Файл: Реферат Методы прессования нанопорошков По дисциплине Объемные наноструктурированные конструкционные материалы.docx
Добавлен: 30.11.2023
Просмотров: 97
Скачиваний: 3
ВНИМАНИЕ! Если данный файл нарушает Ваши авторские права, то обязательно сообщите нам.
Размер и форма частиц зависят от температуры процесса, состава атмосферы и давления в реакционном пространстве. В атмосфере гелия частицы будут иметь меньший размер, чем в атмосфере аргона — более плотного газа. Таким метолом получают порошки Ni, Мо, Fе, Тi, Аl. Размер частиц при этом — десятки нанометров.
В свое время появился, а в дальнейшем утвердился способ получения наноматериалов путем электрического взрыва проволок (проводников). В этом случае в реакторе между электродами помещают проволоки металла, из которого намечается получение нанопорошка, диаметром 0,1...1,0 мм.
На электроды подают импульс тока большой силы (104...106 А/мм2). При этом происходит мгновенный разогрев и испарение проволок.
Пары металла разлетаются, охлаждаются и конденсируются. Процесс идет в атмосфере гелия или аргона.
Наночастицы оседают в реакторе. Таким способом получают металлические (Тi, Со, W, Fе, Мо) и оксидные (TiO2, Аl2O3, ZrO2) нанопорошки с крупностью частиц до 100 нм.
1.3. Механические методы
Способы измельчения материалов механическим путем в мельницах различного типа — шаровых, планетарных, центробежных, вибрационных, гироскопических устройствах, аттриторах и симолойерах.
Аттриторы и симолойеры — это высокоэнергетические измельчительные аппараты с неподвижным корпусом—барабаном с мешалками, передающими движение шарам в барабане.
Аттриторы имеют вертикальное расположение барабана, симолойеры — горизонтальное.
Измельчение размалываемого материала размалывающими шарами в отличие от других типов измельчающих устройств происходит главным образом не за счет удара, а по механизму истирания.
Емкость барабанов в установках этих двух типов достигает 400...600 л.Механическим путем измельчают металлы, керамику, полимеры, оксиды, хрупкие материалы. Степень измельчения зависит от вида материала. Так, для оксидов вольфрама и молибдена получают крупность частиц порядка 5 нм, для железа — порядка 10...20 нм.
Разновидностью механического измельчения является механосинтез, или механическое легирование, когда в процессе измельчения происходит взаимодействие измельчаемых материалов с получением измельченного материала нового состава. Так получают нанопорошки легированных сплавов, интерметаллилов, силицидов и дисперсно-упрочненных композитов с размером частиц 5...15 нм.
Уникальным достоинством способа является то, что за счет взаимодиффузии в твердом состоянии здесь возможно получение «сплавов» таких элементов, взаимная растворимость которых при использовании жидкофазных методов пренебрежимо мала.
Положительной стороной механических способов измельчения является сравнительная простота установок и технологии, возможность измельчать различные материалы и получать порошки сплавов, а также возможность получать материал в большом количестве.
К недостаткам метода относятся возможность загрязнения измельчаемого порошка истирающими материалами, а также трудности получения порошков с узким распределением частиц по размерам, сложности регулирования состава продукта в процессе измельчения. [2,3]
2. Свойства
При получении наночастиц любым методом проявляется еще одна их особенность — склонность к образованию объединений частиц. Такие объединения называют агрегатами и агломератами. В результате, при определении размеров наночастиц, необходимо различать размеры отдельных частиц (кристаллитов) и размеры объединений частиц.
Различие между агрегатами и агломератами не является четко определенным. Считается, что в агрегатах кристаллиты более прочно связаны и имеют меньшую межкристаллитную пористость, чем в агломератах.
Проблема, связанная с агрегированием наночастиц, возникает при их компактировании. Например, при компактировании агрегированного порошка путем спекания, для достижения определенной плотности материала требуются температуры тем выше, чем более крупные объединения наночастиц имеются в порошке.
В этой связи при разработке методов получения нанопорошков продолжаются поиски мер для исключения или уменьшения степени образования объединений наночастиц. Так, в методах получения нанопорошков путем конденсации из паровой фазы оказалось целесообразным точное регулирование температуры образования наночастиц. В химических методах оказывается эффективным исключение воды из некоторых стадий синтеза для уменьшения степени агломерирования.
Используются также методы уменьшения контакта между частицами путем их покрытия (капсулирования), которое затем, перед компактированием, удаляется.
Тем не менее агрегирование и агломерирование наночастиц осложняет получение компактных материалов.
