ВУЗ: Не указан
Категория: Не указан
Дисциплина: Не указана
Добавлен: 26.10.2023
Просмотров: 95
Скачиваний: 2
ВНИМАНИЕ! Если данный файл нарушает Ваши авторские права, то обязательно сообщите нам.
p2=0,2 Sp=0,2*1,5=0,3 мм/мин;Sp2=0,2 Sp=0,2*1,7=0,34 мм/мин
6.3.1.5. Назначаем ускоренную подачу Sуск , мм/мин.
Sуск=2,5 Sp=2,5*1,5=3,75мм/мин; Sуск=2,5 Sp=2,5*1,7=4,25мм/мин
6.3.1.6. Расчет пути шлифования, мм.
Lp=p+
L=0.45+0.06=0.51 мм; Lp=p+
L=0.45+0.06=0.51 мм
Lуск =0,3*0,51=0,153; Lуск =0,3*0,51=0,153
6.3.1.7. Расчет величины пути шлифования пути шлифования по этапам при автоматическом цикловом шлифовании:
-в два этапа:
предварительное шлифование:
Lр1 =Lр –(Lр. уск.+Lр2)=0,51-(0,153+0,3)=0,06мм;
Lр1 =Lр –(Lр. уск.+Lр2)=0,51-(0,153+0,34)=0,02мм;
-чистовое шлифование Lр2=0,25*0,45=0,11 мм.
6.3.1.8. Определение времени выхаживания Твых , мин.
Твых=0,10 [17,карта ШК-3, стр. 202]
6.3.1.9.Расчет основного времени То , мин.
,
мин.
мин.
Продольная подача при обработке поверхности Ø40к6,
продольная подача при обработке поверхности Ø35к6.
6.4. Определение полного времени за операции
6.4.1 Токарная операция
6.4.1.1. Полное основное время
мин
6.4.1.2. Полное вспомогательное время
мин
6.4.1.3. Оперативное время
мин
6.4.1.4 Дополнительное время
мин (К=9%[10. табл. 7])
6.4.1.5. Подготовительно заключительное время [10. табл.92]
6.4.1.6. Норма времени
6.4.2.Шпоночно-фрезерная операция
6.4.2.1 Полное основное время
мин
6.4.2.2. Полное вспомогательное время
мин
6.4.2.3. Оперативное время
мин
6.4.2.4. Дополнительное время
мин (К= 9% [10. табл. 7])
6.4.2.5. Подготовительно заключительное время [10. табл.92]
6.4.2.6. Норма времени
6.4.3. Кругло-шлифовальная операция
6.4.3.1 Полное основное время
6.4.3.2. Полное вспомогательное время
6.4.3.3. Оперативное время
6.4.3.4 Дополнительное время
(К=9%[10. табл. 7])
6.4.3.5. Подготовительно заключительное время [10. табл.92]
6.4.3.6. Норма времени
7. Расчет количества станков, необходимых для выполнения производственной программы и процента их использования (для операций у которых рассчитаны режимы резания и нормы времени)
Номинальный фонд работы оборудования
52- число недель в году
40- число рабочих часов в неделю
7- число праздников в году
7- число рабочих часов
1-число смен
Действительный фонд рабочего времени оборудования
К1 = 0,95 - коэффициент, учитывающий простой оборудования из-за ремонта
К2 = 0,98 - коэффициент, учитывающий простой оборудования из-за отсутствия рабочего
Фд = 2031·0,95·0,98 = 1891 час
Количество станков для серийного производства
Тшт – штучное время на i ю операцию
Nд = 14 – количество деталей в i – й партии
Тп.з.- подготовительно – заключительное время на партию
Число партий в год
7.1 Количество станков для токарной операции
принимаем 1 станок
процент использования – 10%
7.3 Количество станков для шпоночно-фрезерной операции
принимаем 1 станок
процент использования – 18%
7.2 Количество станков для кругло-шлифовальной операции
принимаем 1 станок
процент использования – 9%
8. Оценка технико-экономической эффективности разработанного технологического процесса.
