Добавлен: 26.10.2023
Просмотров: 274
Скачиваний: 5
ВНИМАНИЕ! Если данный файл нарушает Ваши авторские права, то обязательно сообщите нам.
- принятие материалов на учет и хранение /30/.
Основными операциями являются тесно связанные между собой операции по проверке количества и качества товаров. Следует отметить, что проверка количества, как правило, предшествует проверке качества, т.к. условия работы по приемке таковы, что количество прибывшего товара необходимо установить сразу же после его выгрузки и рассортировки /26, 3/.
Товары на складах обычно принимают заведующие отдельными складами или секциями, являющиеся материально ответственными лицами. Сроки приемки товаров должны быть минимальными /27/.
Хранение товаров на складах. Хранение товаров на складе предполагает выполнение следующих операций:
- организация складского пространства;
- размещение товаров;
- создание необходимых условий хранения и охраны товаров;
- организация учета товаров;
- движение и перемещение товаров;
- обеспечение возможностей использования подъемно-транспортного оборудования /43/.
Принятые по количеству и качеству товары выкладывают в тару, пакетируют и перемещают в зону хранения.
Используются несколько основных способов хранения товаров:
- хранение товаров по принципу однородности;
- хранение товаров в зависимости от их размера и веса;
- раздельное хранение товаров повышенного и пониженного потребительского спроса;
- отдельное хранение специфических товаров /52/.
На хранение товары укладываются различными способами (штабельный, стеллажный), выбор которых зависит от формы товара и тары, массы каждого тарного места и физических свойств товаров. Предпочтение отдается такому способу укладки, при котором не допускается повреждение товаров, тары, более рационально используются складские помещения и оборудование и создаются удобства для контроля за состоянием товарных запасов /28/.
Отборка товаров по заказу. Отпуск товаров со склада – заключительный этап складского технологического процесса, который заключается в выполнении заказов на хранящиеся на складе товары.
Отпуск товаров предполагает выполнение следующих операций:
- прием заказа;
- оформление отпуска;
- отбор товаров с мест хранения;
- комплектование заказов и упаковка;
- перемещение укомплектованных заказов в зону погрузки;
- погрузка.
Отборка может быть ручной (для небольшого количества товаров) и механизированной (для партии товаров) /21/.
1.3 Организация эффективного управления складом предприятий
Эффективность работы любого склада зависит прежде всего от эффективности организации всех складских операций, протекающих на складе /20/.
В современной литературе отмечается довольно большое разнообразие путей повышения эффективности организации складов.
Например, автор многочисленных изданий в области складирования А.М. Гаджинский, одним из основных путей повышения эффективности работы склада видит наведение порядка на складе при помощи «АВС-анализа», а также внедрения адресной системы хранения /15/.
Гаджинский А.М. в своих публикациях делает упор в основном на сокращение времени обслуживания потребителей (заказчиков), за счет четкой организации таких этапов технологического процесса, как прием товаров на хранение, размещение на хранение и хранение, отпуск товаров со склада, инвентаризация остатков /16/.
В силу развития информационных технологий, развития компьютеризации общества, такие авторы, как А.Г. Мадера, Е. Козлов, А. Куроедов в решении проблем четкой и эффективной организации складских комплексов видят другой путь – полная автоматизация всех складских операций /32/.
В литературе этих авторов упор делается на снижение вероятности ошибок работников складского хозяйства (человеческий фактор) в ходе осуществления всех складских операций за счет различных отраслевых решений для автоматизации предприятий /29/.
Например, А.Г. Мадера отмечает, что тенденция в организации работы складских хозяйств сегодня – это оптимизация всей деятельности. Важнейшей составляющей повышения эффективности работы склада является совершенствование текущих бизнес-процессов, их оптимизация, при необходимости – реорганизация имеющихся структур, и автоматизация. Под автоматизацией складского хозяйства подразумевается совокупность взаимоувязанных и согласованных процессов, методов и средств, обеспечивающих хранение, перемещение запасов и комплексный учет ТМЦ. Автоматизированное управление технологическими процессами современного складского хозяйства позволяет руководителям предприятий своевременно получать информацию о состоянии дел и при необходимости оперативно корректировать его работу /35/.
