Файл: Выпускная квалификационная работа сулимов Владлен Алексеевич.docx
ВУЗ: Не указан
Категория: Не указан
Дисциплина: Не указана
Добавлен: 26.10.2023
Просмотров: 78
Скачиваний: 1
ВНИМАНИЕ! Если данный файл нарушает Ваши авторские права, то обязательно сообщите нам.
Баллоны предназначены для хранения и транспортировки защитного газа под высоким давлением. Наибольшее применение имеют баллоны емкостью 40 дм3, размеры и масса, которых приведена в таблице.
Таблица 12. Техническая характеристика баллонов
Емкость баллона ,л | 100 и 150 | 150-200 | 200 |
Толщина стенки S, мм | 5,2 | 7 | 9,3 |
Длина корпуса L,мм | 1340 | 1390 | 1460 |
Наружный диаметр D,мм | 219 | 219 | 219 |
Масса, кг | 43 | 60 | 81 |
Углекислый газ находится в баллоне в жидком состоянии. Из одного литра жидкого газа можно получить в процессе работы 509 л газообразного газа.
Редукторы предназначены для понижения давления газа, поступающего из баллона или распределительного трубопровода, и автоматического поддержания постоянного давления в зону сварки, для определения остаточного давления в баллоне. Для нашей установки используется редуктор обратного действия, с механической регулировкой давления, одноступенчатого исполнения марки У-30 и ДЗД-1-59М. Данные редукторы более надежные в работе, безопасные и не требуют дополнительной под регулировки давления в процессе работы, так как в них происходит автоматическая регулировка подачи газа из камеры высокого давления в камеру низкого давления.
При случайном давлении свыше допустимого в камере низкого давления откроется предохранительный клапан, и сжатый газ выйдет в атмосферу.
Подогреватель предназначен для подогрева углекислого газа, поступающего из баллона в редуктор, с целью предотвращения замерзания редуктора. При большом расходе углекислого газа (вследствие поглощения теплоты при испарении жидкого углекислого газа) температура газа понижается, что может привести к замерзанию имеющихся в нем влаги и закупорке кана-лов редуктора. Подогреватель используется только при сварке в углекислом газе. Он состоит из корпуса, змеевидной трубки, по которой проходит углекислый газ, кожуха, теплоизоляции и нагревательного элемента из хромони-келевой проволоки, расположенного внутри змеевика. Подогреватель крепят к баллону накидной гайкой. Питание его осуществляется постоянным током напряжением 20В или переменным током напряжением 36В. провода от шкафа управления присоединяют к зажимам.
Осушитель, применяемый при использовании влажного углекислого газа для поглощения из него влаги, может быть высокого и низкого давления. Осушитель высокого давления. Осушитель высокого давления устанавливают перед понижающим редуктором. Он имеет малые размеры и требует частой замены влагопоглотителя, что неудобно в работе. В качестве влагопоглотителя используют силикагель или алюмогель, реже - медный купорос и хлористый кальций. Силикагель и медный купорос, насыщенный влагой, поддаются восстановлению путем прокаливания при 250-300° С
Газовый клапан, используемый для экономии защитного газа, следует устанавливать по возможности ближе к сварочной горелке, иногда его встраивают в ее ручку. Наибольшее распространение получили электромагнитные газовые клапаны Газовый клапан следует включать так, чтобы была обеспечена предварительная (до зажигания дуги) подача газа, и выключать после обрыва дуги и полного затвердевания кратера шва.
Техническое нормирование показателей полуавтоматической сварки в СО2.
Расчет нормы времени

где Куч – коэффициент учитывающий организацию труда при сварке в СО2 он равен 0,6-0,8.
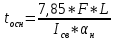
где αн – коэффициент наплавки для сварочной проволоки Св-08Г2С он равен 10 г/Ач.
Расчет расхода электродной проволоки.
Он зависит от силы сварочного тока, площади поперечного сечения шва и техники сварки и коэффициента расхода проволоки, который равен 1,3-1,5

Принимаем коэффициент равный 1,3
Расход углекислого газа
Зависит от времени и положения шва в пространстве и в среднем при сварке на полуавтомате равен 0,3-0,4 дм3/с.
GСО2 = 0,3*tосн*3600
Принимаем расход СО2 равный 0,3 дм3/с.
