Файл: Выпускная квалификационная работа сулимов Владлен Алексеевич.docx
ВУЗ: Не указан
Категория: Не указан
Дисциплина: Не указана
Добавлен: 26.10.2023
Просмотров: 82
Скачиваний: 1
ВНИМАНИЕ! Если данный файл нарушает Ваши авторские права, то обязательно сообщите нам.
ВВЕДЕНИЕ
Металлические калитки сегодня можно встретить везде и всюду. Все большее число людей выбирает металлическую калитку в качестве входной калитки во двор, в различные учреждения, предприятия. Выбрать металлические калитки - долгое время являлось практически единственным способом защитить свое жилище, учреждения. заводы, предприятия от непрошеных гостей. Кроме того, грамотно изготовленная металлическая калитка поможет защитить территорию от воздействия окружающей среды.
Четкое понимание того, для чего предназначена калитка, что она должна делать в процессе эксплуатации (использования), является важнейшим условием для правильного выбора покупателем, или изготовление нужной ему модели калитки.
Назначение калитки определяется функциями, которые выполняют калитки в процессе своей эксплуатации. Эти функции часто называются функциональными свойствами калитки.
Все функции металлических калиток делятся на:
основную функцию, которой обладают все разновидности калиток;
дополнительные функции, которыми различные виды калиток могут обладать или не обладать в зависимости от особенностей своей конструкции.
Основной функцией калитки является закрывание и открывание во время входа на различные территории учреждений или предприятий.
Дополнительными функциями, которые калитки могут выполнять в процессе своей эксплуатации, являются:
- используется для защиты и предотвращение проникновения посторонних лиц на территории учреждения и предприятия.
Герметичность притвора, т.е. плотностью прилегания полотна к коробке, обеспечивается использованием уплотнителей в коробке или торцах калитки.
Сварка является одним из наиболее распространенных технологических процессов, как в машиностроении, так и в строительстве. От качества сварочных работ в строительстве все более зависит надежность и долговечность строящихся объектов.
Сварка - процесс получения неразъемных соединений посредством установления межатомных связей между соединяемыми частями при их нагревании и (или) пластическом деформировании.
По сравнению с другими способами получения неразъемного соединения металлических деталей, в частности, клепкой, сварка имеет ряд существенных преимуществ, важнейшими из которых являются:
-
значительная экономия металла; -
высокая плотность и прочность сварных соединений; -
меньшая трудоемкость изготовления изделий и соответственно низкая себестоимость;
- возможность механизации и автоматизации изготовления отдельных
деталей, узлов и изделий;
-
возможность соединения металлических деталей любой толщины. Основными недостатками сварки являются: -
снижение в ряде случаев механических свойств основного металла;
-
нагрева, что приводит к изменению геометрических размеров конструкций, деформациям и напряжениям; -
необходимость в ряде случаев применять для снятия напряжения термическую обработку; -
необходимость применения правки и последующей механической обработки;
- трудность соединения разнородных металлов и других материалов.
Простейшие приемы сварки были известны еще в глубокой древности.
Начало сварки как науки было положено трудами великого русского ученого-энциклопедиста М.В. Ломоносова и его сподвижника академика Т.П. Рихмана, который в 1753 г. впервые высказал мысль о возможности практического применения "электрических искр" для плавления металлов. В 1902 г. первый русский электротехник, профессор Санкт-Петербургской военно-хирургической академии В.В. Петров, используя гальванический элемент, открыл явление электрической дуги и указал возможные области ее практического применения.
Наши соотечественники первыми в мире во многих странах запатентовали способ дуговой сварки.
В 1882 г. Н.Н. Бенардос предложил способ прочного соединения и разъединения металлов непосредственным действием электрического тока, в котором используется электрическая дуга, горящая между неплавящимся угольным электродом, свариваемым изделием и присадочным металлическим стержнем.
Электрическая дуговая сварка получила дальнейшее развитие в работах Н.Г. Славянова. В 1888 г. он предложил способ сварки металлическим электродом и разработал технологические и металлургические основы электродуговой сварки, первые источники питания постоянного тока (генераторы), сварочные автоматы, ряд составов флюсов и организовал первый в мире сварочный цех по восстановлению литых деталей из стали, чугуна и цветных металлов.
