Файл: Магистральный газопровод характеризует высокое давление (до 10 мпа), поддерживаемое в системе, большой диаметр труб (1020, 1220, 1420 мм) и значительная протяженность (сотни и тысячи километров).doc
ВУЗ: Не указан
Категория: Не указан
Дисциплина: Не указана
Добавлен: 03.12.2023
Просмотров: 155
Скачиваний: 2
ВНИМАНИЕ! Если данный файл нарушает Ваши авторские права, то обязательно сообщите нам.
Таблица 3 - Техническая характеристика ГПА ГТК-10-4
№ п/п | Наименование показателя | Параметры |
1 | Завод изготовитель | НЗЛ |
2 | Год выпуска | 1973 |
3 | Тип нагнетателя | 370-18-1 |
4 | Номинальная подача, млн. м3/сут | 37 |
5 | Станционные условия: Температура наружного воздуха, 0С Атмосферное давление Р ао, МПа | 15 0,1013 |
6 | Сопротивление входного тракта, кПа | 1,01 |
7 | Номинальная мощность N ео, тыс кВт | 10 |
8 | Эффективный к.п.д ГПУ, ео % | 29 |
9 | Номинальный расход топлива G т.го, м3/ч | 3600 |
10 | Удельный расход топлива G т.го / N ео, м3/кВт. | 0,36 |
11 | Температура газа перед ТВД 01 t вх , 0 С | 780 |
12 | Температура газа за силовой турбиной t вых ТНД о, 0 С | 495 |
13 | Степень сжатия осевого компрессора, Ек | 4,4 |
14 | Расход воздуха через компрессор Е вхко, кг/с | 190 |
15 | Степень регенерации, | 0,7 |
16 | Частота вращения силового вала, n ТНДО, об/мин | 4800 |
17 | Частота вращения турбокомпрессора n, об/мин | 5200 |
1.5 Вспомогательные системы
1.5.1 Система обеспечения маслом ГТУ
Масляное хозяйство компрессорного цеха состоит из индивидуальной системы смазки и уплотнения, комплектно поставляемой к каждому агрегату и центральной системы подачи, регенерации и хранения масла.
Индивидуальная система смазки и уплотнения агрегата состоит из рамы-маслобака (рисунок 6), насосов смазки и уплотнения, аккумулятора масла, поплавковой камеры, маслоохладителей, фильтров и трубопроводов, запорной и регулирующей арматуры.
Вдоль компрессорного цеха проложен коллектор аварийного слива масла из рамы-маслобака каждого агрегата. Переливаемое масло отводится в емкость аварийного слива масла емкостью 25 м3 с погружным насосом для откачки масла на склад ГСМ.
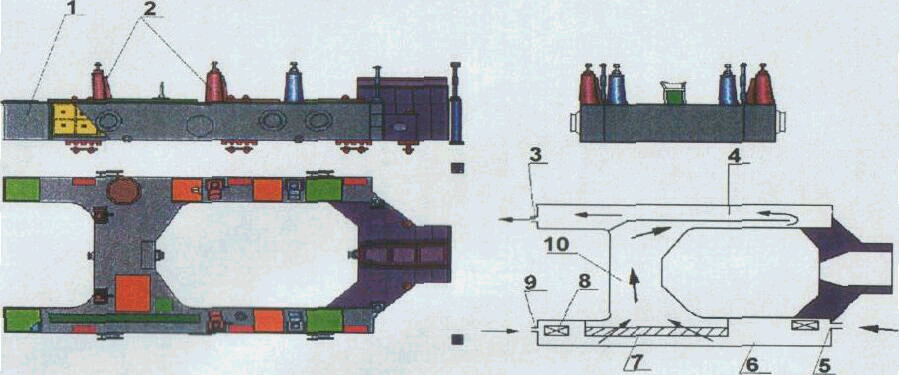
1 – корпус, 2 - опорные стойки, 3 - выход масла, 4 – перегородка, 5 – фланец, 6 - сливной отсек, 7 – фильтр, 8 – воздухоотделитель, 9 – фланец, 10 - отсек чистого масла
Рисунок 6 - Рама-маслобак
На трубопроводах аварийного слива масла из каждого агрегата предусмотрена дистанционно управляемая задвижка с пневмоприводом и задвижки (на байпасе) с ручным управлением, штурвалы которых вынесены за стенку под галерею нагнетателей. Охлаждение масла производится в воздушных холодильниках, поставляемых заводом изготовителем агрегатов. Маслоохладители расположены под воздухозаборной камерой. Для предпускового разогрева масла предусмотрен обогрев маслоохладителей электрокалорифером и установка масляного подогревателя предпускового подогрева, теплоносителем в котором является горячая вода из системы отопления.