Так как Ср у станков, используемых для токарной, кругло-шлифовальной и шпоночно-фрезерной операции меньше 1, то эти станки могут быть использованы при изготовлении других деталей в других технологических процессах.
9. Безопасность технологической системы (ГОСТ 12.3.025)
9.1 Инструкция по технике безопасности при работе на токарном станке.
До начала работы:
1. Правильно наденьте спецодежду, застегните пуговицы, спрячьте волосы подголовной убор;
2. Проверьте наличие и надежность крепления защитных ограждений и соединения защитного
заземления с корпусом станка;
3. Прочно закрепите резец и обрабатываемую деталь, выньте ключ из патрона и положите на
установочное место;
4. Проверьте работу станка на холостом ходу и исправность пусковой коробки путем включения и выключения кнопок и рычагов управления ;
5. Перед самым началом работы наденьте защитные очки.
Во время работы:
1. Резец подведите плавно только к вращающейся обрабатываемой детали, не допускайте увеличения сечения стружки;
2. Перед выключением станка обязательно отведите резец от обрабатываемой детали;
3. При работе на центрах проверьте, надежно ли закреплена задняя бабка, и следите, чтобы засверловка была достаточной;
4. При выключении тока в сети во время работы немедленно выключите пусковую кнопку.
После окончания работы:
1. Отведите суппорт и выключите электродвигатель;
2. Удалите стружку со станка при помощи щетки, а из пазов станка крючком;
3. Протрите и смажьте станок, приведите в порядок инструмент и индивидуальные средства защиты.
9.2.Техника безопасности при работе на фрезерном станке.
До начала работы:
См. пункты 1,2,4,5 соответствующей части раздела 9.1. а так же:
1. Расположите инструмент и заготовки в определенном порядке на приставной тумбочке;
2. Прочно закрепите фрезу и обрабатываемую деталь .
Во время работы :
1. фрезу к обрабатываемой детали подводить плавно, и не допускайте увеличения сечения стружки;
2. Пользуйтесь только исправным инструментом;
3. Перед включением станка отведите фрезу от обрабатываемой детали;
4. При выключении тока в сети во время работы немедленно выключить пусковую кнопку станка.
Так же запрещается :
1. Работать на любых металлорежущих станках в легкой обуви;
2. Работать на станке в рукавицах, перчатках;
3. Работать с открытой головой.
Действия при авариях :
1. При возникновении любой аварийной ситуации немедленно выключить станок;
2. Сообщить мастеру участка;
3. При необходимости принять меры по оказанию первой помощи пострадавшим и ликвидации аварии.
Соблюдать правила противопожарной безопасности.
Выводы: В результате выполнения данного курсового проекта я разработал технологический процесс изготовления заданной детали (вал) , а именно : выбрал (уточнил) вид заготовки ;
выбрал станки ; измерительные средства , приспособления и инструмент необходимые для изготовления детали ; выбрал методы и способы изготовления различных поверхностей детали (например, посадочные места под подшипники шлифуются по методу врезного шлифования); рассчитал режимы резания и нормы резания на 3 операции и разработал операционную технологическую карту.