В нашей стране в середине двадцатых годов начались довольно интенсивные исследования в различных областях сварки. Всему миру известны имена ученых В.П. Вологдина, Н.Н Рыкалина, С.А. Николаева, К.К. Хренова, К.В. Любавского, А.А. Ерохина и др. Особую роль в развитии и становлении сварки сыграл академик Е.О. Патон, организовавший в 1929 г. лабо
раторию, а затем институт электросварки АН УССР. В настоящее время более 96% стальных конструкций при изготовлении выполняются на сварке, а на монтаже уровень применения сварки составляет около 60%.
Трудоемкость сварочных работ занимает значительную долю в общей трудоемкости выполняемых работ. Так, при изготовлении строительных металлоконструкций сварка составляет около 24% общей трудоемкости, при монтаже внутрицеховых трубопроводов - 25-30%, технологического оборудования - 5-8%, металлоконструкций - 16-18% и т.д.
В современных условиях, как повышение качества сварных соединений, так и выполнение возросших объемов сварочных работ могут быть обеспечены на основе дальнейшей автоматизации и механизации процессов сборки и сварки, применения более совершенной технологии и организации сварочных работ, совершенствования обучения и повышения квалификации кадров.
ГЛАВА1. ОСНОВНАЯ ЧАСТЬ 1.1.Основные требования, предъявляемые к сварным конструкциям
На любом участке всегда есть несколько калиток- запасной выход, проход к соседям, вход в вольер, птичник. Даже вход в теплицу, это тоже своего рода калитка. Самый популярный способ изготовления калитки- сварить из профильной трубы, или круглой трубы, раму корпус и обшить каким- нибудь материалом.
У этой конструкции калитки много достоинства:
1.Прочность и надёжность, это немаловажно –калитка работает постоянно, открывается и закрывается несколько раз в день.
2.Большой срок службы.
3.многообразие форм и расцветок используемых материалов позволяет сделать калитку в любом стиле: «глухую» из профнастила, с орнаментом из кованных или готовых элементов декора, прозрачную из сетки или рабицы, или решётку из труб меньшего сечения.
4.Простота изготовления и установки. Изготовления рамы-каркаса-основная операция при изготовлении калитки.
Калитка делается из прямоугольной рамы с перекладиной по середине или по диагонали. К одной стороне привариваются петли, рама крепится на столб которая является стойкой для калитки. Далее каркас обшивается профнастилом или листом металла, сеткой в зависимости от предназначения. Сварку калитки начинают со сборки внешней рамы
, и на специальном столе сваривают все её элементы между собой, важно следить за правильностью сборки углов под 90градусов, проверять диагональность.
Можно сваривать калитку в виде арки, эллипса или другой формы. Прежде всего, хозяин выбирает тип калитки. Выбор зависит от размера дома и участка. Самая распространённая калитка- это распашная калитка , которая должна гармонировать с воротами и сочеталась с размерами ворот. Это важно не только с эстетической точки зрения, но и для нормального функционирования конструкции. Ведь чем тяжелее калитка, тем быстрее изнашиваются петли и замки.
Сварочные работы начинаются с подготовки чертежей и материалов, которые понадобятся в процессе сварки калитки.
Калитка должна быть не более высотой 2метров, иначе конструкция получится перегруженной и нефункциональной.
Калитки широко применяются во всех видах. Металлические калитки, как правило, выполняют из стали.
К изготовлению металлической калитки предъявляются следующие требования:
- конструкция должна быть прочной выносливой и устойчивой при действии на него эксплуатационных нагрузок;
- должна сохранять полную работоспособность в течение заданного срока службы, а именно в течении заданного гарантийного срока службы;
- должна выполняться с наименьшей трудоемкостью;
- для точного установления отдельно взятых деталей относительно друг друга применить сборочно-сварочное приспособление;
- для изготовления калитки, использовать основные и сварочные материалы, предусмотренные технологическим процессом, а именно сталь марки 20 по ГОСТу 1050-88 и сталь 09Г2 по ГОСТу 19282-89;
- сварочную проволоку СВ-08Г2С по ГОСТу 2246-70 и защитный газ СО2 по ГОСТу 8050-85;
- ручную дуговую сварку выполнять штучными электродами марки ОЗС-4;
- наличие трещин и шлаковых включений в прихватках не допускается:
- при сварке использовать рациональные режимы и технику заполнения швов с учетом особенностей и толщины металла;
- сварку производить полуавтоматом в среде защитного газа СО2;
- сварочное оборудование должно соответствовать паспортным данным, оснащено контрольно-измерительными, регулирующими приборами и защитными устройствами, обеспечивающих установленные режимы сварки и безопасность работ;
- сварные швы не должны иметь резких переходов от основного к наплавленному металлу и дефектов и должны быть не ниже прочности основного металла;
- после сварки предусмотреть зачистку сварных швов от шлака и металлических брызг и подвергнуть сварную калитку внешнему осмотру.