ГЛАВА2.ПОДГОТОВКА МЕТАЛЛА К СВАРКЕ
2.1.Подготовительно-сборочные работы
Элементы и размеры швов сварных соединений, выполненных сваркой под слоем флюса, регламентируются ГОСТом 8713-79. Тавровое соединение выполняем соответственно типу Т1
В целом подготовка кромок состоит из обрезки и разделки по определеннойформе в зависимости от толщины. Подготовленные кромки перед сваркой должны быть очищены от ржавчины, масла, краски, влаги и других загрязнений, наличие которых может привести в процессе сварки к образованию пор, шлаковых включений и других дефектов. Очистке подвергают околошовную зону шириной 25-30мм, применяя для этого вращающиеся щетки или другой абразивный инструмент. Затем выполняют сборку деталей.
При сборке деталей для сварки необходимо обеспечивать совпадение кромок и выдерживать установленный нормами размер зазора между ними. В случаях, когда устранение зазора представляет большие затруднения, необходимо принимать меры против протекания расплавленного металла и флюса, применяя подварку или выполняя сварку на флюсовой подушке. На флюсомедной подкладке (медная подкладка с канавкой, заполненной флюсом) и так далее.
Смещение свариваемых кромок относительно друг друга для листов толщиной более 10 мм не должно превышать 0,1 толщины листа, но не более 2 мм.
Сборка и прихватка осуществляется в специальных приспособлениях. При массовом и серийном изготовлении изделий используют сборочно-сварочные приспособления
Во избежание образования пор, на стыкуемых под сварку кромках не должно быть влаги, ржавчины, окалины, масла, краски. Загрязнения необходимо тщательно удалять с кромок перед сборкой. В случае применения при сборке прихваток их перед сваркой надо очистить от шлака.
Угловые швы характеризуются катетом и формой шва. Различают три типа угловых швов: нормальный, выпуклый (усиленный) и вогнутый (ослабленный). Форма шва выбирается в зависимости от условий эксплуатации изделий. В сварных конструкциях, работающих под действием вибрационных нагрузок, тавровые соединения стремятся выполнять вогнутыми швами.
Особое внимание необходимо уделять равномерности зазора по всей протяженности шва, так как неравномерный зазор. В местах с повышенным зазором шов получается вогнутым, а с небольшим зазором слишком выпуклый.