Я приобрел, определенные навыки по проектированию технологических процессов изготовления деталей резанием и систематизировал полученные ранее знания по ряду дисциплин, положения которых использовались при выполнении данной работы.
Опись входящих в проект листов:
1. Чертежи детали (А4)
2. Переработанный чертеж детали (А2)
3. Чертеж заготовки (поковки) (А2)
4. Технологические эскизы (А1)
Список используемой литературы:
1. Гжиров Р.И. Краткий справочник конструктора: справочник-Л. : Машиностроение, Ленинград издание ,1983.-464 с., ил.
2. ГОСТ 7505-89 «Поковки стальные, штампованные. Допуски, припуски и кузнечные напуски .»
Издательство стандартов, 1990 г.
3. Зорин И.М. , Зыбкин В.В., Коротков В.М. Справочник Конструктора. Новгород:»Вента-2»,1988 г.; в 2-х томах.
4. Зуев А.А. Технология машиностроения. 2-е изд., испр., доп.- Спб.: Издательство»Лань»,2003-496 с.
5. Косилов А.Г. Справочник технолога машиностроителя, в 2-х томах, Москва 1963 г.
7. Курс лекций по технологии сельскохозяйственного машиностроения, Лисов А.И.
8. Кучер А.М. и др.: Металлорежущие станки, М.: Машиностроение.
9. Лисов А.И., Головин С.И., Иванов Е.Г. Технология сельскохозяйственного машиностроения: Методическое руководство к выполнению курсового проекта студентами всех видов обучения Машино-
строительного профиля /Нижегородская государственная сельскохозяйственная академия. Н.Новгород ,2002 г.
10. Матвеев В.А., Пустовалов И.И. Техническое нормирование ремонтных работ в сельском хозяйстве.- М.: Колос, 1979.-288 с., ил.
11. Металлорежущие станки, выпущенные в 1989-1990 г.: Номенклатурный каталог; в 2-х частях /ЭНИМС.-М.: ВНИИТЭМР,1988.
12. Некрасов С.С., Зильберман Г.М. Технология материалов. Обработка конструкционных материалов резанием. М.;»Машиностроение», 1974г.,288с.
13. Нефедов Н.А. ,Осипов К.А.: Сборник задач и примеров по резанию металлов и режущему инструменту: Учеб. пособие для техникумов по предмету»Основы учения о резании металлов и режущему инструменту». 4-е изд., пераб. и доп. М.: Машиностроение,1984г.-400с.,ил.
14. Номенклатурный справочник: Универсальные металлорежущие станки, выпускаемые предприятиями министерства станкостроительной и инструментальной промышленностью в 1971-1972г.
Москва ,1974г.
15. Чернов Н.Н. Металлорежущие станки: Учебник для машиностроительных техникумов, 3-е изд.
пераб. и доп.-М.: Машиностроение, 1978г.-389с., ил.
6.3.1.5. Назначаем ускоренную подачу Sуск , мм/мин.
Sуск=2,5 Sp=2,5*1,5=3,75мм/мин; Sуск=2,5 Sp=2,5*1,7=4,25мм/мин
6.3.1.6. Расчет пути шлифования, мм.
Lp=p+
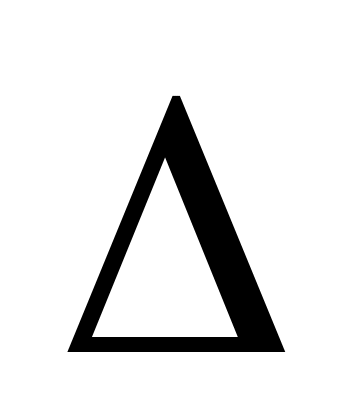
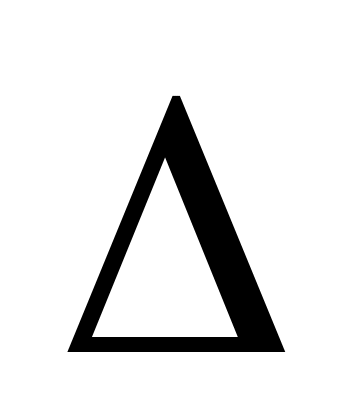
Lуск =0,3*0,51=0,153; Lуск =0,3*0,51=0,153
6.3.1.7. Расчет величины пути шлифования пути шлифования по этапам при автоматическом цикловом шлифовании:
-в два этапа:
предварительное шлифование:
Lр1 =Lр –(Lр. уск.+Lр2)=0,51-(0,153+0,3)=0,06мм;
Lр1 =Lр –(Lр. уск.+Lр2)=0,51-(0,153+0,34)=0,02мм;
-чистовое шлифование Lр2=0,25*0,45=0,11 мм.
6.3.1.8. Определение времени выхаживания Твых , мин.
Твых=0,10 [17,карта ШК-3, стр. 202]
6.3.1.9.Расчет основного времени То , мин.
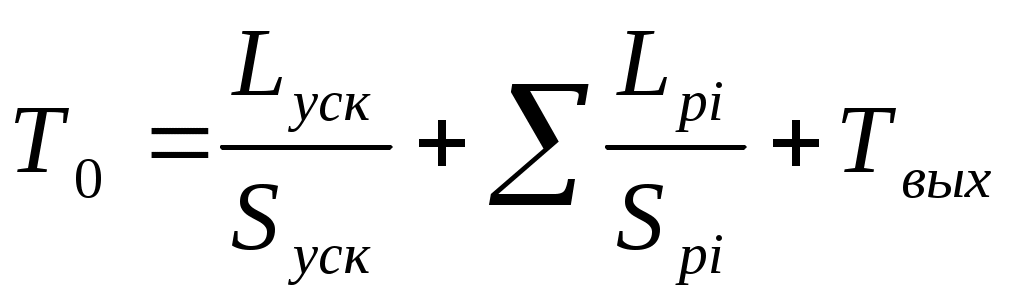