1.2.Организация рабочего мета при изготовлении конструкции
Сварочные посты для ручной дуговой сварки
Специально оборудованное рабочее место для сварки называют сварочным постом. Сварочные посты могут быть стационарными и передвижными.
Стационарные сварочные посты (рис.1) размещают в цехах для изготовления сварных конструкций. К посту подают собранную под сварку конструкцию, при выполнении швов сварщик передвигается, а источник питания током и пусковая аппаратура остаются неподвижными. Передвижения сварщика обусловлены длиной сварочного кабеля - не более 30-40 м; при большей длине падает напряжение в сварочной цепи, что затрудняет процесс сварки. При сварке небольших конструкций сварочный пост оборудуют в кабине размерами в плане примерно 2 х 2 м и высотой не менее 2 м. Стенки кабины могут быть изготовлены из негорючих и неэлектропроводящих материалов, например из асбестовых листов. При использовании фанеры и брезента их пропитывают огнестойким составом, например раствором алюмокалиевых квасцов.
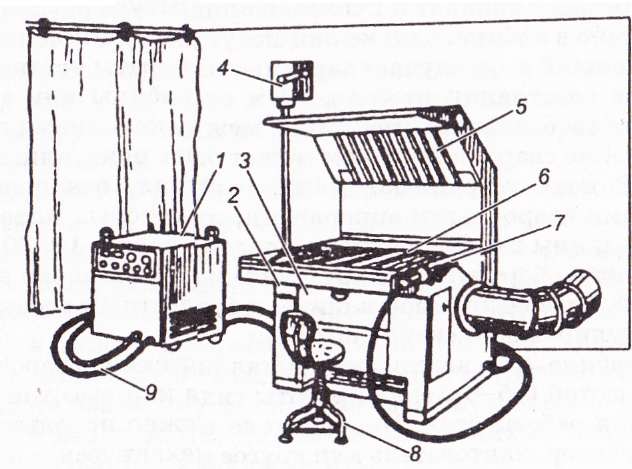
Рис. 2.1. Стационарный сварочный пост для ручной дуговой сварки:
1 - источник сварочного тока; 2 - стол для электродов; 3 - ящик для инструмента; 4 - рубильник;
5,6: - вытяжная камера; 7 – электродержатель; 8 - стул сварщика; 9 - сварочные провода
Стены окрашивают в светло-серый цвет красками, хорошо поглощающими ультрафиолетовые лучи (цинковые или титановые белила, желтый крон и др.). Освещенность кабины должна быть не менее 80 лк.
Кабину оборудуют местной вентиляцией с воздухообменом 40 м/ч на каждого рабочего. Вход в кабину закрывают брезентовыми шторами с огнестойкой пропиткой. Между стенками и полом должен быть зазор не менее 50 мм для вентиляции. Пол должен быть выложен огнестойким материалом (кирпичом, бетоном). Для включения источника сварочного тока в кабине имеется рубильник или магнитный пускатель.
Сварочный аппарат и пусковая аппаратура расположены обычно в кабине, однако они могут быть вынесены и за ее пределы. В этом случае сварочные аппараты устанавливают на расстоянии не более 15 м от кабины или места сварки в свободных промежутках между колоннами цеха.
Питание сварочным током может быть централизованным. В цехе устраивают машинный зал, оснащенный мощными сварочными аппаратами, от которых проводят медные шины вдоль колонн для подачи тока к 15-30 постам. Посты оборудуют распределительной пусковой аппаратурой, подсоединяемой к шине, и балластным реостатом для регулирования сварочного тока.