Рама-маслобака сварной конструкции выполнена из листовой стали. На верхнем листе рамы установлены опорные стойки 2 на которые лапами опирается корпус турбокомпрессора, на специальные опорные площадки устанавливается корпус подшипников силовой турбины, размешаются люки для установки оборудования внутрь маслобака, а также для окраски и очистки маслобака; имеется шесть реперных площадок для установки гидроуровней при монтаже оборудования. Через реперные площадки проходят 12 анкерных шпилек для крепления рамы к фундаменту,
В раме-маслобаке созданы условия для прохода масла от сливного к заборному отверстию 3 в течение пяти минут, этого достаточно для выделения из масла воздуха. Масло поступает через фланцы 5 и 9 в два воздухоотделителя 8, в сливной отсек 6 и через сетчатые фильтры 7 в отсек чистого масла.
Масло движется со скоростью примерно 0,058 м/с. Огибая перегородку 4, масло подается к инжектору главного маслонасоса. Поперек протока масла устанавливаются
ребра жесткости с отверстиями и щелями, которые турбулизуют поток, улучшая выделение воздуха. С целью исключения протечек масла через масляные уплотнения, улучшения выделения воздуха из масла, лучшего гашения пены в маслосистеме установлен инжекторный отсос воздуха и паров масла из корпусов подшипников и из маслобака, в результате чего вся система находится под разряжением. Масляный бак должен быть герметизирован, что повышает также и пожаробезопасность при доливке масла во время работы ГТУ.
На раме-маслобаке установлены: вертикальный пусковой центробежный электронасос, поплавковый и электронный указатели уровня, сетчатые масляные фильтры, воздухоохладители, инжекторы главного маслонасоса, все маслопроводы в пределах турбоблока.
В системе смазки, регулирования и уплотнения нагнетателей и привода применяется масло турбинное ТП- 22.
1.5.2 Назначение и принцип действия системы топливного и пускового газа (БПТПГ)
Система предназначена для подачи пускового газа к турбодетандеру с целью запуска турбины и подачи топливного газа в камеру сгорания. В качестве топливного и пускового газа компрессорных агрегатов используется транспортируемый газ после специального блока редуцирования.
В систему топливного и пускового газа входит следующее оборудование:
-комплект запорной арматуры с ручным и автоматическим управлением;
-блок редуцирующих и предохранительных клапанов;
-блок сепараторов;
-KИП и А;
-обогревающие устройства;
-замер расхода газа.
Пусковой газ после блока редуцирования с давлением 2,5 МПа направляется в коллектор пускового газа компрессорного цеха Dу =200.
В соответствие с ТУ 108-641-77 расход топливного газа на один агрегат составляет 4,4 тыс. н. м3/час (ГТК-10-4). Давление топливного газа 1,5±0,03 МПа. Расход пускового газа на один запуск в соответствии с ТУ 108-641-77 нормируется не более 1000 кг. Давление пускового газа 2,5±0,03 МПа. Время запуска агрегата из холодного состояния, включая принятие нагрузки, соответствующей оборотам силового вала 3300 об/мин., составляет ориентировочно 15 мин.
1.6 Очистка газа от механических примесей
Установка очистки газа предназначена для очистки природного газа от механических примесей, углеводородного конденсата, воды и их сбора и состоит из:
- шести мультициклонных пылеуловителей
- дренажных коллекторов диаметром Ду=100мм

150 мм;
- емкости сбора углеводородного конденсата и жидкости.