Продольная подача при обработке поверхности Ø40к6,
продольная подача при обработке поверхности Ø35к6.
6.4. Определение полного времени за операции
6.4.1 Токарная операция
6.4.1.1. Полное основное время
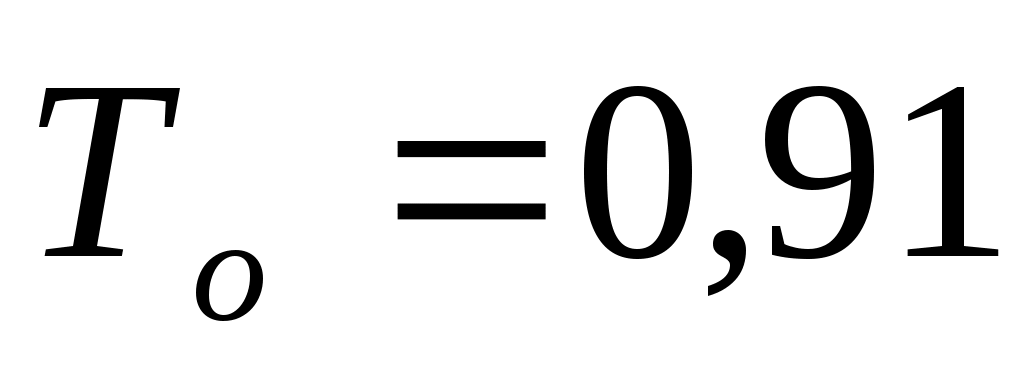
6.4.1.2. Полное вспомогательное время