Требуются большие механические усилия или повышение температуры (при спекании), чтобы преодолеть силы агломерирования.[2]
3. Методы формования изделий из нанопорошков.
Компактирование является технологическим процессом, в результате которого из порошка получают готовую деталь. Процесс обычно проводят в две стадии:
формовка и спекание. В ряде методов обеспечивается совмещение этих стадий в одну. Для получения объемных наноматериалов из порошков в основном используется формовка при комнатной температуре с последующим спеканием [7].
3.1. Методы формовки
В порошковой металлургии в настоящее время применяются множество технологий формовки. Для прессования нанопорошков наиболее широкое распространение получила технология одноосного прессования. Используются такие его методы как: статическое (прессование в пресс-формах или штамповка), динамическое (магнитно-импульсное и взрывное) и вибрационное (ультразвуковое) прессование [7]. Указанные виды прессования достаточно известны, повсеместно используются при формовке обычных порошков и достаточно широко освещены в литературе [6].
Для получения высокоплотных формовок используется прессование, при котором условия сжатия материала близки к всестороннему. Эта технология получила название изостатического прессования. Существует несколько его вариантов: гидростатическое, газостатическое, квазигидростатическое. При изостатическом прессовании порошка его помещают в эластичную или деформируемую оболочку. Получаемые формовки отличаются практически однородной плотностью (правда иногда во внутренних объемах формовки она несколько меньше) и не имеют выраженной анизотропии свойств. Недостатком является достаточная сложность и дороговизна оборудования и сложность выдерживания точности размеров формовки [8].
Гидростатическое прессование проводят при использовании резиновых или других эластичных оболочек толщиной 0,1-2 мм. Оболочку с порошком помещают в рабочую камеру гидростата и нагнетают туда жидкость (масло, вода, глицерин и др.) под высоким давлением (от 100 до 1200 МПа). Получаемые формовки могут иметь сложную форму
Газостатическое прессование проводят при использовании металлических оболочек (капсул) из алюминия или пластичных сталей. Форма оболочек – простая, максимально приближенная к готовым изделиям. Часто газостатическому прессованию подвергают уже полученную ранее другими методами заготовку. Металлическую капсулу помещают в газостат, в рабочей камере которого создают давление до 200…300 МПа [1-4].
Квазигидростатическое прессование является упрощенным вариантом гидростатического прессования. Порошок помещают в эластичные оболочки, прессование которых проводят при одностороннем или двустороннем приложении давления в обычном прессовом оборудовании. Материал оболочки (резиновая масса, эпоксидные смолы и т.д.) должен под давлением вести себя подобно жидкости, иметь определенную упругость и не склеиваться с порошком.
Успешно начал использоваться в последнее время и метод интенсивной пластического деформирования – кручение под давлением. В отдельных случаях для получения лент применяют прокатку.
3.2. Методы спекания
Спекание формовок из нанопорошка ограничено невозможностью использовать высокие температуры. Повышение температуры спекания приводит к уменьшению пористости, но, с другой стороны, ведет и к росту зерна. Эту проблему решают рядом методов активации, позволяющих добиваться получения низкой пористости изделий при более низких температурах спекания [6-8]:
применение высокоскоростного микроволнового нагрева (при увеличении скорости нагрева с 10 до 300 град/мин необходимая температура спекания нанопорошка TiО2 снижается с 1050 до 975 оС [7]);
ступенчатое контролируемое спекание;
плазмоактивированное спекание.
проведение спекания в вакууме или восстановительных средах (для металлических порошков)
Методы спекания под давлением
Совмещение процессов формования и спекания или проведение спекания под давлением позволяет достигать больших значений плотности, в том числе и близких к теоретическому значению при использовании меньших температур нагрева. Наиболее простой способ – спекание при одноосном приложении давления. Так по данным [7] при проведении спекания нанопорошка железа под давлением прессования до 400 МПа температура спекания, при которой отсутствует пористость, снижается с 700 до 350 оС, а размер зерна изделий уменьшается с 1,2 мкм до 80 нм. Схема установки, разработанной в ИМЕТ РАН для спекания нанопорошков под давлением приведена на рис. 4.11. В случае металлических нанопорошков для активации процесс проводят в вакууме или восстановительной атмосфере.