При сборке детали временно закрепляют струбцинами, прихватками или скобами. Чтобы избежать непровары в начале шва и образование кратера в конце шва применяют технологические планки на входе и выходе сварного шва, которые после сварки и остывания шва удаляют. Форма разделки кромок входных и выходных технологических планок должна быть такая же, как и кромок основного соединения. Они же являются скрепляющими элементами. Приваривать планки необходимо качественно, так как непровар в начале шва может вызвать
образование продольных горячих трещин, которые могут распространиться на основной шов.
2.1.Эскиз изделия
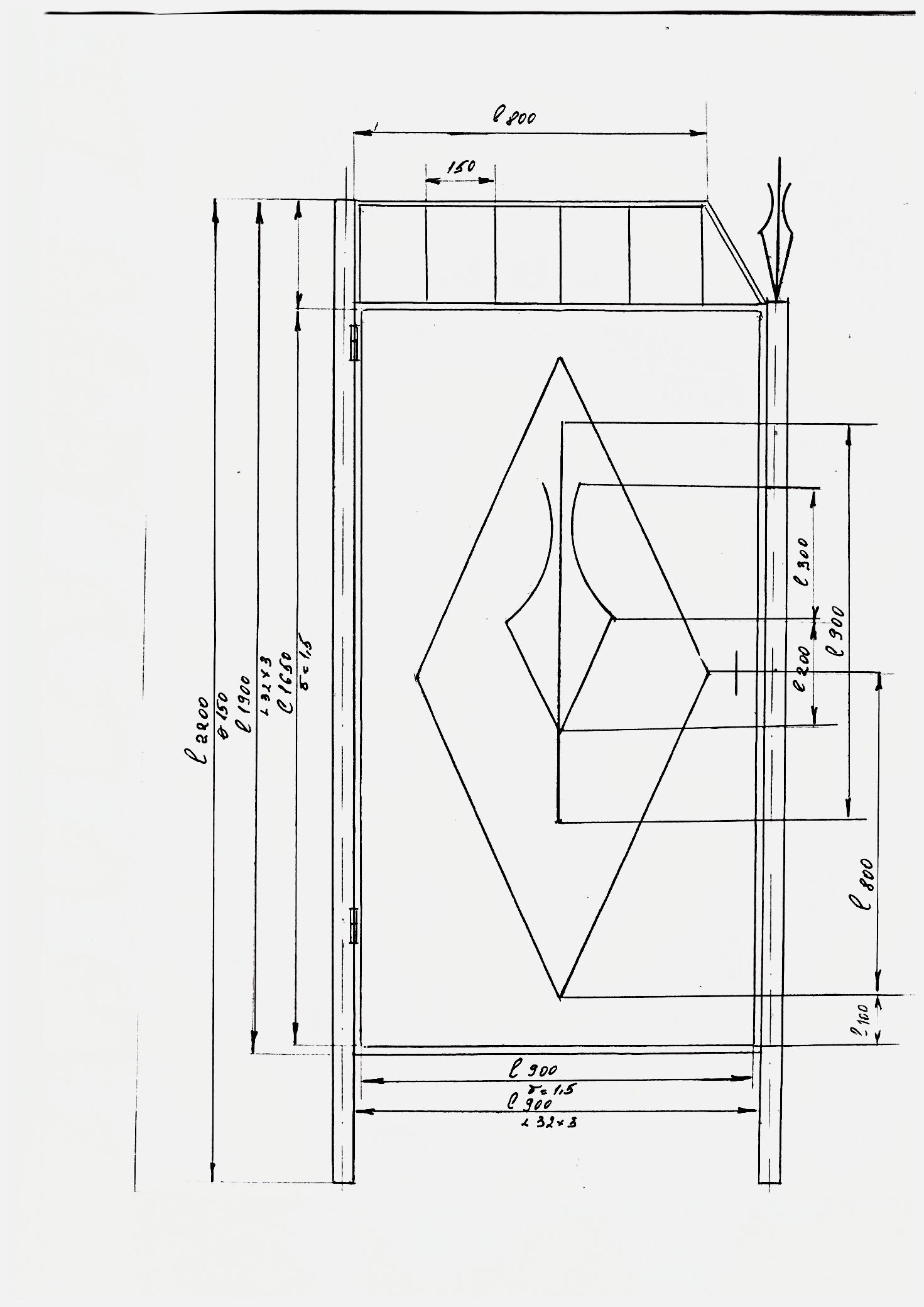
2.3.Ведомость металла на изготовления конструкции
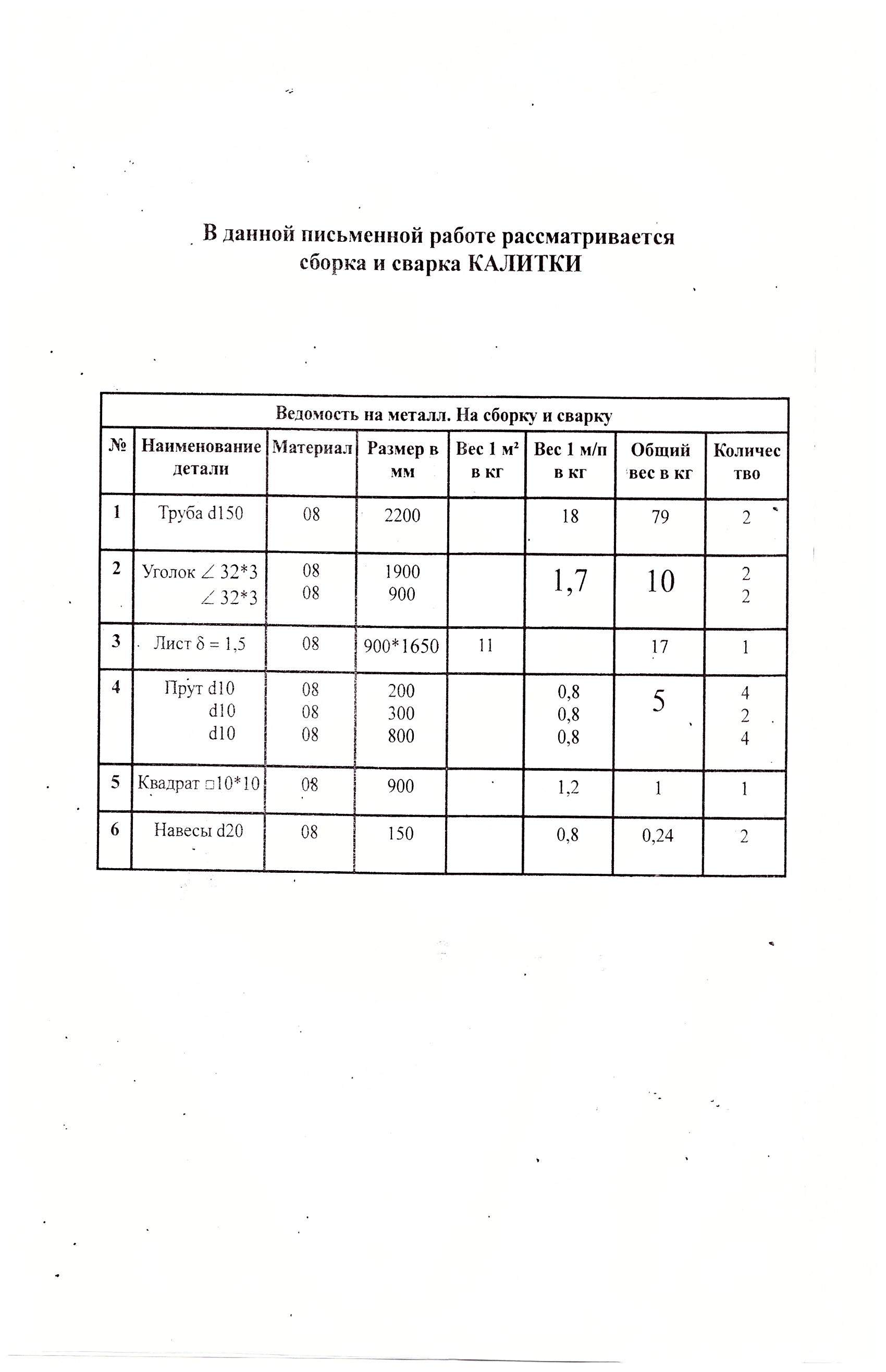
2.4.Расчёт расхода металла на изготовления изделия
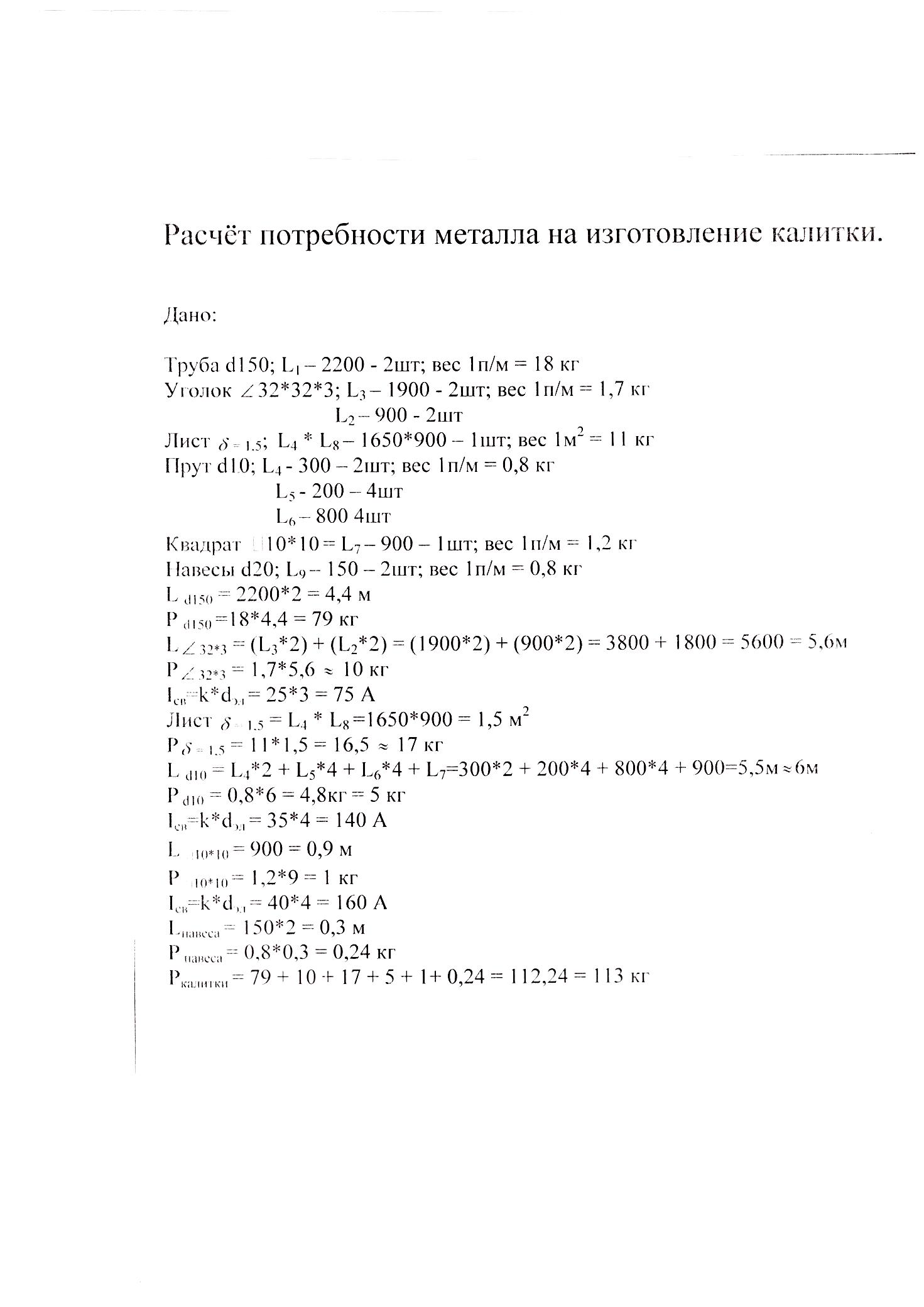
2.5.Технолоическая карта на изделие
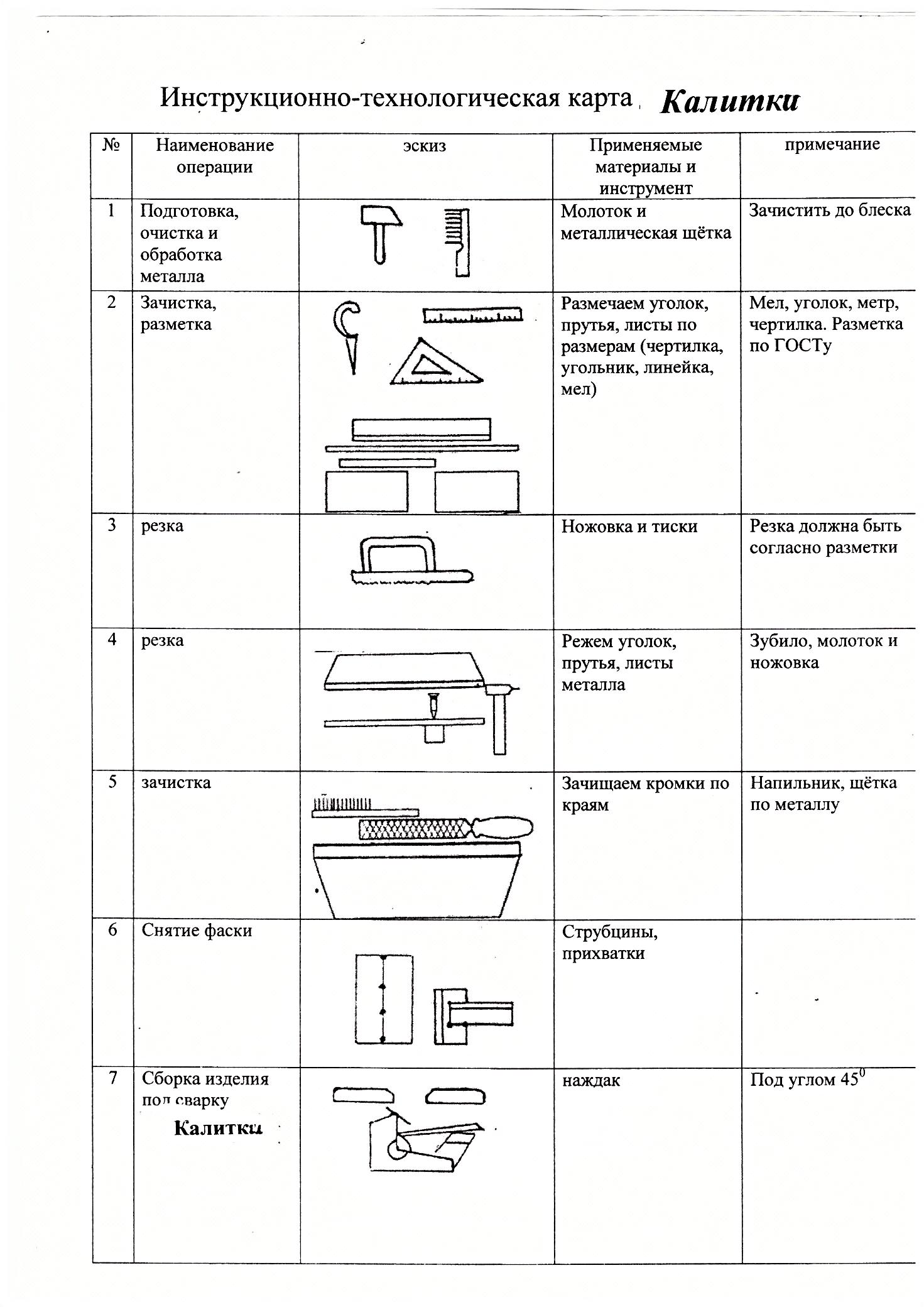
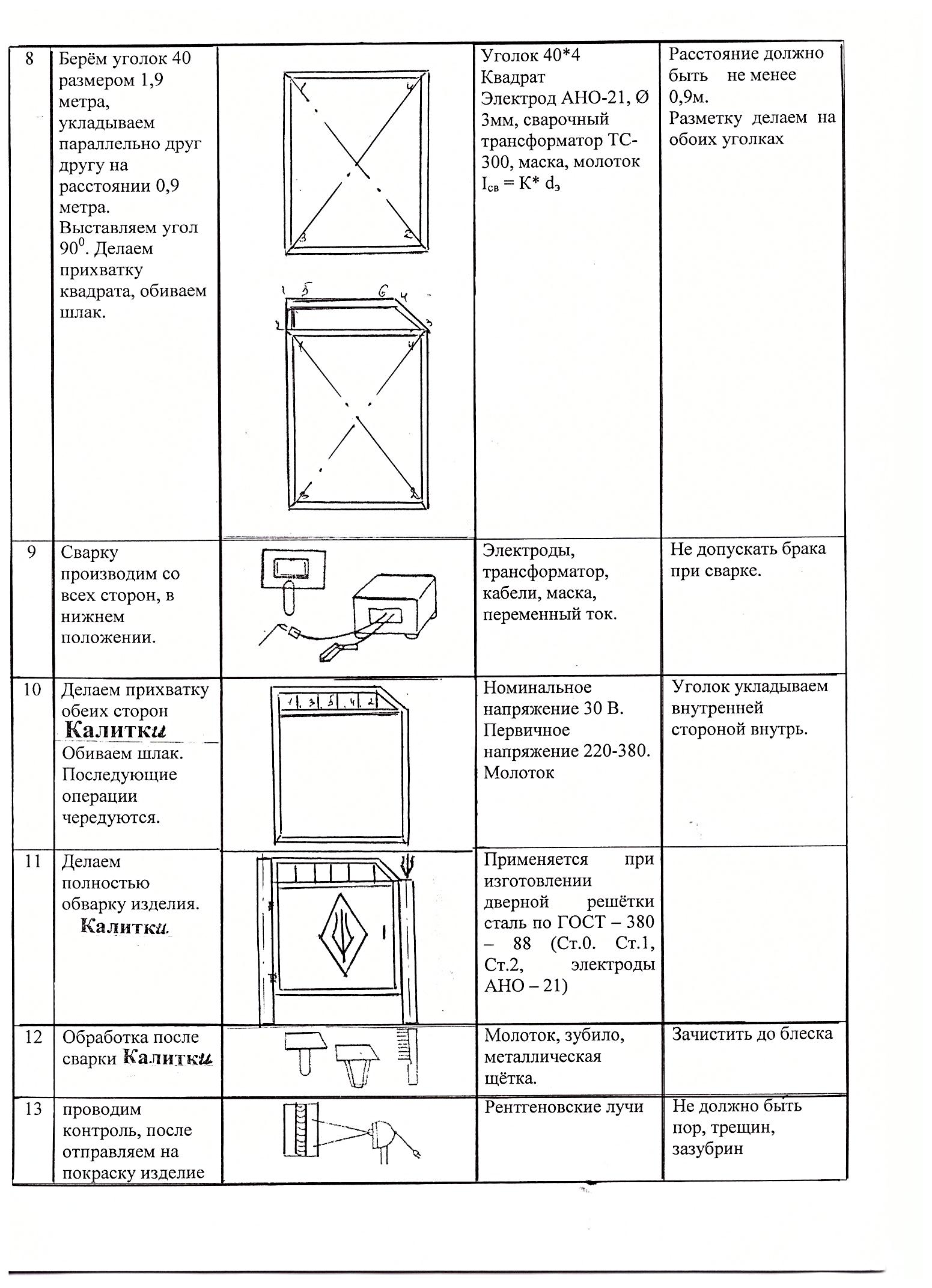
ГЛАВА3.ТЕХНИКА ВЫПОЛНЕНИЯ СВАРНЫХ ШВОВ
3.1.Деформации и напряжения при сварке
ГЛАВА4.КОНТРОЛЬ КАЧЕСТВА СВАРНОГО ИЗДЕЛИЯ
4.1.Выбор методов контроля заданной сварной конструкции