6.4.1.3. Оперативное время

6.4.1.4 Дополнительное время

6.4.1.5. Подготовительно заключительное время [10. табл.92]
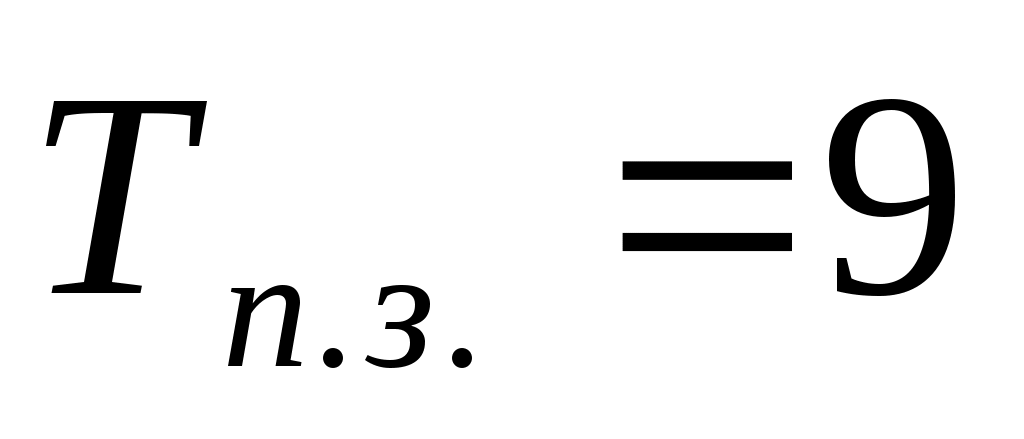
6.4.1.6. Норма времени