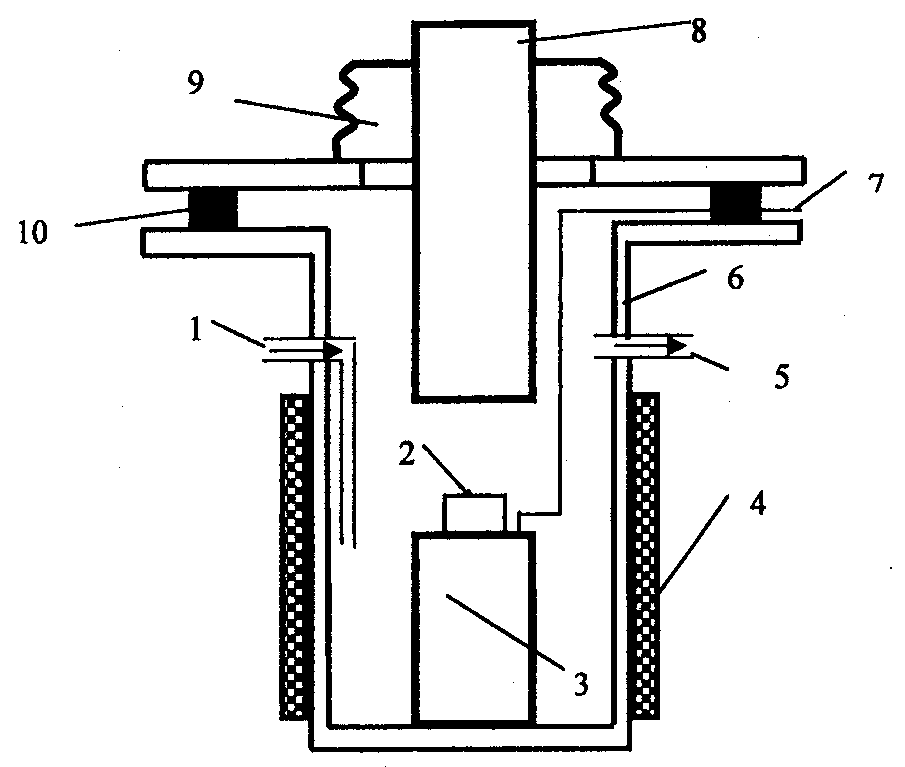
Рис. 1. Схема установки, разработанной в ИМЕТ РАН для спекания нанопорошков под давлением: 1- вход инертного или реакционного газа, 2- формовка, 3- наковальня, 4- нагревательный элемент, 5- вывод газа, 6- рабочая камера, 7- термопара, 8- пуансон, 9- сильфон, 10- герметизирующая прокладка [7].
Более прогрессивным методом совмещения процессов формовки и спекания является горячее изостатическое прессование. Метод горячего изостатического прессования (ГИП) с использованием газостатов является универсальным и широко известен в практике порошковой металлургии [5, 6]. В современных установках могут быть достигнуты давления до 300 МПа и температуры до 2000 оС. Металлические сварные капсулы для порошков изготавливают в этом случае из углеродистой или коррозионностойкой стали. Для простых изделий используются только стальные капсулы, а для изделий достаточно сложной формы – изготавливаемые по отдельной технологии специальные металлокерамические формы. На качество изделий влияют не только технологические параметры ГИП, но и качество изготовления капсул и процесс их заполнения порошком. Часто при заполнении порошком применяют виброуплотнение порошка, проводят дегазацию и тщательную герметизацию капсул [5, 6]. В случае нанопорошков из-за их большой удельной поверхности и склонности к газонасыщению проведение дегазации особенно важно [7].
Более дешевым вариантом, заменяющим ГИП, является так называемый метод быстрого ненаправленного компактирования [5, 6]. В этом процессе используется нагреваемая толстостенная цилиндрическая пресс-форма, которая после заполнения порошком подвергается одноосному сжатию под высоким давлением (до 900 МПа). При этом внешние стенки пресс-формы плотно прилегают к металлическому цилиндру соответствующих размеров, который препятствует деформации пресс-формы. В результате заполненный порошком внутренний объем, который имеет форму будущей детали, находится под квазиизостатическим давлением. Метод позволяет спрессовать металлический порошок почти до 100% плотности всего за несколько минут.
Метод высокотемпературной газовой экструзии заключается в получении формовки гидростатическим методом при комнатной температуре, ее термической обработке в среде водорода при относительно низкой температуре и последующем экструдировании при повышенной температуре [7,8]. Этот метод позволяет проводить компактирование порошков при кратковременном температурном воздействии и достаточно больших температурах. Например, компакты, полученные этим методом из никелевого нанопорошка, отличались высокими прочностными показателями при одновременных очень хороших показателях пластичности [8, 9].