Ti | S | P | |
Св-08ГС | ≤0,1 | 1,40 ÷ 1,70 | 0,60 ÷ 0,85 | ≤0,20 | ≤0,25 | - | - | ≤0,0250 | ≤0,030 |
Сварочная углекислота.
Согласно ГОСТ 8050-85 «Двуокись углерода газообразная и жидкая. Технические условия» газообразная и жидкая углекислота поставляется трех видов: высшего, первого и второго сортов. Для сварки рекомендуется использовать углекислоту высшего и первого сорта. Применение углекислоты второго сорта для сварки допускается, однако желательно наличие осушителей газа, для извлечения влаги. Он представляет собой корпус, заполненный материалом (обычно силикагелем, медным купоросом или алюмогелем), хорошо впитывающим влагу.
Допустимое содержание углекислого газа и некоторых примесей в различных марках углекислоты приведено в таблице 7.
Таблица 7.
Характеристики марок углекислоты по ГОСТ 8050-85
Марка углекислоты | Высший сорт | Первый сорт | Второй сорт |
Объемная доля углекислого газа, % | 99,8 | 99,5 | 98,8 |
Доля воды, % | нет | нет | ≤0,1 |
Содержание водяных паров, г/м3 | ≤0,037 | ≤0,184 | Не нормируется |
Транспортируется и хранится в баллоне чёрного цвета с жёлтой надписью.
5.Организация рабочего места при выполнении заданного процесса
5.1 Требования к оборудованию
5.1.1. Пост для полуавтоматической сварки в углекислом газе должен состоять (черт. 1)
1 - баллон с углекислым газом; 2 - подогреватель; 3 - редуктор-расходомер;
4 - осушитель; 5 - механизм подачи проволоки; 6 - шкаф управления;
7 - источник питания дуги; 8 - шланговый держатель; 9 - свариваемое изделие
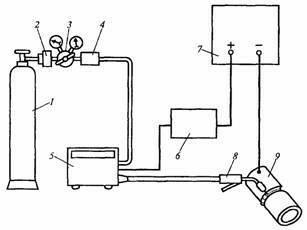
черт 1.
5.1.2. Источники сварочного тока.
В настоящее время используется три основных вида источников.
1) Сварочные трансформаторы.
Громоздкие и тяжелые машины, вырабатывающие переменный ток. Так как в данной работе сварка производится только на постоянном токе, эти источники во внимание не принимаются.
2) Сварочные выпрямители.
Современные тиристорные сварочные выпрямители находят широкое распространение в цеховых условиях, где масса и габариты источника не играют большой роли. Развитая система управления последних моделей позволяет в широких пределах менять сварочные режимы, а применяемые схемы стабилизации режима позволяют использовать эти источники в производстве ответственных сварных конструкций.
3) Инверторные источники питания.
Сварочные инверторы используются как источники питания для сварочных аппаратов для всех методов дуговой сварки плавлением и в настоящее время являются наиболее современным видом сварочных источников питания. Среди других сварочных аппаратов сварочные инверторы отличаются хорошими сварочными свойствами, компактностью, малой массой и низким уровнем энергопотребления. Применяемая в последних моделях инверторов система управляемого каплепереноса позволяет добиться исключительного качества формирования шва.
Потому я выбрал синергетический, сварочный, инверторный полуавтомат Aurora PRO SPEEDWAY 175 IGBT 10038, который предназначается для выполнения широкого спектра задач. Он подходит для профессионального использования на производстве, при строительстве или монтаже металлоконструкций. Встроенная функция "форсаж дуги" сварки позволяет повысить стабильность горения дуги, а вероятность прилипания электрода - снизить. На лицевой панели располагается кабель, с помощью которого обеспечивается легкая смена полярности. Фильтр, через который проходит напряжение, представляет собой современный силовой блок IGBT. Благодаря встроенному устройству защиты от колебаний сети, агрегат продолжает стабильно работать при напряжении до 120 В в полуавтоматическом режиме и до 140 В в режиме ручной электродуговой сварки. Широкий диапазон рабочих температур (от - 20 до +50) позволяет проводить работы не только в закрытых помещениях.