6.4.2.Шпоночно-фрезерная операция
6.4.2.1 Полное основное время
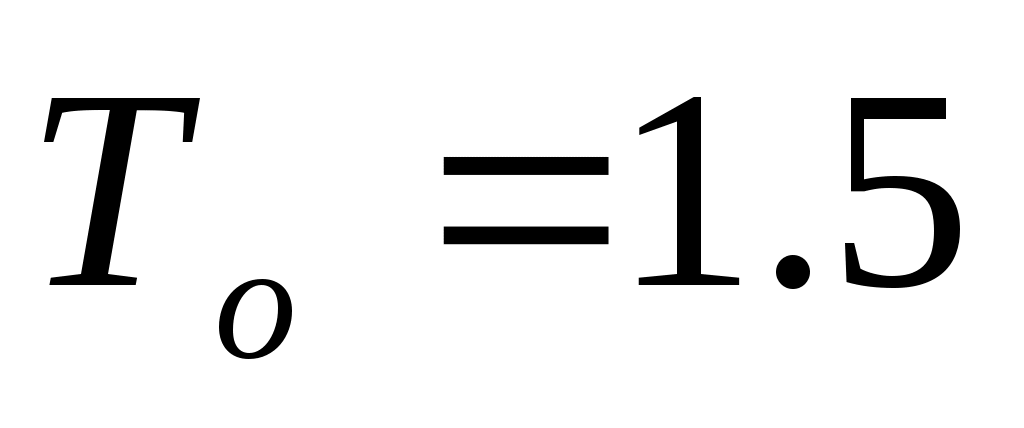
6.4.2.2. Полное вспомогательное время

6.4.2.3. Оперативное время

6.4.2.4. Дополнительное время

6.4.2.5. Подготовительно заключительное время [10. табл.92]

6.4.2.6. Норма времени

6.4.3. Кругло-шлифовальная операция
6.4.3.1 Полное основное время

6.4.3.2. Полное вспомогательное время

6.4.3.3. Оперативное время

6.4.3.4 Дополнительное время

6.4.3.5. Подготовительно заключительное время [10. табл.92]
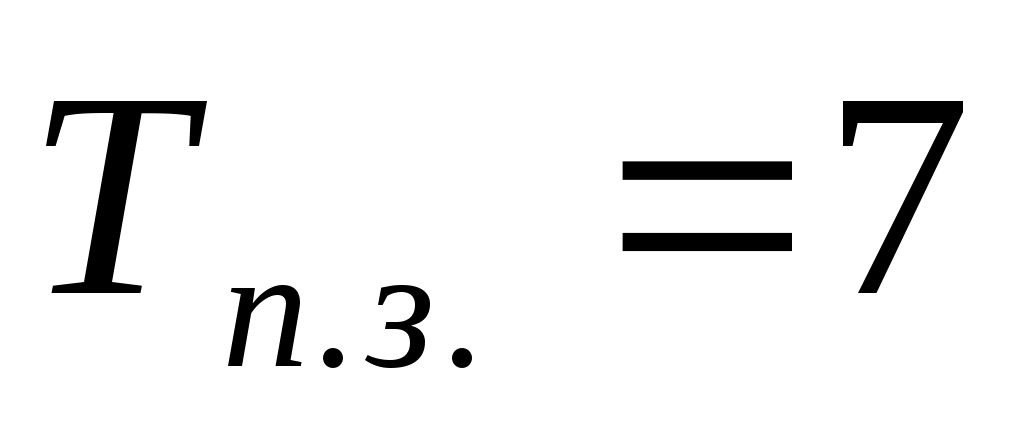
6.4.3.6. Норма времени