Есть еще одна группа специалистов, которые для улучшения работы склада предлагают руководителям большое внимание уделять организации системы складирования, правильного подбора необходимого складского оборудования (В.Р. Белик, М. Карусева) /28/ .
Данные авторы утверждают, что поскольку склад является неотъемлемой частью практически любого предприятия, занимающегося производством, то хранить, а значит, складировать в действующей и активно ведущей хозяйственную деятельность организации всегда найдется, что. Рачительный руководитель, организуя склад, должен обязательно позаботиться о том, чтобы его объем (полезная площадь и высота) использовались максимально эффективно. И при этом он неизбежно придет к мысли о необходимости установки на складе подходящего стеллажного оборудования /7/.
М. Карусева утверждает, что решать проблему оборудования склада, нуждающегося в стеллажах предприятие должно обращаться только в те фирмы, которые специализируется на их производстве. Таким образом, предприятие без проблем получит требуемый результат с гарантированным качеством. /28/.
В данной работе решено воспользоваться рекомендациями сразу нескольких авторов, поскольку все они имеют под собой четкое обоснование и применение на практике какого-либо одного пути повышения эффективности организации складского хозяйства не сможет решить все проблемы функционирования складского комплекса исследуемого предприятия.
1.3.1 Организация контроля за размещением товара и отбором по заказу
На товарных складах хранится большая номенклатура грузов, поэтому правильное их размещение по камерам и местам хранения значительно упрощает всю работу складов /37/.
Важнейшим требованием, которому должно отвечать правильно организованное хранение товаров на складе, является обеспечение качественной и количественной сохранности товаров. Складские работники должны хорошо знать свойства хранимых товаров, и требования к условиям хранения, владеть технологией хранения. К условиям хранения относят условия окружающей среды, т.е. температуру, влажность, солнечный свет и т.п. Технология хранения включает в себя схемы размещения товаров на складе, способы их укладки и обработки /49/.
Условия и технология хранения товаров в основном зависят от их физико-химических свойств, следовательно, могут определяться применительно не только к отдельным товарам, но и к целым товарным группам. Совместное размещение товаров однородного режима хранения обеспечивает правильное товарное соседство, исключающее возможность вредного воздействия товаров друг на друга при совместном хранении.
Функционирование склада сопровождается затратами трудовых и технических ресурсов. Снизить эти затраты можно путем разделения всего ассортимента на группы, требующие большого количества перемещений, и группы, к которым обращаются достаточно редко. Размещение названных групп товаров в разных зонах склада позволит минимизировать количество передвижений на складе /53/.
Как правило, часто отпускаемые товары составляют лишь небольшую часть ассортимента, и располагать их необходимо в удобных максимально приближенных к зонам отпуска местах, вдоль так называемых «горячих» линий (рисунок 2). Товары, требующиеся реже, отодвигают на «второй план» и размещают вдоль «холодных» линий. Вдоль «горячих» линий могут располагаться также крупногабаритные товары и товары, хранящиеся без тары, т.к. их перемещение связано со значительными трудностями.
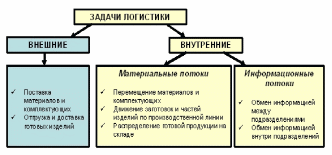
Рисунок 2 – Разделение потоков на складе на внешние и внутренние
Таким образом, задача определения приемлемого варианта размещения товаров на складе не является новой для торговли и системы материально-технического снабжения. Разработаны различные алгоритмы, предлагающие решать эту задачу с помощью ЭВМ. Решение заключается в определении оптимальных мест хранения для каждой товарной группы /40/.
Несмотря на очевидное достоинство, применение этих методов сдерживается необходимостью наличия на складах соответствующего программного обеспечения и вычислительной техники, а так же специально подготовленного персонала.