Технические характеристики Aurora PRO SPEEDWAY 175 IGBT 10038
• Номинальное напряжение на входе, В 220
• Max ток, А 175
• Min ток, А 10
• Диаметр электр/провол, мм 1-4/0.6-1.0
• Вес, кг 12,8
• Max мощность, кВт 8,1
• Степень защиты IP23S
• Наличие сетевой вилки да
• Габариты, мм 420х220х439
• Режим сварки с газом/без газ
Шланг подвода газа, проволоки, электроэнергии.
Разрез такого шланга изображен на Рис. 7. 7.
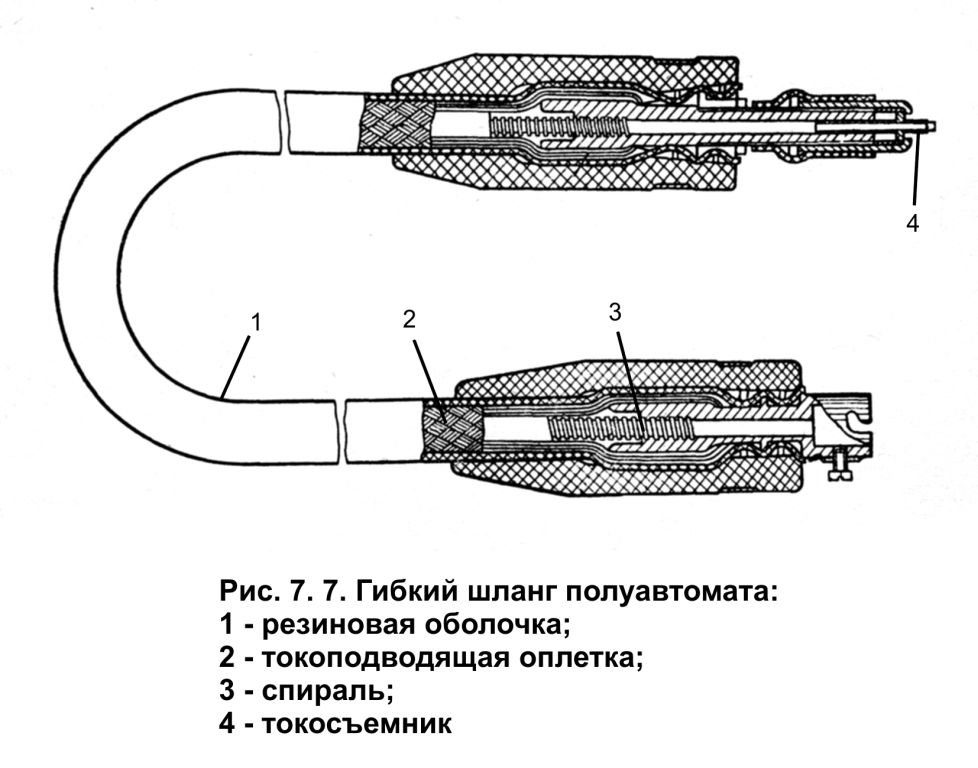
Резиновая оболочка является направляющей для подвода защитного газа.
Ток к токосъемнику подводится по многожильной токоподводящей оплетке.
Спираль облегчает скольжение сварочной проволоки.
Ток к сварочной проволоке подводится с помощью токосъемника.
Соотношение между диаметром сварочной проволоки и внутренним диаметром спирали и токосъемника
Таблица 8
Диаметр электродной проволоки, мм | Внутренний диаметр спирали, мм | Внутренний диаметр токоподводящего наконечника, мм |
0,8 | 1,5 | 0,9 |
1,0 | 1,5 | 1,2 |
1,2 | 2,5 | 1,4 |
1,4 | 2,5 | 1,6 |
Газоэлектрическая горелка.