7. Расчет количества станков, необходимых для выполнения производственной программы и процента их использования (для операций у которых рассчитаны режимы резания и нормы времени)
Номинальный фонд работы оборудования
52- число недель в году
40- число рабочих часов в неделю
7- число праздников в году
7- число рабочих часов
1-число смен
Действительный фонд рабочего времени оборудования
К1 = 0,95 - коэффициент, учитывающий простой оборудования из-за ремонта
К2 = 0,98 - коэффициент, учитывающий простой оборудования из-за отсутствия рабочего
Фд = 2031·0,95·0,98 = 1891 час
Количество станков для серийного производства
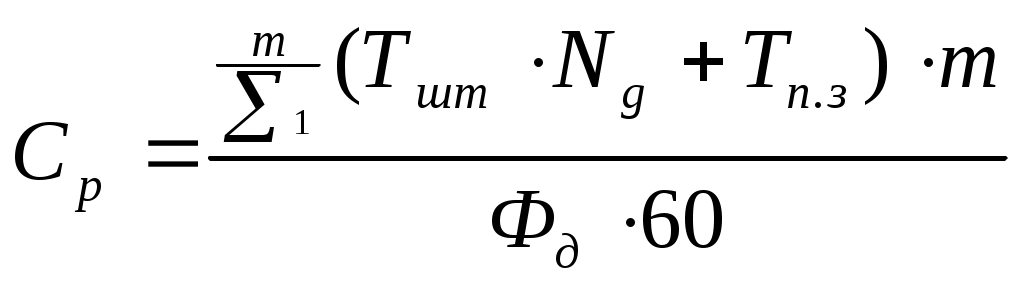
Тшт – штучное время на i ю операцию
Nд = 14 – количество деталей в i – й партии
Тп.з.- подготовительно – заключительное время на партию
Число партий в год
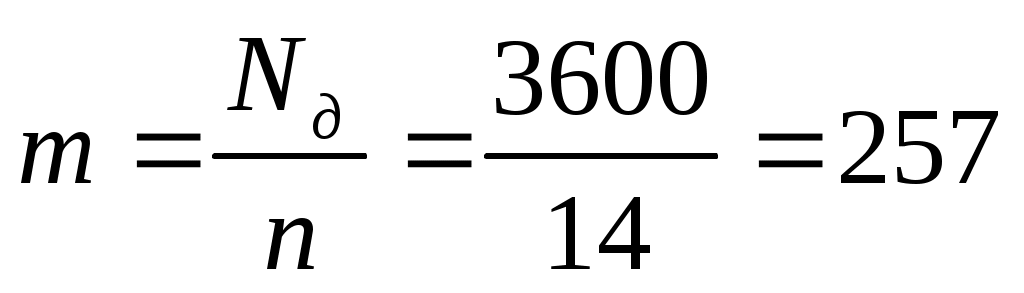
7.1 Количество станков для токарной операции
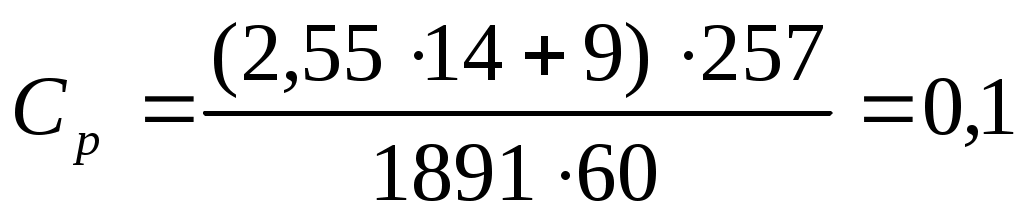
процент использования – 10%
7.3 Количество станков для шпоночно-фрезерной операции
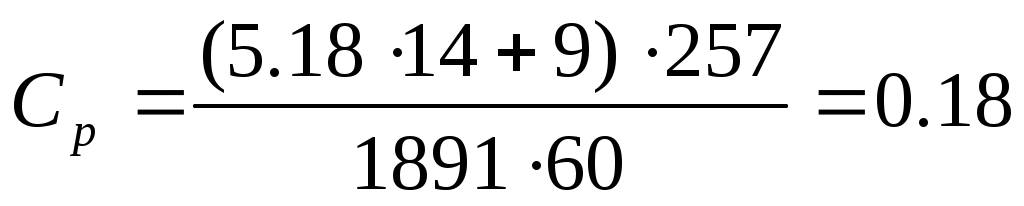
процент использования – 18%
7.2 Количество станков для кругло-шлифовальной операции
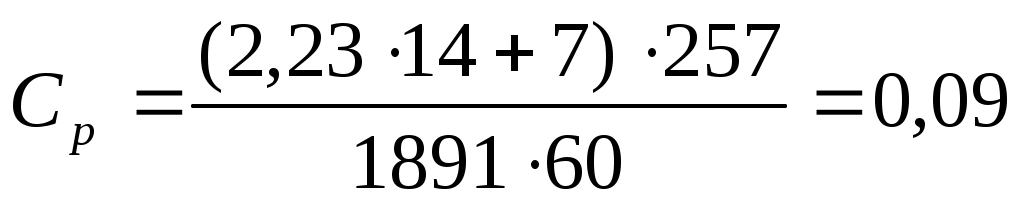
процент использования – 9%
8. Оценка технико-экономической эффективности разработанного технологического процесса.
Так как Ср у станков, используемых для токарной, кругло-шлифовальной и шпоночно-фрезерной операции меньше 1, то эти станки могут быть использованы при изготовлении других деталей в других технологических процессах.
9. Безопасность технологической системы (ГОСТ 12.3.025)
9.1 Инструкция по технике безопасности при работе на токарном станке.
До начала работы:
1. Правильно наденьте спецодежду, застегните пуговицы, спрячьте волосы подголовной убор;
2. Проверьте наличие и надежность крепления защитных ограждений и соединения защитного
заземления с корпусом станка;
3. Прочно закрепите резец и обрабатываемую деталь, выньте ключ из патрона и положите на
установочное место;
4. Проверьте работу станка на холостом ходу и исправность пусковой коробки путем включения и выключения кнопок и рычагов управления ;
5. Перед самым началом работы наденьте защитные очки.
Во время работы:
1. Резец подведите плавно только к вращающейся обрабатываемой детали, не допускайте увеличения сечения стружки;
2. Перед выключением станка обязательно отведите резец от обрабатываемой детали;
3. При работе на центрах проверьте, надежно ли закреплена задняя бабка, и следите, чтобы засверловка была достаточной;
4. При выключении тока в сети во время работы немедленно выключите пусковую кнопку.
После окончания работы:
1. Отведите суппорт и выключите электродвигатель;
2. Удалите стружку со станка при помощи щетки, а из пазов станка крючком;
3. Протрите и смажьте станок, приведите в порядок инструмент и индивидуальные средства защиты.
9.2.Техника безопасности при работе на фрезерном станке.
До начала работы:
См. пункты 1,2,4,5 соответствующей части раздела 9.1. а так же:
1. Расположите инструмент и заготовки в определенном порядке на приставной тумбочке;
2. Прочно закрепите фрезу и обрабатываемую деталь .
Во время работы :
1. фрезу к обрабатываемой детали подводить плавно, и не допускайте увеличения сечения стружки;
2. Пользуйтесь только исправным инструментом;
3. Перед включением станка отведите фрезу от обрабатываемой детали;