Названные ограничения могут быть преодолены в результате применения метода Парето (20/80), согласно которому 20 % объектов, с которыми обычно приходится иметь дело, дают, как правило, 80 % результат /9/.
Наиболее часто применяемый на практике вариант контроля запасов представляет собой, так называемую систему контроля «АВС», которая основана на классификации материальных ресурсов в зависимости от их роли в производственном процессе.
В группу «А» включаются наиболее важные материальные ресурсы, потребляемые производством в значительных количествах (их удельный вес в общем потреблении предприятием материальных ресурсов составляет, как правило 70-80 %). Однако в общей номенклатуре типосорторазмеров основных и вспомогательных материалов они занимают не более 15-20 %. На практике на промышленных предприятиях принято устанавливать ежедневный контроль за состояние запасов этой группы материальных ресурсов.
В группу «В» входят материальные ресурсы, имеющие меньшее значение для производственного процесса по сравнению с номенклатурной группой «А». в общем объеме потребления материальных ресурсов как по объему, так и по номенклатуре, группа «В» занимает, как правило, порядка 15-20 %. В свою очередь, периодичность контроля за состоянием запасов по данной классификационной группе по времени имеет значительно больший интервал – примерно один раз в десять дней.
К группе «С» относятся материальные ресурсы, которые по номенклатуре занимают наибольший удельный вес (до 50 %). Обычно доля потребления материальных ресурсов группы «С» в производственном процессе весьма незначительна (не более 5-10 %), поэтому состояние их запасов контролируется значительно реже предыдущих групп – примерно один раз в месяц /9/.
На складе применение метода Парето позволяет минимизировать количество передвижений посредством разделения всего ассортимента на группы, требующие большого количества перемещений, и группы, к которым обращаются достаточно редко, что обеспечивает больший контроль за качеством и количеством хранимых товаров.
Операции ручной отборки и подготовки товаров к отпуску являются на складах предприятий наиболее трудоемкими. Стоимость рабочей силы на участке подборки может составлять до 50 % стоимости всей рабочей силы, используемой на складе.
Хронометраж работы отборщика показывает что его рабочее время распределяется приблизительно следующим образом:
-
отборка товара по заказу – 10 %; -
вынужденный простой во время пополнения запаса в зоне отборки, либо во время работы в этой зоне другого отборщика – 20 %; -
работа с отборочными местами – 30 %; -
перемещение между местами отборки – 40 %.
Актуальность задачи сокращения времени на перемещение очевидна. Ее решение заключается в выделении на складе зоны для хранения резервного запаса и зоны для хранения отбираемого запаса /18/.
Отбираемые запасы располагают на нижних ярусах стеллажей, размещенных на «горячих» линиях, т.е. в доступных для осуществления операций отборки местах.
Разделение резервного и отбираемого запаса может осуществляться двумя способами: вертикальное разделение – резервный запас находится над отбираемым; горизонтальное разделение - резервный и отбираемый запас находятся в разных местах склада.
Сокращение вынужденного простоя обеспечивается за счет организации хранения товаров, пользующихся высоким спросом, в нескольких местах зоны отборки (рисунок 3).
Таким образом, у разных отборщиков появляется возможность одновременно отбирать один и тот же товар.
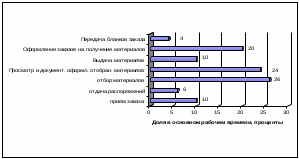
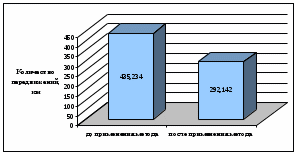
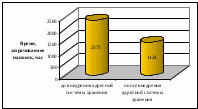
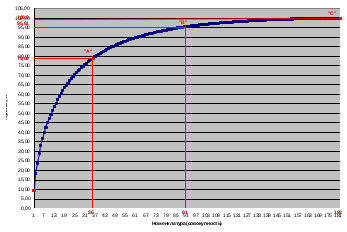
Цели автоматизации малого склада ООО «Веб логистик»