Для полуавтомата Aurora PRO SPEEDWAY 175 IGBT10038 выбрал горелку MIG-150 BRIMA. Горелка снабжена эргономичной ручкой с несколькими вырезами, которые хорошо ложатся в ладонь сварщика. Кабель-канал может принимать проволоку от 0.6 до 1.0 мм. Длина рукава составляет 3 м, чего достаточно для стационарного сварочного поста в мастерской. Если варить на токе 150 А, то продолжительность включения составит 60%. Евроразъем оснащен выступающей рельефностью, которая облегчает подсоединение к сварочному аппарату. Аксессуар охлаждается воздухом снаружи и газом изнутри.
Горелка примечательна удлиненным соплом, которое подходит для сварки на прямой и обратной полярности (меньше греется). Еще угол наклона гусака минимальный, что позволяет заводить ее в трубы и вести сварку в труднодоступных местах.
Во время работы пистолет нуждается в постоянном уходе. Брызги металла, в изобилии образующиеся при газовой сварке, попадают в полость между газовым соплом и контактным наконечником. Их необходимо регулярно удалять маленькой отверткой. Второе приспособление, что
должно быть всегда под рукой, – кусачки-бокорезы. Ими удаляется излишек сварочной проволоки. В процессе сварки необходимо контролировать такой параметр, как вылет сварочной проволоки.
Понижающий редуктор.
Для понижения давления углекислого газа, поступающего из баллона, до рабочего состояния и поддержания его постоянным необходимо применять понижающие редукторы по ГОСТ 13861-80 «Редукторы для газопламенной обработки. Общие технические условия (с Поправкой)». Рекомендуется применять углекислотные редукторы У-30. Допускается применение кислородных редукторов РК-53Б, РКД-8, ДКП-1-65 и ДКД-8-65, а также редукторов для защитных газов АР-10, АР-40, АР-150, А-30, А-90 и Г-70.
6. Технологические указания по сварке
6.1 Полуавтоматическая сварка в среде углекислого газа.
6.1. 1 Полуавтоматическая сварка в защитных газах выполняется на постоянном токе обратной полярности.
6.1.2. Выбор диаметра сварочной проволоки и зависимости от толщины свариваемого металла рекомендуется производить в соответствии с табл.9.
Таблица 9.
Зависимость диаметра сварочной проволоки от толщины свариваемого металла
-
Толщина свариваемого металла, мм
Диаметр сварочной проволоки, мм
До 2 включ.
Св. 3 " 5 "
" 4 " 8 "
"6"12"
" 10 и более
0,8-1,0
1,0-1,2
1,2-1,4
1,4-1,6
1,6-2,0
6.1.3. Ориентировочный расход сварочной проволоки при сварке в углекислом газе и смесях CO2 + O2составляет от 1,1 до 1,15 кг на 1 кг наплавленного металла, а при сварке в смесях на основе аргона - от 1,05 до 1,06 кг.
6.1.4. Ориентировочный расход защитной газовой среды составляет от 0,5 до 0,7 м3 на 1 кг наплавленного металла. Наименьшее количество газа расходуется при сварке тавровых соединений и угловых с внутренней стороны, средне-стыковых и наибольшее - угловых с наружной стороны.
6.1.5. Рекомендуемый диапазон режимов сварки в зависимости от диаметра сварочной проволоки и пространственного положения шва приведен в табл.10.
Таблица 10.
Зависимость режимов сварки от диаметра сварочной проволоки
-
Диаметр
сварочной
проволоки
мм
Пространственное положение шва
Вылет
электрода, мм
нижнее
режимы сварки
сварочный ток, А
напряжение дуги, В
0,8
1,0
1,2
1,4
1,6
2,0
50-120
50-180
120-260
130-350
150-420
200-500
17-20
20-23
21-24
21-25
21-28
26-34
6-10
7- 12
8-12
10-14
12-18
14-20