4. При выключении тока в сети во время работы немедленно выключить пусковую кнопку станка.
Так же запрещается :
1. Работать на любых металлорежущих станках в легкой обуви;
2. Работать на станке в рукавицах, перчатках;
3. Работать с открытой головой.
Действия при авариях :
1. При возникновении любой аварийной ситуации немедленно выключить станок;
2. Сообщить мастеру участка;
3. При необходимости принять меры по оказанию первой помощи пострадавшим и ликвидации аварии.
Соблюдать правила противопожарной безопасности.
Выводы: В результате выполнения данного курсового проекта я разработал технологический процесс изготовления заданной детали (вал) , а именно : выбрал (уточнил) вид заготовки ;
выбрал станки ; измерительные средства , приспособления и инструмент необходимые для изготовления детали ; выбрал методы и способы изготовления различных поверхностей детали (например, посадочные места под подшипники шлифуются по методу врезного шлифования); рассчитал режимы резания и нормы резания на 3 операции и разработал операционную технологическую карту.
Я приобрел, определенные навыки по проектированию технологических процессов изготовления деталей резанием и систематизировал полученные ранее знания по ряду дисциплин, положения которых использовались при выполнении данной работы.
Опись входящих в проект листов:
1. Чертежи детали (А4)
2. Переработанный чертеж детали (А2)
3. Чертеж заготовки (поковки) (А2)
4. Технологические эскизы (А1)
Список используемой литературы:
1. Гжиров Р.И. Краткий справочник конструктора: справочник-Л. : Машиностроение, Ленинград издание ,1983.-464 с., ил.
2. ГОСТ 7505-89 «Поковки стальные, штампованные. Допуски, припуски и кузнечные напуски .»
Издательство стандартов, 1990 г.
3. Зорин И.М. , Зыбкин В.В., Коротков В.М. Справочник Конструктора. Новгород:»Вента-2»,1988 г.; в 2-х томах.
4. Зуев А.А. Технология машиностроения. 2-е изд., испр., доп.- Спб.: Издательство»Лань»,2003-496 с.
5. Косилов А.Г. Справочник технолога машиностроителя, в 2-х томах, Москва 1963 г.
7. Курс лекций по технологии сельскохозяйственного машиностроения, Лисов А.И.
8. Кучер А.М. и др.: Металлорежущие станки, М.: Машиностроение.
9. Лисов А.И., Головин С.И., Иванов Е.Г. Технология сельскохозяйственного машиностроения: Методическое руководство к выполнению курсового проекта студентами всех видов обучения Машино-
строительного профиля /Нижегородская государственная сельскохозяйственная академия. Н.Новгород ,2002 г.
10. Матвеев В.А., Пустовалов И.И. Техническое нормирование ремонтных работ в сельском хозяйстве.- М.: Колос, 1979.-288 с., ил.
11. Металлорежущие станки, выпущенные в 1989-1990 г.: Номенклатурный каталог; в 2-х частях /ЭНИМС.-М.: ВНИИТЭМР,1988.
12. Некрасов С.С., Зильберман Г.М. Технология материалов. Обработка конструкционных материалов резанием. М.;»Машиностроение», 1974г.,288с.
13. Нефедов Н.А. ,Осипов К.А.: Сборник задач и примеров по резанию металлов и режущему инструменту: Учеб. пособие для техникумов по предмету»Основы учения о резании металлов и режущему инструменту». 4-е изд., пераб. и доп. М.: Машиностроение,1984г.-400с.,ил.
14. Номенклатурный справочник: Универсальные металлорежущие станки, выпускаемые предприятиями министерства станкостроительной и инструментальной промышленностью в 1971-1972г.
Москва ,1974г.
15. Чернов Н.Н. Металлорежущие станки: Учебник для машиностроительных техникумов, 3-е изд.
пераб. и доп.-М.: Машиностроение, 1978г.-389с., ил.