Контроль исходных материалов. Для обеспечения высокого качества сварных соединений необходим контроль исходных материалов (основного металла, электродов, сварочной проволоки, защитных газов и т. д.). Качество исходных материалов устанавливают на основании сертификатных данных, для чего определяют их соответствие требованиям данного технологического процесса сварки изделий. При наличии внешних дефектов, а также при отсутствии сертификатов исходные материалы допускают к использованию только после проведения химического анализа, механических испытаний и испытаний на свариваемость.
Основной металл в виде литых заготовок проверяют на наличие пор, усадочных раковин и трещин. Особое внимание обращают на зоны, подлежащие сварке. Эти места должны быть тщательно очищены от грязи, масла, краски, ржавчины и других загрязнений. Прокат проверяют на наличие расслоений, окалины, равномерности толщины листа и т. д.
Электроды проверяют на равномерность толщины покрытия, на наличие в нем трещин и других механических повреждений. Выполняют пробную сварку
, чтобы установить характер плавления электродного стержня и покрытия, легкость отделения шлака и качество формирования сварного шва (жидкотекучесть расплавленного металла, разбрызгивание). Электроды должны удовлетворять требованиям действующих ГОСТов.
Сварочную проволоку проверяют на чистоту поверхностей, отсутствие покрытий, нежелательных для данного технологического процесса сварки, расслоений и закатов. Выполняют пробную сварку, применяя соответствующий защитный газ, для установления качества материалов по показателям, упомянутым выше для электродов.
Защитные газы проверяют на отсутствие вредных примесей и влаги.
Свариваемость - свойство металла (или сочетания металлов) образовывать при установленной технологии сварки соединение, отвечающее требованиям, обусловленным конструкцией и условиями эксплуатации изделия. Проверка исходных материалов на свариваемость должна предшествовать принятию решения об использовании тех или иных материалов в сварной конструкции. В соответствии с указанным, свариваемость контролируют в двух случаях: при выборе материалов и разработке технологии сварки, т. е. при подготовке производства на стадии проекта; при запуске материалов в производственный цикл, т. е. при технологической подготовке производства. Вторая проверка связана с возможными отклонениями плавок основного металла, проволоки, а также партий электродов.
Контроль оборудования и оснастки. Качество сварных соединений в большой степени зависит от исправной работы сварочного оборудования. Цель и назначение данного вида контроля - обеспечить поддержание сварочного оборудования в рабочем состоянии в соответствии с паспортными данными на каждую машину или аппарат. Машины и аппараты для дуговой сварки должны обеспечивать устойчивое горение дуги, требуемую точность и правильность регулировки режима сварки. Эти параметры подлежат тщательной проверке каждый раз перед пуском оборудования и в процессе производства.
В значительной мере качество сварного соединения зависит от качества используемой специальной оснастки и приспособлений. Сборочные приспособления должны обеспечивать требуемую прочность и жесткость, точное, быстрое и надежное закрепление элементов сварной конструкции; необходимую степень точности всех размеров свариваемой детали, узла, изделия; установку свариваемого объекта в положение, удобное для сварки, и др. Эти требования должны быть отражены в технических условиях на проектирование и изготовление приспособлений. Вновь изготовленные приспособления до ввода в эксплуатацию проверяют на соответствие техническим условиям.