Пылеуловитель (производительность Q = 20 млн. м3/сут) предназначен для очистки природного газа от сухих механических примесей или жидкости на компрессорных станциях магистральных газопроводов.
Пылеуловитель представляет собой аппарат цилиндрической формы диаметром Ду=2000 мм и высотой Н=9225 мм со встроенными циклонами.
Для полного и эффективного отделения из потока газа конденсата и механических примесей аппарат содержит три следующие основные секции:
- секция ввода газа;
- секция очистки газа;
- секция сбора уловленной жидкости и механических примесей.
Секция ввода газа состоит из вводной трубы диаметром Ду=500 мм и распределительного корпуса.
Секция очистки газа состоит из пяти циклонов ЦН-15 диаметром
Ду = 600 мм закрепленных неподвижно на нижней решетке. Циклонный элемент состоит из корпуса трубы диаметром Ду = 600

Нижняя часть аппарата, являющаяся сборником примесей, обогревается при помощи подогревателя змеевикового типа, необходимого для подогрева жидкости в зимнее время. В нижней части аппарата находится дренажный штуцер диаметром Ду = 50 мм.
Для обеспечения контроля за нормальной работой, пылеуловитель снабжен штуцерами: для манометра, указателя уровня и штуцерами для сигнализатора (регулятора) уровня.
Для осмотра внутренней части аппарата, периодической его очистки, имеются два люка-лаза. Люк имеется также в нижней решетке, на которой крепятся циклонные элементы.
Пылеуловитель работает следующим образом: неочищенный газ через штуцер входа поступает в секцию ввода газа, проходит через циклонные элементы, где благодаря закручиванию потока газа в завихрителе и происходит очистка газа от механических примесей или жидкости. Отсепарированные в циклонных элементах механические примеси или конденсат собираются в сборнике в нижней части аппарата, откуда удаляются через дренажный штуцер при периодической продувке по мере накопления.
Количество пылеуловителей определяется из условия, чтобы при отключении одного аппарата, оставшиеся в работе обеспечивали необходимую степень очистки проектного объема газа при потерях давления не более 0,04 МПа.
1.7 Охлаждение газа
Блок охлаждения газа предназначен для охлаждения газа, нагреваемого в процессе компримирования в нагнетателях (средний нагрев газа в группе ЦБН составляет 35-400С). Вследствие этого ухудшается режим работы ГП, увеличиваются энергозатраты на транспорт газа. Для улучшения режима работы ГП, а также для предотвращения плавления изоляции трубопровода, протаивания грунта и как следствие потери устойчивости трубопровода, а также для предотвращения значительных термических напряжений необходимо охлаждение газа для поддержания его температуры в рабочих пределах.
На линейных КС охлаждение газа осуществляется после его компримирования в нагнетателях перед поступлением в линейную часть. Это связано с тем, что более эффективно охлаждение осуществляется при высоких температурах газа, в этом случае резко уменьшается требуемая поверхность охлаждения, а следовательно и эксплуатационные и капитальные затраты на системы охлаждения.
Наибольшее распространение в настоящее время на КС получили аппараты воздушного охлаждения газа (АВО), которые не требуют предварительной подготовки теплоносителей, имеют простые схемы и надежны в эксплуатации.
На КЦ-4 установлены 24 АВО типа «Хадсон»
Техническая характеристика
-
Номинальное рабочее давление, кгс/см2
76
Расчетное давление, кгс/см2
81
Пробное давление при гидроиспытании, кгс/см2
121
Число ходов по газу
1
Номинальный расход газа, тыс. кг/ч
196
Потребление электроэнергии, кВт
32
Количество секций
24
Площадь поверхности теплообмена, м2
11872
Основные конструктивные размеры
-
Длина трубного пучка, мм
10000
Размер аппарата в плане, мм
10250х6050
Высота трубного пучка, мм
580
Наружный диаметр трубки, мм
25,4
Толщина стенок трубок, мм
2,1 +10%
Количество трубок
276
Среда – природный газ